Welding is a skill that’s much in demand today. And with so many segments of our economy relying on it, there is no reason to believe that will change anytime soon. Buildings, vessels, and automobiles are some of the items where welding is the key to their construction, but they represent a small percentage since so many other things are built using metal that requires some welding.
Bad weld can cause anything from a minor annoyance to a complete catastrophe, so they must be recognized and repaired or prevented in the first place. However, determining whether a weld is good or bad can be complicated. Still, it is essential to be able to do so since welding in industries such as constructions building means lives depend on practical and durable welds.
Usual Criteria to Help You Identify
Weld Quality
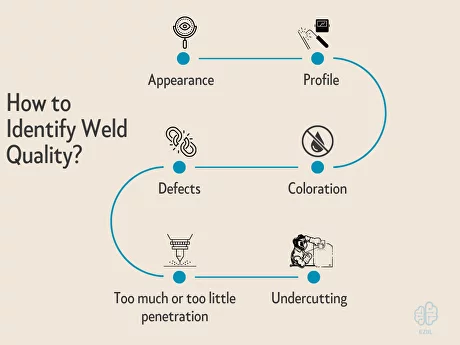
- Appearance: Welds should have a smooth and uniform appearance.
- Profile: Depending on the application, welds must be flat, concave, or convex.
- Coloration: An acceptable weld will have a color-free appearance, indicating no oxidation.
- Defects: Two of these are porosity caused by contamination of the weld and craters from a rapid reduction in the current.
- Too much or too little penetration: If the weld penetrates too little, the joint will be weak, and if it over-penetrates, the backside of the joint could have a poor finish.
- Undercutting: If the parent metal thins at the edges of the weld, it typically indicates filler metal relative to the current.
What are the Signs of Good and Bad Welds in
Different Techniques?
Metal Inert MIG
Metal inert MIG is one of the most frequently-chosen welding methods.
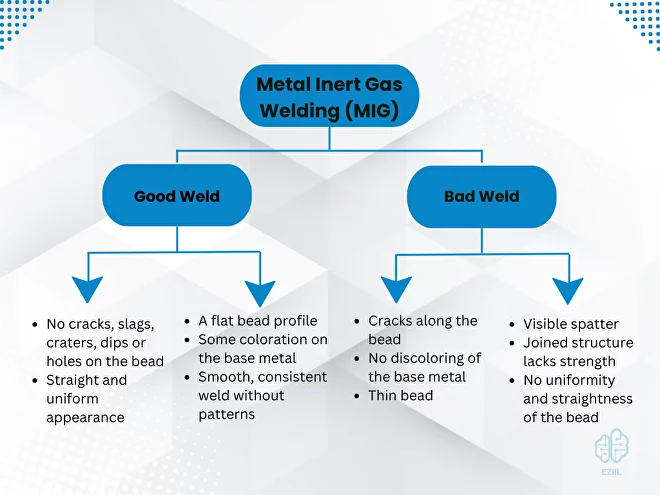
Let’s look at the signs of a good MIG weld:
- No cracks, slags, or holes on the bead
- A smooth, consistent weld without patterns or discoloration
- Some coloration on the base metal
- A flat bead profile, which is neither concave nor convex
- Straight and uniform appearance
- No craters or dips in the bead
How can you spot a bad MIG weld?
- No uniformity and straightness of the bead
- Cracks along the bead
- No discoloring of the base metal
- Thin bead
- Visible spatter
- Joined structure lacks strength
Tungsten Inert Gas Welding (TIG)
TIG is considerably more challenging to achieve and requires a higher skill level before producing quality welds. It is a technique used on various metals, including stainless steel, aluminum, magnesium, and copper alloys, and quite frequently in the aerospace industry.
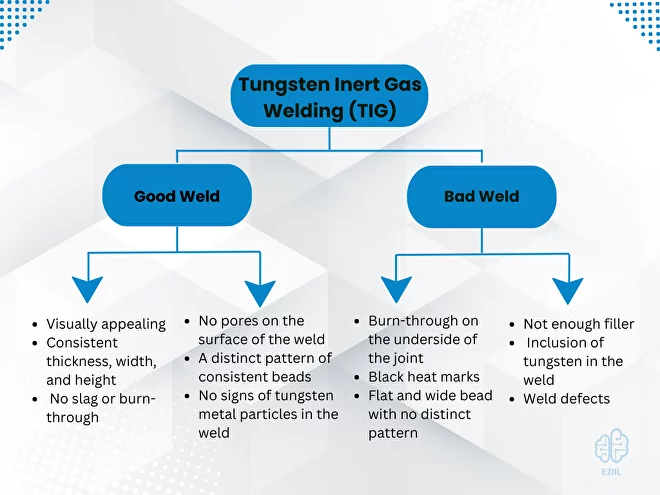
A good TIG weld has the following characteristics:
- No signs of tungsten metal particles in the weld
- A distinct pattern of consistent beads
- No pores on the surface of the weld
- No slag or burn-through
- Consistent thickness, width, and height
- Visually appealing
A bad TIG weld will show the following flaws:
- Burn-through on the underside of the joint
- Black heat marks that are difficult to remove
- Flat and wide bead with no distinct pattern
- Not enough filler
- Inclusion of tungsten in the weld
- Weld defects
Shielded Metal Arc Welding (Stick Welding)
Stick Welding is relatively easy to learn and works with several materials, including carbon steel, stainless steel, cast iron, copper, and aluminum.

The following are signs of good stick welds:
- Consistent thickness
- No spatter
- Straight and uniform bead
- No holes or cracks in the bead
Poor stick welding techniques may result in the following:
- Inconsistent bead width and height
- Slag on the weld surface
- Weld defects, such as cracking, undercutting, or breaks in the bead
- Spatter
Book a 60-minute demo to see
how eziil mrp solution works for you
Professional Welds Inspection Tools
The following are commonplace weld inspection methods and procedures:
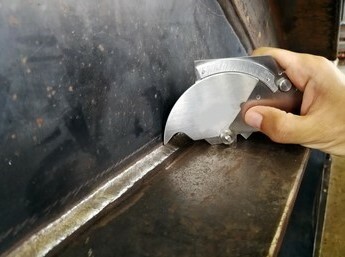
Source: https://www.smartveritas.com
Visual Inspection
Visual inspections are the most common and cost-effective way of testing welds. Weld inspectors must have significant experience and knowledge from years of hands-on welding to visually inspect a weld and understand the difference between acceptable appearance and welding defects.
Immediately after welding, operators perform the first visual inspection, looking for obvious defects, uneven weld beads, undercut edges, and other inconsistencies. However, remember that a weld that doesn’t look good isn’t necessarily a bad weld. Other tests, such as those listed below, can find hidden flaws (or the absence of them) more reliably than a visual inspection.
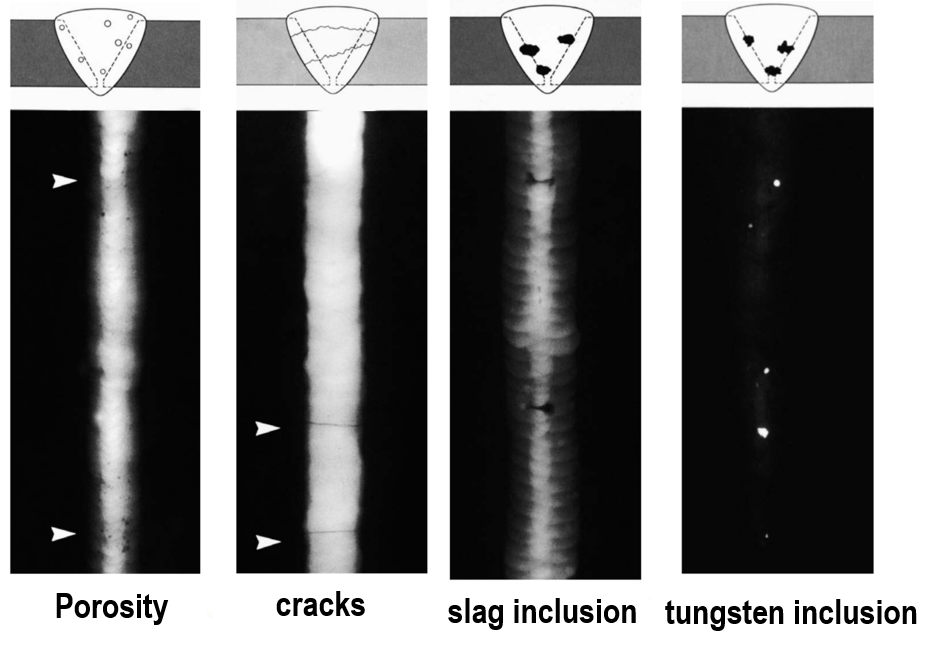
Source: https://www.orangecoasttesting.com
X-Ray Inspection
Also called radiographic inspection, x-rays are an accurate and efficient inspection method. The process uses gamma rays to pass through the weld and the surrounding base metal. Experienced inspectors look at the x-rays and can determine if a weld meets strength requirements or contains deformities or defects.
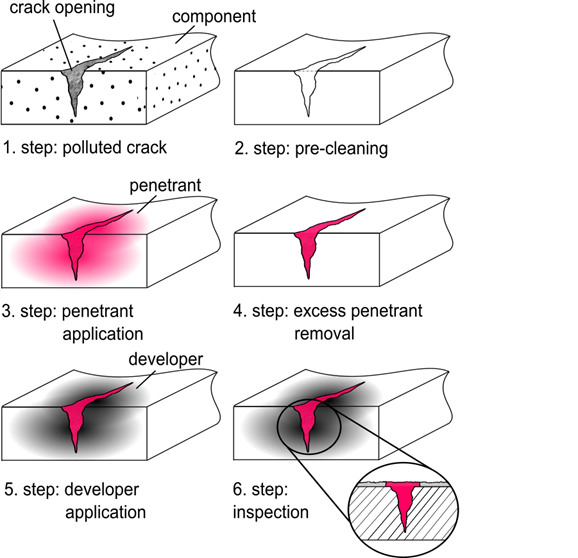
Source: https://yenaengineering.nl
Liquid Penetration
This inspection method involves spraying a brightly colored liquid dye over the weld and left to soak in after it has cooled. After a short period, an inspector can see any irregularities or defects in the weld since the liquid’s color will change, usually becoming darker in the area of a crack or hole.
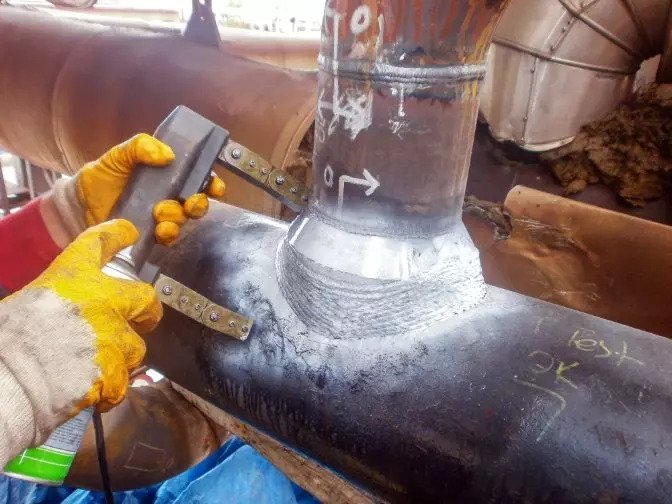
Source: https://www.flyability.com
Magnetic Particle Inspection
Probes are placed on either side of the inspection area, allowing amperage to pass through the material. Whenever the amperage encounters a discontinuity, the probes are diverted, and amperage leaks to the surface, creating magnetic poles and allowing the inspector to determine the location of the irregularity.
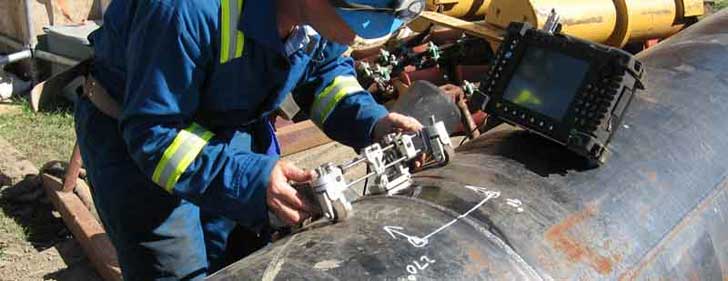
Source: https://www.wermac.org/others
Ultrasonic Weld Inspection
With ultrasonic testing, a high-powered mechanical frequency beams into the weld, and if it strikes a discontinuity, it is reflected to a transducer (receiver). The signal is measured to help determine the size, shape, and type of weld failure. This method is effective at finding internal discontinuities but requires exceptional operator knowledge and expensive equipment.
Producing Strong and Reliable MIG Welds: Best Practices and Common Pitfalls
MIG welding is a popular welding technique used in a wide range of welding projects, from automotive repair to metal fabrication. When performed correctly, MIG welding can produce strong, reliable welds that can withstand significant stress and strain. However, when performed incorrectly, MIG welding can result in bad welds that are weak, unsightly, and potentially dangerous.
One of the most important factors in producing a good MIG weld is selecting the appropriate welding wire and filler metal for the job. Welding wire comes in a variety of sizes and compositions, and choosing the right one for the specific application is critical for producing a high-quality weld. Similarly, selecting the appropriate filler metal can ensure that the weld is strong and resistant to cracking and other forms of failure.
Another key factor in producing a good MIG weld is maintaining proper weld bead size and shape. The weld bead is the visible part of the weld, and ensuring that it is uniform in size and shape can help ensure that the weld is strong and consistent. This requires careful attention to the welding gun angle, travel speed, and wire feed rate.
Despite the best efforts of even the most skilled welders, bad welds can still occur. Common causes of bad welds include incorrect welding wire and filler metal selection, improper welding gun angle, insufficient travel speed, and incorrect wire feed rate. Bad welds can result in weak, unsightly, and potentially dangerous welds that can compromise the structural integrity of the welded part.
In order to prevent bad welds from occurring, it is important to carefully inspect the weld after it has been completed. This can include visual inspection of the weld bead, as well as non-destructive testing techniques such as magnetic particle inspection. In cases where bad welds are identified, they can be corrected by grinding out the bad weld and re-welding the joint with the appropriate welding wire and filler metal.
In conclusion, producing a good MIG weld requires careful attention to welding wire and filler metal selection, as well as proper welding gun angle, travel speed, and wire feed rate. While bad welds can still occur despite the best efforts of skilled welders, they can be prevented through careful inspection and correction of any identified issues. By following best practices for MIG welding, welders can produce high-quality welds that are strong, reliable, and visually appealing.
Turning Bad Welds into Good Welds
Welding techniques and settings are typically the primary sources of bad weld, which can be countered by improving a welding operator’s techniques, set-ups, and knowledge base.
Welding operators can take steps to avoid bad welds and produce good welds by adopting the best practices and techniques. This means not only selecting the correct welding process and settings, but also ensuring that the welding gun is properly positioned and that the filler metal is added consistently. A good weld should be visually appealing, with a smooth and uniform weld bead that shows proper fusion and penetration. Bad welds, on the other hand, may contain defects like porosity, pinholes, or slag on the weld surface, which can compromise the strength and reliability of the weld. By focusing on producing good welds and avoiding common pitfalls, welders can improve the quality of their work and ensure that their projects are built to last.
Additionally, you can learn more about “Welding defects to watch out for” on our blog.