Metallitootmise tarkvara on tehnoloogiline vahend, mis aitab metallitootjaid tootmis- ja juhtimisprotsessides.
Ettevõtted kasutavad seda oma tootmisprojektide kontrollimiseks, jälgimiseks ja haldamiseks, alates projekteerimisest ja planeerimisest kuni tegeliku tootmise ja tootmisjärgsete etappideni, nagu tarnimine ja paigaldamine.
See tarkvara aitab ratsionaliseerida toiminguid, parandada täpsust ja suurendada tootlikkust, võimaldades metallitootjatel kontrollitud viisil kasvada.
Metallitootmise tarkvara valikute hulgast võib olla keeruline ülesanne. Need keerukad digitaalsed tööriistad on loodud selleks, et lihtsustada toiminguid, suurendada täpsust ja lõppkokkuvõttes suurendada tootlikkust metallitööstuses.
See artikkel juhatab teid läbi selle valdkonna kõige paremini hinnatud tarkvara, tuues välja nende peamised omadused, eelised ja selle, kuidas need võivad teie äritegevust potentsiaalselt muuta.
Ükskõik, milline lahendus, peamine põhjus metallitootmistarkvara kasutamiseks on tootmisprotsessi kontrollimine, et saaksite seda kontrollitud viisil kasvatada.
See annab ülevaate sellest, mis toimub planeerimise seisukohast.
Siiski on need elemendid, mis teevad tarkvara kasulikuks, samad, mis muudavad selle teie ettevõttes rakendamise keeruliseks ja hirmutavaks. Aastate jooksul kasutatud asjade vahetamine millegi uue vastu nõuab palju usaldust valmistarkvara lahenduse vastu.
Selle artikliga püüame anda teile mõned suunised, mida arvestada ja kuidas hinnata erinevaid lahendusi, et see protsess oleks võimalikult sujuv.
1. Eziil
Eziil on tipptasemel metallitootmise tarkvara, mis on loodud selleks, et anda teile tootmisprotsessist reaalajas ülevaade.
Selle eesmärk on parandada tootmisprotsesse
tõhusust, täpsust ja tootlikkust.
Sellel on täiustatud lahendused kõigi esmaste metallitootmisprotsesside jaoks, nagu projektijuhtimine, materjalide ja tööde arved, jooniste haldamine, hanked, ladustamine, planeerimine, aruandlus, tarnimine, arvete esitamine jne.
See funktsioon annab täieliku kontrolli kõigi teie tootmise osakondade üle, andes töötajatele täieliku läbipaistvuse selle üle, mida nad peavad saavutama.
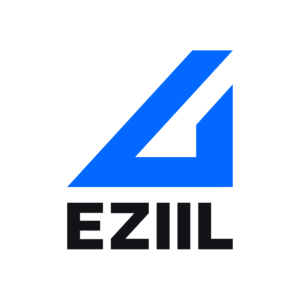
Tarkvara plussid.
- Keskenduda ainult projektipõhistele metallitootjatele
- Väga intuitiivne ja hõlpsasti kasutatav materjalinimekirja lahendus
- Keeruliste ülesannete lihtsustamine väiksemateks rakendatavateks sammudeks
- Projekti kulude analüüs (plaan vs. tegelikkus)
- Tootmisetappide jälgimine, materjalikasutus ja tehase tootmisvõimsuse planeerimine
- Kasutajasõbralik kasutajaliides ja integratsioon olemasolevate süsteemidega
- MobilE lahendus töökoha aruandluseks ja jooniste vaatamiseks
Tarkvara miinused:
- Pilvelahendused ei tööta ilma internetiühenduseta
- Eziil rakendusteenus peab seadistama ja kohandama vastavalt teie vajadustele.
Vaatamata nendele väiksematele reservatsioonidele on Eziil endiselt väga kasulik vahend tootmisettevõtetele, kes soovivad oma tootmisprotsessi optimeerida digitaliseerimise abil.
Kuna nad pakuvad rakendusteenust, käivad nad teiega protsessi samm-sammult läbi.
See meetod aitab neil arvestada tagasisidet, nii et lahendus täiustub aja jooksul pidevalt, mis teeb sellest suurepärase valiku tootmisettevõtetele, kuna nad alles määravad tuleviku.
On eelistatav olla süsteemis, mis kasvab aja jooksul, selle asemel et olla kinni fikseeritud süsteemis.
2. Strumis
Strumis on terasetööstuse ja ehitussektori vajadustele vastav tootmise juhtimise tarkvara.
See on loodud terasetootmise protsessi sujuvamaks muutmiseks alates esialgsest pakkumisest kuni projekti lõpetamiseni, vähendades käsitsi sisestatud andmeid ja võimalikke vigu, tagades täpsed kulukalkulatsioonid ja ajajuhtimise.
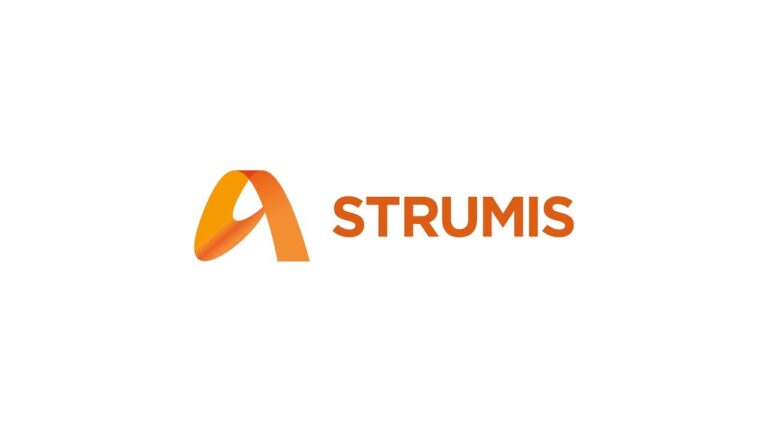
Tarkvara plussid.
- Osade jälgimine reaalajas täieliku jälgitavuse tagamiseks
- Integratsioon BIM-modelleerimise tarkvaraga
- Materjalide raiskamise vähendamine planeerimis- ja pesitsusfunktsioonide abil
- Tootlikkuse suurendamine automatiseerimise abil
- Tootmisprojektide kulude kontroll
Tarkvara miinused:
- Tarkvara keerukus võib tekitada väljakutse esmakordsetele kasutajatele.
- Esialgne seadistamine võib enne tulemuste saamist võtta palju aega ja vaeva.
- Kõrgtehnoloogiline lahendus, mis ei pruugi olla kuluefektiivne väiksematele tootmisettevõtetele, kes teevad eri tüüpi projekte.
- Kohapealsed lahendused peavad aja jooksul uuele versioonile uuendada
- Legacy-tarkvara on juba ammu turul
Üldiselt on Strumis tugev vahend, mis võib asjakohase rakendamise korral suurendada terasetootmise tõhusust.
Rakendamine on keeruline ja nõuab järsku õppimist, mis lisab tootjale riski, kuna algne investeering on märkimisväärne.
Täielikult toimiva süsteemi ja koolitatud meeskonnaliikmete jaoks kuluv aeg on märkimisväärne.
Mida lihtsam on tootmisprotsess toote seisukohast, seda lihtsam on Strumis töövoogudesse integreerida.
3. Tekla PowerFab
Tekla PowerFab on kõikehõlmav terasetootmise juhtimistarkvara.
See on vahend, mis on loodud tegevuse ratsionaliseerimiseks, tagades optimaalse tõhususe ja tootlikkuse terasetootmisprotsessis.
EPM tarkvara pakub reaalajas teavet ja visualiseeringuid varude kontrollimiseks, ostmiseks, tootmiseks ja projektijuhtimiseks.
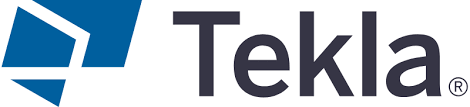
Tarkvara plussid.
- Põhjalik: Konsolideerib mitu protsessi ühte platvormi
- Sobib hästi valmistajatele, kes pakuvad ka projekteerimistöid ja teevad need Teklas, nii et nad saavad ühtlustada teavet Tekla Power Fab’i teostamiseks.
- Reaalajas nähtavus: Pakub ajakohast teavet paremate otsuste tegemiseks
- Integratsioon: Liidestub sujuvalt teiste Tekla ja Trimble’i lahendustega.
Tarkvara miinused:
- Õppekõver: See võib nõuda aega, et kasutajad omandaksid oskuse.
- Nõuab tehnilisi jooniseid ja muid allikaid peale Tekla.
- Maksumus: Tarkvara võib olla väikeettevõtete jaoks kallis, arvestades selle ulatuslikke funktsioone.
Lühidalt öeldes on Tekla PowerFab terasetootjatele tõhus vahend, mis pakub suurt kontrolli ja nähtavust tootmisprotsessi üle.
Eriti hea on see valmistajatele, kes ise projekte Teklas projekteerivad, seega on see loogiline järgmine osa tööprotsessis.
Selle ulatuslikud funktsioonid võivad aga tekitada õppimise väljakutse.
4. Construsteel
Construsteel metallitootmise tarkvara on terviklik lahendus, mis on loodud metallitootmise protsessi tõhustamiseks.
Tarkvaral on võimsad funktsioonid, mis võimaldavad kasutajatel luua, prototüüpe ja toota kvaliteetseid metalldetaile täpselt ja tõhusalt.
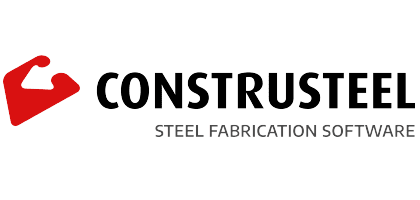
Tarkvara plussid.
- Võimalus integreeruda sujuvalt erinevate masinatega, suurendades tootlikkust ja vähendades käsitsi tehtavat tööd.
- Intuitiivne kasutajaliides ja tugevad simulatsioonivõimalused
- Tarkvara toetab erinevaid failiformaate, mis suurendab selle ühilduvust teiste projekteerimisvahenditega.
Tarkvara miinused:
- Nõuab järsku õppimist neile, kes ei ole CAD-tarkvara tundnud.
- Kõrged kulud võivad olla väikeettevõtete jaoks takistuseks
- Klienditoe reageerimisaega tuleb parandada.
Nendele puudustele vaatamata on Contrusteel hea potentsiaalne valik metallitootmistarkvara jaoks.
Samas võib seda olla raske rakendada, sest kasutamisest on vähe teavet ja kasutajaskond on väiksem, seega on tõenäosus, et keegi teie meeskonnas seda juba kasutab, väike.
See kogemuste puudumine tekitab rakendamise kitsaskoha, mis takistab kasutajatel süsteemist maksimaalset kasu saamast.
5. SysPro
SysPro metallitootmise tarkvara on terviklik lahendus, mis on loodud metallitootmise tööstuse unikaalsete vajaduste rahuldamiseks.
See pakub integreeritud lähenemist tootmisprotsessi kõigi aspektide haldamiseks ja kontrollimiseks, alates projekteerimise algfaasist kuni lõpptootmiseni.
SysPro tõhustab tegevust, suurendab tootlikkust ja suurendab kulutõhusust.
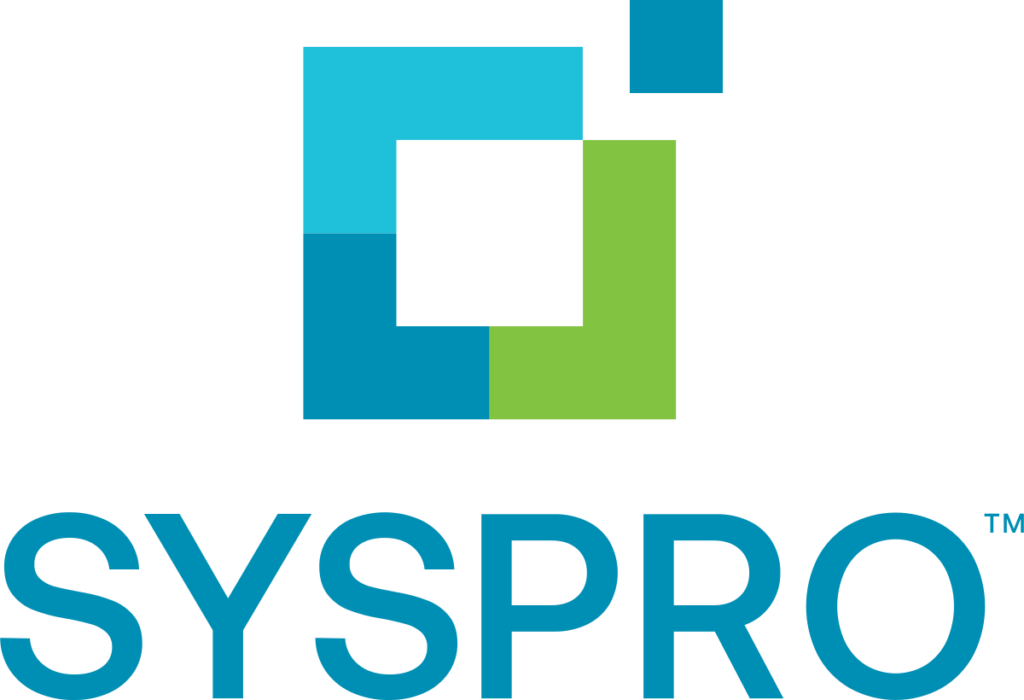
Tarkvara plussid.
- Jälgib täpselt varusid
- Tõhus kulukontroll ja jäätmete vähendamine
- Pakub reaalajas nähtavust toimingute kohta, aidates õigeaegset otsustamist.
- Toetab sujuvat integreerimist teiste ärisüsteemidega, suurendades tegevuse tõhusust.
Tarkvara miinused:
- See on uute kasutajate jaoks keeruline
- Teenindab mitmesuguseid tööstusharusid, kuid ei ole keskendunud tootmisele.
- Esialgne seadistamine ja integreerimine on aeganõudev ja võib nõuda spetsiaalset koolitust.
Vaatamata nendele piirangutele on SysPro mitmekülgne tööriist, mis võib oluliselt suurendada tootlikkust metallitootmises.
Kriitiline tegur on selle rakendamine ja hindamine, kas see sobib loomulikult teie praeguste tööprotsessidega.
6. Fabtrol
FabTrol Systems on olnud ülemaailmne liider terasetootmise halduslahenduste valdkonnas, pakkudes töökindlat metallitootmise tarkvara.
FabTrol on loodud terasetootjate tegevuse ratsionaliseerimiseks, tootlikkuse suurendamiseks ja täpsuse suurendamiseks.
See on suurepärane kalkulatsiooni, materjali haldamise ja tootmisülesannete automatiseerimisel, mis viib tõhususe suurenemiseni.
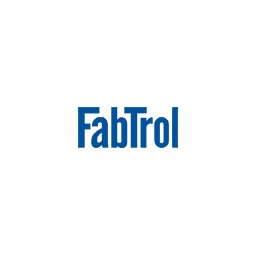
Tarkvara plussid.
- Hea hinnanguline funktsionaalsus
- See on olnud turul pikka aega ja seda kasutatakse laialdaselt.
- Selge töökorraldus terasetootja jaoks
- Põhjalikud aruandlusvõimalused
- Integratsioon populaarsete CAD-lahendustega, mis teeb sellest kõik-ühes-lahenduse metallitootmise haldamiseks
Tarkvara miinused:
- Kulud võivad olla väikeettevõtete jaoks takistuseks.
- Süsteemi kasutajaliides ei ole väga kaasaegne
- Töötab ainult kohapealse lahendusena
- Ametlik klienditeenindus ei ole enam kättesaadav
FabTrol on tarkvaralahendus, millel on suurepärane ülemaailmne kasutajaskond, kuid see väheneb kogu aeg, sest tarkvara jaoks puudub ametlik tugi.
Olemasolevad kasutajad võivad seda esialgu edasi kasutada, kuid peavad lõpuks üle minema kaasaegsematele toetatud lahendustele.
FabTrol’i, selle põhiomadusi ja selle lõpetamise ohte käsitlevat teavet leiate meie artiklist:“FabTrol MRP lõpetatakse 2023. aastal“. See juhatab teid läbi uute MRP-lahenduste hindamise protsessi, mis viib lõpuks meie soovituseni tõhusa FabTroli alternatiivi kohta.
Mis on metallitootmise tarkvara?
Metallitootmise tarkvara erinevad funktsioonid võivad hõlmata CAD/CAM-funktsioone, tööde jälgimist, materjali- ja varude haldamist ning kulude hindamist. Kõigi nende funktsioonide integreerimisega võimaldab tarkvara ettevõtetel saada tervikliku reaalajas ülevaate oma tegevusest.
See võib automatiseerida korduvaid ülesandeid, vähendada inimlikke vigu ja võimaldada kiiremat otsustamist. See on oluline vahend ettevõtetele, kes loodavad jääda konkurentsivõimeliseks pidevalt muutuvas metallitööstuses.
Edu tuleb õigest rakendamisest, sest süsteem peab sobima tootja äriprotsessi, et kõik ettevõtte töötajad kasutaksid seda oma töös. Asjakohane rakendamine loob lihtsa protsessi ja läbipaistvuse, mis võimaldab teabe kiiret liikumist ilma viivituste ja vigadeta.
Millised on metalli valmistamise tarkvara tüübid?
Metallitootmise tarkvara on kahte põhitüüpi, sõltuvalt nende määratud funktsioonidest.
Materjalivajaduste planeerimine (MRP) on tarnete planeerimise süsteem, mis aitab tootjatel mõista oma varude vajadusi, tasakaalustades samal ajal pakkumist ja nõudlust.
See sisaldab reaalajas ostude haldamist, tööde planeerimist ja edenemist ning projekti marginaale.
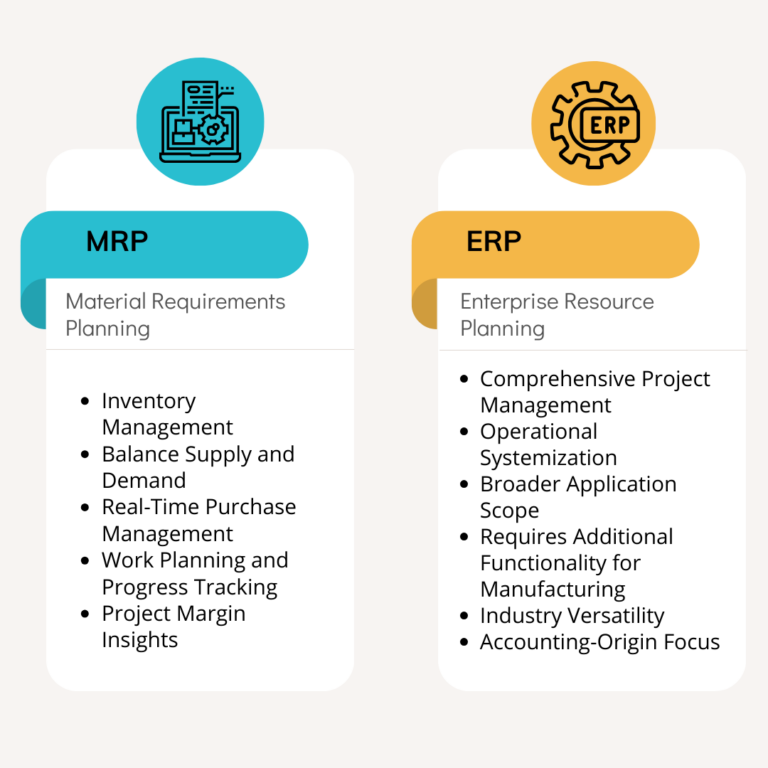
Ettevõtte ressursside planeerimine (ERP) tarkvara haldab projekte, võimaldades ettevõtetel süstematiseerida tegevusi laiemalt, võimaldades kasutamist igas osakonnas.
Siiski vajab see tavaliselt rohkem funktsionaalsust, kuna ERP on üldisem lahendus.
ERPi kasutamisel on tõenäoliselt olemas punkt, kus tootmine vajab seda ja MES-lahendust töövoogude korraldamiseks tootmisosakonna tasandil.
ERP on tavaliselt kavandatud erinevatele tööstusharudele ja pärineb pigem raamatupidamise kui tootmise seisukohast. See muudab süsteemi üldisemaks.
Muu tootmistarkvara hõlmab arvutipõhist projekteerimistarkvara (CAD) detailide kavandite loomiseks ja arvutipõhise tootmise (CAM) tarkvaraprogramme detailide, komponentide ja toodete mehaaniliseks töötlemiseks.
Samuti analüüsib pesade loomise tarkvara töödeldavaid detaile ja määrab kindlaks, kuidas need detailid lehel, plaadil või torul paigutada, et materjali tõhusalt ära kasutada.
Tavaliselt on CAD-süsteemid integreeritud MRP- või ERP-süsteemiga, et ühtlustada töövoogu. Nesting-lahendused võivad erineda sõltuvalt kasutatavatest masinatest või tootmistüübist, kuid tavaliselt ei ole need ka MRP- või ERP-süsteemides.
Kes kasutab metallitootmise tarkvara?
Alates müügist kuni müügitöötajateni kasutavad kõik ettevõtte töötajad metallitootmise tarkvara, mis ühtlustab protsesse ja suurendab projektide tõhusust.
Paljud spetsialistid kasutavad metallitootmise tarkvara kui olulist tööriista tootmissektoris.
Selle peamised kasutajad ettevõttes on müük, kalkulaatorid, projektijuhid, projekteerijad/konstruktorid, hankijad, tootmisjuhid ja -planeerijad, vormistajad ja tootmistöölised.
Kõik ettevõttes on protsessi kaasatud, sest nad vajavad olulist teavet projektide kohta või ajakohastatud teavet, mis põhineb nende tööprotsessis tehtud rollidel.
Tarkvaralahenduste peamine eesmärk on süstematiseerida kogu tootmisprotsessis kasutatav teave ja seejärel ühtlustada seda inimeselt inimesele, et vältida topeltkandeid ja vigu.
Kuna igaüks teeb seda, mida on vaja teha, saavad kõik meeskonna liikmed näha hetkeolukorda ja teha otsuseid reaalajas oleva teabe põhjal.
See suurendab tootlikkust, sest inimesed ei pea raiskama aega teabe otsimisele ja pidevale tulekahju otsimisele, sest nad teavad, mis toimub ja mis vajab tähelepanu just praegu.
Book a 60-minute demo to see
how eziil mrp solution works for you
Kui palju maksab tootmise tarkvara?
Metallitootmise tarkvarasse investeerimine võib tuua kaasa erinevaid kulusid, mis sõltuvad mitmest tegurist, näiteks ettevõtte suurusest (inimeste arv, tehased jne), vajalikest funktsioonidest, sellest, kas tarkvara on kohapealne või pilvepõhine, ning teenustasudest, nagu analüüs, rakendamine ja integreerimine.
Tavaliselt ei paku enamik pilvepõhiseid tarkvarasid rakendustuge, sest nad keskenduvad sellele, et teenuskulud oleksid võimalikult madalad.
See paneb palju vastutust lõppkasutajale, et lahendus kasutusele võtta ja tööle panna.
Pilvepõhise versiooni hind on tavaliselt kasutajate arvu järgi ja põhineb ettevõtte tasandil kasutatud funktsioonil.
Mõnikord võivad lisanduda lisakulud tehingute mahu eest kuus või aastas ja muud tasud erifunktsioonide eest.
Tavaliselt püüavad pilvelahendused hoida hinnakujundust võimalikult lihtsana, sest nad pakuvad iseteenindatavaid, valmislahendusi ja soovivad vältida klientidega otsest suhtlemist. Selline lähenemine selgitab, miks hinnad kasutaja kohta võivad ulatuda 49 dollarist kuni 350 dollarini kuus.
Peate teadma, et hind korrutatakse kasutajate arvuga, seega kaaluge enne otsustamist, kui palju kasutajaid teil süsteemis töötaks.
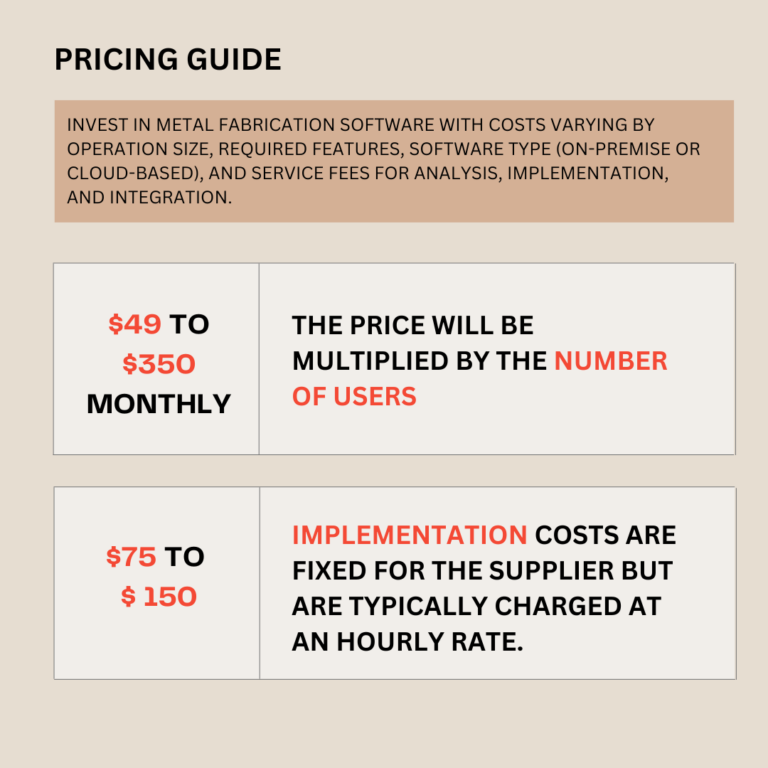
Litsentseeritud kohapealse tarkvara ostmine võib maksta 10 000 kuni 100 000 dollarit, sõltuvalt funktsioonidest ja kasutajate arvust. Sõltumata teie organisatsiooni suurusest, tundub see tavaliselt palju raha ja riski. Kõige märkimisväärsem risk on investeerida eelnevalt litsentsitasudesse, teadmata, kas see süsteem teie jaoks töötab. Tehes nii märkimisväärse investeeringu, jääte lahenduse külge, mis sunnib teid selle kasutusele võtma või kaotama.
Sellel strateegial on ka eeliseid, sest see sunnib teid muutuma, selle asemel, et mitte pühenduda. Kõik sõltub sellest, kuidas teile meeldib tegutseda, kuid investeeringu seisukohast on pilvepõhised igakuise renditasuga lahendused palju parem valik. Saate hoida esimese investeeringu madalana, koguda aja jooksul kogemusi ja lepingu üles öelda, kui see lahendus või lähenemisviis ei tööta teie jaoks. See valik võimaldab teil muuta kurssi, pöördudes tagasi varasema meetodi juurde või leides teile paremini sobiva süsteemi.
Tavaliselt on tarkvara litsentseeritud “as-is”, mis tähendab, et ostate praeguse versiooni. Tänapäeval liigub maailm üha kiiremini ja süsteemid vananevad 5-7 aasta jooksul. Siis tuleb osta uus litsents, et asendada vana. Vana versiooni kasutamine ja seejärel uuendamine uuele versioonile võib tunduda nagu nuppudega telefonilt nutitelefonile uuendamine, sest aja jooksul on nii palju muutunud. Mõned valmistustarkvara pakkujad pakuvad võimalust saada uuendusi, makstes kindlaksmääratud aastase uuendustasu, mis moodustab protsendi teie litsentsi väärtusest, mis varieerub10-25%.
Siiski on risk, sest seda uuendust tuleb teha süstemaatiliselt. Lõppude lõpuks on litsentseeritud lahendused teie serveris ja vajavad lisatööd. Seevastu pilvelahendused lahendavad selle probleemi kuutasuga. Iga kord, kui tuleb uuendus, saate selle kätte, mis võimaldab muutusi teha järk-järgult ja tunduda pigem evolutsiooni kui revolutsioonina.
Rakendushinnad on tarnija jaoks konkreetsed, kuid tavaliselt tehakse tunnitasu 75 kuni 150 dollarit. Hind sõltub rakendaja staažist ja sellest, kas süsteem on üldisem (odavamad hinnad) või tööstusspetsiifiline (kõrgemad hinnad).
Eksperdid maksavad rohkem raha, kuid sama tööstusharu konsultandi olemasolu võib teha 5-10 korda rohkem vahet võrreldes inimesega, keda tuleb koolitada, et ta mõistaks teie tööstusharu. Kogemus on sarnane uue töötaja töölevõtmisega: Kas te võtate kellegi, kes on seda tööd teinud ja saab kiiresti ülesanded kätte, või võtate inimese, keda peate õpetama oma tööstusharu nüansside osas?
Isegi kui ta on varem töötanud, kasutanud e-kirju, teinud Exceli ja korraldanud kohtumisi, on siiski palju vaja katta, et mõista, kuidas terasetootmine toimib.
Lõppkokkuvõttes võib odavam rakendusmaksumus tuua kaasa pikema projekti teostamise aja, tõsta ebaõnnestumise riski ja tuua kaasa kõrgema koguhinna.
Seega on rakendajate tausta hindamine vajalik osa rakenduskuludest. Kulusid mõjutab ka see, kui palju on ettevõttes inimesi, keda on vaja koolitada ja uusi protsesse rakendada.
Kui vajate läbipaistvaid, korratavaid kirjalikke protsesse, siis võtab selle väljatöötamine ja kõigi samamoodi arusaamiseks ühtlustamine lisaaega. Aeg tähendab tavaliselt raha, seega on rakendamiskulud suuremad.
Hind varieerub suuresti sõltuvalt teie ettevõtte suurusest, sellest, kes on müüja ja kas vajate ka rakendusteenuseid või mitte.
Kuidas valida metalli valmistamise tarkvara?
Õige metallitootmistarkvara valimine on kriitiline otsus, mis võib oluliselt mõjutada teie tegevuse tõhusust ja kasumlikkust.
See võimas tööriist võib teie protsesse sujuvamaks muuta, vähendada raiskamist, suurendada tootlikkust ja lõppkokkuvõttes parandada teie tulemuslikkust.
Siiski on oluline mõista oma unikaalseid nõudeid ja valida lahendus, mis vastab kõige paremini teie ärieesmärkidele.
Siin on nõuandeid, mis aitavad teil tarkvara valikul:
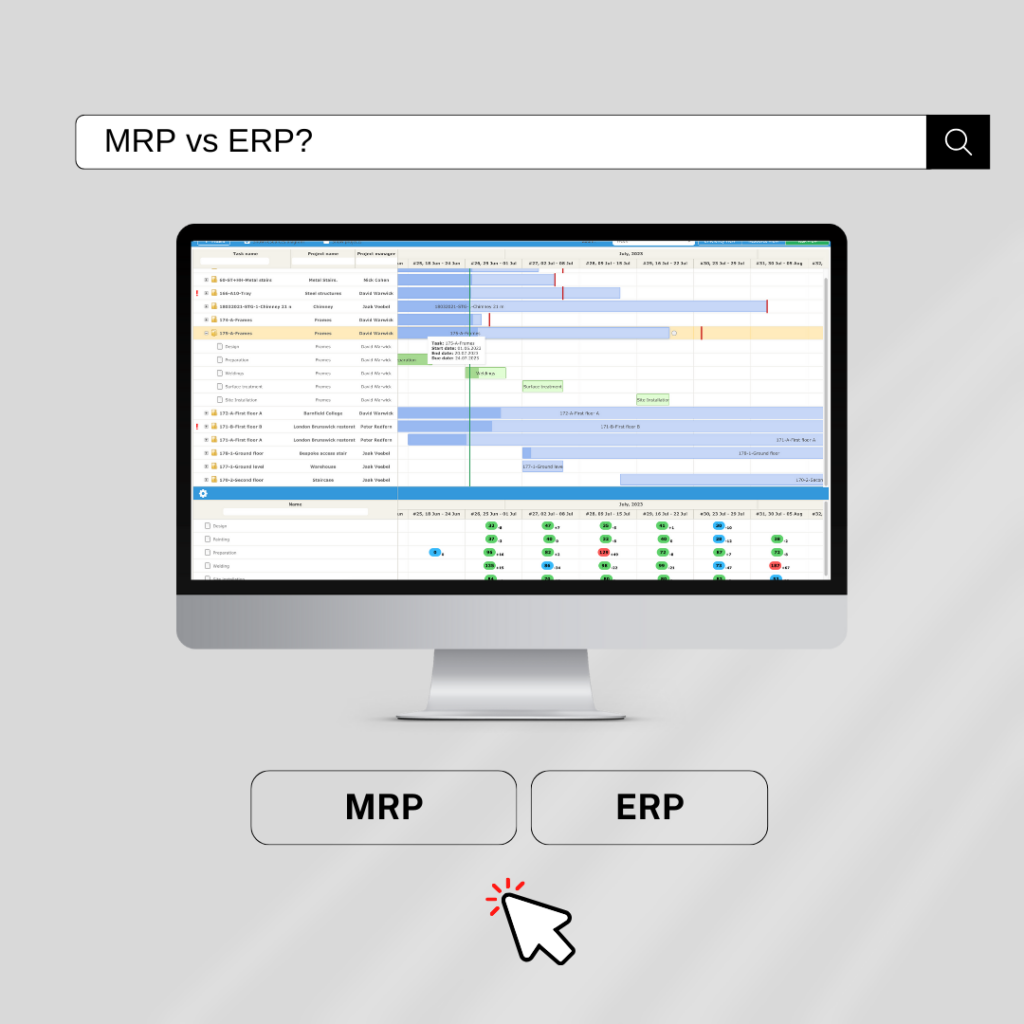
Probleemi tuvastamine, mida te lahendate tootmise tarkvara abil
Tootmistarkvara on teinud revolutsiooni tootmistööstuses, lahendades mõned selle kõige keerulisemad probleemid.
Üks selline probleem on ressursside, sealhulgas materjalide, aja ja tööjõu ebaefektiivne kasutamine. Vananenud manuaalsete protsesside tulemuseks on sageli materjali raiskamine, mis tuleneb planeerimise puudumisest, vigadest teabe tõlgendamisel või halvast ülevaatest toimuvast. Samuti kulutavad need rohkem aega ja inimressurssi, suurendavad tootmiskulusid ja suruvad inimesed tuletõrjerežiimi, kus üks probleem ajab teist taga.
Selle tulemusena tuleb rohkem aega ja kõik oleks pidanud olema tehtud juba eile.
Tootmistarkvara lahendab selle probleemi, pakkudes täpset töövoogu ja süstemaatilist planeerimist, tagades materjalide optimaalse kasutamise ning seades selge ja arusaadava töövoo, et säästa aega ja vähendada tööjõudu.
Teine kriitiline probleem töötlevas tööstuses on sujuv koostöö ja kommunikatsioon erinevate sidusrühmade vahel. Traditsioonilised meetodid tegid selle keeruliseks, sest teave on tavaliselt inimeste peades või hajutatud postkastidesse või erinevatesse Excelsüsteemidesse. Planeerimiseks ja otsuste tegemiseks vajaliku teabe saamine võtab aega, mille tulemuseks on tootmisgraafikute hilinemine ja sagedased vead. Tootmistarkvara vähendab seda riski märkimisväärselt.
Tarkvara võimaldab reaalajas koostööd kõigi kriitiliste sidusrühmade vahel, kes töötavad projekti eri etappides koos, tagades, et kõik on ühel lainel.
Te võite juba teada, millised probleemid teie organisatsiooni vaevavad, kuid nende tuvastamine võib olla keeruline, kui töötate pidevalt ettevõtte sees tuletõrjerežiimis. Mõnikord on abiks partneri kaasamine, kes aitab teil probleemi tuvastada ja suunab teid õigete lahenduste leidmiseks õigele teele.
Nii või teisiti on oluline kaasata ettevõtte sidusrühmad (projektijuhid, kalkulaatorid, koostajad, tootmistöötajad jne) tuvastamis- ja otsustusprotsessidesse. Väljakutsed kasvavad, kui liigute ulatuslikumate ja suurema tonnaažiga tööde juurde, peate tööd jagama tarnepartiideks ja juhtima mitut projekti samaaegselt, teil on pikemad ettevalmistusajad (peate nägema pikalt ette) ja eri inimesed vastutavad teiste osakondade eest.
Keerukus tekib ka siis, kui selle osakonna töö on jagatud eri inimeste vahel; paljude liikuvate osade lisamine ja kõigega kursis olemine on väga aeganõudev ja sisaldab palju võimalikke riske.
Suurepärane näitaja teie praeguse protsessi tervise kohta on vaadata teie koosolekuid.
Kas 90% koosolekute ajast kulub sellele, et aru saada, kus kõik seisavad (milline on progressi seis), või tehakse seda eelnevalt ja 90% koosolekute ajast läheb lahenduste leidmiseks projektidele, mis ei edene nii nagu vaja?
See näitab, kui hea on kommunikatsiooniliin.
Oletame, et teil on palju tuletõrjet ja enamasti saate aru, milline on teie tootmisprojekti seis. Sellisel juhul on see punkt, kus te peate hakkama otsima tootmislahendusi, mistõttu te loete seda artiklit. See on vaid üks näide. Tõenäoliselt on veel palju muid asju, mis vajavad parandamist, ja miks te otsite lahendust.
Parim viis on neid asju märgata ja üles kirjutada. Võite otsida algpõhjuseid või kasutada seda nimekirja oma müüja kinnitamiseks. Müüjatega kohtudes esitage oma mured ja kaaluge, mida nad lahenduseks välja pakuvad. Kui see kõlab loogiliselt, teate, et räägite eksperdiga. Kui see on lihtsalt hägusus ja udu, siis võite olla kindel, et see müüja ei ole teie jaoks.
Kuid selleks peate olema selge, mida soovite lahendada, seega hakake märkama, mis teie tootmisprotsessis toimub, mis teie arvates ei toimi ja mis ei meeldi.
Müüja varasemate kogemuste kindlaksmääramine metallitootmise tarkvaraga
Metallitootmise tarkvara rakendamiseks on vaja muudatuste haldamist. See nõuab väga organiseeritud lähenemist, et muuta üksikisikud, meeskonnad ja organisatsiooni protsessid praeguselt tööviisilt uuele tööviisile. Samal ajal, kui te seda teete, ei saa te tootmist peatada, seega peab see toimuma siis, kui te teete seda, mida te teete: tarnite oma klientidele tootmisprojektid õigeaegselt!
Selle edukaks muutmine nõuab hoolikat planeerimist ja tundlikkust töötajate murede suhtes, sest uus tarkvara võib viia tööülesannete muutumiseni, sest on stressirohke õppida midagi uut, samal ajal kui tuleb hoida vana. Seetõttu tekib protsesside ja inimeste harjumuspärase tööviisi muutmisel vastupanu.
Edukas muudatuste juhtimine arvestab seda kõike parimal võimalikul viisil ja eespool mainitud ekspertidest rakendajad müüja poolelt tunneksid end kogemuste ja tulemuste põhjal nagu päev vastu ööd. Selle teekonna kavandamine nõuab oskust tööstuses, empaatiat inimeste murede suhtes, süsteemset tegutsemisviisi, järjekindlat lähenemist ja selleks hästi sobivat tarkvara. Kõiki neid elemente on võimalik saavutada ainult varasema kogemuse kaudu.
See tagab, et töötajad mõistavad tootmistarkvaraga töötamise eeliseid uuel viisil ja hakkavad uskuma tõhususe, täpsuse ja tootekvaliteedi parandamise võimalusse metallitöötlemisprotsessides. See hõlmab ka piisavat koolitust ja tuge, et aidata töötajatel uue süsteemiga kohaneda, vähendada häireid ja tagada sujuv üleminek.
Olulist rolli mängib ka teie meeskonna varasem kogemus tarkvaraga. Tuttavus tarkvara kasutajaliideste, funktsioonide ja funktsioonidega võib oluliselt vähendada uue tarkvaraga seotud õppimiskõverat, suurendades tootlikkust kohe alguses. Lisaks võimaldab varasem kogemus tarkvara rakendamisel hinnata prioriteete. See soodustab paremat koostööd, seades prioriteedid ja mitte koormates neid üle taotluste ja tegevustega, mida on vaja tulevikus, mitte praegu.
Sama oluline on kaaluda ühilduvust olemasolevate süsteemide või plaanitavate süsteemidega. Kui otsustate, kellega koostööd teha, tuleks enne tarkvara ostmist tõsiselt kaaluda tarnijate kogemusi selles valdkonnas sarnaste projektidega.
Üldised vs. tööstusspetsiifilised lahendused
Tööstusspetsiifilised tootmistarkvaralahendused pakuvad märkimisväärseid eeliseid üldiste alternatiivide ees, eelkõige seoses sellega, kui lihtne on neid rakendada ja kui nad töötavad teie praeguse tööprotsessiga samas filosoofias.
ERP ei sobi hästi tootmisele, sest see on üldine lahendus. Tööstusspetsiifilised tarkvaralahendused on kohandatud vastavalt tööstusharu unikaalsetele vajadustele ja väljakutsetele.
Näiteks kui olete EX3 tootja, peate jälgima konkreetsete talade valmistanud inimeste materjalitunnistusi ja teadma, millist traatkeevitusseadet kasutatakse. Seda konkreetset nõuet saab mõista ja esitada ainult keegi, kes tunneb seda tööstusharu. See eelis võimaldab sujuvamaid toiminguid, vähem vigu ja paremat kvaliteeti, suurendades tootlikkust ja kasumlikkust.
Teine eelis on kohandamise tase, mida pakub valdkonnaspetsiifiline tarkvaralahendus. Erinevalt üldisest tarkvarast saavad ettevõtted neid lahendusi kohandada ja skaleerida, et viia need vastavusse ettevõtte kasvu, muutuvate vajaduste ja tööstuse arenevate suundumustega. Selline paindlikkus tagab, et tarkvara jääb aja jooksul asjakohaseks ja pakub väärtust, pakkudes paremat investeeringutasuvust.
Puuduseks on see, et sellist tootmislahendust võidakse kasutada vähem, sest üldiste lahenduste pakkumine võimaldab juurdepääsu laiematele turgudele ja rohkem kasutajaid on süsteemiga tuttavad. Rohkem kasutajaid surub hindu odavamalt ja spetsiifilised lahendused võivad olla kallimad, sest ta tunneb ja pakub väärtust valmistajatele.
Samuti on tööstusspetsiifiliste tarkvaralahenduste puhul olemas spetsiaalne tugi, mis tähendab, et probleemide tekkimisel räägib kasutaja ekspertidega samas keeles, mõistab oma tööstusharu nüansse ja lahendab kiiresti kõik probleemid. Seevastu üldine tarkvara pakub tavaliselt tavapärast kliendituge, mis võib vajada rohkem ekspertiisi, et lahendada tööstusspetsiifilisi probleeme. See parem tugi võib kaasa tuua vähem seisakuid ja minimaalseid häireid tegevuses, muutes töö sujuvamaks ja paremini hallatavaks.
Kõik see kuulub samasse kategooriasse nagu rakendustootja kogemus.
Tarkvara funktsionaalsus
Tarkvara funktsionaalsuse kindlaksmääramine on koht, kus kummi kohtub teega ja kus paljud tarkvarapaketid põrkuvad oma esimese suurema takistuse taha. Ükskõik kui hea on rakendaja, tarkvara või eelnevalt tehtud plaan, tuleb alati ette konarusi.
Kui teabe lisamine on keeruline, võib kogu rakendusetapp jääda ootele. Kõik muu saab õigete projekti ja Bill Of Materiali andmete korralikult toimida. See peab olema valmistajatele arusaadav, kuidas projektid jõuavad MRP-, ERP- või tootmissüsteemidesse. See on ülioluline, sest iga projekt on individuaalne ja see tuleb sisestada tarkvarasse nullist.
Kui see võtab vähem aega, siis võtab see hanke- ja tootmistegevusest etteasteaega ning lõpuks võib vältida hilinemist kohapealse tarnega. See on üks oluline põhjus, miks tööstusspetsiifilise tarkvara kasutamine on sujuvaks üleminekuks oluline, sest seda muret tuleb arvestada ja lahendada.
Tõenäoliselt on väga lihtne importida otse CADist (SolidWorks, AutoCAD) või importida IFC-mudeliga.
Kõige tähtsam on see, et teave saab hõlpsasti ja kiiresti sisestada valmistamistarkvarasse, mis muudab konverteerimise kiiremaks, lihtsamaks ja vähem vigade tekkimiseks.
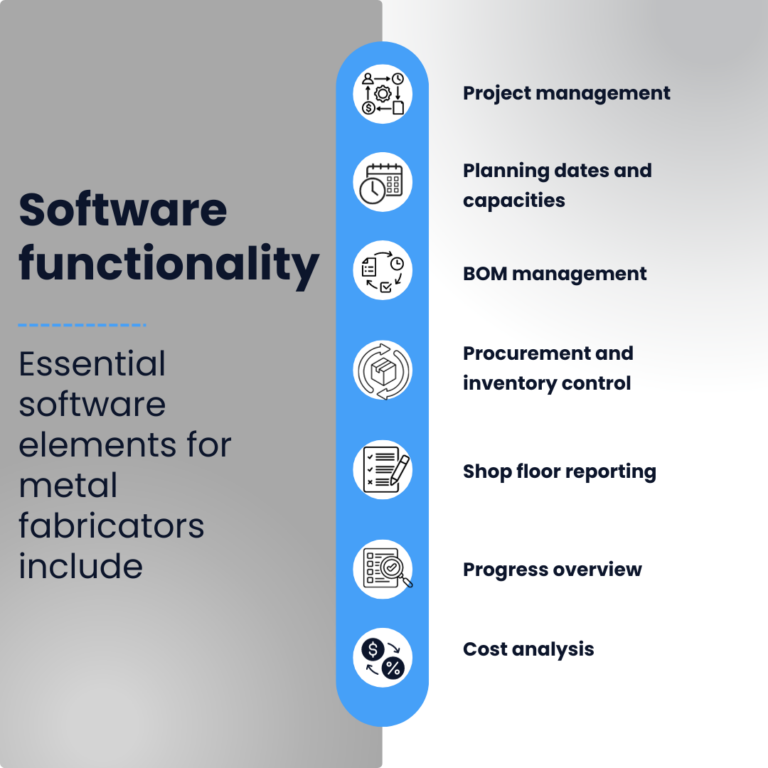
Metallitööstuses tegutsevatel töötlejatel peaks olema vähemalt järgmised elemendid tarkvaras:
- Projektijuhtimine: Projektijuhtimise funktsioon, mis võimaldab jagada projekte partiideks/etappideks. See soodustab paremat suhtlust meeskonnaliikmete ja klientide vahel, edendades probleemide lahendamist ja projektide õigeaegset lõpuleviimist.
- Kuupäevade ja võimsuste planeerimine: Planeerimine algus- ja lõpukuupäevad, mis põhinevad osakonnal, lisades hinnangulised tunnid, annab võimsuse planeerimise, et kogu teie meeskond mõistaks ühtemoodi, kus on protsessis kitsaskohad ja milliseid tähtaegu uutele projektidele lubada.
- BOMi haldamine: . Materjalide loetelu on terviklik loetelu toorainetest, koostetest, alakoostudest, osadest, komponentidest ja kogustest, mis on projekti jaoks vajalikud. Hea süsteem suudab hallata ka jooniseid ja kaardistada marsruute (Bill of operations), nii et kõigil oleks selge, mida on vaja teha ja kuidas see välja näeb. See on tavaliselt inseneride või joonestajate töövahend. Mõnes ettevõttes on see töö jagatud, nii et tootmisjuht või planeerija teeb operatsioonipoolt.
- Hanked ja varude kontroll on kaks tõhusa tarneahela juhtimise komponenti. See element tagab, et tootjad hangivad kaupu ja teenuseid õiglase hinnaga, säilitades samal ajal nõudluse rahuldamiseks optimaalse varude taseme. Hankemenetlus sisaldab palju käsitsi tehtavat tööd. Seega tuleb oluliselt tõsta töö tõhusust ja riski, et midagi unustatakse, ei jõua õigel ajal kohale, mistõttu tuleb tootmine peatada ja ümber planeerida.
- Tehasearuandlus annab reaalajas ülevaate tootmisprotsessides toimuvast. Kas näete, kas planeerimine oli õige ja me oleme ikka õigel ajal? Samuti võimaldab see ettevõtetel mõista, kus on tootmise kitsaskohad, kus on hinnangud täpsed, milline on töötajate oskuste tase, kas meil on vaja tootmisprotsessi parandada või mida on vaja anda alltöövõtu korras millegi väljastpoolt. Täielik jälgitavus teenib ka teie klienti, kes vajab selget dokumentatsiooni oma EX2-, EX3- või EX4-projektide kohta. Täpsus loob usalduse, mis viib uue äritegevuse juurde.
- Progressi ülevaade võimaldab igal meeskonnaliikmel teada, kus projekt on reaalajas, selle asemel, et arvata, kus me oleme. See peaks olema ajajoonel nähtav, et kiiresti tuvastada, mis toimub.
- Kuluanalüüs, et teada saada, milline on teie projekti kasumlikkus. Seda saate kasutada otsuste tegemisel selle kohta, kuhu investeerida. Tasuvus näitab projekti kasumit (või selle puudumist) igal hetkel ja sellest õppimine teeb teie kasvu.
Vältige kiusatust teha seda kõike korraga ja ühe hoobiga.
Nagu kehaga, on ka kehaga võimatu üleöö kõhnaks saada. Sama kehtib ka organisatsiooni kohta.
Uute tööviiside rakendamine ja vanadest harjumustest vabanemine võtab aega. Kui püüda kõike korraga lahendada, siis ajab see kõik üle ja paneb kõik seisma.
Tehnilised kaalutlused: kohapealsed (serverid) vs. pilvepõhised lahendused (SaaS)
Tootmistarkvara jaoks on saadaval kaks peamist kasutusviisi: kohapealne ja pilvepõhine.
Kohapealne tarkvara nõuab otse ettevõtte kohaliku riistvara ja serverite paigaldamist. Suurettevõtted eelistavad seda võimalust sageli selle kontrolli tõttu, mis võimaldab ettevõtetel kohandada tarkvara vastavalt oma vajadustele ja säilitada andmeid oma sisevõrgus.
See nõuab siiski märkimisväärseid alginvesteeringuid, mitte ainult tarkvara, vaid ka riistvara, seadistamise, hoolduse ja IT-toe jaoks. See lisandub tarkvarakuludele, sest selle ülalpidamine läheb teile igakuiselt maksma; ühel hetkel peate vahetama serveri ja tegelema varukoopiate, turvalisuse ja kõigi muude tehniliste asjadega, mis võivad olla väikeste ja keskmise suurusega tootjate jaoks üle jõu käivad.
Seevastu pilvepõhine tootmistarkvara asub teenusepakkuja serverites ja sellele on juurdepääs interneti kaudu. Sellel mudelil on mitmeid eeliseid, sealhulgas skaleeritavus, lihtne juurdepääs mis tahes asukohast ja madalamad algsed kulud.
Teenusepakkuja hoolitseb tavaliselt uuenduste, turvalisuse ja hoolduse eest, vabastades teid sisemistest IT-ressurssidest. Pilvelahendused on sageli tellimuspõhised, mis võib olla paljudele ettevõtetele rahaliselt paremini hallatav.
Üks asi, mida süsteemi valikul tehnilisest seisukohast arvesse võtta, on rakendusprogrammide liidesed (API). See mängib tänapäeval üha olulisemat rolli, võimaldades erinevatel tarkvararakendustel omavahel suhelda ja suhelda. Need laiendavad olemasoleva tarkvara funktsionaalsust, võimaldades arendajatel integreerida ja kasutada kolmanda osapoole teenuseid või funktsioone, ilma et nad peaksid aru saama nende rakendamise keerulistest üksikasjadest.
Tavaliselt on pilvepõhised lahendused selliste lahenduste jaoks avatumad kui kohapealsed lahendused.
Siiski on igal tarkvara kasutuselevõtu tüübil omad probleemid.
Kohapealse tarkvara hooldamine ja uuendamine on kulukas ning see ei pruugi pakkuda samasugust ligipääsetavust või skaleeritavust nagu pilvepõhised lahendused.
Samal ajal sõltub pilvepõhine tarkvara internetiühendusest, seega ei ole see võimalus ilma internetiühenduseta kättesaadav.
Tarkvara tugi: kui palju abi saate?
Terasetootmistarkvara pakkujad peaksid pakkuma tugivõimalusi, et tagada nende toote mõistmine.
Esialgu peaksid nad pakkuma tehnilist tuge kasutamise käigus tekkivate otseste probleemide lahendamiseks.
Tehniline meeskond on tavaliselt kättesaadav telefoni, e-posti või live-chati kaudu, tagades, et teil on igal sammul abikäsi.
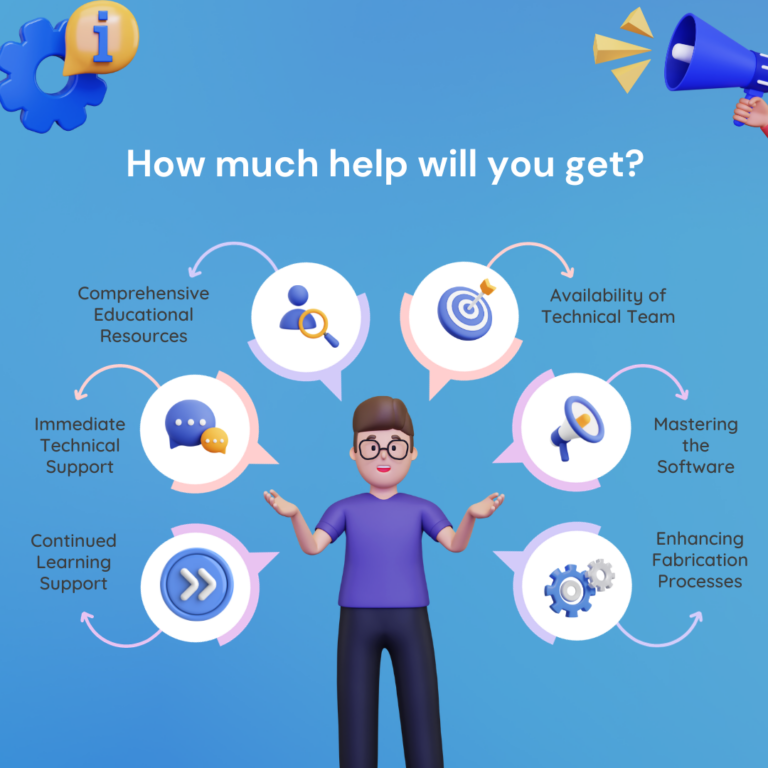
Lisaks otsesele tehnilisele abile otsige tarkvara pakkujaid, kes pakuvad jätkuvat tuge koolituse ja haridusressursside kaudu.
Need ressursid võivad sisaldada kasutusjuhendeid, videoõpetusi, veebiseminare või isegi individuaalseid koolitusi, mille eesmärk on aidata teil mõista tarkvara funktsioone ja nende tõhusat kasutamist.
See pidev õppetugi on oluline tarkvara omandamiseks, võimaldades teil kasutada selle täielikku potentsiaali ja lõppkokkuvõttes parandada teie tootmisprotsessi.
Inimesed ja väärtused sobivad
Teie väärtustega kooskõlas oleva tarkvarapakkuja valimine on oluline, et edendada pikaajalist suhet, mis toetab ettevõtte kasvu ja jätkusuutlikkust.
Selline kooskõla on usalduse, tõhusa suhtluse ja vastastikuse mõistmise alus, mis on hädavajalik tehnoloogilise integratsiooni keerulisel maastikul vältimatute takistuste ületamisel.
Samuti võib ühine väärtuste kogum hõlbustada sujuvamaid läbirääkimisi, projektide kooskõlastamist ja tõhusamaid probleemide lahendamise protsesse, säästes mõlemale poolele väärtuslikku aega ja ressursse.
Pikemas perspektiivis ei ole suhe tarkvarapakkujaga pelgalt tehinguline suhtlus, vaid strateegiline partnerlus, mis võib oluliselt mõjutada teie ettevõtte arengut.
Tarkvarapakkuja, kes mõistab ja jagab teie ettevõtte väärtusi, on tõenäoliselt rohkem pühendunud teie ärimudelile ja eesmärkidele kõige paremini vastavate lahenduste pakkumisele.
Selline pühendumus võib kaasa tuua kvaliteetsed teenused, uuenduslikud lahendused ja koostöö, mis aitab oluliselt kaasa teie ettevõtte edule.
Kokkuvõttes
Kuigi tootmistarkvara valimisel tuleb arvestada paljude teguritega, on oluline vältida liiga paljude valikute ülekoormamist.
Valige kolm kuni viis põhitegurit, mis on teie vajaduste jaoks kõige olulisemad. Nende omaduste hulka kuulub tarkvara kasutusmugavuse, funktsionaalsuse ja klienditoe kvaliteedi hindamine. Pidage meeles, et õige metallitarkvara võib ühtlustada teie tootmisprotsesse, suurendada tõhusust ja lõppkokkuvõttes aidata kaasa teie projekti edule. Seetõttu tasub investeerida aega hästi läbimõeldud otsuse tegemisse, kuid samal ajal vältige analüüside paralüseerimise lõksu langemist.
Oletame, et olete veendunud, et digitaliseerimine on õige tee, kuid te ei tea veel, kas see toob teile investeeringu tagasi. Siis olete oodatud lugema mõningaid juhtumiuuringuid, mis näitavad, millist tulu on teised sarnased ettevõtted valmistustarkvara rakendamisega teeninud.
Allikad:
https://www.tekla.com/
https://www.aveva.com/
https://construsteel.com/en/
https://eu.syspro.com/
https://www.strumis.com/
Selle artikli koostamisel on kasutatud erinevate veebisaitide ressursse. Konkreetne teave on saadud eespool nimetatud allikatest.
Mis on metallitootmise tarkvara?
See on tootmise planeerimise ja tootmisprotsessi juhtimise süsteem, mis on loodud lehtmetalli ja terase töökodade jaoks. Erinevalt üldistest ERP-süsteemidest saab sellega hakkama pesade paigutuse, materjalide langetamise, lõikelehtede ja keevisõmbluste marsruutimisega.
Milline metallitootmise tarkvara on parim aastal 2025?
“Parim” tööriist sõltub kaupluse suurusest ja töökorraldusest. Väikeste ja keskmise suurusega töökodade jaoks on EZIIL Starter eelarvesõbralik valik, mis ühendab MESi sügavuse ja kasutajaliidese, mida teie meeskond saab kiiresti õppida. StruMIS ja SigmaNest domineerivad suurettevõtete paigaldamisel.
Kui palju maksab StruMIS?
StruMISi müüakse moodulite kaupa; tüüpiline 10 kasutaja pakett koos pesade ja inventariga algab umbes 18 000 euroga, millele lisandub iga-aastane hooldus. Kui otsite eelarvesõbralikku alternatiivi, on EZIIL Starter parim valik väikestele ja keskmise suurusega metallitöötlemispoodidele.
Milliseid funktsioone peaks metallitootmise tarkvara sisaldama?
Otsige BOM-i importi, pesade optimeerija, reaalajas toimuva töö jälgimist, töökoha terminale, Gantt-ajaplaneerimist ning tööjõu ja jäägi analüütilist analüüsi.
Kas MES või ERP on metallitootmise jaoks parem?
MES on spetsialiseerunud igapäevasele tootmise kontrollile; ERP tegeleb finants- ja ostutegevusega. Paljud tootmisettevõtjad kasutavad raamatupidamiseks lihtsat ERP-süsteemi ja ühendavad MESi, nagu EZIIL, tootmisosakonna üksikasjadega tegelemiseks.
Kui palju maksab metallitootmise tarkvara kokku?
Kerged tarkvaravahendid, nagu EZIIL, algavad 90 eurost kuus; täisfunktsionaalsed kohapealsed komplektid võivad ületada 50 000 eurot pluss tugiteenus. Ootuspärane tasuvus 6-12 kuu jooksul, kuna väheneb praakimine ja ületunnid.