Eziil helped VMT Tehased go from gut feeling to good planning, improving their shipping accuracy, significantly increasing their engineers’ productivity and curtailing their engineers’ onboarding time. On top of that, their work environment overall stress level is lower, due to reliable process and planning overview. By working smarter they increased their turnover by 30% without hiring new people.
VMT Tehased
Products: mainly 3 types of structural steel components and assemblies:
- Building structures like trusses, posts and beams. They produce various kinds of steel structures for commercial, public, agricultural and industrial buildings.
- Bridge structures that require advanced traceability and quality control.
- Special structures like large circular staircases for commercial buildings.
Staff: 125 people
Factories: 3 in separate locations with production area around 9700 m²
Production capacity: 5500 products with around 7500 tons of steel per year
2020 turnover: € 13.8 million with € 622K revenue
Home page: http://www.vmt.ee/en/tehased.html
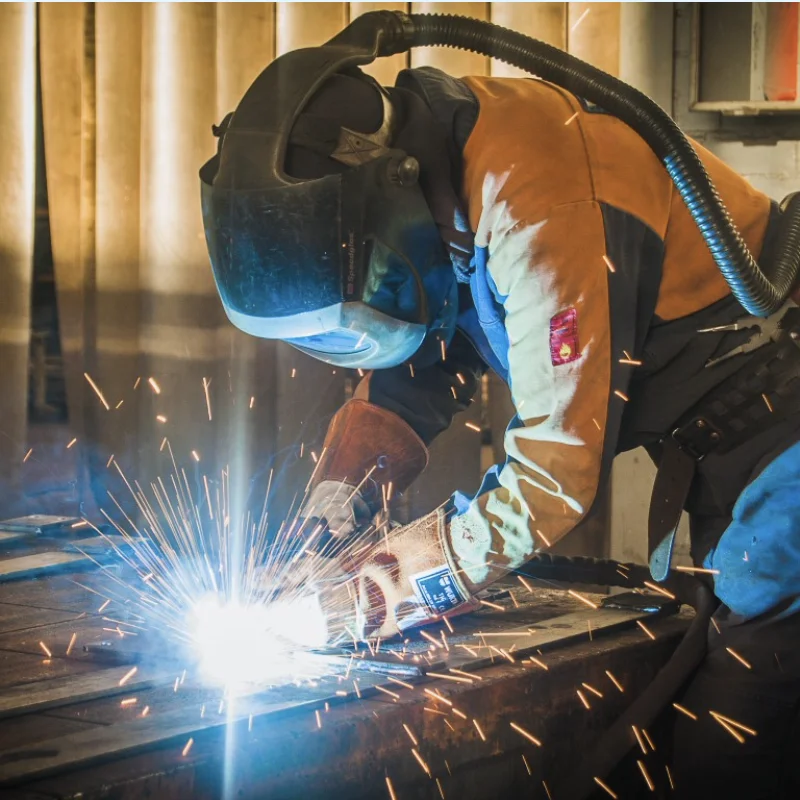
Life before Eziil
Before implementing Eziil BOM, VMT Tehased production procedures were already at a very good level, as they had obtained all the main production certificates (CE, EN 1090-1 EXC3, EN ISO 3834-2, IWE, EN ISO 9606-1, EN ISO 15614-154). However, most of these procedures were still on paper or in people’s heads and in countless spreadsheets.
All their BOMs were prepared in Excel spreadsheets and stored on a local server or SharePoint. There was a spreadsheet for every project and stage of the project, which were quite standardized, yet different in accordance to project type and complexity. All in all, production data was scattered in different sources which left too much room for interpretation by engineers, purchase and production.
Their main production technology challenges fell into 5 categories:
1. Managing BOM information
2. Standardizing engineers’ work
3. Onboarding engineers
4. Planning projects and deliveries
5. Managing more complicated projects
6. Overall stress levels
How Eziil helped VMT Tehased simplify their BOM process
VMT adopted Eziil BOM in 2018. As a result, VMT Tehased:
- Raised their engineers’ work efficiency by 40%
- Increased their turnover by 30% without hiring new people
- Increased their supply security from 45% to 98%
- Stayed profitable despite the rise of input costs
- Cut their engineer onboarding time from 3 months to a week
- Significantly reduced their overall stress levels
1. Managing BOM information
Managing product technology in spreadsheets was a task on its own. The procedure consisted of different spreadsheets and steps that the people just had to know they had to fill. The data was scattered in different spreadsheets and you needed to create additional separate spreadsheets to get the full overview. All this administrative work was monotonous and it was very simple to mess something up by mistake. If someone forgot to follow the procedure, the overview was lost.
Life with Eziil
With Eziil, they have a clear overview of the projects and their status. One can be sure that the data is correct. Everyone uses the same articles in BOM (Bill of Materials) and operations in BOO (Bill of Operations) and understands the projects the same way. The engineers can focus on what’s really important, not juggling and updating the spreadsheets. There is less room for mistakes, which in turn cause fewer errors and delays for procurement and production.
Eziil also has many convenient features that speed up the work, e.g. copy-pasting from Excel to Eziil BOM, standardized material library, pre-defined routings, operation attributes for additional filters and production outputs, etc. Also, the all-time favourite, printing out work orders.
2. Standardizing engineers’ work
With spreadsheets, every engineer managed their BOMs differently. They used different wording in article names or structure, which caused confusion in the purchasing and production. Often, this resulted in material shortage, wrong order of cutting material, production stops, or other compliance issues. Technologists had to jump in to solve critical non-compliances where work was impeded. That wasted engineering and production time and in the end delayed the production schedule.
Life with Eziil
Eziil BOM gave the engineers a top-notch tool to make their job easier and save time. With Eziil, all information is stored the same way, all the engineers work the same way and the process is standardized. There is a specific field for everything production or purchasing needs to know. All other parties have a clear understanding of what needs to be done and how. The BOM also checks mandatory fields to avoid forgetting and mistakes. This reduces unplanned work for engineers, as there is less non-compliances from purchasing and production – and less putting out fires! All parties have exactly the same information and a clear picture.
Book a 60-minute demo to see
how eziil mrp solution works for you
3. Onboarding engineers
When VMT was using spreadsheets onboarding an engineer could take more than 3 months until they were able to produce quality production documentation. In the meantime, they also needed to ask a lot of questions and additional information from senior engineers which in turn slowed everybody down. The new employee was frustrated because they had to reinvent the wheel and senior engineers were frustrated because they needed to invest a lot of time in onboarding and keep their projects on schedule at the same time. Not to mention, one had to be a serious Excel guru to get things done fast.
Martin Lehemets, the COO of VMT Tehased notes that onboarding time for engineers has fallen to a week – as opposed to the previous 3 months. “Long onboarding time can really put a strain on company growth. Now, finding new people is easier. We can even use apprentices to prepare some projects and in the end, can’t make a difference if it was done by a senior or junior employee.”
Life with Eziil
With BOM software, the process is straightforward and clear, which lowers the engineer’s onboarding barrier. Firstly, they can use a standardized article base, which is a big win. They can learn Eziil by watching user manual videos and looking up earlier projects to use as an example and quality baseline. Now they can give more complicated projects to less experienced employees. Many tasks are simplified or automatized, which also shortens the learning curve.
4. Planning projects and deliveries
Previously, planning relied on turnover, which in practice was basically gut feeling. Projects are with different complexity, use different resources and input prices change. Noone had a clear understanding of how much time projects could take and whether they had the capacity or not. When more complex projects overlapped in one department, the whole production could halt to a stop.
This created a lot of tension between sales and production. There was a constant conflict on whether they could take on a project or not and what delivery time they could promise. Eventually, it was more like predicting and praying, which usually resulted in putting out fires, ordering last minute subconstruction work with a high price and working overtime to keep up with the delivery schedule. There were constant delays that created enormous stress and exhaustion. If sales needed a status update on a project, they had to physically check the situation on the production floor. Giving mid-term project reports was also a stressful challenge.
Life with Eziil
Martin says that better planning has been the biggest general change: “Eziil gives everyone a real-time overview of the current state of resources and workload. We’ve become more precise and we can make firm promises.”
“Today, big projects might fall behind schedule for up to a week. In the old days, it was not uncommon to fall behind for several months,” notes Martin.
Everybody has the same picture about resources, so there is no fighting over whether we have resources or not. You can see it on both the department and factory level. Rainer says: “At one point we cancelled even weekly sales and production meetings that used to concentrate on resources – where we stand, how much work we can take on, and when. We saw that thanks to Eziil, we didn’t need that anymore. Everybody already had the information to make better decisions.”Martin notes “We used to play catch up with our deadlines, but today we’re often even ahead of schedule. You can see straight away if we can take on more work, what delivery times we can promise and where we could run into bottlenecks. Instead of guessing and opinions, we have hard data – it’s an enormous transformation.”
With Eziil BOM they also started project phase milestone planning. Project deadline gets divided into sub-deadlines for engineering, procurement, preparation, welding, painting, packing etc. This way they can respond quickly if a project starts going off schedule in some department.
5. Managing more complicated projects
VMT was shifting to bigger and more complex projects. This firstly puts strain on preparing the production technology. All information had to be very precise to minimize mistakes since they had multiple production sites, they used some rental workforce and also subcontractors. Getting an overview of what was going on and where was a real struggle. Projects had multiple stages and if anything changed in one stage, it also had to reflect in other stages. One can only imagine how handling all this in spreadsheets became a constant source for non-compliance issues and last-minute fires.
Life with Eziil
With Eziil, all BOM data is in one place and managing complicated multi-stage projects is simple, clear and concise. If one makes any changes to an article (e.g. detail’s name or the drawings’ file), it reflects throughout the assembly, which mitigates the risk of error.
The BOM also has information about subproduction and how work is divided between different production sites. That enables fast data output to all suppliers to clearly organize their work. Standardization is the key and giving orders always, in the same way, removes a lot of confusion from the process. There’s less guesswork on the shop floor with clear work instructions and drawings that are always presented in the same way – same with the suppliers.
6. Overall stress levels
With spreadsheets and gut-feeling planning, the stress levels used to be through the roof. Deadlines were missed since there were constant surprises coming up. To get back to schedule, they constantly needed to oversee the production process and do overtime. This all was their day-to-day normality.
Life with Eziil
With Eziil, people’s work has become more organized, clear and predictable. Rainer says that stress levels play an important role in employee motivation: “It’s a shame all this Excel madness is not directly measurable. Many things got taken care of on the go with a lot of tension. Noone calculated how much that really cost – how many people got burned and how many burned out. In hindsight, the cost seems high – very high. If you’d ask our engineers today to start using spreadsheets again, they definitely wouldn’t agree to that.”
whats next?
As the next step, VMT is implementing the Eziil procurement module. Martin says: “Eziil BOM data is the foundation for all upcoming processes. Next, we’ll systematize purchasing and want to move all our sub-contract, project-based and standard material purchases to Eziil. We’re halfway there and already see remarkable results.”
Are you looking for the right BOM tool for your metal production?
Book a 60-minute demo and see Eziil in action.