The four basic welding positions are flat (1F/1G), horizontal (2F/2G), vertical (3F/3G) and overhead (4F/4G). Each letter tells you whether it’s a fillet (F) or groove (G) weld, while the number marks the work-piece orientation. Higher codes like 5G or 6G combine challenging angles for certification tests.
Non-welders might assume that experienced welders sit in a work area throughout their shift and weld the metal components on their worktable, moving around the table occasionally while repositioning the workpiece as necessary.
However, in the real welding world, that’s not the norm. Joining two metal parts is challenging since workpieces are often attached to the floor, ceiling, or an out-of-the-way location.
Thus, welding positions are essential to every welding operator’s workday.
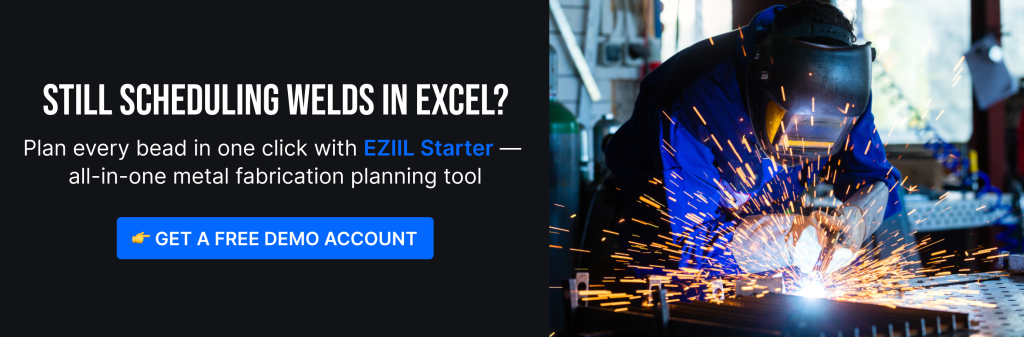
What is a Welding Position?
A welding position is a technique of joining metals from different angles. Typically, welders use five welding positions: horizontal, flat, vertical, overhead, and inclined. The most frequently-used welds are grooves and fillets, which welders can perform in all five positions, while other welds might use only one or two positions.
Unique letters designate fillet and groove welds (image credit: https://weldguru.com):
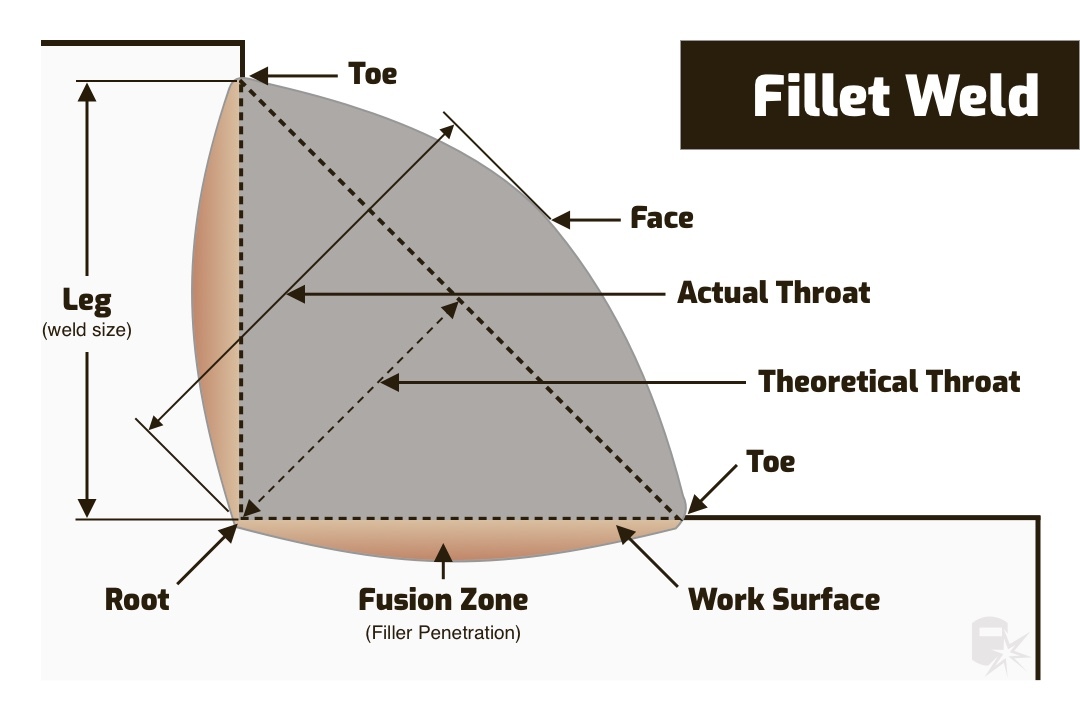
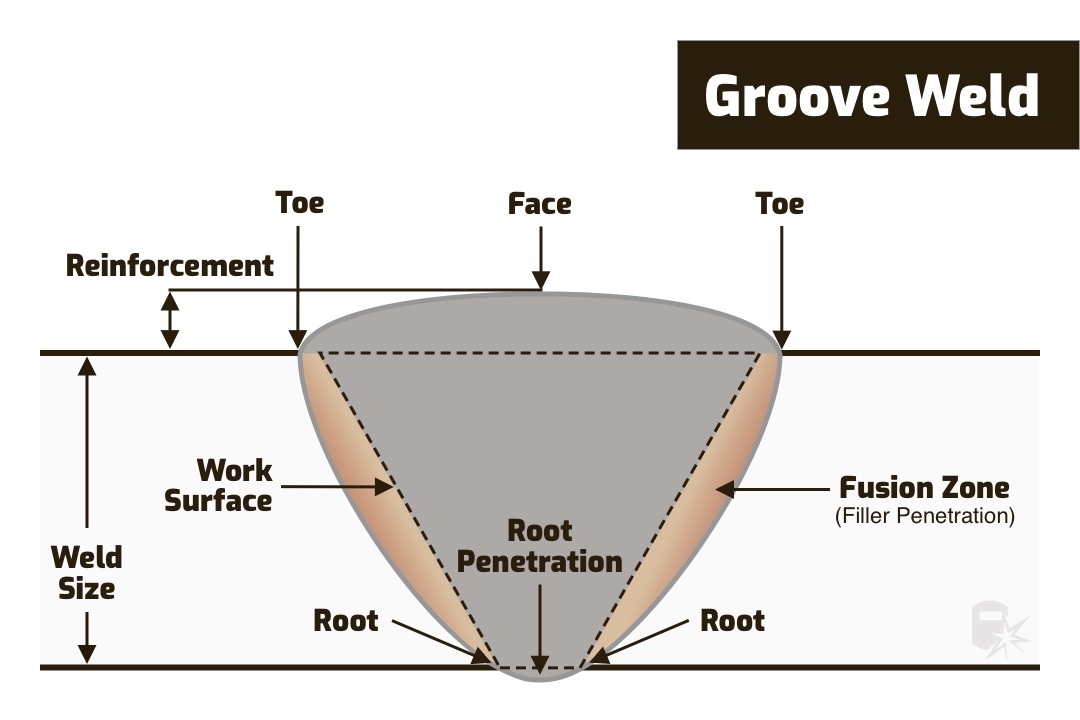
The Welding Positions
The letters associated with the numbers listed below are F and G. As mentioned, F is fillet, and G is groove.
#1 Flat Position: When the welder locates the workpiece on the floor or workbench, the position is called the flat position. It is considered the most accessible position because you are not welding against gravity. When using the flat position, it’s best to maintain the tip angle, flame position, and consistent motion. The tip should be at a 45-degree angle with the plate surface.
In the flat position, the weld puddle goes into the joint evenly in a fluid state. The molten metal might be hotter than usual, and the deposition rate will be higher because gravity draws the metal downward at the joint. You can do every welding process in a flat position.
A 1F welding position indicates a flat welding position (1) with a fillet weld (F), while a 1G tells you it’s a flat position (1) but with a groove weld (G).
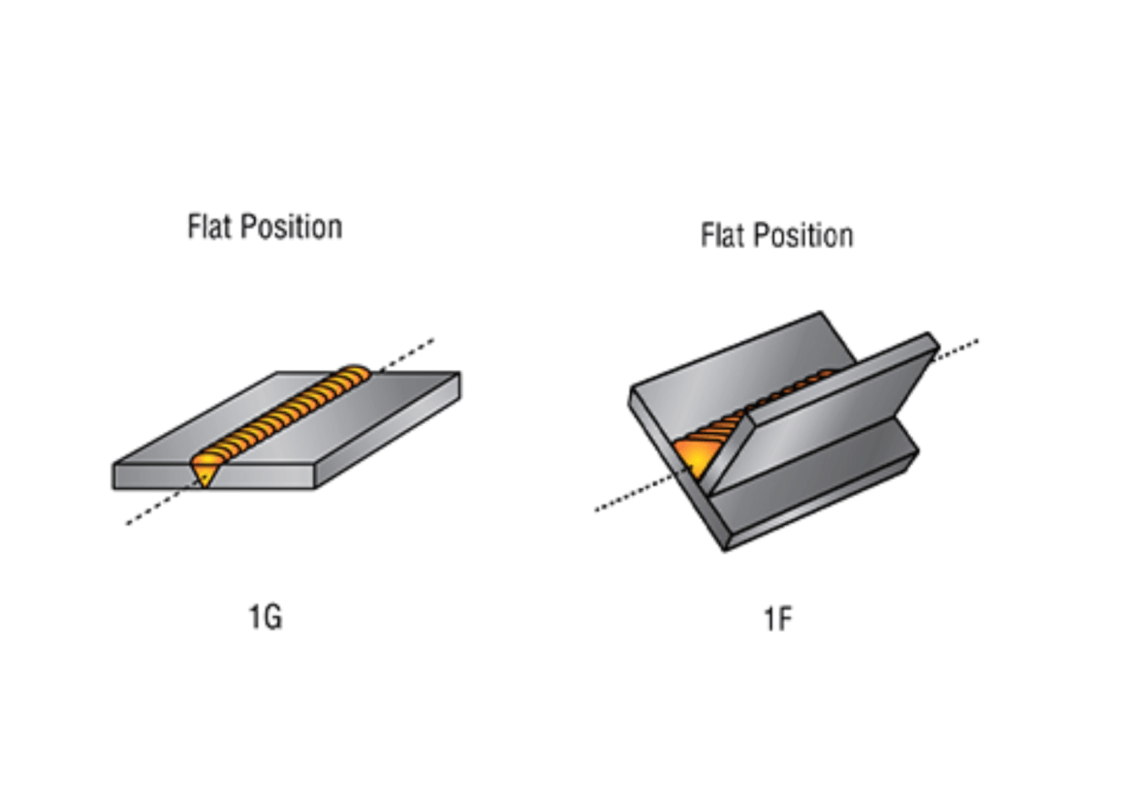
Image credit: https://www.millerwelds.com
#2 Horizontal Position: As the name implies, the welding axis stays horizontal during this process. For a 2F fillet weld, the welding is done on the upper side of the horizontal and vertical surfaces, and for a 2G groove weld, the welding is done on the vertical plane, and the face of the weld lies on the plane.
A 2G weld is slightly more challenging than a 2F weld since the weld puddle can sag. Gravity will take over if you run the molten metal too hot horizontally, so ensure the weld puddle is not too fluid. Compared to the flat position, the horizontal position needs more practice to perfect and is considered an out-of-position weld.
The 2F is a fillet weld position, with the torch angled at 45 degrees, and 2G is a groove weld position involving the weld axis in a horizontal plane and the weld face in a perpendicular plane.
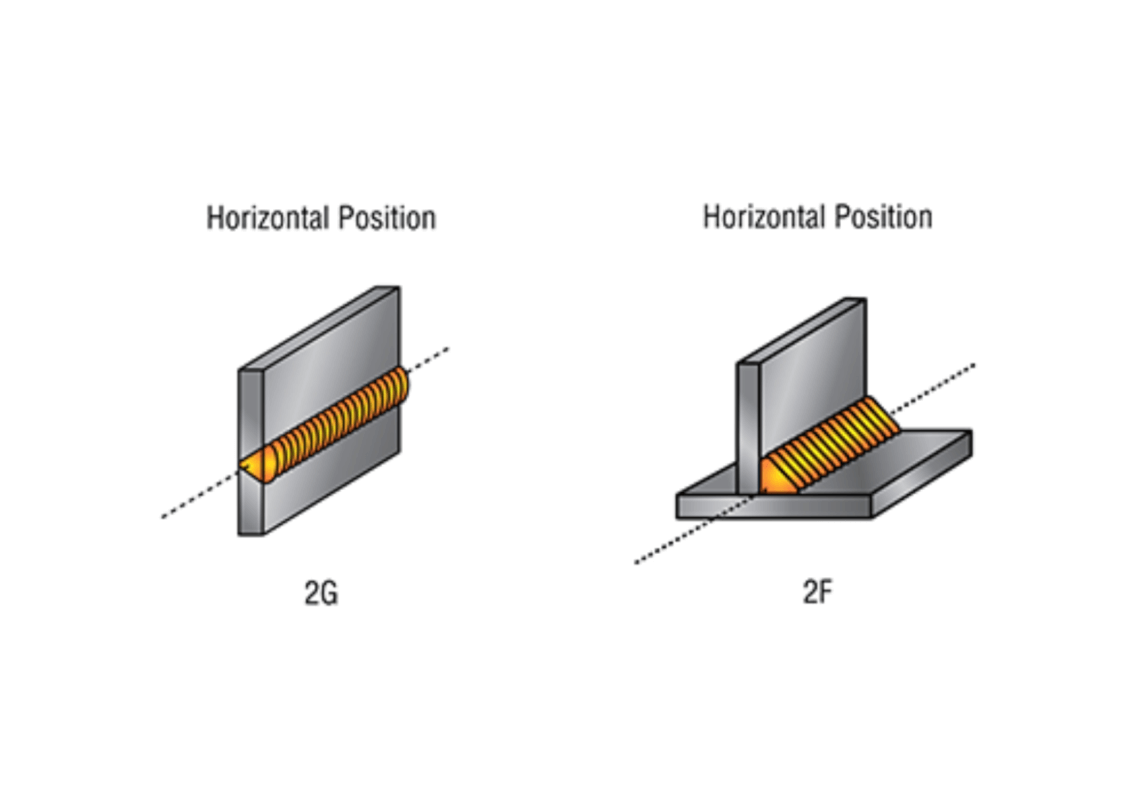
Image credit: https://www.millerwelds.com
#3 Vertical Position: In this process, the axis of the weld remains vertical–it can be vertically up or down. You can change the flame’s angle to control the metal flow, with the 90-degree angle suitable for 3G welding and the 45-degree angle for 3F welding. The primary consideration in the vertical position is puddle manipulation, and you can use a zigzag, upside-down, or triangular motion to do this.
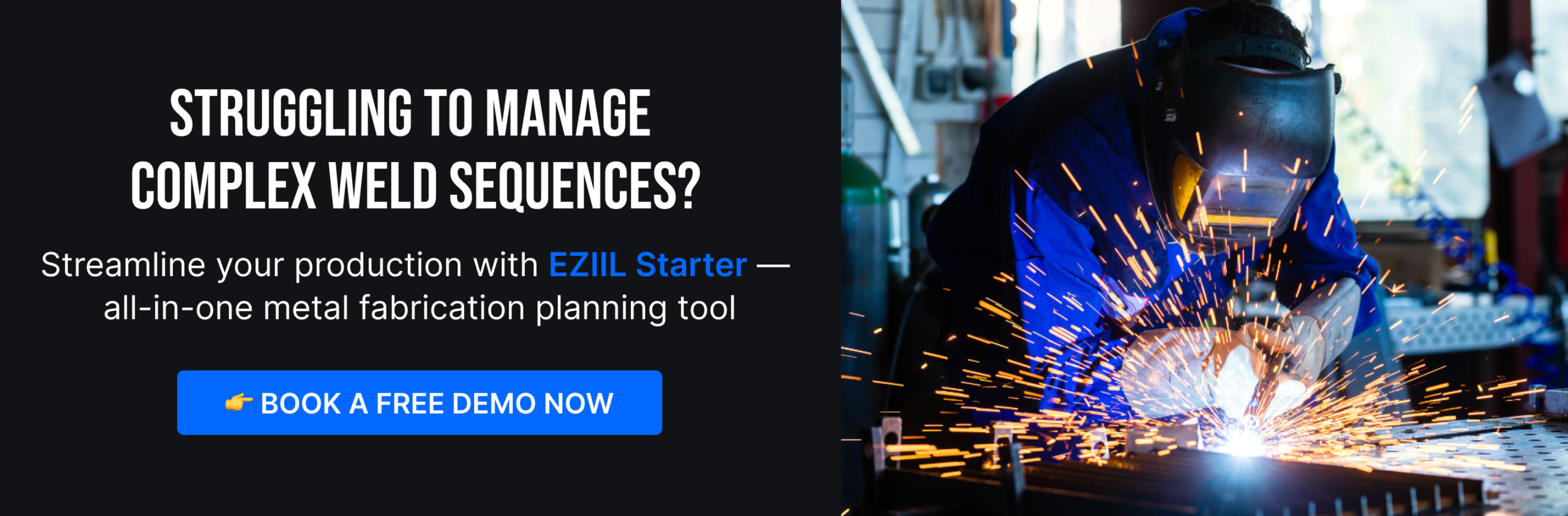
The workpiece and the weld are perpendicular or almost perpendicular in this welding position. 3F is the vertical fillet position, and 3G is the vertical groove. One issue when performing this weld is the molten metal flowing downward and accumulating.
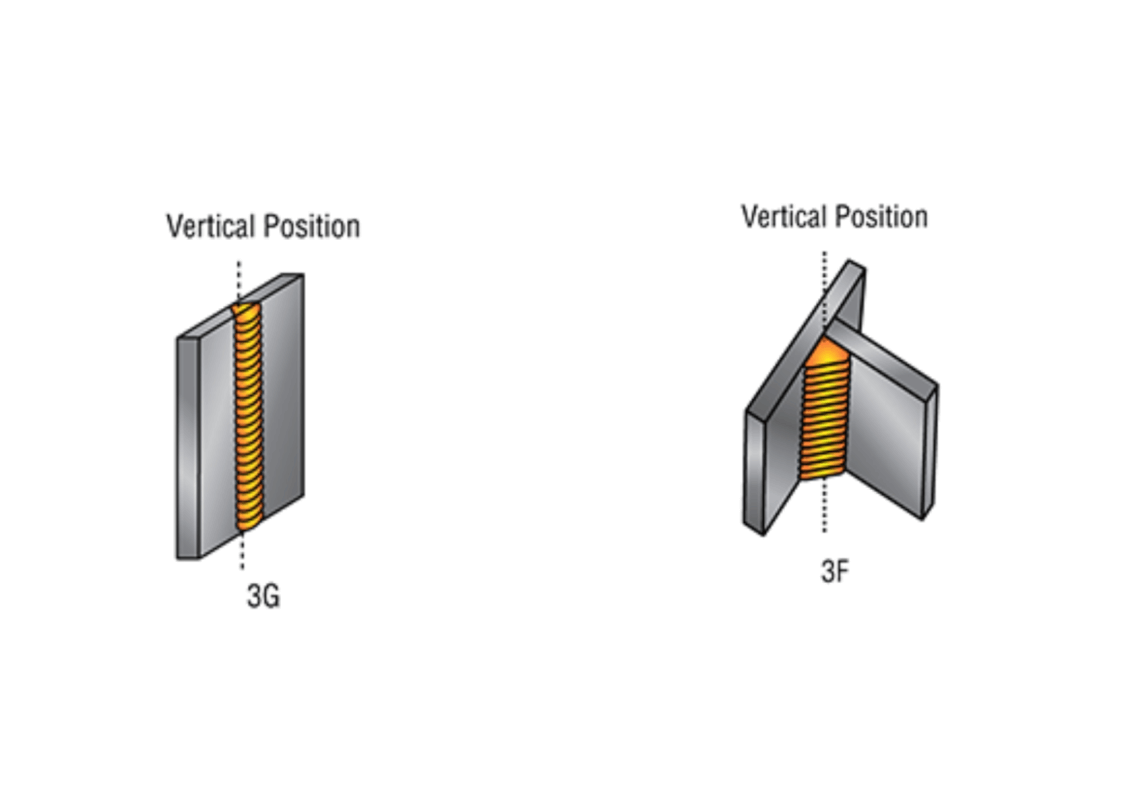
Image credit: https://www.millerwelds.com
#4 Overhead Position: When the welding is done from the lower surface of a joint, it is called the overhead position. The metal you deposit can sag, and the beads have higher crowns. Overhead welding is required when the workpiece is fixed and cannot be moved.
The flame should be regulated, so the metal gets enough time to freeze quickly. The techniques of the vertical positions are also valid with overhead, but it is critical to be aware of the falling sparks as you weld.
The challenging overhead position is performed with the torch at a 45-degree angle, and the 4G and 4F welding positions are appropriate for groove and fillet welds. Remember, the metal can sag from the plate, causing a crown, so keep the molten metal puddle small to avoid this.
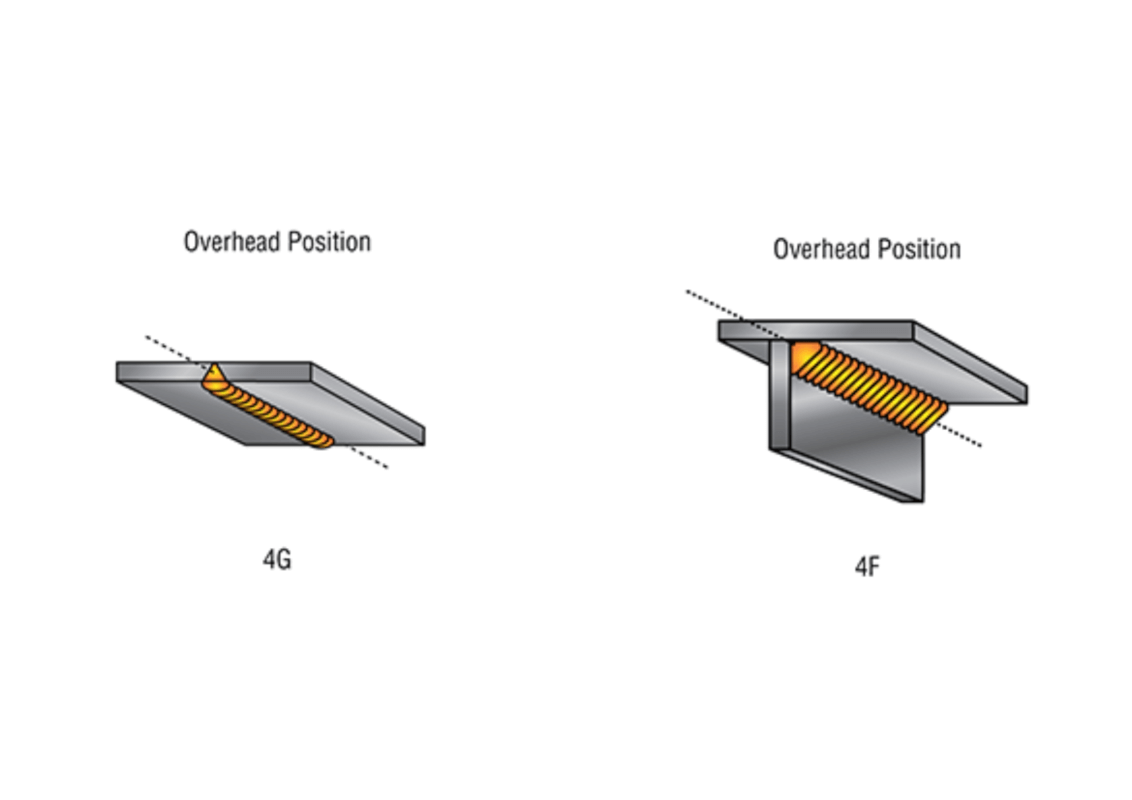
Image credit: https://www.millerwelds.com
#5 Inclined Position: The workpiece is placed in an inclined plane, and gravity causes the molten metal to flow downward in a flat position. A small arc produces the proper beads in the inclined position.
5G Welding Position: The 5G pipe welding position is used when the pipe’s axis is stable horizontally and cannot be turned or rotated. Two methods exist to complete these welds: 5G uphill and 5G downhill. In the former, welders start from the overhead position, go to the horizontal, and finally to the flat position. In contrast, with the downhill position, welders start from the flat position, progress to the horizontal position, and end with the overhead position.
6G Welding Position: One of the most challenging welding positions, 6G is similar to 5G, but the pipe is positioned at 45° to the other. The 6G position requires three welds: horizontal, flat, and vertical.
The difficulty comes from filling metal flowing downward and the fact that in the vertical position, it is overhead welding. The 6G weld position is primarily used for fabricating and installing pipes and pipelines in oil and gas plants, industrial plants, and any industry using pipes and pipelines.
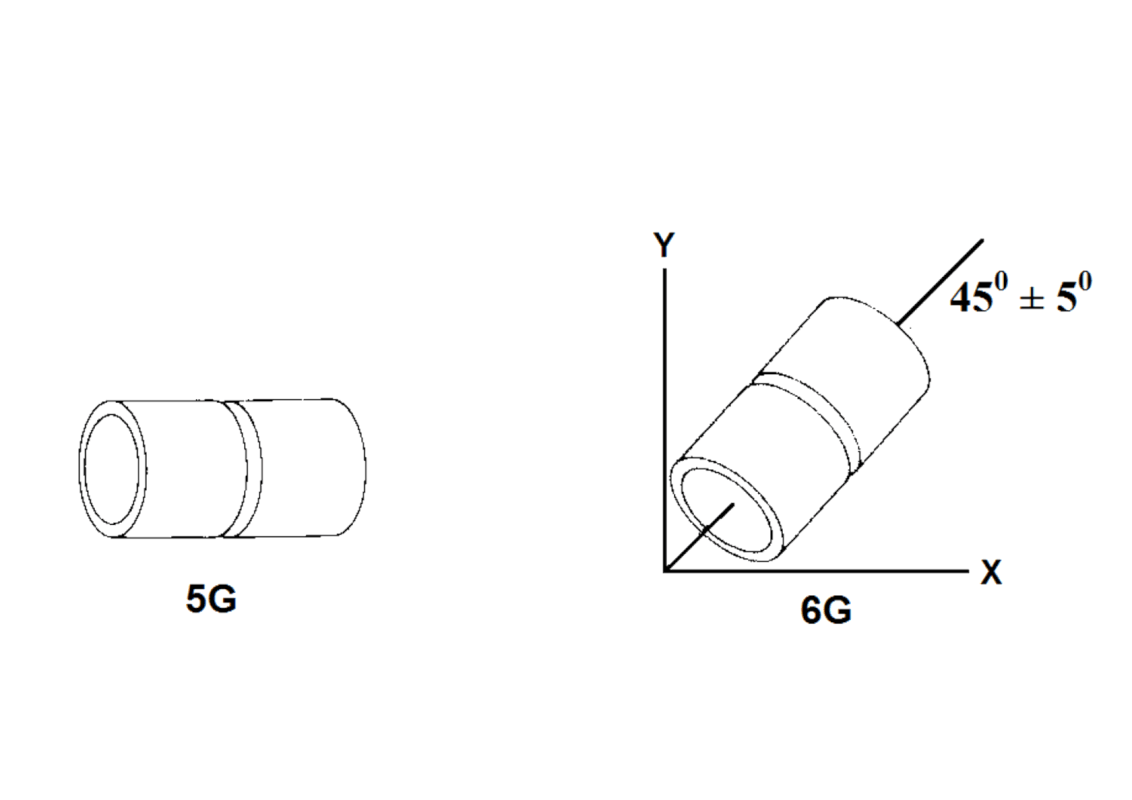
Image credit: https://www.weldingandndt.com
Conclusion
The information on welding positions like 1G, 2G, 3G, 4G, 5G, and 6G/6GR (see chart below) benefits students, welders, educators, and other professionals. Welding positions are essential in the welder certification process since new welders could be tested for jobs from 1G to 6G for fillet and groove welds.
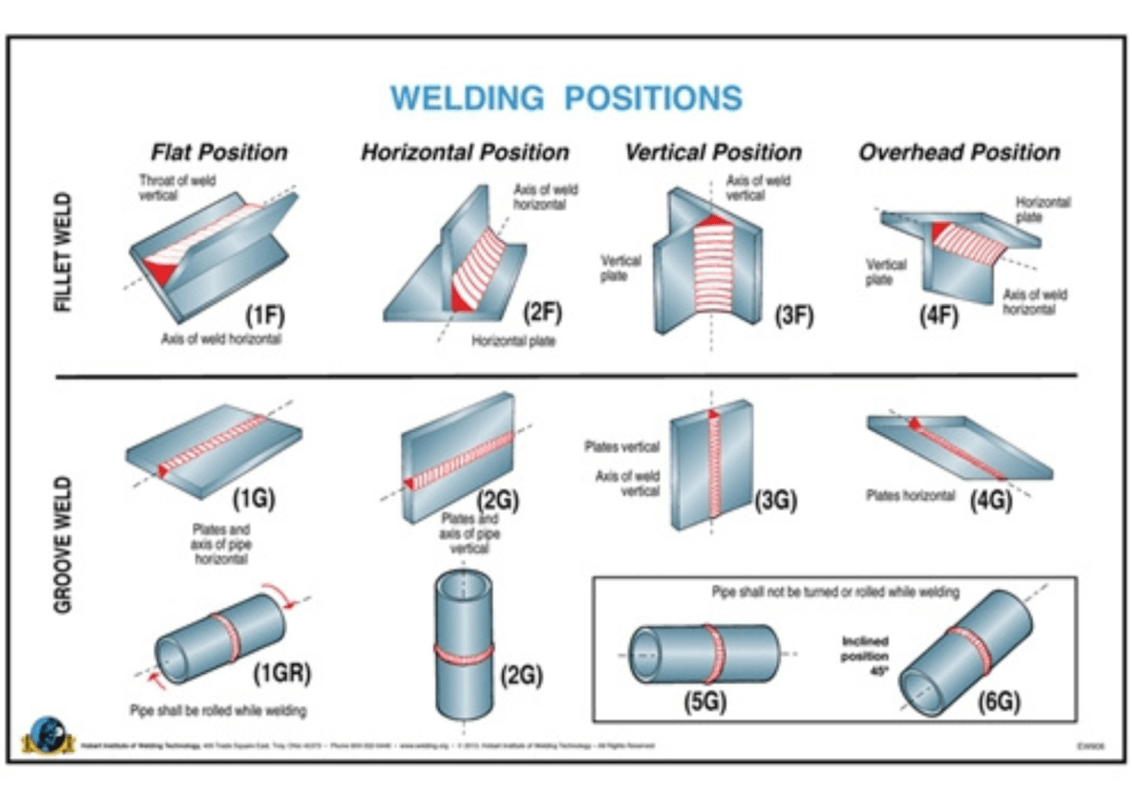
Welding is a critical process in product design and mechanical engineering, joining various components and structures together. Different types of welding, such as arc welding, MIG welding, and TIG welding, can be utilized depending on the application. A key factor in determining the success of a welding process is the welding position, which dictates the technique and approach required for achieving a strong and stable joint. This text will discuss four common welding positions: 1G, 2F, 3G, and 4G, highlighting their applications in pipe welding and the creation of fillet welds.
1G Welding Position
The 1G welding position, also known as the flat position, is the simplest and most comfortable welding position for most welders. In this position, the welder lays the workpiece horizontally, enabling them to deposit the weld bead using gravity. This position is frequently employed in pipe welding, where it is used to join pipes or tubes with a straight, horizontal axis. 1G is also suitable for creating fillet welds in a flat orientation. The use of filler metal in this position is straightforward, as it is fed consistently into the weld joint without the need for complex manipulation.
2F Welding Position
The 2F welding position, or the horizontal position, involves welding a workpiece positioned vertically, with the weld joint running horizontally. In this position, the welder must control the filler metal deposition carefully to prevent it from sagging or dripping due to gravity. Pipe welding in the 2F position requires the welder to maintain a steady and controlled motion, ensuring a consistent weld bead profile. Fillet welds can also be created in the 2F position, with the welder using appropriate techniques to compensate for gravity’s influence on the filler metal.
3G Welding Position
The 3G welding position, or vertical position, refers to welding a workpiece positioned vertically, with the weld joint running vertically as well. This position presents a higher level of difficulty, as the welder must manage the filler metal and weld bead while combating the effects of gravity. Pipe welding in the 3G position requires a high degree of skill and technique to ensure a consistent and robust weld. Similarly, creating fillet welds in this position demands precise control of the welding process and filler metal manipulation.
4G Welding Position
The 4G welding position, also known as the overhead position, involves welding the underside of a workpiece positioned horizontally. In this position, the welder must contend with the most challenging conditions, as gravity works against the filler metal and weld bead deposition. Pipe welding in the 4G position necessitates excellent technique and control to prevent the filler metal from falling out of the joint. The creation of fillet welds in the 4G position is also a complex task, requiring a high level of skill and expertise in the welding process.
In summary, the four welding positions, 1G, 2F, 3G, and 4G, play a significant role in the success of various types of welding processes in product design and mechanical engineering. These positions influence the approach and techniques required for pipe welding and the creation of fillet welds. A welder’s ability to master these positions and manipulate the filler metal and weld bead effectively is crucial for ensuring strong, durable, and high-quality welds.
What are the 4 basic welding positions?
The basic positions are flat, horizontal, vertical and overhead. They’re numbered 1 to 4 and define the angle between the weld and gravity.
What do 1G, 2G, 3G and 4G mean in welding?
The number shows the work-piece orientation; “G” means a groove weld. 1G is a flat groove, 2G horizontal, 3G vertical and 4G overhead.
How many welding positions exist in total?
Standards list four foundational positions, but test codes add 5G, 6G and 6GR for pipe or complex angle welds—so up to seven in practice.
Which welding position is easiest for beginners?
Flat position (1F/1G) is easiest because gravity helps the molten pool spread evenly and reduces the chance of sagging or porosity.
Why are 6G welds harder than 3G welds?
A 6G test fixes the pipe at a 45° incline, forcing you to weld in multiple orientations without moving the work-piece—so it bundles several difficulties into one certification.
Does welding position affect joint strength?
Yes. Out-of-position welds (vertical, overhead) often need different travel speeds and amperage. Poor settings can lower fusion and reduce joint strength.