When looking at structural channel materials, you will almost certainly run into the question, “What is the difference between U-Channel and C-Channel?”. This is a common question, and the answer is a little more nuanced than one may imagine.
C-beam and U-Channel tend to be referenced in codes and by manufacturers as the same thing in North America and most other countries, simply being referred to as structural channel.
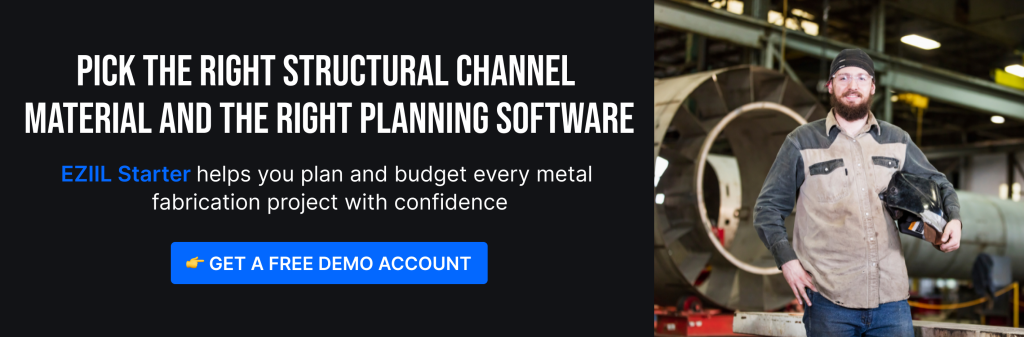
In Europe, however, codes have been made around C-Channel and U-Channel in an effort to both standardize their applications, as well as reduce confusion when purchasing. U-Channel is referred to as UPE Channel in Europe while C-beam is referred to as UPN Channel per Standard UNI 5680-73.
The answer to their actual difference lies primarily in the method of manufacturing and intended application of the channel. These differences are due to the materials the channels are manufactured from, as well as the manufacturing processes utilized to create the channel shapes.
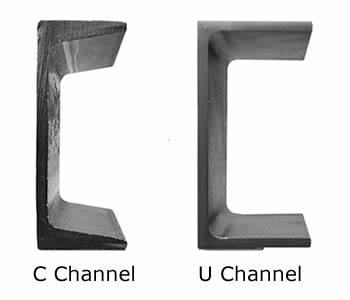
Image credit: https://www.steel-sections.co
Structure Channel Terms
When looking at structural channel, there are a few key terms to understand that will further help the distinction between C-Channel and U-Channel. A majority of the terms between the two are universal, with the primary difference between them being their feature ratios. See the image below to help visualize what each term is referencing:
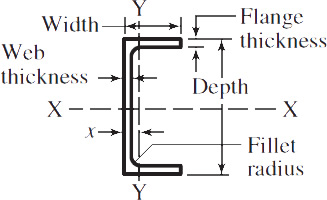
Width: Width is the total length measured from the backside of the ‘C’ shape to the front end of the flanges when viewing the piece as if it were the letter C.
Depth: Depth is also referred to as channel depth, and it is the measure of the length between the top and bottom of the ‘C’ when viewing the pieces as if it were the letter C.
Flange Thickness: Flange thickness is the measure of thickness of the ‘legs’ that are protruding to form the general channel shape.
Web Thickness: The web thickness is the measure of the thickness of the ‘backbone’ of the general channel shape as denoted in the image.
Fillet Radius: Each inner corner of the channel shape has a specified fillet radius. This is similar to that of other structural members like I-Beams and Angle Iron. The fillet radius is not typically specified by manufacturers but can be provided upon request.
C-Channel (UPN Channel)
C-beam is shaped very similarly to that of U-Channel, but it has tapered flanges that start out thicker from the web and thin down as they progress to the end of the total width. This geometry is a result of the versatile manufacturing process that creates C-beam, which is a continuous rolling operation. This rolling can be done hot – a process in which the material is heated to high temperatures to help reduce the force required to form the product which results in a ‘soft’, more flexible finished product, or cold – a process where the material is formed at rolled temperature which results in a stronger, but more brittle finished product.
C-beam is more common for industrial and structural applications in most nations – that is because it is a product that is more readily available and one that can be hot rolled with stronger materials that are then post processed to achieve greater strength as a percentage of weight ratios and is more commonly manufactured that U-Channel. C-beam is traditionally used as steel support beams in building applications and framing applications for equipment skids.
C-Channel comes in a large variety of sizes, and manufacturers tend to specialize on certain size ranges due to these large varieties present. To find the right size of C-Channel for your application, refer to each manufacturer’s website to identify sizes offered and work with what is readily available. Tables displaying size ranges should be readily available and will look like the below image which describe all major dimensions of the C-beam in a tabulated, easy to follow formula.
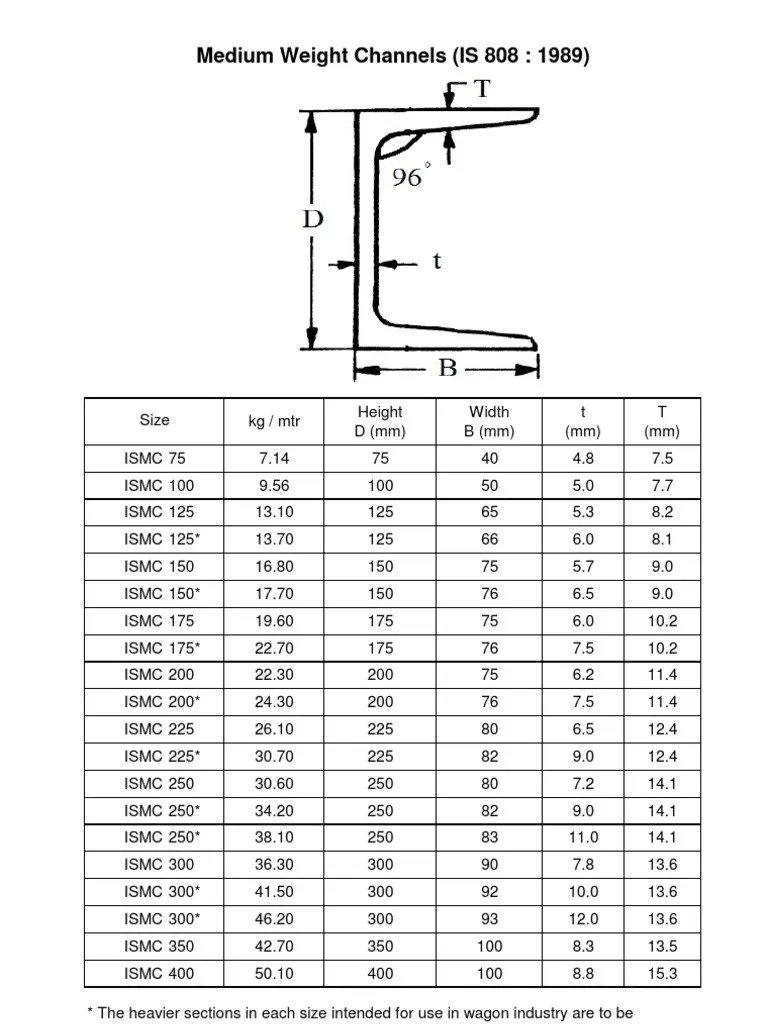
U-Channel (UPE Channel)
U-Channel is harder to find, tends to be made of weaker metals, and is typically used in lightweight or decorative applications in North America.
Although U-Channel has a greater strength as a percentage of weight ratio (depending on application), its difficulty to manufacture at thicker and larger geometry sizes makes it a more costly to produce and a less practical solution to general fabrication needs in most regions.
U-Channel also goes by the name Parallel Flange Channel and tends to be more custom to each manufacturer and industry standard sizes are not as common aside from the European standard surrounding UPE Channel.
When selecting U-Channel, it is a good idea to confirm size offerings from manufacturers before making design decisions as not every supplier will carrier the same product size ranges.
The table below shows a manufacturer’s specific size offerings of U-channel, and it should be noted that these size offerings appear more customized than those of C-Channel offerings.
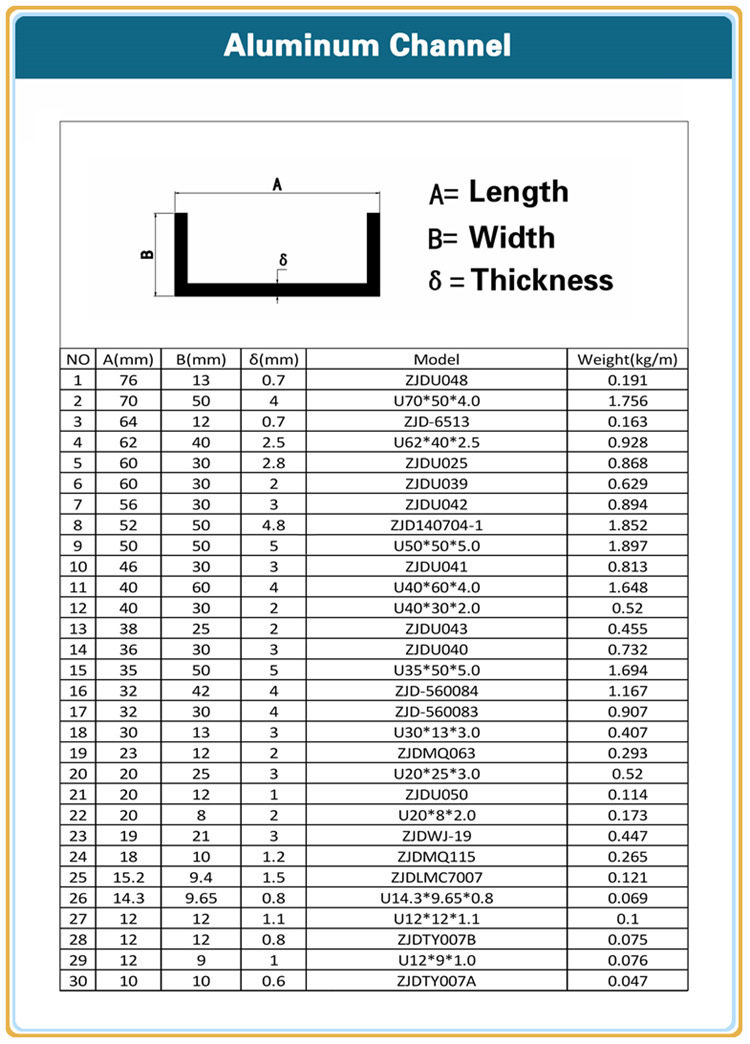
U-Channel is made in a variety of processes, but none of these processes are cheaper or easier to perform than that of the C-Channel hot rolling processes. While U-Channel can be made using traditional hot rolling techniques, the thickness ratios and lack of a tapered flange create a challenge for roller design and these issues tend make the process more prone to warping once cooled.
U-Channel can be made from square tubing by cutting the top section away, die extrusion processes that take billets and extrude them through specific shaped dies (only possible for softer metals like various grades of aluminum), and flat plate rolling in a cold rolling process.
Steel Channels: An Overview
Steel channels are a popular type of structural steel used in construction and industrial applications. They are made of steel and come in various sizes and shapes. One notable feature of steel channels is their flat surface, which makes them ideal for joining and attaching other materials.
The flat surface of steel channels allows for a stable and secure connection between the steel and other materials. This is particularly useful in construction and manufacturing where the steel channels are often used as a base for supporting heavy equipment or structures. The flat surface also makes it easier to weld or bolt steel channels together, creating a sturdy and durable joint.
Steel channels are available in different types, including hot-rolled steel channels and cold-formed steel channels. Hot-rolled steel channels are created through a heating and rolling process, while cold-formed steel channels are formed through a series of bending and folding operations.
The flat surface of steel channels is also useful in creating custom shapes and designs. Fabricators can easily modify the steel channels by cutting, drilling, or bending them to fit specific applications. They can also attach accessories or other materials to the flat surface of the steel channel to enhance its functionality.
In summary, steel channels are a versatile type of structural steel with a flat surface that makes them ideal for various applications in construction and manufacturing. Their flat surface provides stability, ease of attachment, and customization options, making them an attractive choice for engineers and fabricators alike.
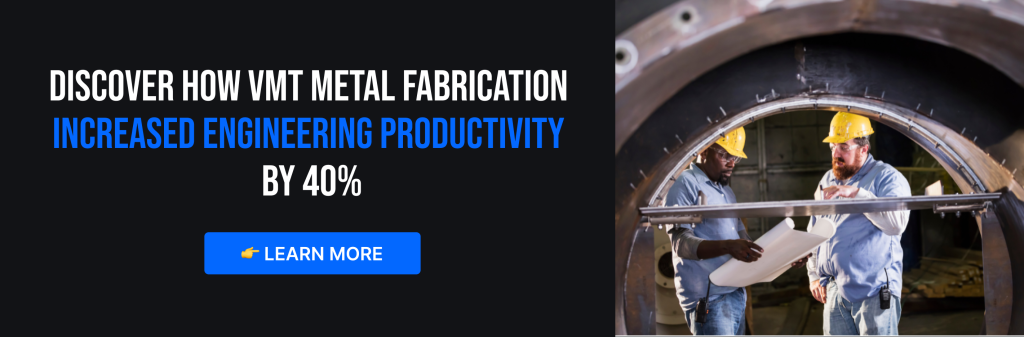
Conclusion
When considering C-Channel and U-Channel for your design applications, it is important to note that U Channel will tend to be offered in smaller sizes in most locations of the world, which leads C-Channel to being your primary choice for structural applications or applications that require stronger, larger support members. Both geometries offer very similar strength to weight ratios, with the primary difference being the size offerings available on the open market. Both versions of structural channel are essential to our daily world and can be found in almost every commercial and residential building in some fashion (for example: galvanized handrails).
Structural channel in either form can be found in applications regarding doorways, tracks and sliders for machines, posts and supports for buildings as well as building corners, walls & railings, decorative elements, and general framing applications for larger building construction.
As always, it is highly recommended to confirm with manufacturers when working through the design process to confirm availability, cost, sizing, and potential material grades for your specific application.
Especially with U-Channel, not all manufacturers will offer the same geometries as others, and the difference in their respective offerings can be immense.