As we head into 2025, utilizing the capabilities of the right production scheduling and planning software can mean the difference between staying ahead of the curve or falling behind your competitors.
Unplanned bottlenecks crop up when tasks aren’t sequenced properly or when materials aren’t allocated on schedule. Missed deadlines not only dent your revenue but also chip away at your company’s reputation. Rework due to design errors or poor communication is both time-consuming and expensive, while confusion over job statuses can cause you chaos in your shop, making it difficult for team members to follow through on tasks effectively.
If these are some of the issues you see yourself battling with more often than not, it’s a good indicator that it’s time for you to adopt a specialized production planning and scheduling software.
The good news is, that there’s plenty of amazing production planning solutions out there. But which one to go for?
When choosing a production planning software, there are some distinctive factors specific to your use case, industry and needs that you might want to consider:
- Budget and total cost of ownership
- Initial cost (setup, licensing, hardware if on-premise)
- Ongoing subscription fees or maintenance costs
- Hidden costs (customization, integrations, training)
- Complexity and ease of use
- Learning curve for new users
- Level of training and support available
- Industry-specific features
- Custom workflows and routing tailored to your manufacturing niche
- Tools designed for specific production processes (e.g., metal fabrication)
- Customization and flexibility
- Ability to tailor modules and dashboards
- Configurability of reports and data views
- Integration capabilities
- Compatibility with existing ERP, CRM, accounting, and other business systems
- Availability of APIs and support for data import/export
- Third-party app integrations
- Scalability
- Suitability for small teams versus large enterprises
- Options for adding or removing features as your business grows
- Ability to handle increasing data volumes or multiple production sites
- Modular design that allows for phased implementation
- Deployment and implementation
- Cloud-based versus on-premise solutions
- Estimated time for setup and full deployment
- Customization services and consultancy support
- Intuitiveness of the user interface
- Vendor support and training
- Availability and responsiveness of customer service
- Quality of training materials and onboarding programs
- Performance and reliability
- Real-time data tracking and reporting capabilities
- System uptime guarantees and backup strategies
- Performance under high data loads
- Security and compliance
- Security protocols
- Compliance with industry regulations (GDPR, FDA, ISO)
- Role-based access controls and audit trails
We get it, it’s a lot to consider and take it. But we’re here to help! In this article we’re highlighting the top vendors for specific use cases, pain points and budgets. Let’s dive in.
1. EZIIL Starter — Best overall budget-friendly pick for project-based metal fabricators
EZIIL Starter is purpose-built for project based metal fabricators who need an easy transition from chaotic spreadsheets and pen-and-paper workflows into a digital platform. Unlike full-blown ERP systems that can overwhelm smaller shops with unused features (and hefty price tags), EZIIL strikes a sweet spot: it’s powerful, modular, and specifically tailored to fabrication processes—from quoting and scheduling to real-time capacity management and productivity tracking.
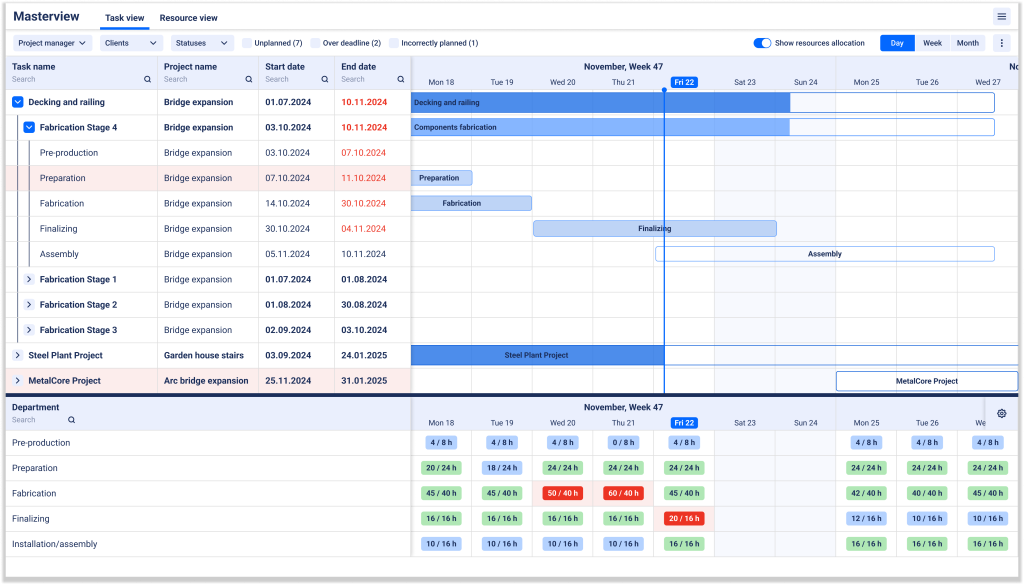
Key features
- Shop floor planning and scheduling
- Drag-and-drop job assignments
- Real-time capacity checks to avoid bottlenecks
- Department-specific task visualization
- Centralized data and collaboration
- Store all customer details, drawings, and documents in one place
- Set standardized input fields to reduce errors
- Production and profitability analytics
- Compare planned vs. actual hours to identify inefficiencies
- Auto-planning for repeat projects with custom task templates and routing
- Mobile reporting
- Time logging and job status updates via iOS/Android devices
- On-the-go visibility so supervisors and managers can stay informed
- Scalability with add-on modules
- Implement at your own pace and only pay for the features you use
- Enterprise (optional): BOM and purchase management, warehouse/inventory control, subcontracting management, advanced analytics, and EN 1090-2 compliance
Pricing
- Starter plan from $90/month:
- 1–15 users at $90/month
- 16–50 users at $160/month
- 51–150 users at $250/month
- Enterprise: Add advanced modules as needed without committing to the full suite. Book a demo for a custom quote.
Who is EZIIL Starter production planning software best suited for?
- Small-to-mid sized metal fabricators (20–200 employees) aiming to phase out Excel and manual methods without jumping headfirst into a complex ERP
- Project based fabricators that need real-time shop-floor tracking, straightforward scheduling, and an affordable, flexible option to scale up later
- Job shops focusing on on-time delivery, reducing rework, and improving visibility for all stakeholders
Pros and cons
Pros:
- Tailor-made for metal fabrication workflows
- Fast vendor supported implementation (2-3 weeks from kick off to going live)
- Modular approach prevents “ERP bloat” — only pay for what you need
- Intuitive dashboards, drag-and-drop scheduling, and real-time tracking
- Planned vs reality reporting on projects
- Mobile app integration for convenient shop-floor updates
- Highly rated customer support
- Affordable monthly pricing with no long-term lock-ins
- Light weight cloud-based solution
Cons:
- Advanced features (like BOMs, inventory management) require Enterprise add-ons
- Not a universal solution for non-fabrication industries
2. Monday — Best for industry agnostic cross-department workflows
Monday.com is a popular work operating system that offers flexible task boards, collaborative features, and automation to help teams plan and deliver projects efficiently.
Although not designed exclusively for metal fabrication, Monday can be adapted for basic production scheduling. Thanks to its visual interface, drag-and-drop features, and robust integrations, it remains a strong pick for businesses that want a single platform to unify operations across multiple departments—production, sales, marketing, and beyond.
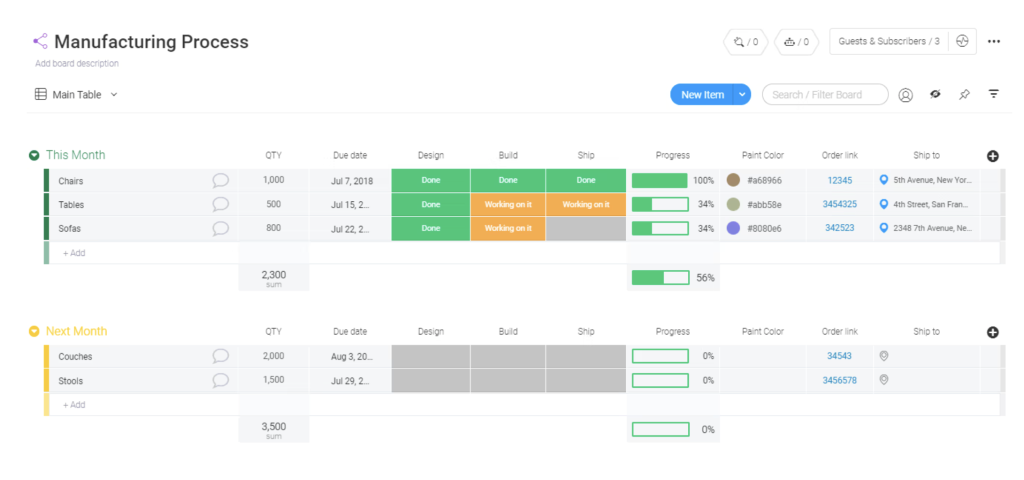
Key features
- Customizable workflows
- Build your own boards with columns for tasks, due dates, owners, progress updates
- Collaboration and automation
- Automate notifications, alerts, and hand-offs between team members
- Collect customer orders or internal requests automatically via embedded forms
- Visual dashboards
- Get a basic overview of production status, pending tasks, or overdue items
- Kanban boards, calendar view, timeline, and Gantt chart (on certain plans)
- Cross-functional connectivity
- Connect with finance, HR, or marketing workflows within the same platform
- Extensive library of integrations
Pricing
(Billed annually; each plan has a free 14-day trial. Pricing below is total per month for 1 seat, multiplied by the number of seats.)
- Free
- Up to 2 seats
- Limited boards and features
- Basic: $9/seat/month
- Unlimited free viewers and items, 5 GB storage, basic dashboards
- Standard: $12/seat/month
- Includes Timeline & Gantt, Calendar, guest access, limited automations/integrations
- Dashboards combining up to 5 boards
- Pro: $19/seat/month
- Private boards, time tracking, more generous automation/integration limits
- Dashboards combining up to 20 boards
- Enterprise: N/A
- Includes multi-level permissions, advanced security, and custom onboarding
Who is Monday production planning solution best suited for?
- Teams needing a generalist platform to manage everything from marketing campaigns to production tasks
- Companies wanting broad automation and integration with popular apps, plus a visually appealing interface
- Organizations where multiple departments must collaborate on shared data boards (sales, finance, HR, etc.)
Pros and cons
Pros:
- Highly visual and customizable boards
- Good for cross-team collaboration and broad workflows
- Wide range of native integrations and automation templates
- Scalable plans that suit freelancers up to large enterprises
- Clear color-coding and progress updates for quick overviews
Cons:
- Not specialized for metal fabrication; may require more setup or third-party integrations for advanced scheduling features
- Automations and integrations can quickly consume monthly “action” limits, prompting plan upgrades
- Customer support feedback is mixed, with some users citing slow or repetitive handoffs
- Some advanced functionalities (e.g., time tracking, private boards) locked behind higher plans
- Pricing can increase steeply as team size and automation needs grow
3. Frepple — Best open-source solution for manufacturing and distribution companies
Frepple is an open-source, cloud-based planning tool designed for mid-sized companies that need agile production and inventory planning. Built to extend the capabilities of traditional ERP systems, Frepple covers demand forecasting, inventory management, and production scheduling.
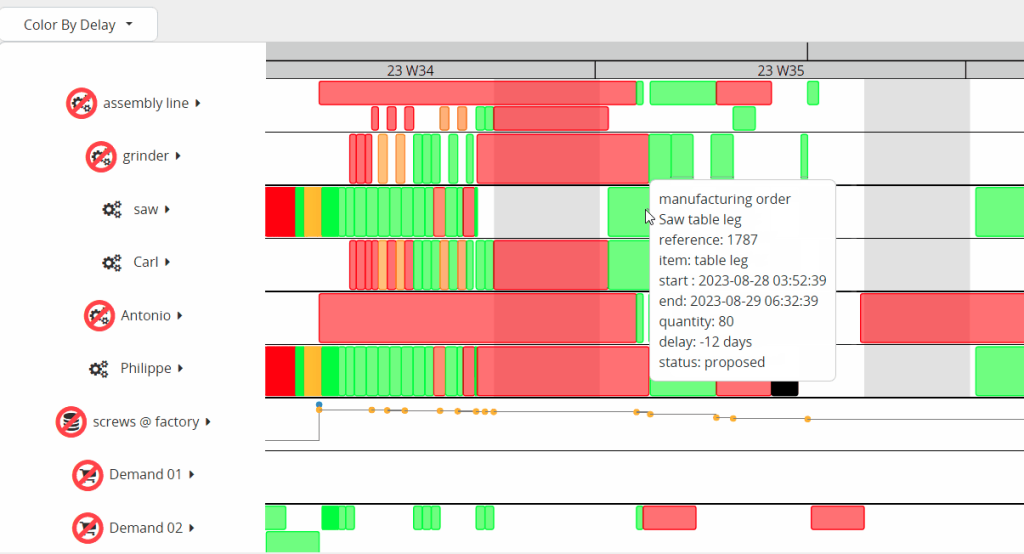
Key features
- Demand forecasting and inventory planning
- Forecast future demand and adjust sales predictions to optimize inventory levels
- Calculate safety stock levels and dynamically adjust plans to minimize stockouts
- Production scheduling
- Visual scheduling via drag-and-drop Gantt charts to manage production orders
- What-if scenarios and real-time adjustments
- Simulate production disruptions (e.g., machine breakdowns, rush orders) to test alternative scheduling options
- Make on-the-fly adjustments based on real-time production progress
- Flexible integration
- Extendable via REST API, CSV/Excel imports, and direct database access
Pricing
- Basic plan: Approximately €612 per month (billed annually)
- Standard plan: Approximately €765 per month (billed annually)
- Implementation services: Additional implementation services range from €2,000–€5,000 for a proof of concept to €5,000–€25,000 for full-scale implementations
Who is Frepple production planning solution best suited for?
Ideal for industries such as injection molding, metal machining, spare parts, and aerospace; values transparency, flexibility, and fast implementation.
- Mid-sized manufacturing and distribution companies looking to transition from spreadsheets to a robust, agile planning system
- Organizations that need comprehensive production planning with the ability to integrate with existing ERP systems
- Companies that value open-source solutions with transparent pricing and a flexible, extendable architecture
Pros and cons
Pros:
- Open-source core with transparent pricing and a community edition for trial
- Fast planning algorithms that can reduce planning time significantly
- Flexible integration options via API, CSV, and Excel
- Effective at aligning production capacity with demand, reducing forecast errors and stockouts
- Agile implementation with a relatively short timeline (10–12 weeks)
Cons:
- May require significant customization for unique production processes
- Implementation can involve steep additional costs for professional services and support
- Some users report that extensive customization is needed to fully adapt the tool to their specific workflows
- Documentation and training materials, while available, may require a learning curve for teams new to open-source planning tools
4. Katana — Best for manufacturers with multiple warehouse locations with a strong emphasis on inventory visibility
Katana Cloud Inventory is a manufacturing and inventory management platform designed to give you a unified, real-time view of stock levels and order statuses. It supports both simple and more advanced needs like production management, demand forecasting, and warehouse management. With integrations for major e-commerce platforms like Shopify and WooCommerce, plus accounting tools like QuickBooks Online or Xero, Katana is ideal for manufacturers who sell direct-to-consumer or need an omnichannel approach.
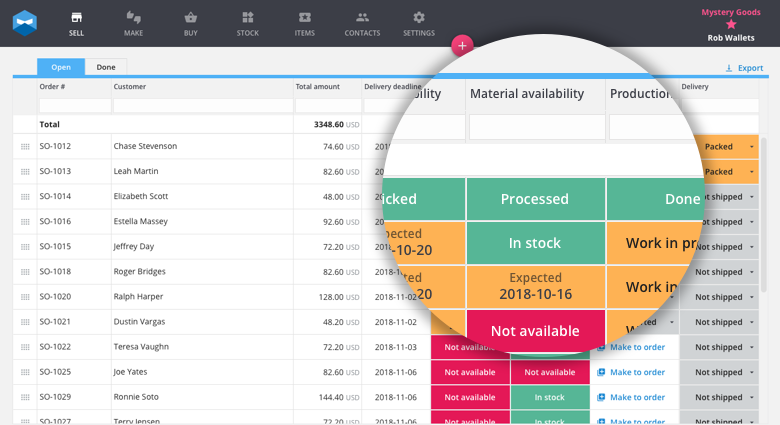
Key features
- Inventory and purchase management
- Real-time stock tracking for raw materials and finished goods
- Automated purchase orders and reordering
- Multi-currency and multi-location support on certain plans
- Production and planning
- Bill of materials (BOM) management for complex products
- Shop Floor App for real-time task assignments and progress updates
- Demand forecasting
- AI-powered demand planning to help replenish inventory proactively
- Reports and analytics to identify top-performing products
- Warehouse app (add-on)
- Barcode scanning, bin location management, mobile picking/packing
- Full traceability for batches, serial numbers, and labeling
Pricing
(Billed annually; quarterly pricing available at a higher rate)
- Starter: $179/month
- 1 inventory location, unlimited SKUs, unlimited users, basic features
- Standard: $359/month
- Includes everything in Starter, plus advanced insights, barcode scanning, up to 3 locations, and multicurrency
- Professional: $799/month
- Adds unlimited inventory locations, full traceability, forecasting, warehouse management, and access to API
- Enterprise: Custom pricing for larger, more complex operations
Who is Katana production planning solution best suited for?
- Small-to-mid sized manufacturers or e-commerce brands needing robust, real-time visibility into stock levels and production schedules
- Companies with complex BOMs, contract manufacturing, or multiple warehouses that need a single system to unify everything
- Teams looking for integrations with Shopify, WooCommerce, and accounting software, plus advanced forecasting and warehouse features
Pros and cons
Pros:
- Real-time inventory oversight and demand forecasting
- Straightforward e-commerce integrations (Shopify, WooCommerce)
- Powerful production management features with a Shop Floor App
- Flexible scaling from Starter to Pro, with advanced warehouse add-ons
- Highly rated customer support
Cons:
- Advanced features (like multi-location, forecasting, full traceability) can be pricey for smaller shops
- Some users report occasional lag or incomplete features for specialized workflows
- Limited offline handling of inventory transfers or partial shipments on lower-tier plans
- Not a metal-fab-specific tool, so may require customization or workarounds for certain fabrication steps
5. MasterControl Manufacturing Excellence — Best for regulated and quality-intensive use cases
MasterControl Manufacturing Excellence (Mx) is a digital manufacturing platform geared toward heavily regulated industries. It replaces paper-driven processes—like batch records and device history records—with electronic workflows that integrate seamlessly with quality management systems (QMS) and other enterprise tools. By focusing on compliance, audit-readiness, and data integrity, MasterControl helps manufacturers reduce errors, speed up reviews, and meet stringent industry standards.
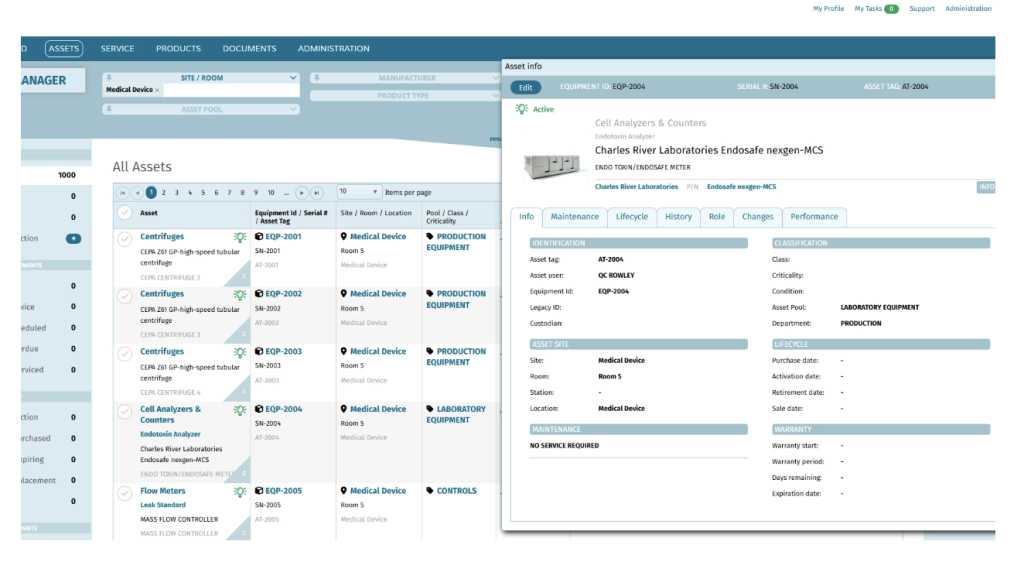
Key features
- Modern MES (Manufacturing Execution System)
- Digitize and streamline production steps with automated data capture
- Real-time tracking of work-in-progress, equipment usage, and operator actions
- Electronic batch records and device history records
- Dynamic process controls, built-in compliance checks, and auto-alerts for deviations
- Significantly reduces paper usage and cycle times in life science settings
- Connected operations and asset management
- Integrates with ERP, LIMS, QMS, IoT devices, and more
- Electronic logbooks, equipment calibration, and maintenance management
- Compliance and audit trails
- Automated record-keeping, e-signatures, and configurable access controls
- Simplifies compliance with FDA, ISO, GMP, and other regulatory standards
Pricing
- Custom quote only: Costs vary based on number of users, modules needed, and scope of integrations
Who is Mx production planning software best suited for?
- Highly regulated manufacturers that need top-tier traceability and compliance
- Companies seeking a paperless, audit-ready environment for batch records and device history records
- Organizations that need seamless integration between production, quality assurance, R&D, and supply chain systems
Pros and cons
Pros:
- Comprehensive compliance controls and error-proofing
- Accelerated review and product release through real-time exception handling
- Strong integration potential (ERP, QMS, LIMS, etc.)
- Significantly reduces paper record handling
- Ideal for regulated life sciences (FDA, GMP, ISO standards)
Cons:
- Complex setup and validation: can be time-consuming for small teams
- Higher price point, typically for larger enterprises or established SMBs with bigger budgets
- Limited manufacturing-specific features if your focus isn’t regulated industries
- Some users note a steep learning curve and “rigid” workflows
6. Visual Planning — Best for companies with complex production operations
Visual Planning is a flexible, collaborative scheduling and resource management software designed to streamline complex production operations. With a centralized platform that integrates manufacturing order planning, resource allocation, inventory management, and process monitoring, Visual Planning aims to improve efficiency and help make data-driven decisions.
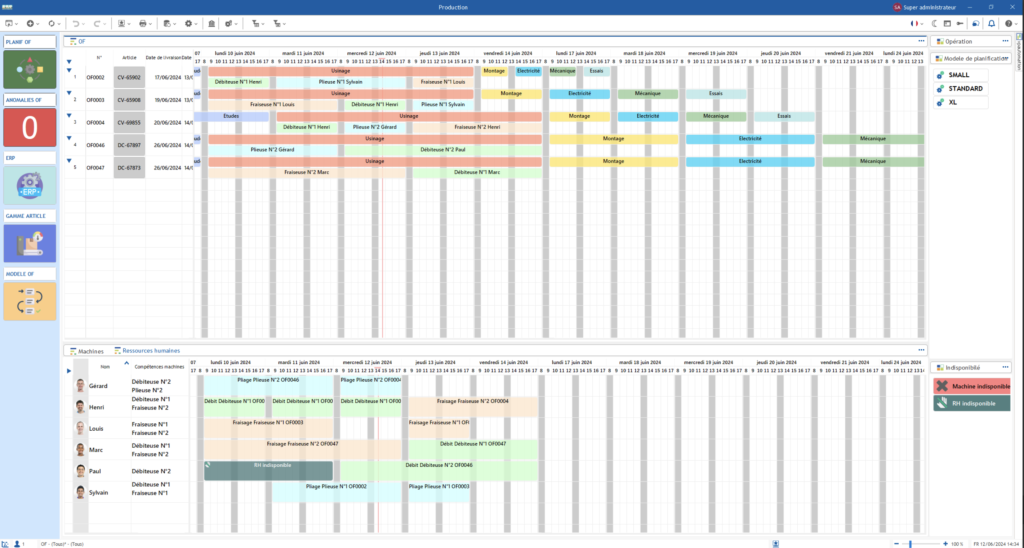
Key features
- Centralized scheduling and resource management
- Comprehensive planning of production orders with real-time updates
- Automation and customization
- VPAutomation for automatic scheduling and resource auto-assignment
- Customizable views (Gantt charts, load plans, control totals) to track performance and costs
- Data centralization and integration
- Import/export features (XLS, CSV, XML, JSON) and a REST API for integration with ERP, MRP, HR, and other systems
Pricing
VP DESK (for main schedulers):
- SaaS: $55 per user/month (annual billing)
- Subscription: $660 per year per user
- Lifetime Licence: $1,270 (plus 20% maintenance per year)
- VP PORTAL (for daily users):
- SaaS: $40 per user/month or $480 per year per user
- Lifetime Licence: $790 (plus 20% maintenance per year)
- VP GO (for mobile users):
- SaaS: $15 per user/month or $180 per year per user
- Lifetime Licence: $290 (plus 20% maintenance per year) (Note: Pricing details are based on annual billing and may vary with license type and configuration.)
Who is Visual Planning solution best suited for?
- Manufacturers and production managers who require a ****customizable scheduling tool
- Businesses that need to integrate data from multiple systems and want granular control over resource allocation and cost management
Pros and cons
Pros:
- Highly flexible and customizable with robust automation features
- Centralizes diverse production data for informed decision-making
- Multiple delivery and licensing options to fit different business models
- Strong integration capabilities via API and standard data formats
Cons:
- Initial setup and customization can be time-intensive, especially for smaller teams
- Steeper learning curve for users not familiar with advanced scheduling tools
- Some users report occasional glitches in automation or integration with external tools
7. Plex Smart Manufacturing Platform — Best for Holistic Smart Manufacturing
Plex offers an all-in-one cloud-delivered solution that connects people, systems, and machines. Covering MES, ERP, quality management, and supply chain planning. It’s engineered to help manufacturers optimize capacity and maintain traceability across the entire production process.
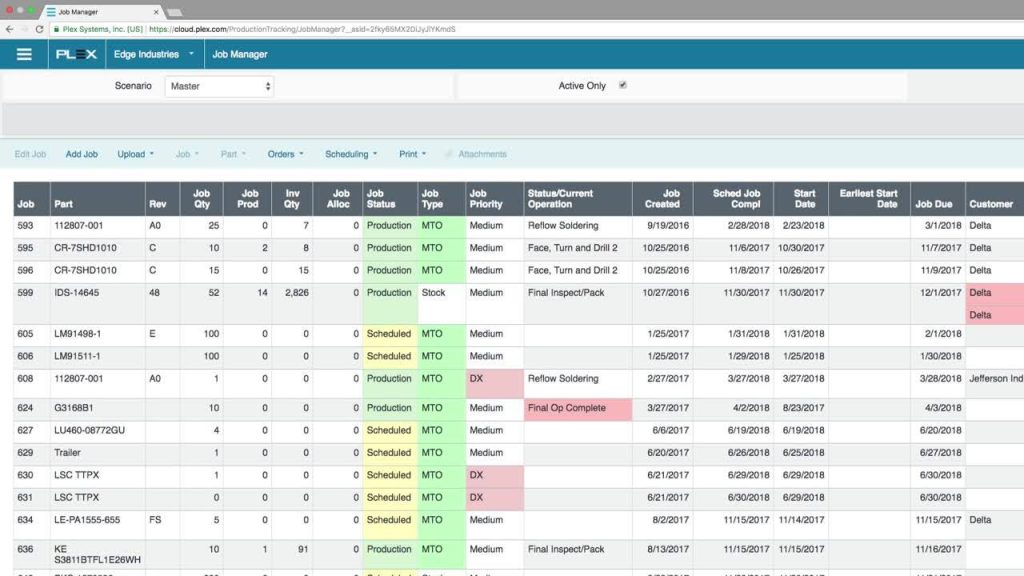
Key features
- Manufacturing production planning and scheduling
- Scheduling with capacity constraint management across work centers
- Materials requirement planning (MRP) for accurate inventory and order forecasting
- Real-time production management
- Centralized control panels for real-time visibility into shop floor activities
- Digital Kanban systems and pull scheduling to reduce overproduction
- Comprehensive integration and data analytics
- Seamless integration with ERP, quality, and asset management systems
- Production analytics dashboards for KPIs such as OEE, scrap rate, and machine availability
- Tooling, maintenance and ssset management
- Integrated modules for preventative maintenance and tooling control to optimize uptime
Pricing
- No public pricing details available
Who Is This Solution Best Suited For?
- Mid-to-large manufacturers seeking an integrated, enterprise-level solution for smart manufacturing
- Companies that need comprehensive production control across discrete and process manufacturing environments
- Organizations that require real-time production visibility, robust analytics, and advanced capacity management to drive lean practices
Pros and Cons
Pros:
- Holistic integration of MES, ERP, quality, and supply chain management
- Strong real-time production visibility and robust analytics capabilities
- Advanced scheduling options with finite capacity and resource optimization
- Enables error-proof production and better communication across departments
Cons:
- Custom pricing may be prohibitive for smaller manufacturers
- Users report usability challenges and a steep learning curve for some modules
- Some screens and interfaces can feel disjointed, requiring time to master
- Customer support experiences are mixed, with some reporting difficulties in timely resolutions
What is a production planning software?
Production planning software is a specialized digital tool designed to help manufacturers schedule, coordinate, and optimize their production processes. At its core, it enables companies to create detailed production plans that allocate tasks, manage resources, track progress, and adjust operations in real time. The software replaces manual methods—such as spreadsheets and paper‑based systems—with an integrated, data‑driven platform that improves accuracy, reduces errors, and enhances overall efficiency.
This type of software is for anyone involved in production—ranging from small job shops to large industrial manufacturers. In particular, production planning software is invaluable for:
- Project-based manufacturers: Companies like metal fabricators who handle custom, one-off projects and need precise scheduling.
- Mid-to-large enterprises: Organizations with multiple production lines that require coordinated resource allocation and real-time monitoring.
- Regulated industries: Businesses in sectors such as pharmaceuticals or medical devices, where compliance and traceability are paramount.
- Companies transitioning from manual processes: Businesses still reliant on spreadsheets, emails, or paper records that are seeking to streamline operations and reduce manual errors.
When should metal fabricators start looking into a specialized production planning software?
If you’re a shop executive, production manager, or project lead in a metal fabrication business with anywhere from 20 to 200 employees—and you’re still juggling Excel spreadsheets, pen-and-paper job tickets, and chaotic email chains—you’ll benefit immensely from a robust planning platform.
Some of the common struggles that a specialized production scheduling and planning software like EZIIL can help with include:
- Accelerating customer demands: Clients want faster turnarounds and tighter customization, meaning your old-school processes might struggle to keep up.
- Increased complexity as shops expand: As you take on more jobs or diversify your product range, manual tracking and scheduling become exponentially harder.
- Desire to avoid ERP bloat and overspending: Many full-blown ERP solutions are costly and come with features you won’t use. By choosing a more focused system, you pay only for what you need now.
Immediate benefits of a production planning and scheduling software:
- Real-time visibility: See at a glance how each job is progressing and where your bottlenecks are.
- Fewer delays and bottlenecks: Automated scheduling helps you allocate resources properly and prevent downtime.
- Enhanced profitability: Better planning cuts out wasted hours and reduces expensive rework.
- Improved collaboration and on-time deliveries: Centralized data makes it easier for teams to align on tasks and keep customers happy.