Several metal-working processes, including laser and water jet cutting, are available as profile-cutting techniques for manufacturers. However, it’s more likely that you’ll see a plasma cutter sitting on the floor of the average metal fabrication shop.
Why? Because plasma metal cutting has several advantages over other methods, including cost-effectiveness, enhanced productivity, higher precision, and repeatability. Also, the plasma cutter machine works on any conductive material and various thicknesses.
But first…
What is Plasma?
As you probably already know, the three states of matter are solid, liquid, and gas. However, plasma is often called the fourth state of matter, commonly occurring throughout the galaxy.
Plasma forms when additional energy is added to a gas, allowing its molecules to move faster and collide with more force. These collisions enable the molecules to separate into their basic atoms, separate from their outer shell electrons, and form ions.
At this point, the ionized gas becomes plasma.
What Does a Plasma Cutter Do?
Plasma cutting, a method of metal fabrication, utilizes ionized gases heated to over 20,000°C to melt various metal materials.
Although mentioning plasma steel cutting causes most people to envision a 4 ft. x 8 ft.
CNC plasma machine cutting profiles from digital files, plasma cutting can be a manual operation using a hand-held plasma torch.
Regardless of the technology (or lack thereof), the plasma torch-cutting process is essentially the same.
How Does a Plasma Cutter Work?
Plasma cutting employs heat to melt metals rather than relying on mechanical methods. The process operates by transmitting an electric arc through a specific gas, allowing for precise cutting
Plasma cutting involves using heat (typically over 20,000 degrees C) to melt metal rather than cut it mechanically. The plasma arc cutter sends an electric arc through a plasma-cutting gas before passing it through a constricted opening called a nozzle.
As the gas squeezes through the restricted nozzle opening, it picks up speed and elevates the temperature, forming plasma.
The gas is ejected under such high pressure that it melts the workpiece material and forces it from the cut.
In the intricate world of plasma cutting, the role of compressed air cannot be understated. By channeling compressed air through an air compressor, the plasma cutter efficiently generates the necessary heat to slice through metals with remarkable precision.
It’s this reliance on compressed air, paired with the capabilities of modern air compressors, that allows for the numerous advantages of plasma cutting.
Yet, like any tool, understanding its strengths and limitations is essential for optimal results.
However, not every cutter machine works the same.
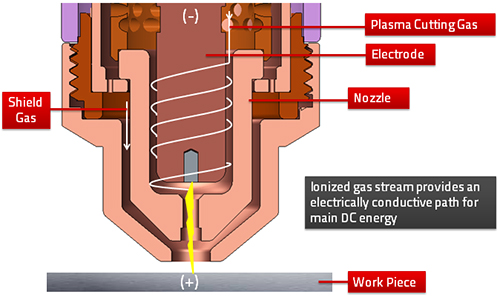
Three TYpes of Plasma-Cutting Processes
High-Frequency Contact: This method is cost-effective but can’t be used with CNC plasma equipment. High-frequency contact cutting involves a high-frequency spark and high voltage that risks interfering with the CNC control and causing issues. The spark forms when the plasma torch contacts the metal, closing the circuit, initiating the spark, and creating the plasma.
Pilot Arc: This process creates the spark inside the torch using a low current circuit and high voltage. The spark creates the pilot arc, and contact with the workpiece creates the cutting arc.
Spring Loaded Plasma Torch Head: Pressing the torch against the workpiece creates a short circuit, which starts the current to flow. The operator releases the pressure to establish the pilot arc.
Book a 60-minute demo to see
how eziil mrp solution works for you
Which Gases are Involved in Using Plasma Cutter Technology?
The gas type depends on the cutting method, material, and thickness.
The most common gases used for plasma cutting include the following:
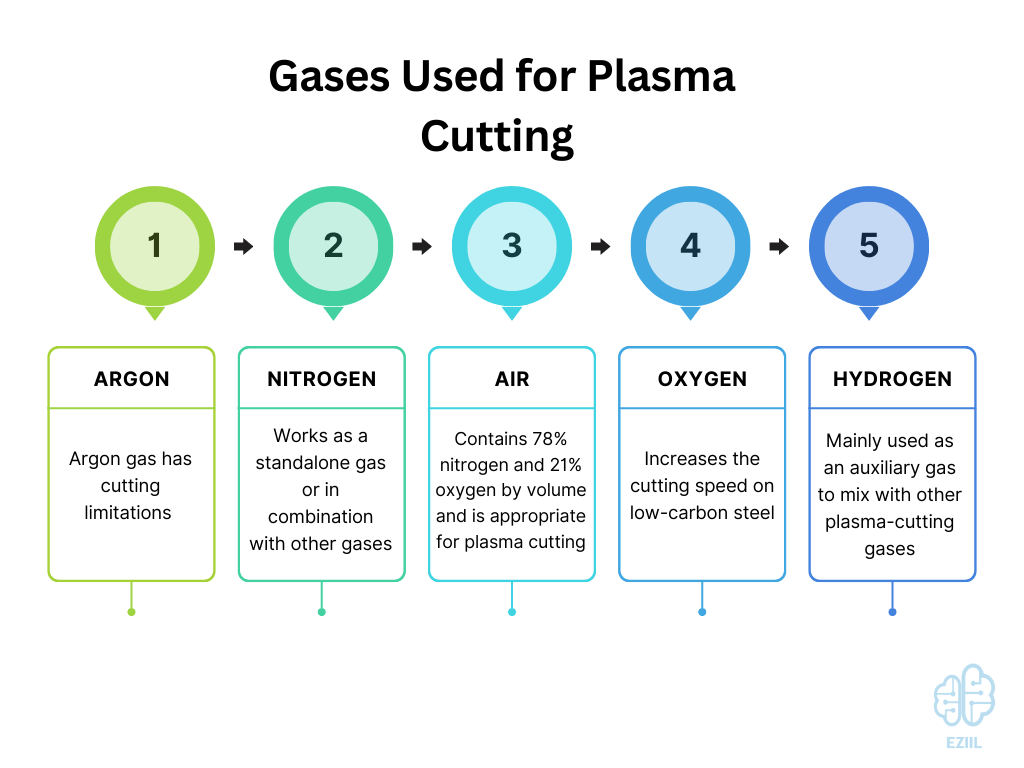
Argon is an inert gas with a stable plasma arc, meaning it reacts very little with most metals at high temperatures. However, argon gas has cutting limitations because of its low plasma arc and slag issues caused by higher surface tension. These problems result in argon being rarely used for plasma cutting.
Nitrogen has better plasma arc stability and a higher energy jet than argon. It forms minimal slag, even when cutting metals like nickel-base alloy and stainless steel with high viscosity. It works as a standalone gas or in combination with other gases, facilitating the high-speed cutting of carbon steel.
Air contains 78% nitrogen and 21% oxygen by volume and is appropriate for plasma cutting. The oxygen constituent of air makes it one of the fastest gases for cutting low-carbon steel and the cheapest. On the negative side, electrodes and nozzles used with air typically have a short service life, and air as a standalone gas causes slag hanging and cut oxidation.
Oxygen, like air, increases the cutting speed on low-carbon steel, although using it with high-temperature and oxidation-resistant electrodes produces better results.
Hydrogen is mainly used as an auxiliary gas to mix with other plasma-cutting gases. The most oft-used combination is hydrogen and argon, which produces a potent plasma-cutting gas.
How to Plasma-Cut Various Materials
As mentioned, the plasma cutting process works on any conductive material, and here are the most common:
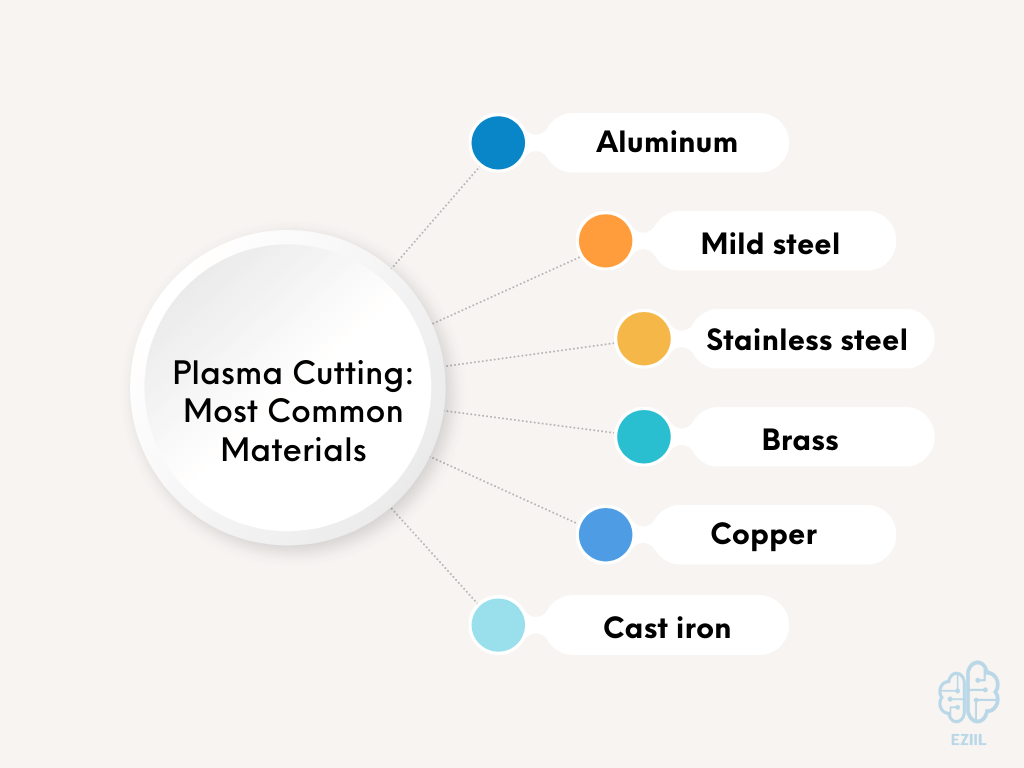
- Aluminum being conductive makes it ideal for plasma cutting, and the process offers advantages with thicker metals compared to other methods. It can cut aluminum thicknesses up to 160mm (6-3/8″) cost-effectively.
- Mild steel is inexpensive, versatile, and weldable, lending to plasma cutting and metal fabrication.
- Stainless steel is corrosion and rust-resistant, and plasma cutting works on plates up to 30mm (1-3/16″) thick and in various grades.
- Brass is another metal easily fabricated using plasma cutting because it’s highly conductive. However, the process should occur in a well-ventilated area since brass contains zinc, and inhaling burning zinc’s fumes is detrimental to health.
- Copper has excellent electrical conductivity and essential qualities, including corrosion resistance, high ductility, and weldability. However, like brass, it must be cut in areas with adequate ventilation.
- Cast iron is popular for its low cost and malleability. It is very conductive, with high compressive strength and low melting temperature making it ideal for plasma cutters.
What is Plasma Cutting Welding?
It can be confusing, but plasma cutting and plasma welding are two distinct processes using plasma technology to manipulate the shape of metals. As we’ve shown, plasma cutters use high-velocity streams of hot gas—argon, nitrogen, or oxygen–to cut through metal.
On the other hand, plasma welding is similar to plasma cutting, but it uses electricity generated from a high-frequency arc welder to join two pieces of metal. Plasma welding requires significantly more skill and precision since it involves combining two parts rather than simply cutting them apart.
What are the Disadvantages of Plasma Cutting?
Although plasma cutting has many benefits over other fabrication methods, there are a few disadvantages, including:
- It can only be used for conductive materials
- Not ideal for metals thicker than 150mm (around 6″)
- Bright flashes during cutting could have a damaging effect on the eyes
- The operation can be noisy, so hearing protection is needed
- Typically produces fumes, so it should only be used in a well-ventilated area
- It could be expensive when using low-life consumables such as nozzles and electrode
Conclusion
The plasma-cutting process involves using the fourth stage of matter (plasma) to cut conductive metals. The process offers several benefits, including versatility, precision, surface quality, lower equipment costs, and higher productivity.
To maximize the potential of plasma cutting and its alternatives, the right software is paramount. Ensuring you’re equipped with the best tools is as essential as selecting the appropriate cutting method for your manufacturing endeavors.
In the realm of steel manufacturing, plasma cutters have revolutionized the way we approach metalwork. These plasma cutters, designed for precision and efficiency, offer unique advantages over traditional cutting methods.
The technology within plasma cutters ensures cleaner cuts, while the versatility of a plasma cutter allows for use on a wide range of metals. Despite its benefits, not every job is suitable for a plasma cutter – laser cutting, waterjet, or oxy-fuel cutting—may work better.
Understanding when to use plasma cutters, and the nuances of each plasma cutter model, can be the key to achieving the desired results. As with any tool, mastering the use of plasma cutters requires insight into both its strengths and limitations.
Whether you’re a novice or an expert, the evolution and potential of plasma cutters in today’s industry cannot be overlooked.