Welding applications are practically limitless, with different jobs requiring various welding joint types. Each welded connection is designed to withstand the forces and requirements of its specific application, making weld joint design a critical factor in producing quality welds.
The term “weld joint design” refers to aligning or connecting two metal pieces, and choosing the right design directly affects the quality, cost, and ultimate safety the weld provides.
The American Welding Society (AWS) The American Welding Society (AWS) recognizes the five most commonly-used welding joint types. Let’s look at them individually to help you determine which of them will be appropriate for your next welding project.
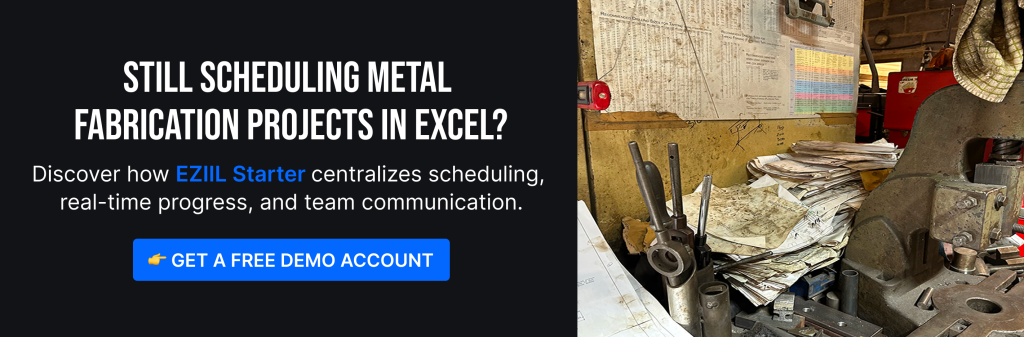
Butt Joint Welding
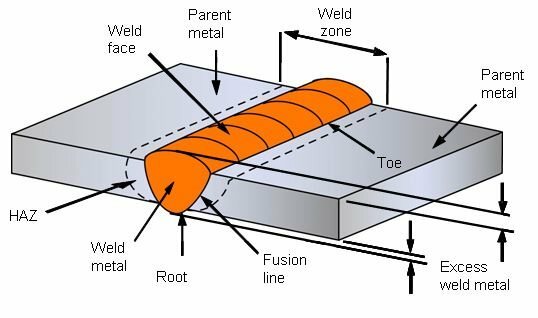
Image credit: https://www.twi-global.com
The most common welded connection is the butt joint, which is called butt welding. The joint forms when two metal pieces are placed together on the same plane surface with their edges meet. Welders often use butt joints to join plates, pipes, tubing, valves, fittings, or structures requiring a smooth, flush weld face.
Butt joints have good mechanical strength when fitted and welded correctly. They can be prepared in various ways or not, creating a square joint design called a square groove. Popular edge preparation includes beveled edges, which can be partially or wholly beveled throughout the material thickness. One of the workpieces might require a bevel (single bevel), or both may need it (V-groove).
Here is a list of popular butt weld joints:
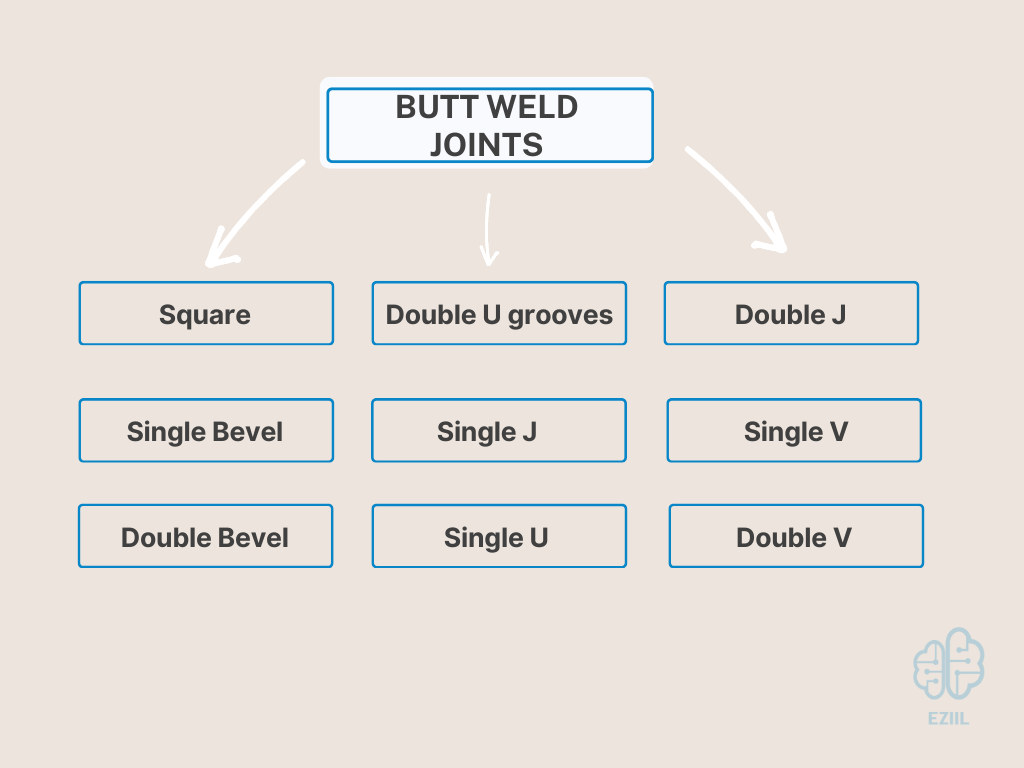
The primary factors determining the type of joint weld preparation include welding codes, appearance, required weld strength, and deeper penetration. Thicker metal requires a change to the joint design to ensure a quality weld. Getting 100% penetration on thick pieces without a groove is challenging or impossible, while thin plates typically can be welded without joint preparation.
Burn-through, cracking, porosity, and incomplete penetration are some defects associated with butt joints.
Tee Joint Welding
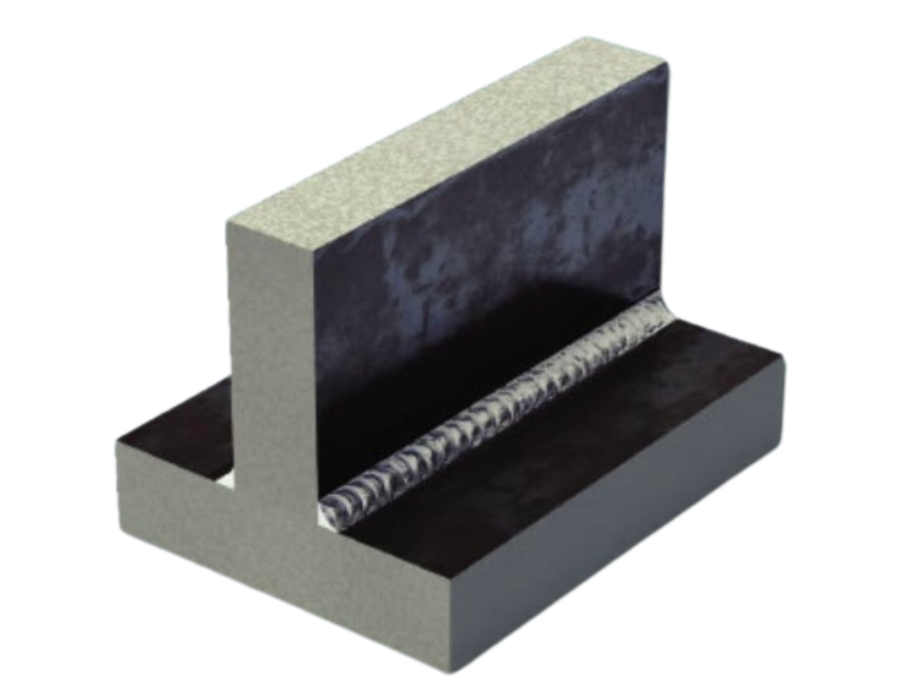
Image credit: https://www.techtransfer.com
Tee welding joints are created when the edge of one metal piece is welded to the flat surface of another, resulting in a 90° intersection or a ‘T’ shape. Tee joints are a type of fillet weld and can also be formed when a tube or pipe is welded onto a base plate.
T-joints typically require minimal joint preparation and are relatively easy to weld, whether in a flat, horizontal, vertical, or overhead position. If the joints are prepared, they can be cut, machined, or ground.
Several welding styles work for creating a tee joint, including the following:
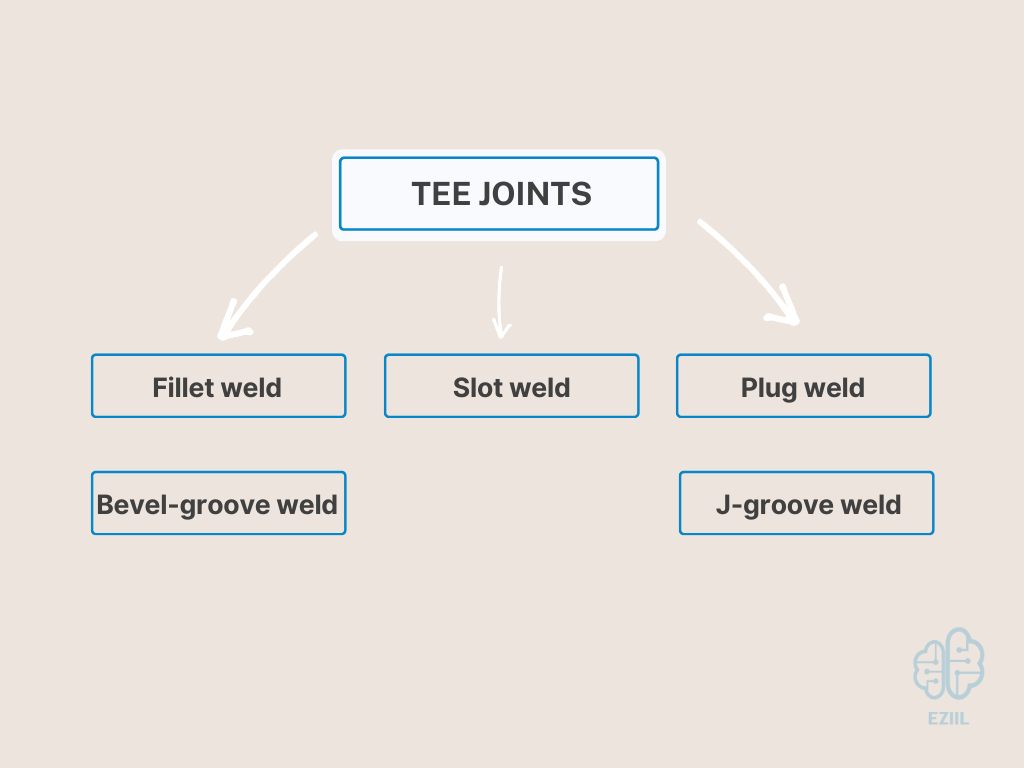
When welding a tee joint, position the weld on the same side of the joint that will be subject to stress. To avoid impact from the opposite side of the joint, causing the weld to fail, weld both sides for maximum strength or when pressure is applied from both directions.
For the optimum amount of penetration on both workpieces of a tee joint, use a 45-degree work angle. When welding different metal thicknesses, focus more weld on the thicker piece.
Edge Joint Welding
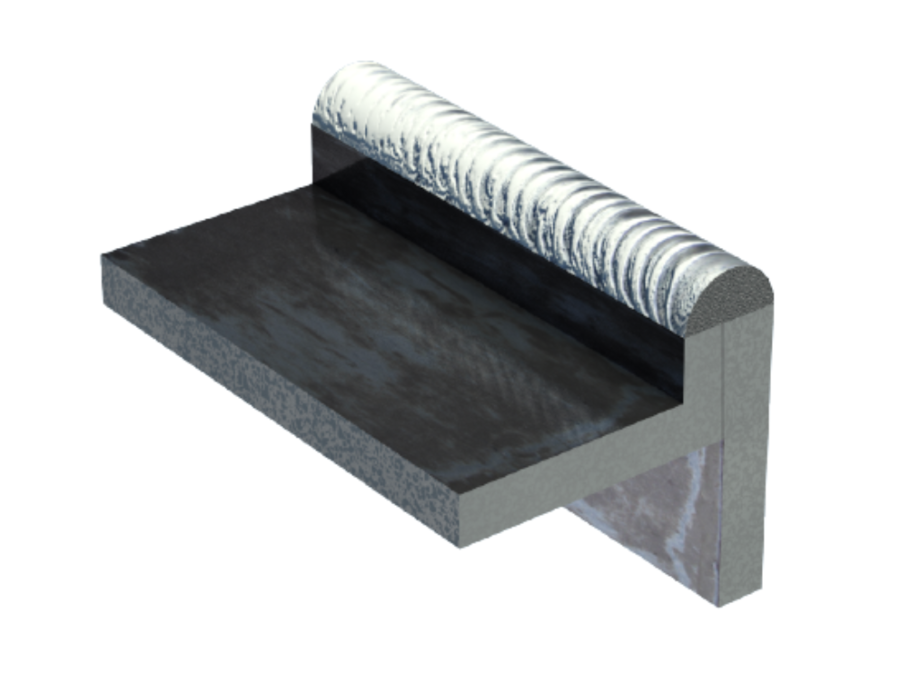
An edge joint means the metal surfaces are placed together, so the edges are even. Sometimes, one or both plates are formed by bending them at an angle. Edge joints are usually confined to workpieces that won’t be subjected to impact or high stress.
Different types of edge joints depend on how the edges are prepared for welding.
They can be left square (square groove), or they can be prepared by machining, cutting, or grinding into one of the following styles:
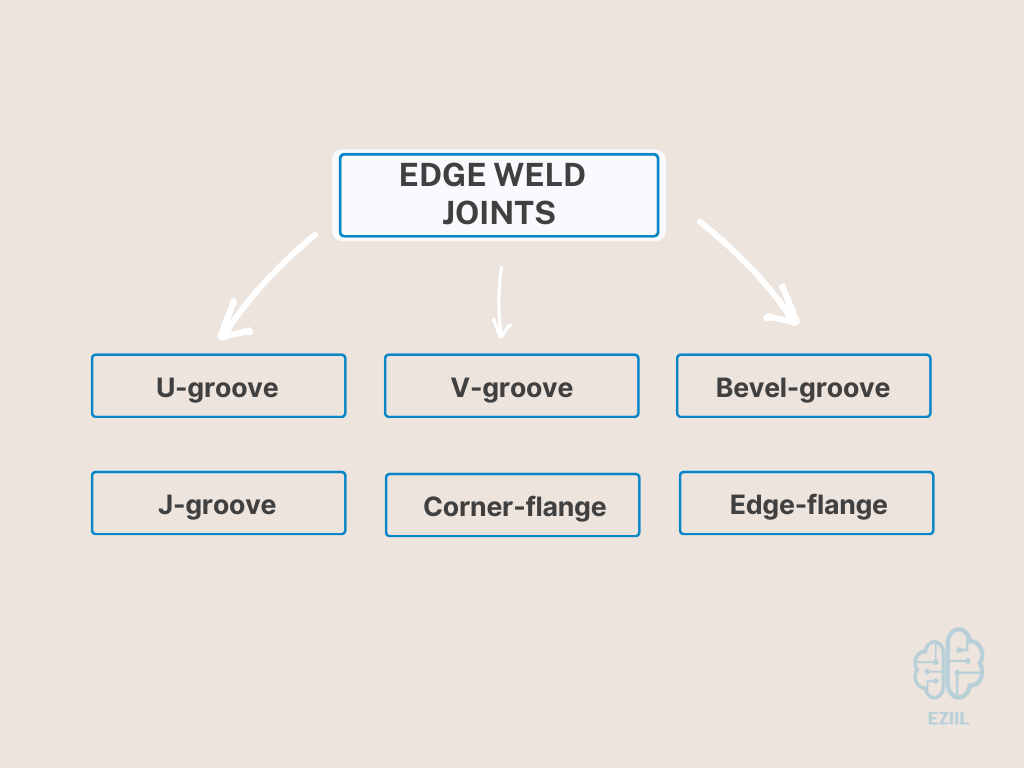
Preparations allow adequate penetration or improve overall coverage. An edge joint can be welded on all sides, providing additional joint rigidity, but they could require post-weld grinding if the weld must be flush with the base material.
Remember, the primary forces causing stresses in welded joints are tensile, compression, bending, torsion, and shear. Edge joints, especially square groove joints, are notoriously weak since the weld does not fully penetrate the joint thickness.
Also, edge joints are more susceptible to corrosion and defects such as porosity, lack of fusion, and slag inclusion because of the overlapping parts.
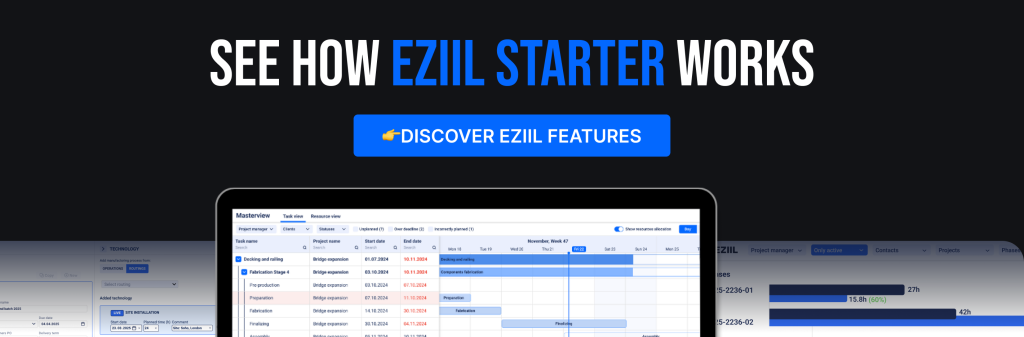
Lap Joint Welding
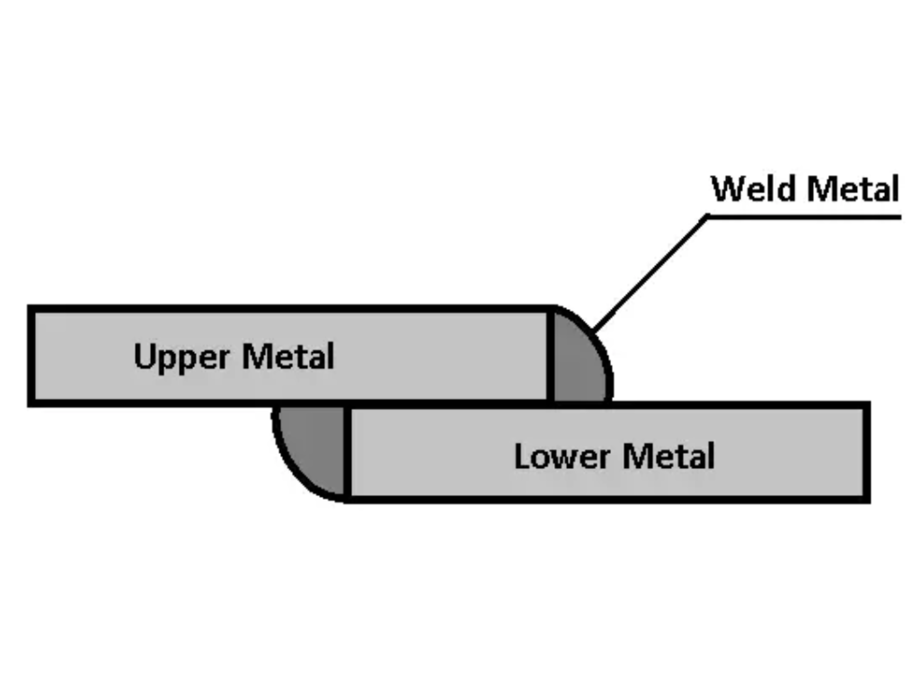
Picture credit: https://www.theengineerspost.com
Lap welding joints are formed when two pieces of metal are overlapped pattern on top of each other. The overlap depends on the thickness of the workpieces—the thicker the metal, the more overlap is required. Although splice joints are seldom used on thicker materials, they are often chosen to join two pieces of different thicknesses, plates and sheet metal.
Splice joints, have excellent mechanical properties, mainly if both sides of the overlapped pieces are welded for additional reinforcement. When welding splice joints, ensure that there are no gaps between the two pieces, and if you are welding a splice joint on thinner materials, reduce your amperage and increase the travel speed to prevent distortion and burn-through.
Splice joint welding methods include:
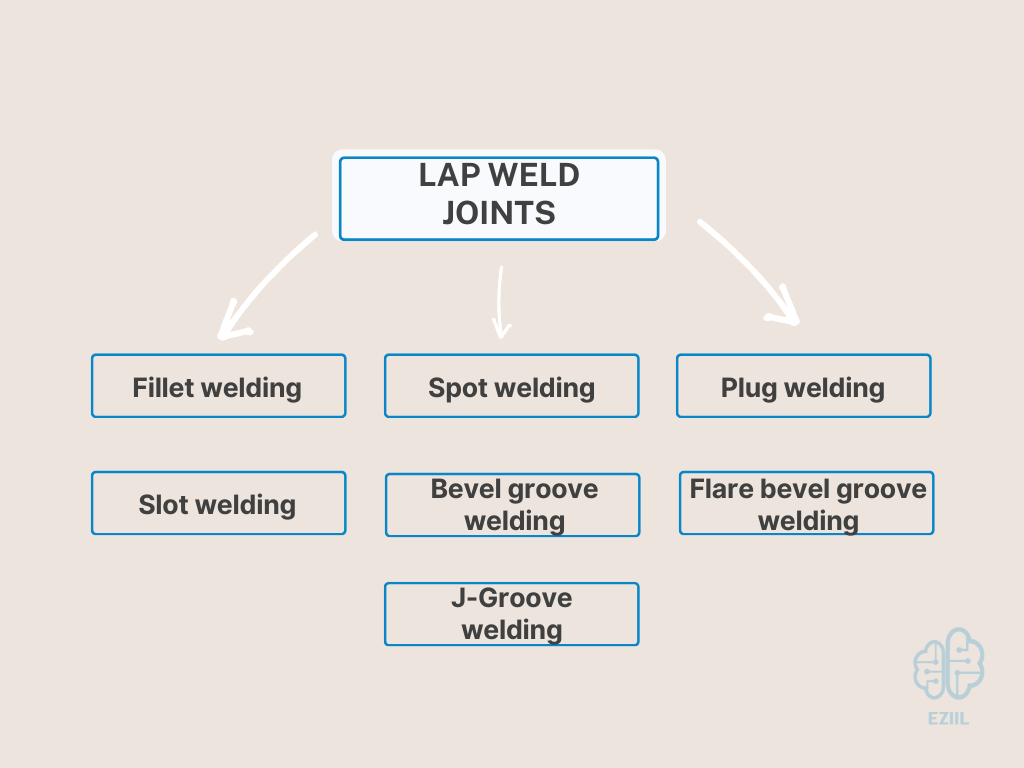
Splice joint welding has much in common with butt welding. However, splice joints offer more strength in higher-stressed areas, and the joints are more obvious and not flush as in butt welding.
Corner Joint Welding
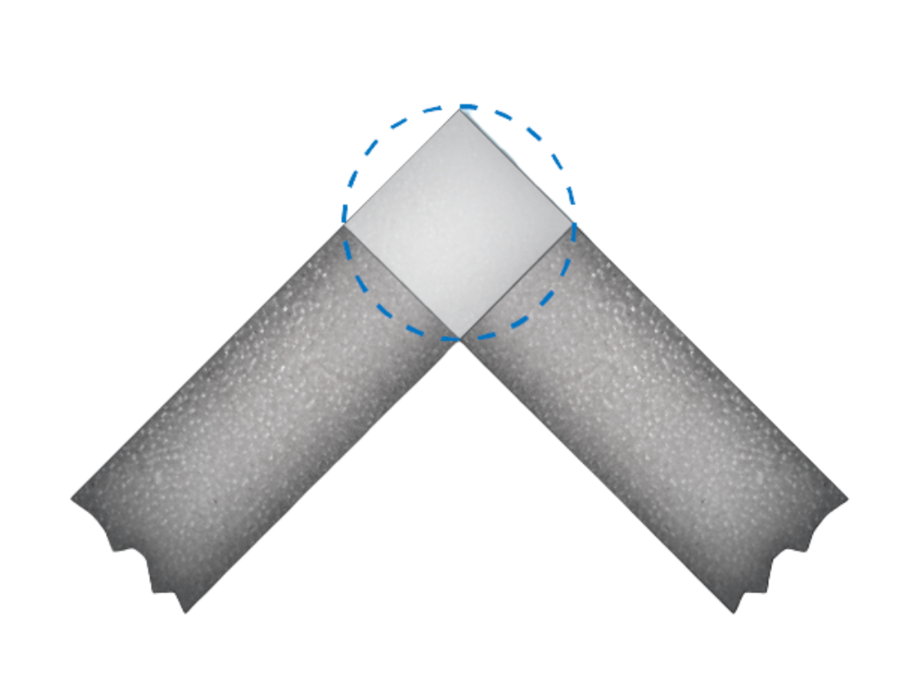
Image credit: https://www.techtransfer.com
When two metal pieces are joined at 90 degrees, making an ‘L’ shape, they form a corner joint. Corner joints are easy to assemble, requiring little preparation, and they are a lot like tee joints except for the position of the metal.
The two types of corner joints are open and closed. With an open corner, two edges meet at their corners, forming a V-groove, and with a closed corner joint, the edge of one piece is flush against the edge of the other, creating a square-butt joint. Welders choose either an open or closed corner based on the material’s thickness and the strength required for the application.
Fitting the workpieces correctly is essential to creating a corner joint since distortion may occur after the weld is applied. If a 90-degree angle is required, building a jig or fixture might be necessary to prevent warping and maintain the angle.
The styles used for creating corner joints include the following:
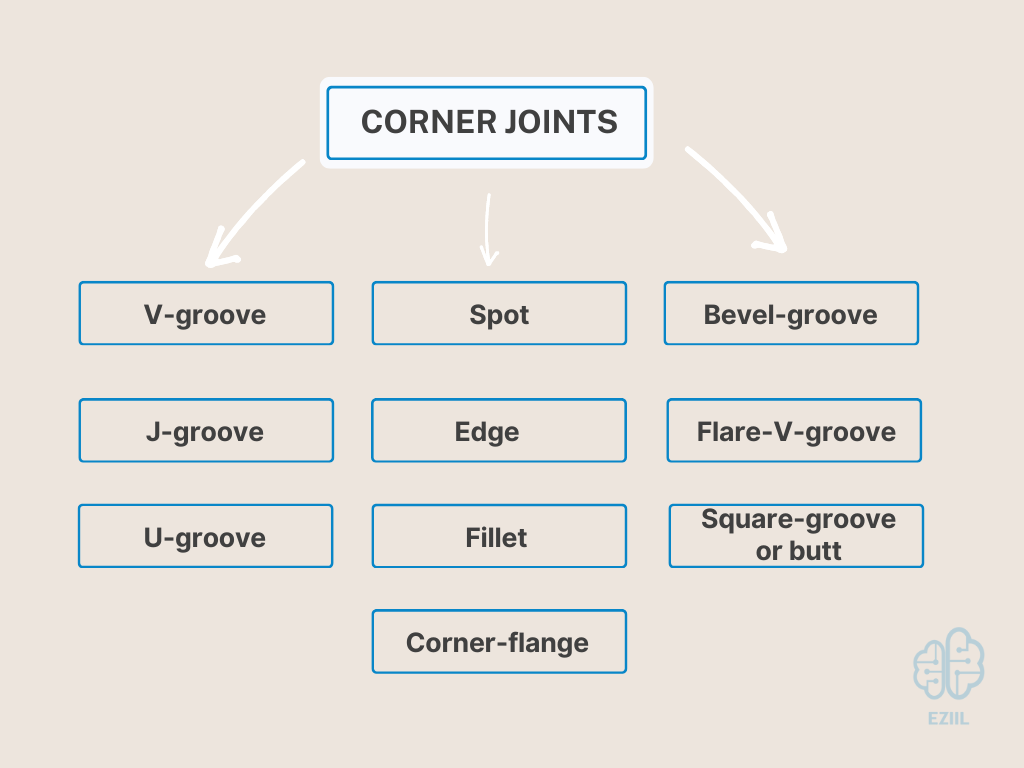
The Importance of Understanding the
Welding Joint Types
Since some joint designs are stronger and handle stress better than others, welding professionals must choose the design that meets their application’s needs. Applying the proper welding joints is more economical, requiring less labor and material. However, determining the best joint design could prevent weldment forces from causing weld and material defects or, even worse, a structural failure threatening lives and property!
Welding joint types are crucial in structural steel and sheet metal fabrication, as they determine the strength and durability of the final product. Fillet welds are one of the most common types of welding joints used in both industries, as they provide excellent load-bearing capacity and flexibility.
Fillet welds are created by fusing two metal pieces at a 90-degree angle, forming a triangular cross-section of weld metal. The welding process involves using filler metal to create a smooth, even fillet weld that fills the corner joint entirely.
Corner joints are just one type of joint used in welding. Other joint types include lap joints, where one piece of metal overlaps another, and butt joints, where two metal pieces are joined end-to-end. Each joint type requires specific welding techniques and settings, and the selection of the appropriate welding process and filler metal is critical to achieving the desired result.
In sheet metal welding, lap joints are commonly used due to the material’s thinness and flexibility. Welding sheet metal requires precise control of the welding heat input to avoid warping or melting the metal. Fillet welds are also suitable for sheet metal joints, especially where load-bearing is not a primary concern.
The weld metal and filler metal used in welding joints play a significant role in the weld’s strength and durability. Using high-quality welding and filler metal is essential to ensure that the joint can withstand the forces and stresses placed upon it.
In conclusion, selecting the appropriate welding joint type, welding process, filler metal, and metal pieces is crucial to achieving a strong, durable, and functional final product. With careful consideration of all these factors, the appropriate joint type and welding techniques can be selected to achieve the desired result.