Eziil helped Vertex Estonia move from Excel-based planning to digitized project technology preparation, make the procedure more transparent, faster and efficient, as well as raise overall employee satisfaction. Altogether it helps them shift to more complicated projects and deliver business value.
Vertex Estonia
Products:
Large scale parabolic antennas including Cassegrain, Gregorian, Front Feed and Offset configurations. Reflector diameters range up to 27 meters with frequencies in C, X, Ku, Ka, Q/V bandwidths.
Industrial equipment (e.g. conveyors, floats) and technological lines for various industries.
Production certificates: ISO 9001; ISO 14 001; ISO 45 001;
EN ISO 3834; EN 1090
Founded: 1981
Location: Tallinn, Estonia
Staff: 76 people
Production area: around 30,000 m² with 6000 m² indoors
2021 turnover: € 6 million
Home page: http://www.vertexestonia.eu/eng/
Vertex Estonia is part of CPI group: https://www.cpii.com/
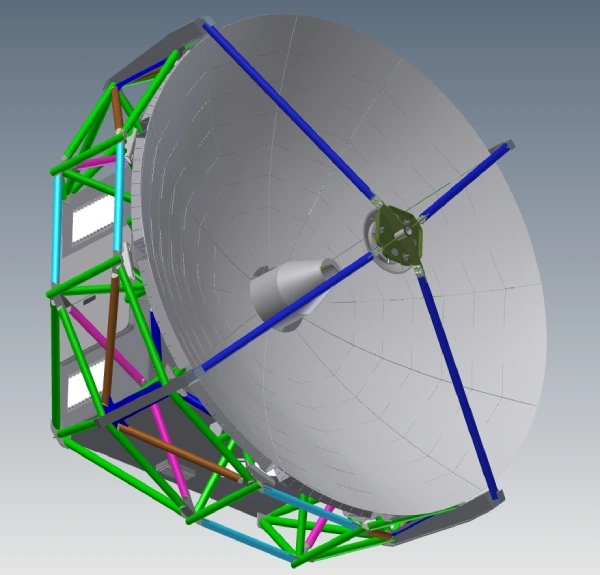
Life before Eziil
Before implementing Eziil BOM, Vertex used the good old spreadsheets. Tamur Mikk, the chief project manager of Vertex says that the system was difficult to maintain and standardise.
They also found revisions challenging, often the changes got lost and the information in Excel didn’t match the information they had elsewhere. As a result, the engineering department had to redo much of their work and couldn’t concentrate on new projects. This also affected the customers and posed a risk of reputational damage.
Vertex mainly had 6 types of production technology challenges:
1. Structuring and organizing data
2. Connecting drawings to materials
3. Project preparation time
4. Employee satisfaction
5. Shifting toward more complex and higher-value-added products
How Eziil helped standardize and centralize the process
Vertex Estonia adopted Eziil BOM in January 2021. Artur Prees, the CEO of Vertex says that when choosing the BOM software, they liked that Eziil is focused on project-based metal fabrication
We were looking for a partner, who’d really know our business and value us as a partner. Now we can say Eziil lives up to the expectation – our concerns are answered and addressed. It’s too soon to talk about specific numbers, but we already see that the process reliability has gone way up. We’re optimistic to get project errors down to a zero.

1. Structuring and organizing data
When Vertex was using spreadsheets, the data was scattered and unorganized. They tried standardizing it, but always went off track. Without clear rules, people could modify data as they pleased and as a result, there were 16 different articles to describe one specific bolt, for example. Such situations caused confusion for both the purchasing and production teams, which in turn resulted in production errors, potential financial damage and customer credibility risk.
Life with Eziil
With implementing Eziil, Vertex tidied up their entire database and can count on it staying that way. Eziil’s clear structure, unified database and connection between drawings and BOM (Bill of materials) lines creates a clear picture for all parties involved. Also, with the bulk edit tool, they can add specifications or additional information to specific product groups. For example, labeling bolts with ISO information in addition to DIN information, without rummaging through endless spreadsheets.
2. Connecting drawings to materials
No one had a real overview of the project scope and structure, or an understanding, which parts are related to what and how will the product eventually play out. The project managers couldn’t really manage the technical information since it was so scattered. Both the spreadsheets and drawings seemed to have a life of their own. For example, the engineering department had a folder of standard drawings but finding the right drawing and making sure it really was the right one – not a random edited copy – wasted a lot of time.
Life with Eziil
With Eziil, all parties have a clear picture of which parts belong to what products and how they’re really related. Every line is related to a specific drawing, original drawings are always attached to the BOM structure and easy to manage.
Artur adds that the drawings’ quick view functionality is also very simple: “Viewing PDF-files is super convenient. Eziil has outdone Microsoft on this one!”
3. Project preparation time
Due to aforementioned problems, getting a project into production used to take a lot of time. Firstly, people had to gather and double-check information from various sources. Also, one had to implement customer requests and suggestions to several spreadsheets manually, while keeping the information coordinated. As a result, spreadsheets didn’t match the drawings, engineers had to revise previous projects and couldn’t take on or complete new projects.
Life with Eziil
Vertex compiled standard product structures into Eziil, which makes preparing a new project much faster. With advanced versioning, redesigning projects or making additions according to the client input is easy, while keeping track of the change history, as well as the original version. The engineering can be sure that the right version ends up in production.
4. Employee satisfaction
Previously the production team was unhappy since the same type of mistakes repeatedly ended up in production. The engineering team was also unhappy since they constantly had to put out production fires and couldn’t focus on the upcoming projects. Assembly workers had to go back-and-forth between engineers to make sure which parts are connected where and which are the right drawings. All in all, no one could work efficiently, people were wasting time on double-checking their assignments and could never be sure that they had all the relevant information.
Life with Eziil
With Eziil BOM, all parties have a clear understanding and the same information to work with confidence. When making changes, one can be sure that they’re reflected in all necessary materials. Also, the assembly workers know where to get the right drawings from and can find and print out the necessary material themselves, without playing the telephone game with other departments.
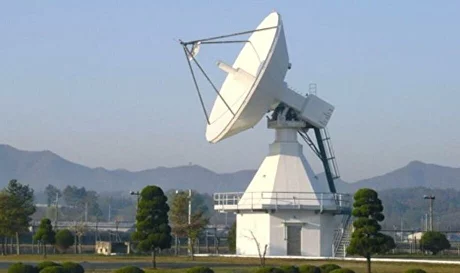
11,2 m Full Motion Antenna in Korea
It’s also worth noting that a simple and modern UI makes everyday work more motivating and enjoyable. Tamur says that onboarding new people has become surprisingly easy: “Several new people have learned everything they need by watching video tutorials. We only had to walk them through very Vertex-specific nuances, like fastener margins and stuff like that.”
5. Shifting toward more complex and higher-value-added projects
Due to its location, Vertex can’t expand physically and increase their production capacity. Thus, the company has to grow through shifting to higher value-added projects. Yet more advanced and complicated projects call for a best-of-class project technology preparation. As they already had constant misunderstandings and disorder with their maze of spreadsheets, taking on even more complicated projects seemed like mission impossible.
Life with Eziil
Eziil has been a great help with its systematicity, central database and good overview of the products. Artur notes that they feel much more confident in accepting challenges: “We can take on more difficult projects with more components and be sure that we won’t forget or mix anything up. We’d definitely recommend Eziil to all the companies with complex projects consisting of many materials and components.”
whats next?
With engineering covered, Vertex is moving on to digitizing their purchasing. Artur says that implementing the Eziil procurement module is the next logical step: “Effectively managing our supply chain will make sure that nothing stands in the way of our production.”
Are you looking for the right BOM tool for your metal production?
Book a 60-minute demo and see Eziil in action.