‘Break sharp edges’ is a common note you will find while looking at a variety of manufacturing prints as either a manufacturer, or an engineer. The note ‘break sharp edges’ implies the application of a finishing process for parts created through one of several different manufacturing processes. A ‘sharp edge’ is also known as an edge that contains small imperfections which can create a sharp surface, and these imperfections are commonly referred to as burrs.
In this article, we will cover what the removal of sharp edges implies (also known as deburring), what manufacturing processes can create a burr, the types of processes commonly used to remove burrs, why the removal of burrs (sharp edges) is important, and proactive approaches to help reduce the likelihood of burrs from being created while manufacturing. We’ll delve into how the break edge technique is essential in ensuring the quality and safety of manufactured parts.
What is Deburring?
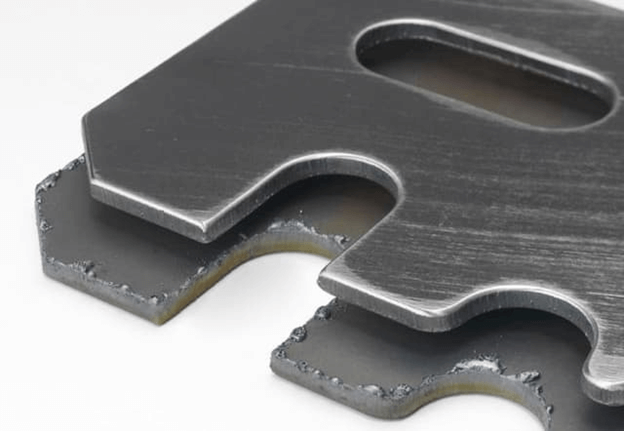
Picture credit: https://www.rapiddirect.com
Stated simply, deburring is the process of removing burrs. As stated previously, deburring is generally synonymous with the phrase, “Break sharp edges”, and it is the process of removing small imperfections on edges of materials, typically metals, as the are manufactured.
Deburring is considered a finishing process when coupled with polishing but can also be used as a post-operation process in preparation for the final finishing process of the part.
Also learn more about Chamfering!
What Causes a Burr?
Burrs can be caused by multiple processes, with the primary cause being machining operations on either a mill or lathe. Other processes that can cause burrs to appear are:
• Laser, water, and plasma cutting where the burr is caused by the occurrence of ‘kerf’ which refers to the imperfections created by the cutting process itself.
• Casting, sintering, and molding processes where flashing is present.
• Drilling, engraving, and other machining processes where metal is removed utilizing another metal tool which can roll material and fracture it.
• Common sheet metal forming processes which roll, press, or extrude material into specific shapes which can result in imperfect edges and features.
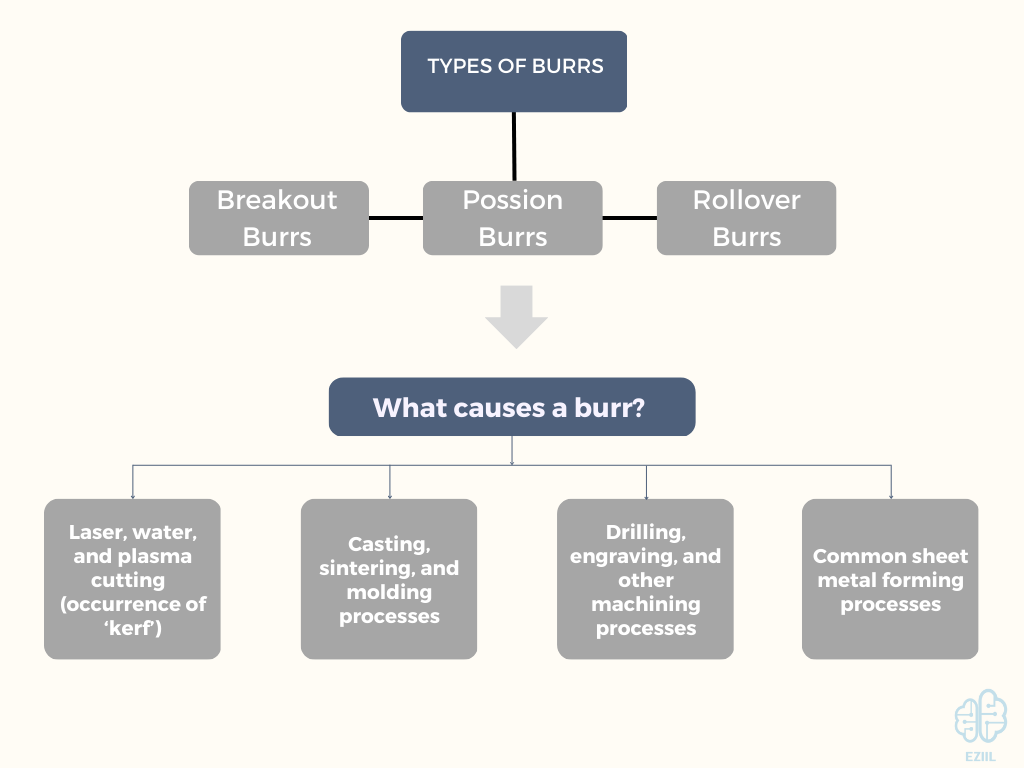
Burrs can be further classified into three distinct types:
• Breakout burrs are those that are caused when material is forced upwards out of a material, and they appear as though they are ‘breaking out’ of the part.
• Possion burrs are those that occur when metal collects at the end of a feature on the workpiece and extend sideways.
• Rollover burrs are the most common types of burrs and they have the appearance of a rolled or curled ‘string’ of metal protruding off the part.
Common Deburring Processes
When determining the optimal process for deburring, one should consider the volume of parts needing to be deburred, the materials that will be deburred, and the manufacturing processes that created the burr.
Manual Deburring
For unpredictable volumes of production requiring deburring, manual deburring tends to be the most economical. Manual deburring is the most common form of deburring found in industry, and it involves the use of various hand tools like rasps and files that are used by technicians to manually scrape or buff burrs off workpieces.
Thermal deburring
Thermal deburring is a process where gases are ignited in order to ‘burn’ the burrs from the workpiece. This process is highly effective when burrs are located in hard to reach places as well as parts that have burrs in multiple locations. While this process is effective, it is not commonly seen in industry.
Mechanical deburring
Mechanical deburring is the second most common form of deburring behind manual deburring, and it involves many of the same tools, but in this process the tools are powered and require less physical exertion from the operator. Grinding wheels, die grinders, and rotary tools are a few examples of the types of tools that perform these tasks. These tools are typically powered by an electric motor or pneumatics.
Electrochemical deburring
Electrochemical deburring is a process where a conductive solution of liquid is used to pass current through workpieces. This current carries electrochemical energy that performs similar to that of thermal deburring, whereas the burrs are blasted off leaving the surrounding metal in-tact. As with thermal deburring, this process is rare and works best with specialty metals like titanium and alloys, and is effective when need to remove burrs from hard to reach areas.
Automated deburring
Automated deburring is becoming more and more common, and it typically involves the use of a CNC machine that performed the initial machining operations. When the machining process is completed, the machine will swap out its tooling for tools that are specifically made for deburring the part, and the machine runs the a program just as it did when machining the part, but with the intent of deburring. This level of automation is being seen more frequently as labor rates increase and ease of CNC machine programming increases through CAM software.
Deburring Tools
Deburring tools are specialized tools used in product design and mechanical engineering to remove burrs and sharp edges from metal parts. They come in various shapes and sizes, including cylindrical, conical, and spherical, and are made from materials such as aluminum oxide and silicon carbide.
Deburring Machines
Deburring machines are specialized machines used in product design and mechanical engineering to remove burrs and sharp edges from metal parts. They use various methods, including rotary deburring and brush deburring, and are essential for achieving high-quality and safe products.
Book a 60-minute demo to see
how eziil mrp solution works for you
Samples of common deburring processes and machines:
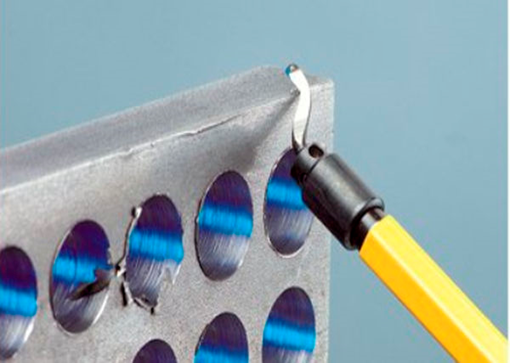
1. Manual Deburring – small part that you want to deburr.
Source: https://www.rapiddirect.com
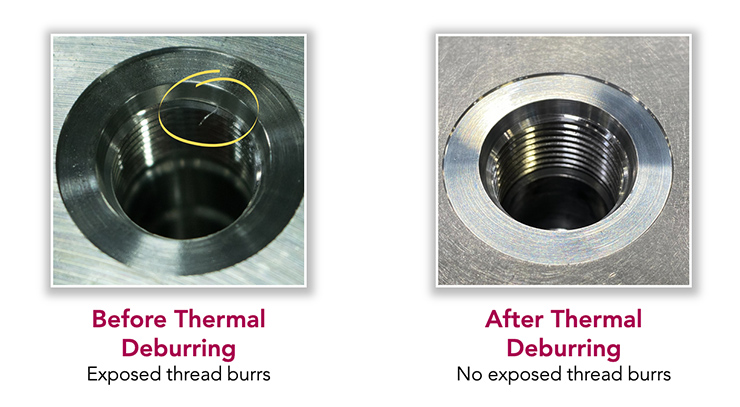
2. Thermal deburring – before and after.
Source: https://www.mobilehydraulictips.com
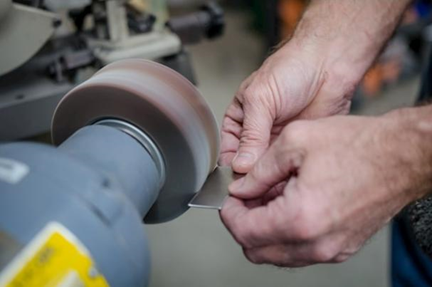
3. Mechanical method of removing burrs.
Source: https://www.rapiddirect.com
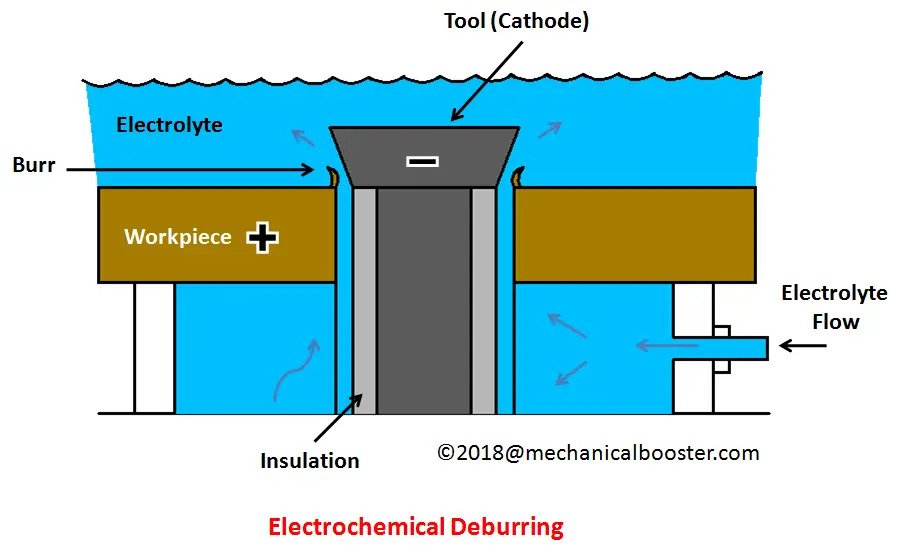
4. Electrochemical deburring process
Source: https://www.mechanicalbooster.com
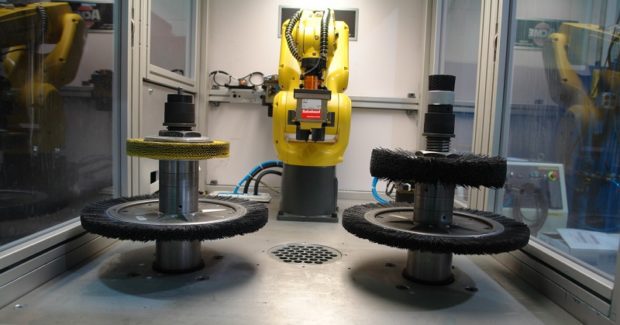
5. Automated brush deburring machine.
Source: https://www.fabricatingandmetalworking.com
Why Burrs Need to be Removed?
Burrs need to be removed for several functional reasons as well as multiple safety reasons. A burr can cause acute damage to mating components, pose a cutting hazard to individuals handling the parts, and increase wear and tear on the part itself.
Below is a list of the most common reasons that burrs are removed when manufacturing parts.
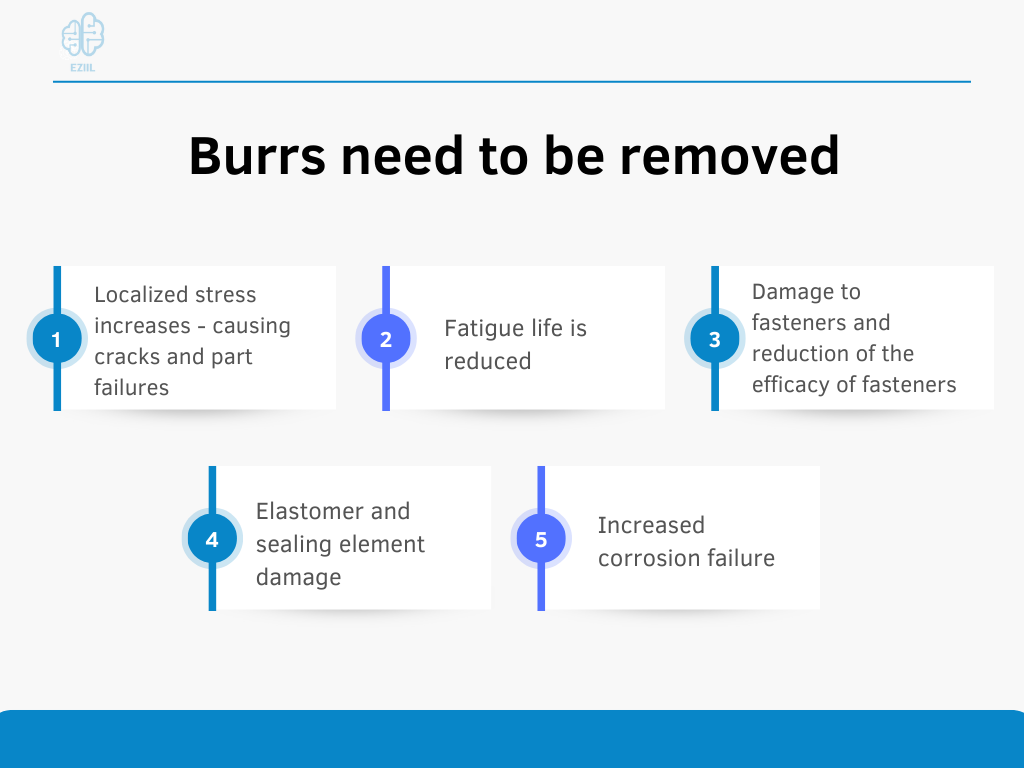
• Localized stress increases because of burrs, causing cracks to form as well as part failure in worst case scenarios.
• Fatigue life is reduced due to the crack propagation and additional wear and tear caused by the presence of burrs.
• Damage to fasteners and reduction of the efficacy of fasteners due to uneven seating surfaces being present as a result of the burrs.
• Elastomer and sealing element damage caused by burrs found in internal groove geometries. This damage can lead to increased safety hazards are seals prevent over pressurization, chemical leaks, and gas evacuation.
• Increased corrosion failure. As cracks and crevices are formed by burrs, catch points for chemicals that can erode material strength become present and hold onto corrosive liquids that would have otherwise slid off the part.
Cutting Edge
The cutting edge is the sharp edge of a cutting tool that is used to remove material from a workpiece. In metalworking, the cutting edge is essential for achieving precise and accurate cuts. However, it can also create sharp edges that need to be removed to ensure the safety of the end-users.
Laser Cutting
Laser cutting is a popular method for cutting metal parts in product design and mechanical engineering. It uses a high-powered laser beam to melt and vaporize the metal, creating a clean and precise cut. However, the cutting edge can still create sharp edges that need to be deburred.
Aluminum Oxide
Aluminum oxide is a commonly used material in deburring tools. It is a hard and abrasive material that is ideal for removing sharp edges and burrs from metal parts.
Silicon Carbide
Silicon carbide is another commonly used material in deburring tools. It is a hard and abrasive material that is ideal for removing burrs and sharp edges from metal parts.
Cutting Tool
A cutting tool is a tool used in metalworking to remove material from a workpiece. It can include tools such as saws, drills, and milling machines, and must be sharp and precise to achieve accurate cuts.
Production Process
The production process in product design and mechanical engineering refers to the series of steps involved in creating a finished product. Break edge is an essential consideration in the production process, as it ensures the safety of the end-users and the quality of the finished product.
How to Reduce the Likelihood and Negative
Impacts of Burrs?
Burrs can be caused by poor feeds and speeds in CNC programs, improper die geometries in stamping operations, and underpowered cutting systems. Ultimately, burrs cannot be removed completely from manufacturing processes, but the likelihood of their appearance can be reduced by employing industry standard machining practices like the employment of cutting fluids which are specialized lubricants applied during machining operations.
Automatic deburring can also prevent the need for post processing beyond the manufacturing operation occurring. This approach is usually the easiest for manufacturers who already run CNC machines with programmed operations, as it typically requires one additional program being made and a small investment in new tooling.
The other primary strategy to reducing the negative impact of the deburring process is to incorporate deburring into your finishing process. This implies utilizing finishing tools that are also capable of deburring your parts while simultaneously cleaning them and finalizing their appearance and surface finish.