Pidevalt arenevas metallitootmise valdkonnas on edu saavutamise võti täiuslik tasakaal täpsuse ja tõhususe vahel.
Selles pöördepunktis peitub märkimisväärne innovatsioon metalli laserlõikus, eriti lehtmetalli laserlõikamise näol.
Selle revolutsioonilise arengu eestvedajateks on sellised tööstushiiglased nagu Oshcut, mis on täielikult ümber kujundanud metallitööstuse maastikku.
Selles ulatuslikus arutelus süveneme metalli laserlõikamisteenuste sisemusse, avame nende sisemise toimimise, rakendused ja nende arengut soodustava tipptehnoloogia.
Oshcut ja täpsuse kunst: Oshcut: Lehtmetalli laserlõikuse maailm
Teekond algab kõige levinumast rakendusest: lehtmetalli laserlõikus. See protsess, mis on keeruliste projekteerimistööde ja suuremahulise tootmise nurgakivi, on kindlalt asetanud laserlõikurid metallitöötluse tööriistakomplekti oluliseks osaks. Need masinad kasutavad suure võimsusega laserite intensiivsust, et luua täpseid lõikeid, graveeringuid või märke mitmesugustele metallidele hingematva täpsuse ja järjepidevusega.
Sellised ettevõtted nagu Oshcut on selle tehnoloogia omaks võtnud, pakkudes spetsialiseeritud metalli laserlõikamise teenuseid. Nende oskusteave tagab veatult puhtad ja täpsed lõiked, mis vastavad iga projekti täpsetele spetsifikatsioonidele.
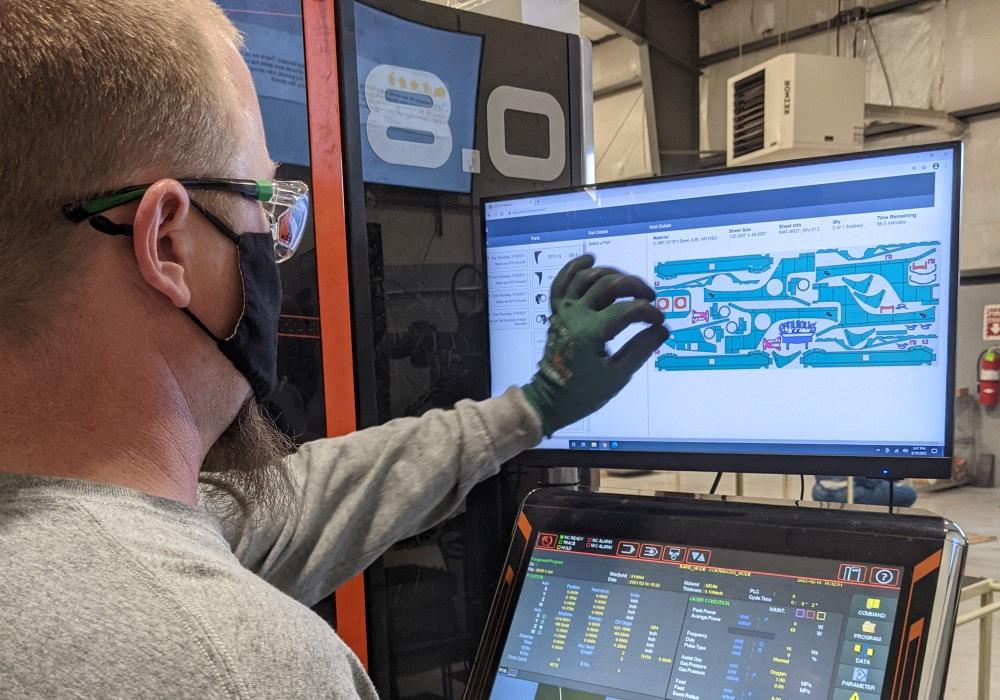
Metalli laserlõikamisteenuste eriline atraktiivsus
Metalli laserlõikamisteenused on muutunud vastupandamatuks ettepanekuks igasuguse ulatusega projektide puhul tänu mitmetele veenvatele omadustele.
Esimene neist on laserlõikusega pakutav võrratu täpsus. See täpsuse tase, mis on eriti oluline metalli laserlõikamise puhul, hõlbustab väga üksikasjalike kujunduste ja keeruliste vormide loomist, muutes selle kasulikuks projektide puhul, mis nõuavad suurt detailsust, näiteks ehetele või kunstiteostele eritellimusel põhinevate kujunduste loomisel.
Teiseks on laserlõikamise tõhusus võrratu. Kiire ja automatiseeritud protsess võimaldab suurt töömahtu, mistõttu on see ökonoomne valik suuremahuliseks tootmiseks.
Lõpuks on laserlõikus tuntud oma mitmekülgsuse poolest. See võimaldab lõigata mitmesuguseid materjale alates terasest ja alumiiniumist kuni eksootiliste metallideni, näiteks titaanini, ning avab maailma võimalusi kohandatud disainilahenduste ja ainulaadsete rakenduste jaoks.
Metalli laserlõikamise tüübid
Igal laserlõikamismeetodil on oma spetsiifilised tugevused ja rakendused, mistõttu on laserlõikamine mitmekülgne tehnoloogia erinevate tööstusharude ja materjalide jaoks.
Laser Cutting Type | Description | Typical Applications |
---|---|---|
CO2 Laser Cutting | Uses carbon dioxide gas to generate the laser beam | Non-ferrous metals, acrylic, wood, plastics |
Fiber Laser Cutting | Utilizes fiber optic cables for the laser beam | Stainless steel, mild steel, aluminum, copper, brass |
Nd: YAG Laser Cutting | Employs neodymium-doped crystals for the laser beam | Thin metal sheets, electronics, jewelry |
Pulsed Laser Cutting | Delivers laser energy in short pulses | Delicate and intricate metal parts |
Continuous Wave (CW) Laser Cutting | Provides a continuous laser beam | Thicker metal materials, high-power applications |
Alumiiniumi vallutus: Kergekaaluline ja väga vastupidav
Laserlõikuseks eelistatud materjalide hulgas on alumiiniumil eriline koht tänu oma erakordsetele omadustele ja sobivusele selle lõikamistehnika jaoks. Alumiiniumi laserlõikus näitab lasertehnoloogia märkimisväärset võimsust ja täpsust.
Vaatamata selle kergusele ja suhteliselt madalale sulamistemperatuurile võrreldes teiste metallidega libisevad laserlõikurid vaevata ja sujuvalt läbi alumiiniumi, mille tulemuseks on puhtad ja täpsed lõiked.
Tänu sellele kvaliteedile on see ideaalne valik mitmesuguste rakenduste jaoks, kus nii kaalu vähendamine kui ka täpsus on olulised, eriti sellistes tööstusharudes nagu lennundus ja kosmosetööstus. Lennundus- ja kosmosetööstuses on alumiiniumi laserlõikusel oluline roll selliste komponentide valmistamisel, mis nõuavad rangelt kaalupiirangutest kinnipidamist, ilma et see kahjustaks konstruktsiooni terviklikkust.
Laserlõikamise eeliseid kasutades saavad lennundusinsenerid saavutada keerukaid konstruktsioone, keerulisi kujundeid ja täpseid geomeetriaid ülima täpsusega, tagades lennukikomponentide optimaalse jõudluse ja ohutuse.
Alumiiniumi mitmekülgsuse ja laserlõikamise võimaluste kombinatsioon teeb sellest nõutava materjali paljudes tööstusharudes, rõhutades materjali omaduste ja tipptehnoloogia märkimisväärset sünergiat.
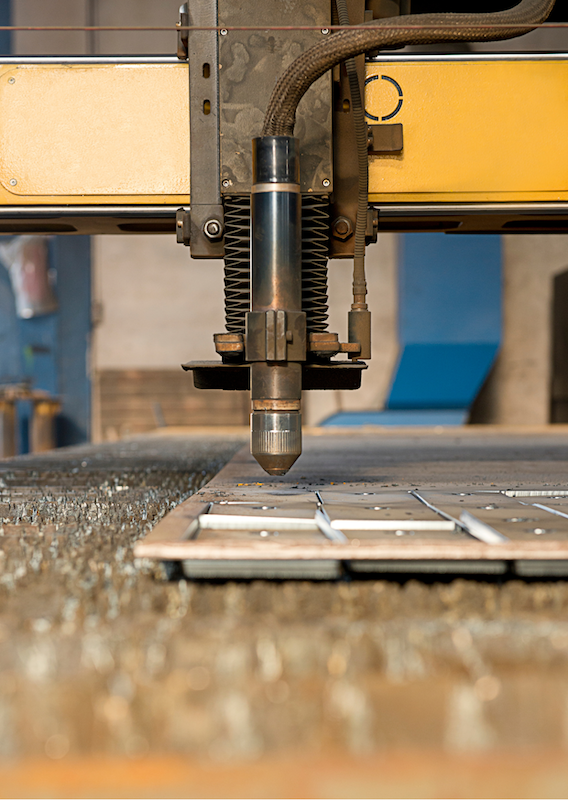
Innovatsiooni juhtimine: Lehtmetalli laserlõikamismasinad: Lehtmetalli laserlõikamismasinad
Nende teenuste keskmes on lehtmetalli laserlõikamispingid. Need keerukad masinad suunavad suure võimsusega laserkiire materjalile, et metalli sulatada, põletada või aurustada, tagades kvaliteetse lõppviimistluse.
Kaasaegsed lehtmetallide laserlõikepingid on enamasti CNC (arvuti numbrilise juhtimise) võimekusega, mis muudab need programmeeritavaks ja automatiseeritavaks. See funktsioon võimaldab luua keerukaid disainilahendusi ja mustreid suure täpsusega, mis on metallitööstuses väga olulised.
Lehtmetallide laserlõikepingid on tipptasemel seadmed, mis kasutavad fokuseeritud laserkiirte võimsust, et lõigata lamedat lehtmetalli erakordse täpsusega. See protsess hõlmab suure võimsusega laserkiire, mis sulatab, põletab või aurustab metalli, tekitades keerulisi ja täpseid lõikeid. Laseri fokuseeritud olemus võimaldab tihedaid tolerantse ja minimaalset materjali raiskamist, mis teeb sellest kulutõhusa ja jätkusuutliku lahenduse.
Tänapäeva kiirelt arenevas tootmismaastikus on efektiivsuse, täpsuse ja mitmekülgsuse otsimine olnud lõiketehnoloogiate pideva arengu liikumapanev jõud. Nende edusammude hulgas on lehtmetalli laserlõikepingid kujunenud revolutsiooniliseks tööriistaks, mis on muutnud lehtmetallist komponentide valmistamise viisi erinevates tööstusharudes.
Book a 60-minute demo to see
how eziil mrp solution works for you
Laserlõikamise revolutsioon: Metallide valmistamine: Metallide valmistamise ümberkujundamine
Laserlõikamise, eriti metallitootmise laserlõikamise kasutuselevõtt on häirinud senist olukorda. Alates isikupärastatud siltidest kuni autoosadeni on laserlõikamise mitmekülgsus ja täpsus toonud kaasa uuenduste laine metallitootmises.
See mõju on terasplaadi laserlõikusel sügavalt märgatav. Paksud terasplaadid, mis on traditsiooniliste lõikamismeetodite jaoks suur väljakutse, annavad laserlõikuritele kergesti järele, eriti ehitus- ja laevaehitustööstuses. Need masinad suudavad oma suure võimsusega kiirtega kergelt läbi lõigata tihedat terast, mis teeb need asendamatuks sellistes tööstusharudes nagu ehitus ja laevaehitus.
Kui soovite koostööd tipptasemel laserlõikamisteenusega, kaaluge Send Cut Send või Oshcut, mis on mõlemad tuntud oma laitmatu täpsuse, kiire tarneaja ja kliendikeskse lähenemise poolest.
Metalli laserlõikamise eelised vs. puudused
Siin on tabel, milles on esitatud metalli laserlõikurite eelised ja puudused:
Advantages of Metal Laser Cutters | Disadvantages of Metal Laser Cutters |
---|---|
High precision: accurate and intricate cuts | High initial cost: xpensive equipment |
Versatility: suitable for various materials | Maintenance costs: regular upkeep required |
No physical contact: non-mechanical process | Power consumption: high energy usage |
Minimal material waste: efficient material use | Limited material thickness |
Complex shapes: easily cuts intricate designs | Cannot handle thick materials effectively |
Speed and efficiency: faster cutting process | Safety concerns: risk of laser exposure |
Automation: easy integration with CNC systems | Reflective materials: some metals are difficult to cut effectively |
Low distortion: minimal heat-affected zone | |
Quick Prototyping: Ideal for small production runs | |
Reduced Tooling Costs: No physical tooling required |
Homne lubadus: Metalli laserlõikamise pidevalt arenev maastik.
Kuna me läheme tulevikku, siis metalli laserlõikamise tee särab potentsiaaliga. Tehnoloogilise arengu ja rahuldamatu täpsuse- ja tõhususnälja tõttu on selle valdkonna kasvu- ja innovatsioonivõimalused piiramatud.
Näiteks on kiudlasertehnoloogia tõusev täht, mida tunnustatakse selle suurepärase lõikamiskiiruse ja energiatõhususe poolest. Need masinad suudavad lõigata isegi peegeldavaid metalle, nagu alumiinium ja vask, ilma tagarefleksioonideta, mis võivad masinat kahjustada, laiendades sellega veelgi laserlõikamise rakenduste spektrit.
Eriti põnev areng selles valdkonnas on 3D-laserlõikamise tehnoloogia kasutuselevõtt. See uuendus võimaldab kolmemõõtmeliste detailide täpset lõikamist, mis kuulutab uue ajastu võimalusi sellistes sektorites nagu autotööstus ja kosmosetööstus.
Metalli laserlõikamise rakendused
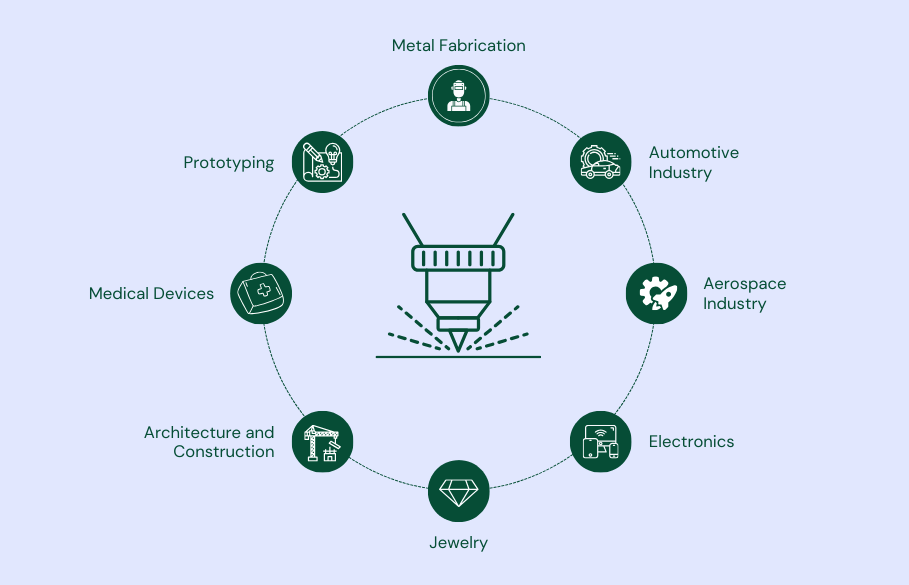
Metalli laserlõikamise rakendused on järgmised:
- Metallitootmine: Laserlõikamist kasutatakse laialdaselt metallitöötlemisprotsessides, et luua täpseid ja keerulisi metallkomponente ja -osasid.
- Autotööstus: Laserlõikusega valmistatakse autode kereosasid, väljalaskesüsteeme ja muid autoosasid.
- Lennundustööstus: Laserlõikamist kasutatakse lennunduslike komponentide, sealhulgas turbiinilabade ja õhusõidukite konstruktsioonide valmistamiseks.
- Elektroonika: Laserlõikamist kasutatakse elektroonikaseadmete, näiteks nutitelefonide, tahvelarvutite ja trükkplaatide valmistamisel.
- Ehted: Laserlõikamist kasutatakse ehtetööstuses täpsete ja keeruliste kujunduste tegemiseks sellistel metallidel nagu kuld, hõbe ja plaatina.
- Arhitektuur ja ehitus: Laserlõikus kasutatakse arhitektuuriliste metallelementide, dekoratiivsete elementide ja konstruktsioonielementide loomiseks.
- Meditsiiniseadmed: Laserlõikamine on seotud täpsete meditsiiniliste implantaatide ja kirurgiliste instrumentide tootmisega.
- Prototüüpimine: Metalli laserlõikamine on eelistatud uute tootekujunduste kiireks prototüüpimiseks.
Konkreetse metalli laserlõikamismeetodi valik sõltub sellistest teguritest nagu metalli tüüp ja paksus, nõutav täpsus, tootmismaht ja kavandatav rakendus.
Konkreetse metalli laserlõikamismeetodi valik sõltub sellistest teguritest nagu metalli tüüp ja paksus, nõutav täpsus, tootmismaht ja kavandatav rakendus. Lisateabe saamiseks lugege meie artiklit “Parim pesatöötlustarkvara laser- ja plasmalõikuseks”
Kokkuvõttes: Navigatsioon metallitootmise uuel ajastul
Alates individuaalsest lehtmetalli lõikamisest kuni ulatuslike tootmisprojektideni on metalli laserlõikurid muutnud revolutsiooniliselt suhtlemist metalliga. Nende masinate täpsus, tõhusus ja mitmekülgsus on toonud kaasa olulise muutuse erinevates tööstusharudes, muutes need praegusel ajastul hindamatuks tööriistaks.
Kui kaalute investeeringut laserlõikamismasinasse või koostööd lugupeetud laserlõikamisteenusega, on oluline mõista selle tehnoloogia võimalusi ja eeliseid, mis on põhiline samm selle täieliku potentsiaali ärakasutamise suunas. Vajalike teadmiste ja ressurssidega varustatud inimene saab kasutada laserlõikamise võimsust, et realiseerida isegi kõige ambitsioonikamaid projekte.
Kuna innovatsioon jätkab õitsemist ja saavutatavate piiride avardamist, on täiesti selge, et laserlõikus on tuleviku metallitootmises esirinnas. Selle põhjaliku juhendi abil on teil hea võimalus mängida olulist rolli selle tuleviku kujundamisel.