Aluminum, an extensively utilized material in our day-to-day lives, has always been renowned for its remarkable lightweight properties, exceptional corrosion resistance, and impressive electrical conductivity.
However, among the myriad of processes that enhance its functionality within the metal industry, anodized aluminum stands out as an essential technique. The primary objective of this article is to delve into the anodization process, shed light on its significance, and explore the extensive array of benefits it offers. These advantages encompass anodizing finishes and colors, in addition to its potential application to other metals, making it a topic of increasing importance due to the growing demand for anodized aluminum.
By thoroughly examining this process, we hope to uncover the reasons behind its popularity and its diverse applications across various industries.
What is Aluminum Anodizing?
Anodizing is a method of enhancing the surface quality of metals, particularly aluminum, via an electrochemical process. The essence of this process lies in forming a layer of aluminum oxide on the material’s surface. The resulting anodized coating significantly improves the metal’s corrosion resistance, surface hardness, and aesthetic appeal.
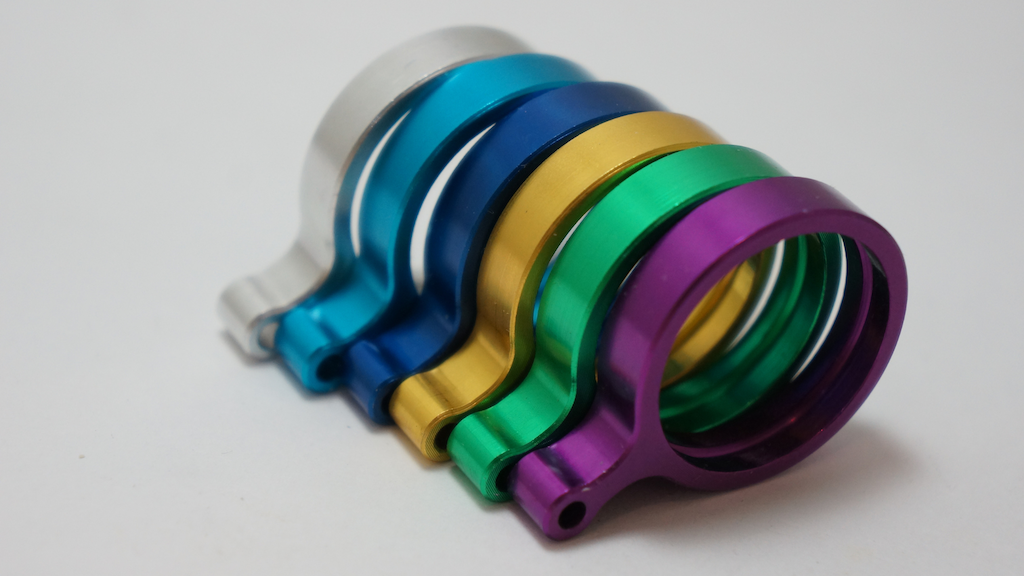
How Does the Anodizing Process Work?
The anodizing process is an electrochemical surface treatment used primarily on aluminum and its alloys to create a durable and corrosion-resistant oxide layer on the metal’s surface.
It involves passing an electric current through an electrolyte solution while the aluminum acts as the anode in the circuit. Here’s a step-by-step explanation of how the anodizing process works:
- Pre-Cleaning: The aluminum surface is thoroughly cleaned to remove any contaminants, oils, or dirt that could interfere with the anodizing process. This step ensures proper adhesion and uniformity of the anodized layer.
- Deoxidizing: In some cases, especially for new aluminum, a deoxidizing step is performed to remove any existing surface oxide layer and expose the pure metal underneath.
- Anodizing Bath Preparation: An electrolyte solution is prepared, usually consisting of sulfuric acid. The concentration of the acid and other additives may vary depending on the desired characteristics of the anodized layer.
- Immersion in Anodizing Bath: The cleaned aluminum part is immersed in the anodizing bath and serves as the anode in the electrochemical cell.
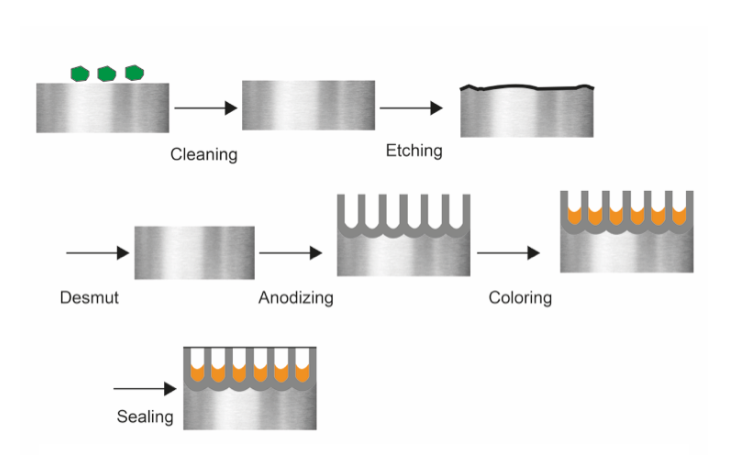
- Application of Direct Current (DC): A direct current (DC) is applied to the electrolyte bath. The aluminum part acts as the anode, while a cathode is also present in the bath to complete the circuit. The cathode can be made of lead or stainless steel.
- Formation of Anodic Oxide Layer: As the current passes through the electrolyte and the aluminum part, an electrochemical reaction occurs at the surface of the aluminum. This leads to the formation of a controlled layer of aluminum oxide on the surface of the metal.
- Pore Formation: The anodic oxide layer is porous and acts as a matrix of interconnected channels. These pores allow for further treatments or the incorporation of dyes for coloring.
- Growth of Anodic Oxide Layer: The thickness of the anodic oxide layer increases with the duration of the anodizing process. The thickness can be controlled to achieve specific functional properties and appearances.
- Sealing: After the desired anodized layer thickness is achieved, the part is removed from the anodizing bath and rinsed. In some cases, the anodized layer may be sealed using hot water or a sealing agent. Sealing helps to close the pores, enhance corrosion resistance, and improve dye retention (if coloring is applied).
- Final Finishing: Once the anodizing process is complete, the anodized part may undergo additional finishing processes, such as dyeing (for color), mechanical polishing, or bead blasting, to achieve the desired appearance and surface characteristics.
The anodizing process produces a protective and aesthetically appealing surface layer, making it a widely used method for various industrial and consumer applications, including aerospace, automotive, architectural, and consumer goods.
Alternatives of anodized aluminum
Anodizing is a surface treatment process used to enhance the corrosion resistance and appearance of metals, particularly aluminum. It involves creating an oxide layer on the metal’s surface through an electrochemical reaction. Although anodizing is a popular choice, there are several typical alternatives for achieving similar surface properties and benefits:
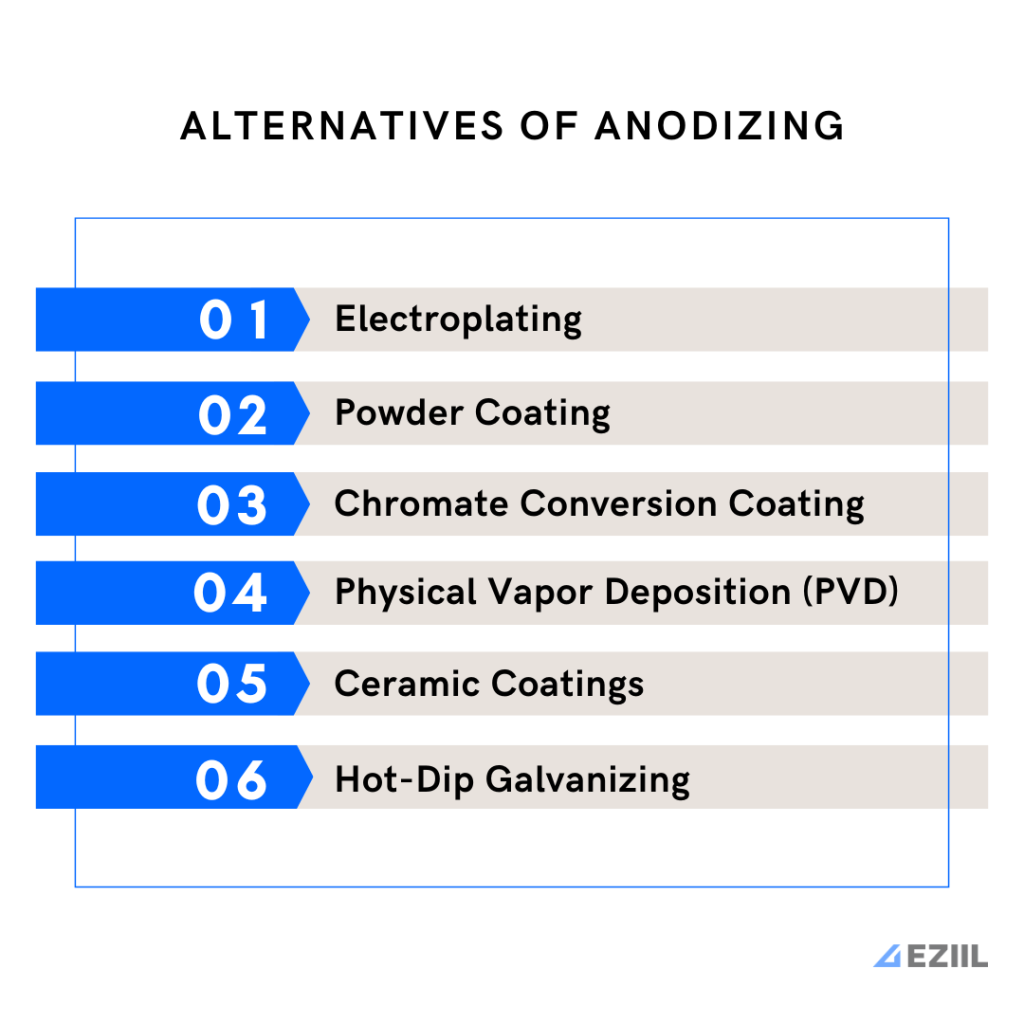
Electroplating: Electroplating involves depositing a thin layer of another metal onto the substrate’s surface. This process can enhance corrosion resistance, provide improved aesthetics, and even offer certain specific functional properties, depending on the plated material used.
Powder Coating: Powder coating is a method where a dry, powdered paint is applied electrostatically to a metal surface. The coated part is then heated, causing the powder to melt and form a durable, protective film. Powder coating offers excellent corrosion resistance, impact resistance, and a wide range of color options.
Chromate Conversion Coating: Also known as chem film or Alodine, chromate conversion coating creates a protective layer on the metal surface. It enhances corrosion resistance, provides good adhesion for paints and adhesives, and can act as a primer for subsequent coatings.
Physical Vapor Deposition (PVD): PVD is a vacuum-based process used to deposit thin films of materials onto metal surfaces. It offers various coatings like titanium nitride (TiN), chromium nitride (CrN), and zirconium nitride (ZrN) for improving hardness, wear resistance, and aesthetic appearance.
Ceramic Coatings: Ceramic coatings are applied by thermal spraying or chemical vapor deposition methods. These coatings provide high-temperature resistance, wear resistance, and thermal barrier properties.
Hot-Dip Galvanizing: This process involves immersing the metal in a bath of molten zinc, creating a zinc coating on the surface. It provides excellent corrosion protection for steel and iron substrates.
Each alternative method has its unique advantages and applications, and the choice of the most suitable surface treatment depends on factors such as the intended use, material properties, environmental conditions, and desired aesthetic appearance.
Why Choose Anodized Aluminum?
Anodized aluminum is a go-to choice for many industries because of its superior properties. Notably, anodized coatings increase durability and longevity, providing a hard, wear-resistant layer on the aluminum surface that’s much thicker than what naturally forms.
Moreover, anodized aluminum is remarkably resistant to corrosion. This property stems from the anodized coating being porous, which allows it to absorb protective substances during the sealing process. It can also withstand high temperatures without losing its structural integrity, unlike some painted or plastic alternatives.
Versatility in Finishes and Colors
A major benefit of anodized aluminum is the variety of anodizing finishes and colors available. From clear to bronze and black, the anodizing color spectrum caters to diverse aesthetic requirements. For instance, home anodizing aluminum allows homeowners to match their décor preferences, while industries can maintain their brand’s color consistency.
One particular process, known as “how to black anodize aluminum,” has gained traction in recent years. Black anodizing involves using tin or nickel in the electrolyte bath to produce a black dyed layer, which provides excellent light absorption, making it a preferred choice in optical applications.
Can Other Metals Be Anodized?
While anodizing is predominantly applied to aluminum, anodization isn’t limited to this material. Other anodized metals include titanium, magnesium, and even zinc.
However, the results and properties vary depending on the metal used. For instance, anodized steel can achieve a greater corrosion resistance, making it suitable for specific industrial applications.
Anodizing and the Environment
Aluminum anodizing is generally considered to be an environmentally friendly surface treatment process compared to many other coating and plating methods. It offers several environmental benefits, but there are also some considerations regarding its impact on the environment:
Positive Environmental Effects
Non-Hazardous Waste: The anodizing process generates relatively low amounts of hazardous waste. The primary waste generated is the aluminum oxide removed from the surface during pre-treatment processes. This waste is generally non-hazardous and can be recycled or safely disposed of.
Reusability: Anodizing baths can often be reused for an extended period, reducing the consumption of chemicals and water. This recycling aspect minimizes the overall environmental footprint of the process.
Energy Efficiency: Anodizing is an electrochemical process, and when conducted with modern equipment, it can be energy-efficient, especially if renewable energy sources are used to power the process.
Durability and Recyclability: Anodized aluminum surfaces are highly durable and resistant to corrosion, extending the lifespan of aluminum products. The extended use of anodized products reduces the need for frequent replacements, promoting resource conservation. Additionally, aluminum is highly recyclable, making it a sustainable material choice.
Negative Environmental Considerations:
Energy Intensive: While the anodizing process is relatively energy-efficient compared to some other surface treatments, it still requires a significant amount of electricity to perform the electrochemical reactions.
Chemicals and Emissions: The chemicals used in the anodizing process, such as sulfuric acid, can be hazardous if not handled properly. Strict waste management and proper disposal of chemicals are essential to prevent environmental harm. Additionally, emissions from the process can be a concern if proper air quality controls are not implemented.
Exploring the Future of Anodized Aluminum
The future of anodized aluminum holds exciting prospects as advancements in technology and growing environmental concerns continue to shape the industry. Here are some key areas to explore:
Sustainable Anodizing Processes: As sustainability becomes a priority, the anodizing industry is likely to focus on further reducing energy consumption and optimizing chemical usage. Advancements in process efficiency and the adoption of eco-friendly electrolytes may contribute to a more sustainable anodizing process.
Nanotechnology and Surface Functionalization: Nanotechnology holds immense potential for creating novel anodized aluminum surfaces with unique properties. Researchers are exploring nanoscale coatings to enhance corrosion resistance, self-cleaning capabilities, and even antimicrobial properties, making anodized aluminum suitable for a broader range of applications.
Colored and Decorative Finishes: The demand for aesthetically appealing anodized aluminum continues to grow. Innovations in dyeing techniques and the use of advanced pigments may lead to a wider array of vibrant and durable colored finishes. Customization options and decorative effects could become more prevalent.
Improved Wear and Abrasion Resistance: Research and development efforts are focused on enhancing the wear and abrasion resistance of anodized aluminum surfaces. New anodizing techniques and coatings may find applications in high-performance industries, such as aerospace, automotive, and electronics.
Final Thoughts
Anodizing aluminum, whether it is at home or professionaly is a vital process in today’s metal industry. Its ability to enhance the durability, aesthetics, and versatility of aluminum makes it an essential process that has been embraced by various sectors. From anodizing finishes and colors to understanding how to black anodize aluminum, the process adds value to this abundant and versatile metal.
In a world increasingly concerned with sustainability and efficiency, the benefits of anodized aluminum stand out. Its low maintenance and recyclable nature make it a material that aligns with the needs of both today and tomorrow. It is not surprising, therefore, that more industries and individuals are choosing anodized aluminum for their projects and products.