Few things annoy a welder as much as weld porosity, yet most have experienced these welding defects at one time or another. The frustration from porosity comes from knowing that it usually affects the weld’s overall strength and integrity and will require remedial action to bring the weld up to the standards of international weld codes.
Fortunately, it is possible to repair porosity, although it’s much preferable to prevent it in the first place. Let’s look at the characteristics of porosity, its causes, and ways to avoid or minimize it during fabrication:
What is Welding Porosity?
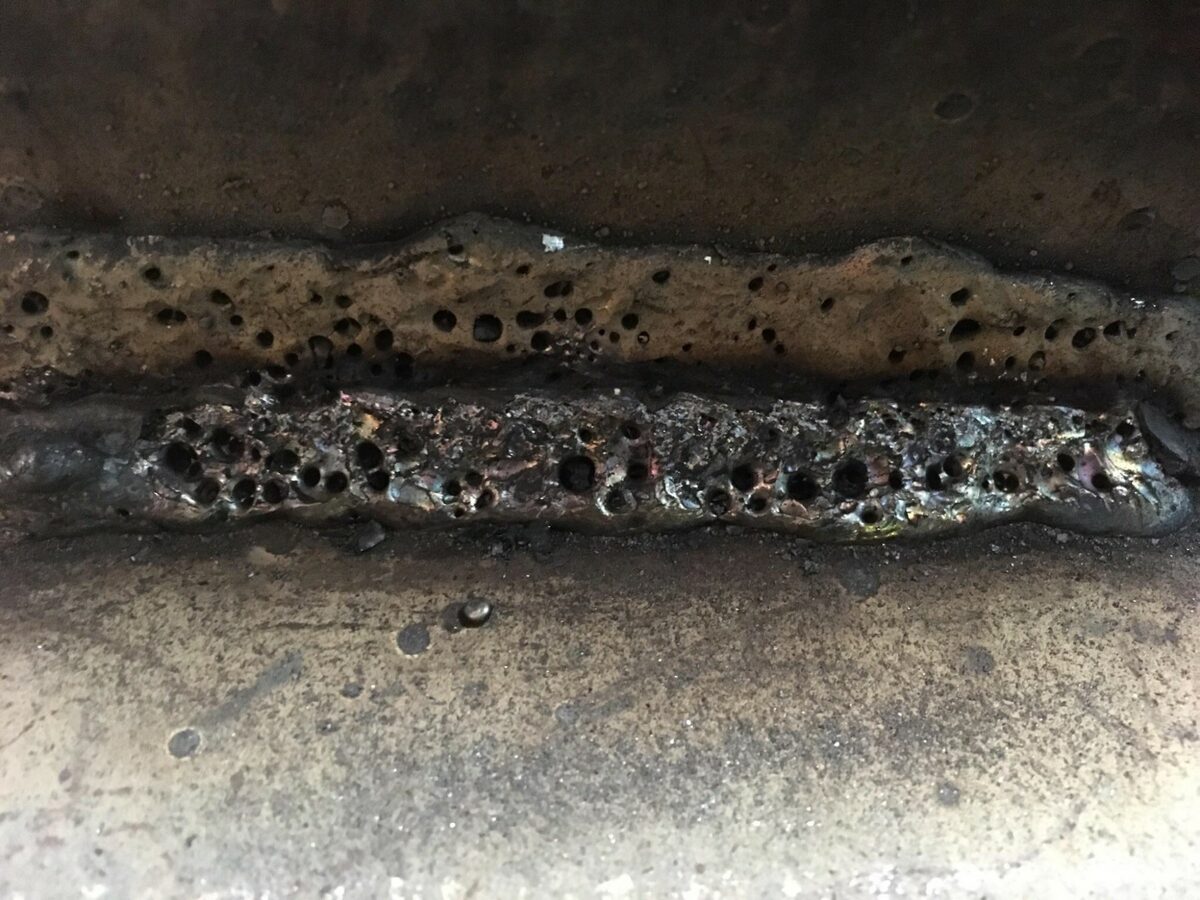
Source: https://www.linkedin.com/pulse
Porosity is a weld defect referring to unwanted trapped gases (often oxygen) within a welded joint. It typically occurs as the weld cools and solidifies. The gas either enters the weld and becomes trapped internally, forming pockets, or is forced from the weld, manifesting as visible holes and pits on the weld’s surface.
Porosity in Welding
Porosity in welding refers to the presence of small voids or holes in the weld bead or the surrounding area. These voids can weaken the weld and reduce its overall integrity, which can ultimately compromise the structural integrity of the entire welded component.
Weld porosity can occur in all types of welding, including MIG welding, TIG welding, and stick welding, and it can be caused by a variety of factors. One of the most common causes of porosity is inadequate protective gas coverage, which can lead to oxidation of the molten metal and the formation of gas bubbles within the weld.
Another common cause of porosity is moisture contamination in the welding wire or the base material. Moisture can vaporize during the welding process, creating gas pockets that can become trapped within the weld.
Porosity can also be caused by improper welding techniques, such as incorrect travel speed, incorrect heat input, or improper electrode manipulation. In some cases, it can be caused by a combination of these factors.
To prevent weld porosity, it is important to use the correct welding techniques and to ensure that the welding equipment and materials are in good condition. This includes properly cleaning and preparing the base material, using the correct welding wire, and ensuring that the shielding gas coverage is adequate.
Why Does Porosity Form?
Porosity forms for various reasons. Some of the common causes include:
- Failing to remove contamination from the base metal
- Improper shielding gas allowing the atmosphere into the weld pool
- Issues with the welding machine
- Incorrect welding technique
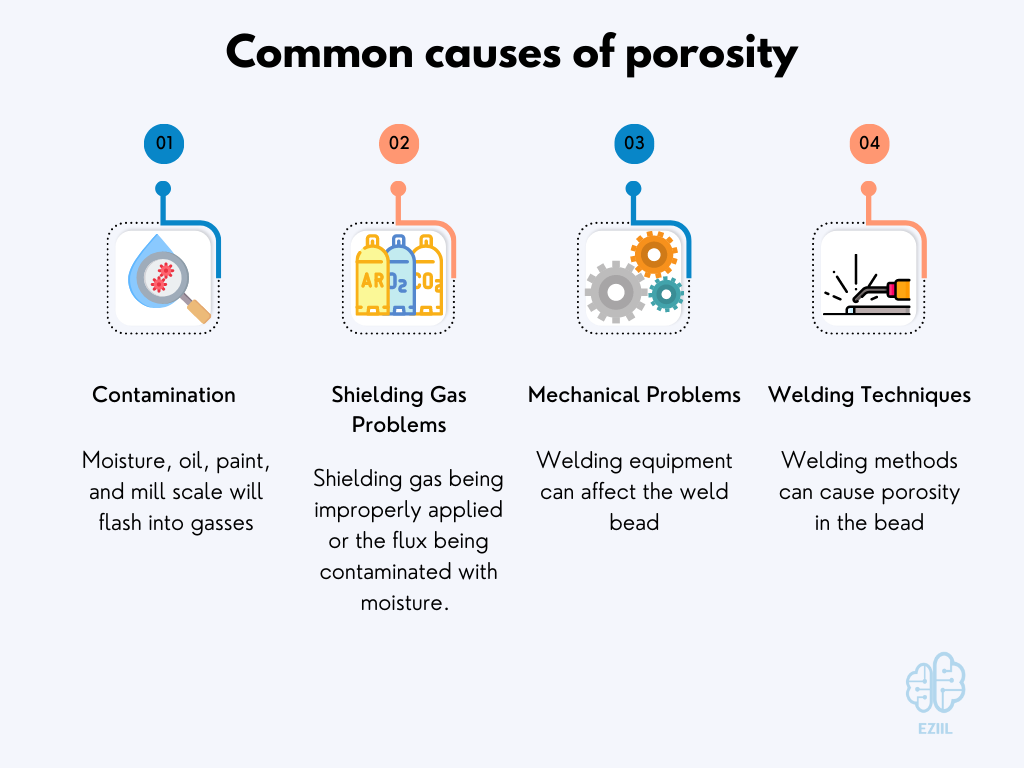
Contamination
Contaminants such as moisture, oil, paint, and mill scale will flash into gasses and can become trapped in the solidifying weld pool.
Shielding Gas Problems
Shielding gas or flux protects the weld pool from reacting with the atmosphere. However, porosity can be caused by the shielding gas being improperly applied or the flux being contaminated with moisture.
When too little shielding gas is used, the liquid metal reacts with the atmosphere trapping gasses, such as oxygen and nitrogen, within the weld pool and forming porosity.
Conversely, too much shielding gas flow pressure can also be a problem. When the gas flow rate is too high, it creates turbulence in the shielding area, pulling the atmosphere into it and resulting in porosity.
Mechanical Problems
Trouble with the welding equipment can affect the weld bead, with the most common issues being:
- Spatter-filled MIG liners interfering with the shielding gas
- Shielding gas contaminated by the supplier
- Cracked MIG liners, worn O-rings, or loose fittings allowing outside air into the shielding gas delivery system
Welding Techniques
Improper welding methods can cause porosity in the bead, and some of these include:
- Stopping a TIG bead too quickly and suddenly removing the shielding gas may cause a crater at the end of the bead.
- An extreme angle of a TIG torch or MIG stinger could prevent the shielding gas from surrounding the weld pool.
- Moving faster than the available shielding gas could also expose the puddle
MIG welding is a popular welding technique that uses a wire as the electrode and an inert gas as the shielding gas. When using MIG welding, it is important to select the correct welding wire based on the type of material being welded.
One common mistake in MIG welding is using the wrong type of welding wire. Using a wire that is not suited for the material being welded can result in poor weld quality and porosity.
To avoid weld porosity in MIG welding, it is important to ensure that the welding wire is clean and free from rust or other contaminants. Contaminated welding wire can lead to inconsistent welds and reduced strength.
Overall, MIG welding can be a highly effective welding technique when performed correctly, with proper selection of welding wire and careful attention to shielding gas and welding parameters.
What are the Different Forms of Porosity?
Although weld porosity is universally defined as a welding defect resulting from gasses trapped in the weld pool during solidification, causing pores and pockets on the surface and within the weld, it can take four common forms:
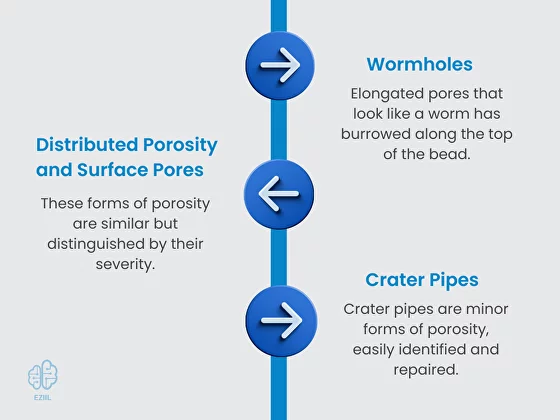
Book a 60-minute demo to see
how eziil mrp solution works for you
Wormholes
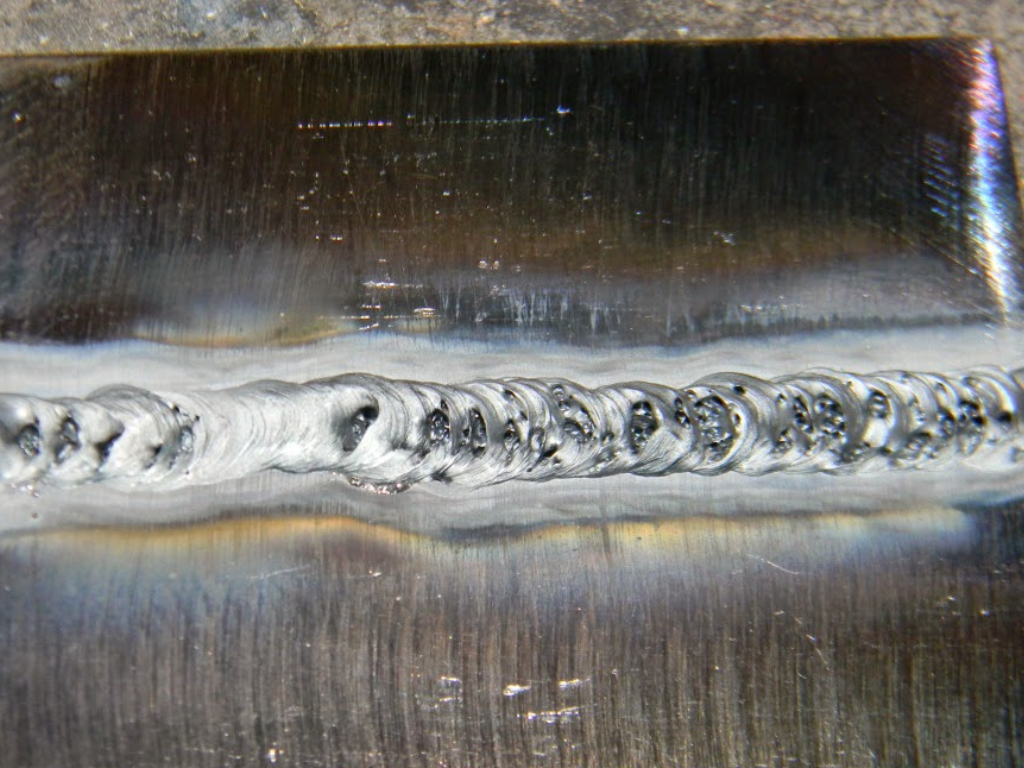
Source: http://cswipquestions.blogspot.com/
Named because they are elongated pores that look like a worm has burrowed along the top of the bead, wormholes occur when an excessive amount of gas forms and becomes trapped inside a weld pool as it solidifies. Removing surface contamination and coatings around the joint area will help eliminate the gas and prevent wormholes.
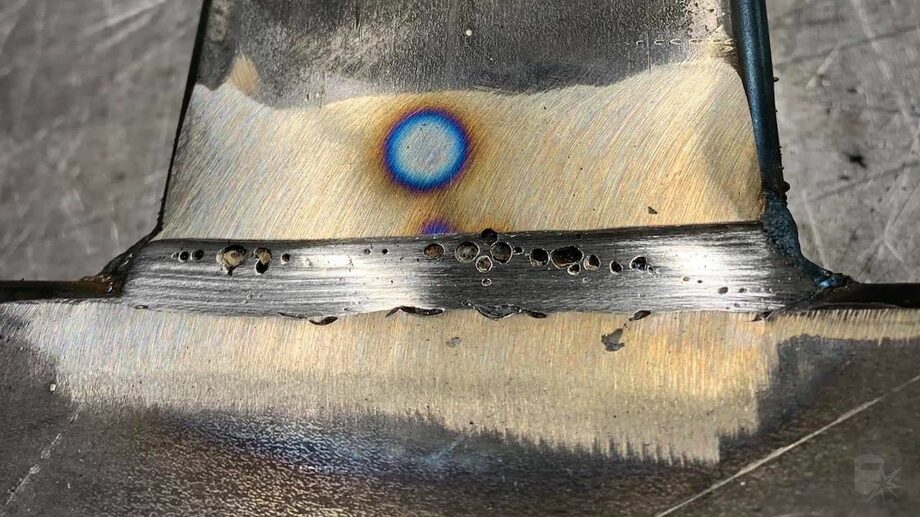
Source: https://weldguru.com
Distributed Porosity and Surface Pores
These forms of porosity are similar but distinguished by their severity. Distributed porosity is more difficult to identify and less severe. It consists of small pores trapped inside the weld bead, and x-raying is sometimes the only way to find it,
On the other hand, surface pores are visible to the naked eye and identifiable by the sizable holes they produce. They are considered severe defects and are frequently accompanied by internally distributed porosity.
Crater Pipes
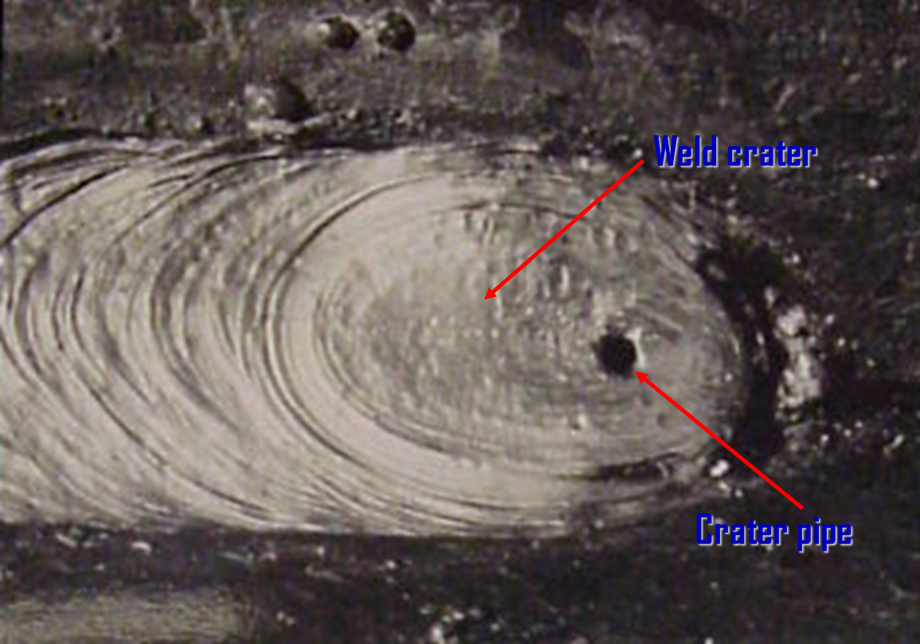
Source: http://cswipquestions.blogspot.com
Crater pipes are minor forms of porosity, easily identified and repaired. They show up during the final solidification process and look like pinprick holes having less effect on the weld’s structural integrity. They are easily preventable by using the correct downslope setting for your machine, or by allowing the cover gas to flow over the cooling weld a few seconds longer as the weld pool completely closes.
How Can I Prevent Most Welding Porosity?
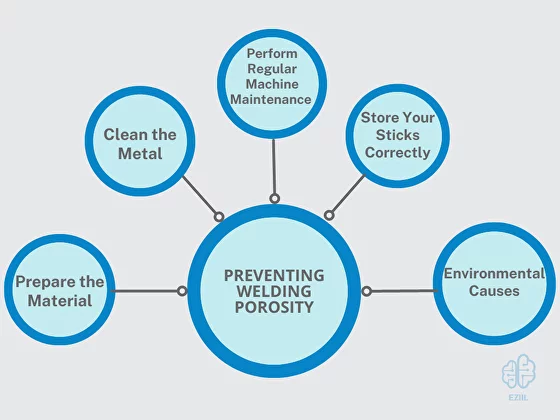
Even by doing everything right, you could run into the occasional defect, but here are a few steps you can take to minimize the chances of porosity:
Prepare the Material
Even though you might be able to weld through paints, primers, and other coatings with some welding methods, it’s typically preferable to weld clean metal, especially with TIG welding. Here are a few specific instructions:
- Grind, sand, or blast paint and coatings to reveal the bare base metal.
- Remove the mill scale from hot-rolled steel.
- Wire-brush aluminum to remove its oxide layer.
Clean the Metal
After removing the coating, clean the metal with a solution such as acetone, isopropyl alcohol, or lacquer thinner. Use a lint-free cloth to apply the cleaning solution, and wipe in one direction to prevent contaminants from spreading around the joint.
Perform Regular Machine Maintenance
Machine maintenance helps prevent porosity and contributes to the weld bead’s overall quality. Here are some maintenance suggestions:
- Clean excessive spatter from the contact tips and nozzles.
- Ensure that TIG gas lenses, diffusers, collet bodies, and O-rings are dirt-free.
- Clean and replace MIG liners often.
- Inspect the fittings on welders and regulators to confirm they are tight and clean.
- Clean your welding rods and wires before you use them.
Store Your Sticks Correctly
Moisture can contaminate stick electrodes, so keep them sealed in dry storage. If rods soak up moisture from the atmosphere, dry them in special rod ovens.
Environmental Causes
Open doors, fans, and even the cooling fans from a welder often create enough disturbance to cause pores in the bead. Try to minimize any air movement that might disrupt the protective gas.
Is It Okay to Weld Over Porosity?
Not usually. However, you can sometimes weld over pinholes (crater pipes) since it is a welding method issue and not contamination. It is especially recommended with TIG welding.
With the other forms of porosity, welding over the defect will likely continue the contamination across the weld bead. Another negative to consider: welding over porosity is quickly identifiable because it creates an unattractive weld.
How Should You Repair Porosity?
Use an angle grinder to remove the weld porosity carefully before rewelding the metal. It’s essential to grind out all the porosity since even if a tiny pore remains, it could show up in an x-ray. As you grind away the weld, try to create a neatly curved groove so that when you reweld the joint, you’ll have better control of where your filler wire sets.
Conclusion
Porosity is an irritation for beginners and seasoned welders, and no one is immune from it. Luckily, it can also be repaired and, in most cases, totally avoided with proper preparation and regular equipment maintenance.
In conclusion, weld porosity can be a frustrating challenge for welders of all levels. However, with proper preparation and regular equipment maintenance, weld porosity can be repaired and largely avoided. Remember, diligence is key to achieving flawless welds and minimizing the occurrence of weld porosity.