FabTrol MRP was discontinued in June 2022 after its owner (AVEVA) stopped new sales and support. Existing licences still run, but no updates or security patches are issued, so most fabricators are migrating to alternative solutions like EZIIL.
The fabrication industry is evolving, and while change is often necessary, it can also lead to challenges and uncertainty. For fabricators, even minor process changes can impact productivity and increase costs. And in 2022, fabricators are experiencing a massive change. AVEVA announced the discontinuation of its steel fabrication management software FabTrol.
MRP systems like Fabtrol are fundamentally important to every aspect of a fabrication. Without an MRP system in place, the flow of information is interrupted, creating production delays and causing added stress, work, and costs. Further down the line, delayed production can also lead to lost business due to dissatisfied customers.
FabTrol has been in use since the 1980s and has since become a staple in many fabrication shops. Now, as FabTrol is sunset, many fabricators that have used Fabtrol to run their businesses for years are scrambling to find a replacement that fits their budgets and minimizes disruptions to their production and fabrication timelines.
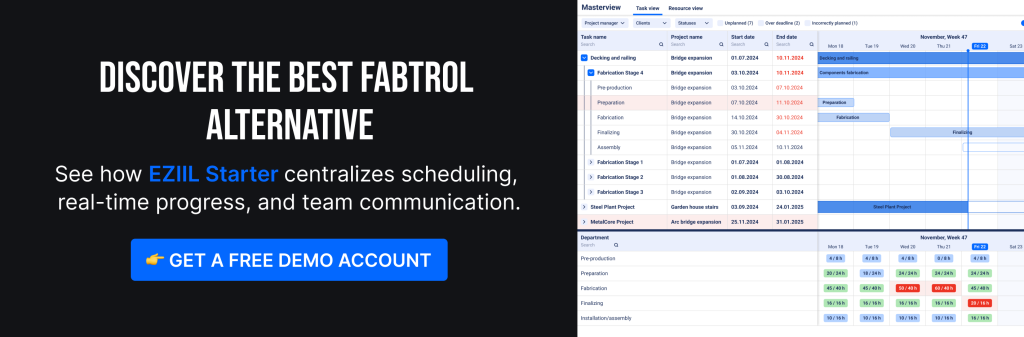
This change comes at an especially challenging time, as fabricators are still struggling with the impact of labor shortages and supply chain disruptions that have persisted in the wake of the COVID-19 pandemic.
The following article breaks down what FabTrol was, its key features and capabilities, why it was discontinued, and what are the risks of staying in a discontinued system like a FabTrol and what to keep in mind in next-generation alternative solutions.
What was FabTrol?
Founded in Eugene, Oregon in 1985, FabTrol Systems was a leading provider of material requirements planning (MRP) software for steel fabrication management. Targeted to mid-to-large fabricators, the platform provided a modular suite of tools and features to streamline fabrication management.
What Were FabTrol’s Key Capabilities
FabTrol offered a range of capabilities that helped fabricators save time, streamline their processes, and avoid costly errors or delays. These included, but were not limited to:
- Cost Estimation: Users could quickly generate accurate project estimates.
- Drawing Management: The software streamlined drawing management, including automatically tracking changes and approvals, which reduced delays and eliminated the risk of errors due to manual data entry.
- Material Management: FabTrol made it easy to optimize material usage, manage material inventory and purchasing based on usage data, and more.
- Production Management: Users could visualize and monitor production progress and keep production on track.
- Project Management: Users could create RFIs, plan project and resource schedules, and manage change orders.
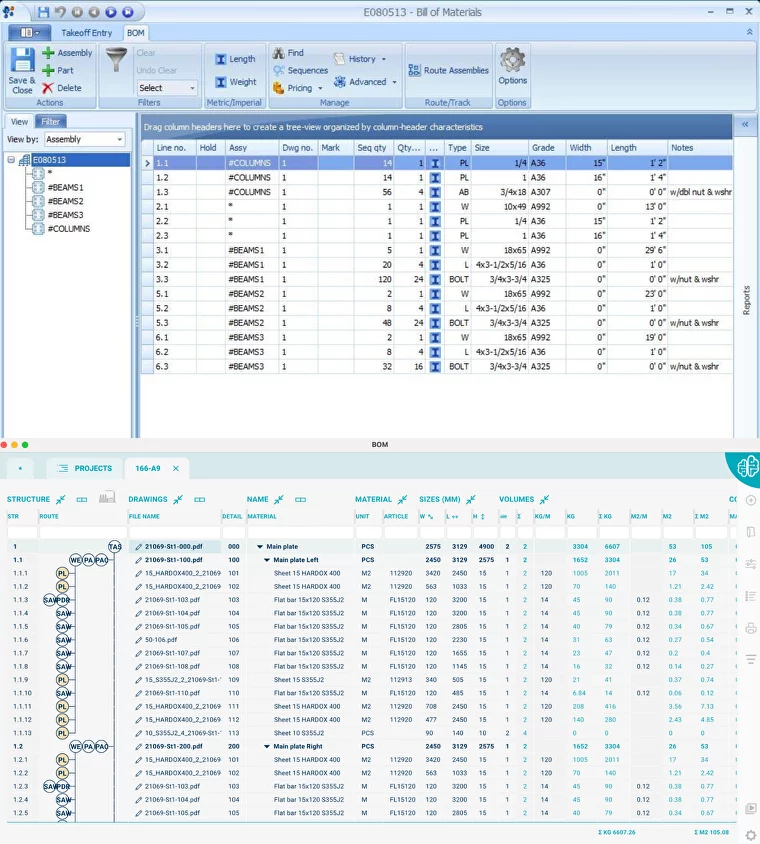
What was Fabtrol Pricing?
When FabTrol was still available for purchase, the costs varied, depending on the number of users and the agreed upon package. However, there is no longer any option to purchase FabTrol, as it is no longer being sold or supported by AVEVA.
What happened to FabTrol?
FabTrol was founded in 1985 by Douglas Cochrane, the result of several years of attempting to “[teach] himself how to program computers and write software to help steel fabricators more closely estimate the cost of projects” (TMCnet). Shortly after founding the company, Cochrane hired saleswoman and welding shop owner Gerry Dennis.
Together, Cochrane and Dennis would build FabTrol into a leading software solution that helped fabricators estimate costs and seamlessly control every aspect of production–including project management, drawing management, and materials management. The software was quickly recognized as a way to save time, accurately estimate project costs, effectively manage products, and virtually eliminate the risk of costly errors due to manual data entry.
By September of 2008, FabTrol Systems had earned 1,050 customers across 22 different countries–and was rapidly growing. At that time, FabTrol courted several offers to purchase the company, and they ultimately chose to sell the company to Dowco Group of Companies, a privately held Canadian firm with plans to expand FabTrol internationally through authorized sellers.
By 2015, FabTrol had continued to expand its market to more than 1,400 global customers, and operations in both North America and the United Kingdom. In June of 2015, FabTrol was acquired by AVEVA, who purchased FabTrol from Dowco for $6.5 million USD. AVEVA continued to offer the solution under the name AVEVA FabTrol until mid-2022.
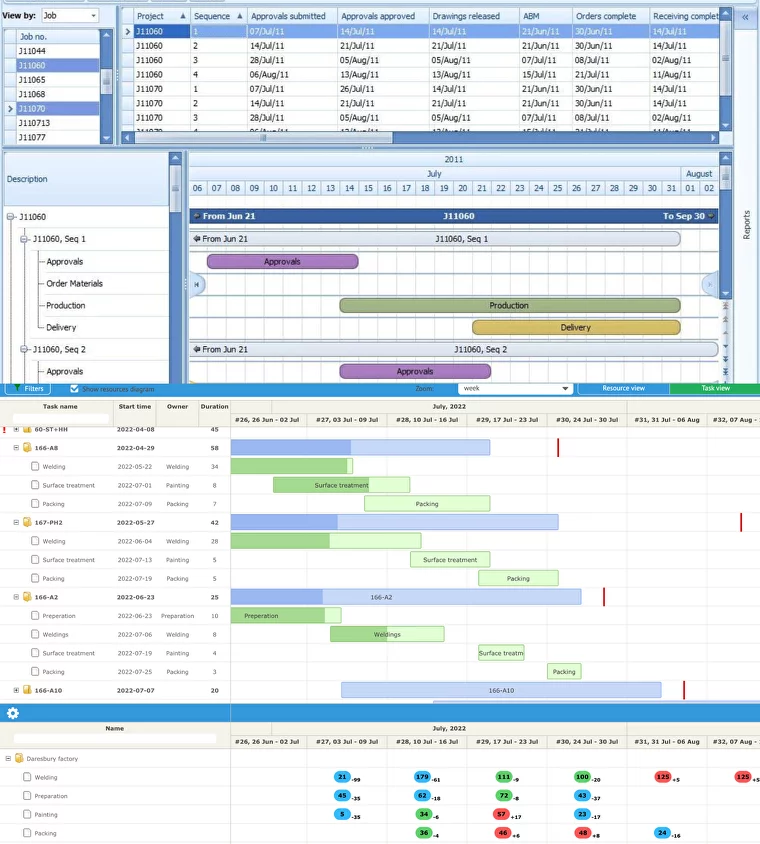
When was FabTrol Discontinued?
As AVEVA shifted focus towards other areas of their business, they made the decision to sunset the FabTrol platform (AVEVA). All sales and development of FabTrol ended on July 22, 2021. Starting September 1, 2022, FabTrol will be officially withdrawn and all license agreements and customer support for FabTrol will end. Therefore, it is critical for fabricators to find a new MRP solution quickly to avoid costly disruptions.
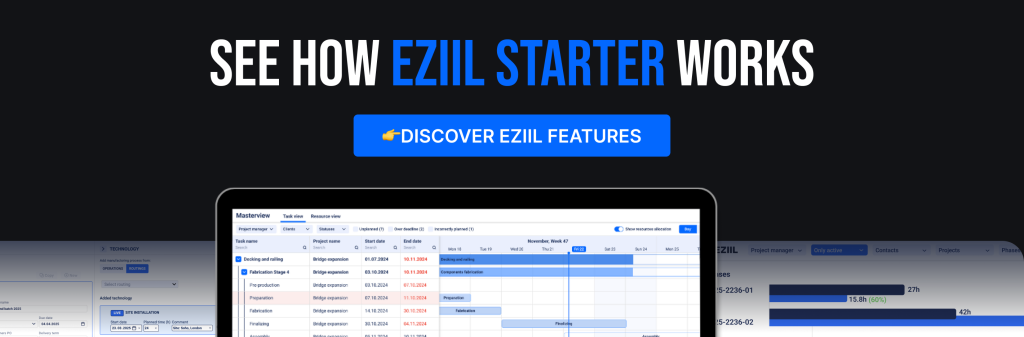
Why continuing with FabTrol MRP can be risky
Every fabricator knows it can be quite time-consuming and costly to change MRP systems. Vetting and implementing a new solution can take time, and because the MRP system is central to everything a fabricator does, choosing the right system is a major decision. However, putting off the transition away from FabTrol poses significant risks that outweigh any benefits of remaining on the old platform. The following are several implications of the FabTrol discontinuation that fabricators need to be aware of:
- No support. Since AVEVA will no longer support FabTrol as of September 1, 2022, users remaining on the platform will be on their own. Even though your users know the system well, they may still need support on how to use additional features, or they may run into other unexpected issues that they aren’t able to troubleshoot. Today, there are still many users that know how to use the FabTrol system. However, as more fabricators move away from FabTrol, there will be fewer and fewer skilled workers available with competency in FabTrol. So, while you can in theory use FabTrol for as long as possible, eventually it will come to a point where something breaks…and it won’t be possible to fix it anymore. Staying on the platform is essentially a ticking time bomb: you are taking on an incredibly high risk and may eventually need to urgently replace a solution that you can no longer use. This could potentially take your production down for an extended period of time, costing you more money in the long run and putting your customer relationships at risk.
- Legacy functionality. The fabricating environment is constantly evolving. The industry continues to innovate with new CAD systems, better ways of planning projection, new types of machines, etc. All of this demands that your MRP system remains up-to-date–something FabTrol will no longer do. Long term, leaving a legacy system like FabTrol in place will create more manual work that your competitors will be able to accomplish with newer, automated solutions.
- User experience. As the current workforce continues to age and more skilled workers approach retirement age, older industries share the challenge of how to hire and retain the next generation of talent. This younger generation of digital natives are keen to keep up with latest technologies and trends–whether it’s sharing videos with the world on TikTok or tracking their every move with their Apple Watch. For them, working in an environment with outdated tech is demotivating and can lead them to seek employment elsewhere. Younger workers will be more likely to join a company (and stay there) when they can keep their skills fresh by working with the latest technologies in their industry.
- The change won’t get easier with time.The longer you wait to make the change, the harder the change will be. You have an opportunity to find the right MRP for your business without taking on the added risks of remaining on a platform that is no longer supported. Plus, workers that continue to use an outdated system for long periods of time will form habits using the old system. This can make it more difficult for them to make the switch later on, especially when the new system is philosophically very different from what they are accustomed to–ultimately putting your MRP implementation at risk of failure.
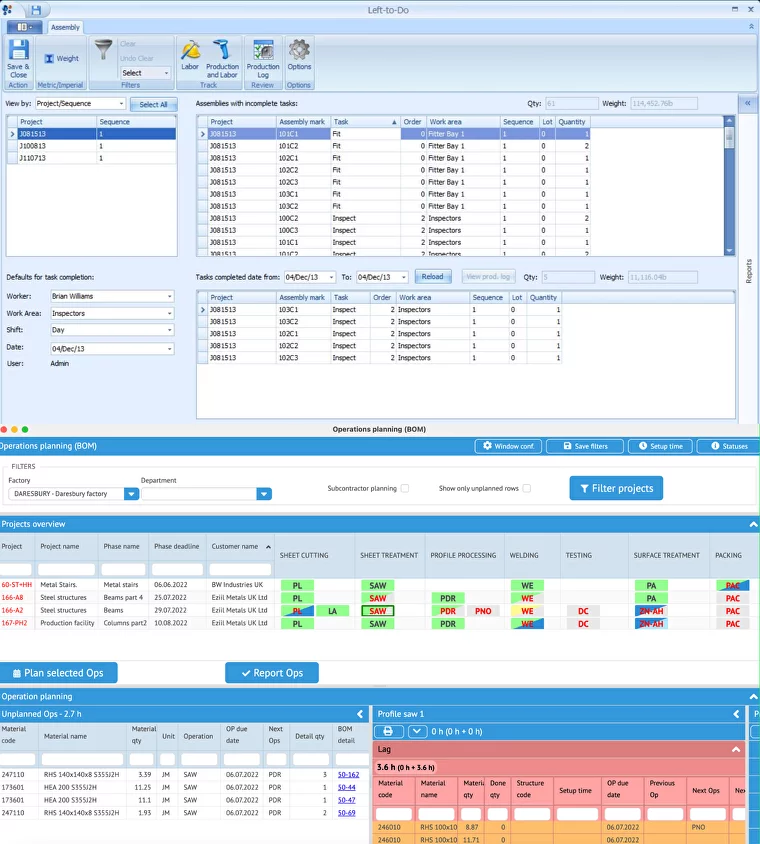
What to consider on going over to a new solution?
There are several important considerations when evaluating a new MRP solution. For example, you must consider:
- Is it a general solution or specific solution for fabricators? Selecting a general solution can be more cost effective, but there is a risk that a more general solution may not cover a fabricator’s specific needs. Selecting a solution that is specifically designed to support the fabricator work flow process can be more expensive, but has a lower risk of failure. Keep in mind that selecting a less expensive solution can actually end up costing more in the long term–in terms of both time, resources, and overall investment–if the solution isn’t suited to your workflows.
- What is involved in migrating data from one system to another? With a system change, there is often the risk of losing your historical sales and production data. However, in some cases, you will be able to export your data from the previous system and important it into the new system. The fastest way to accomplish this is to request data migration services from a vendor who knows the system well enough and can instruct you along the way. This service may come at an additional cost , but it can significantly speed up the process and give you the peace of mind that it’s correctly done. This is also a great time to recognize that every challenge also presents opportunity. For example, if there are frustrating aspects of your existing setup or article code system that needs to be changed, this is the perfect time to make those changes.
- What are the costs of changing people’s habits and processes? Every change is a process of death, something old must die so that something new can be born. This process is never easy and should not be underestimated. Your company has run on MRP and your people are used to relying on that system. Now, bringing something new means changing your processes and ensuring that your team knows how to use the new system and are trained on the new processes. Without proper training this creates a lot of stress that people will often try to relieve by not doing new processes and continuing in the old way, or by starting to bend the system to be closer to what they were familiar with. Either way, this can disrupt the implementation process and lead to the conclusion that “this doesn’t work for us”. To avoid this pitfall, it’s important to not only be aware of the risk and address these behaviors proactively, but also partner with professionals that can guide you and support your people along the way.
- Does the vendor offer implementation support, or will you need to do all of the implementation work on your own? The value of having a knowledgeable consultant available to support you cannot be underestimated. .Even if everything is planned and done right, changing MRP systems is complex, and you’ll need fast, reliable support in case issues arise. You can not afford to stop production until someone figures out what the problem is and can test potential solutions. Including vendor professional support in the process will lower your risk of stops and downtime time, because they know their own system inside out and will know what to do if something unexpected arises.
- What is the cost model? For example, is it an onsite license model or a SaaS cloud model? This can be a philosophical change in mindset. In early days, all the licenses were sold as license fee, and you had your own onsite servers to keep it up and running. Nowadays, the world is moving on cloud strategy and software as a service (SaaS) is a new reality. This offers the benefit of lowering your initial capital investment and reduces the complexity of the implementation because you only need an internet connection to get started.
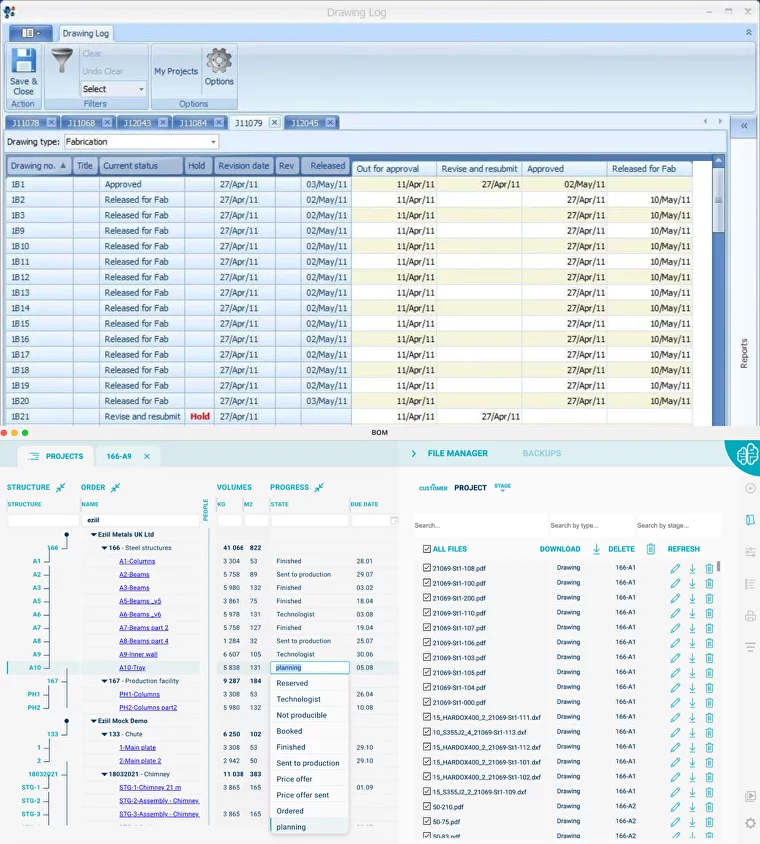
What is a Good Replacement for FabTrol?
There are many MRP solutions on the market today, a reality that can be overwhelming for fabricators looking for a replacement that can integrate effortlessly into their fabrication workflows.
Eziil has quickly emerged as the best MRP software to digitize production for custom metal fabrication. That’s because Eziil is specifically designed to support the workflows of project-based production–rather than serial production–where each project is unique. Eziil provides a seamless flow of information without adding administrative strain to your processes.
Eziil is the next generation of fabrication management, a powerful and easy to use solution that seamlessly fits into your fabrication toolbox, digitizes your production, and turns your data into knowledge – and action – in real time.
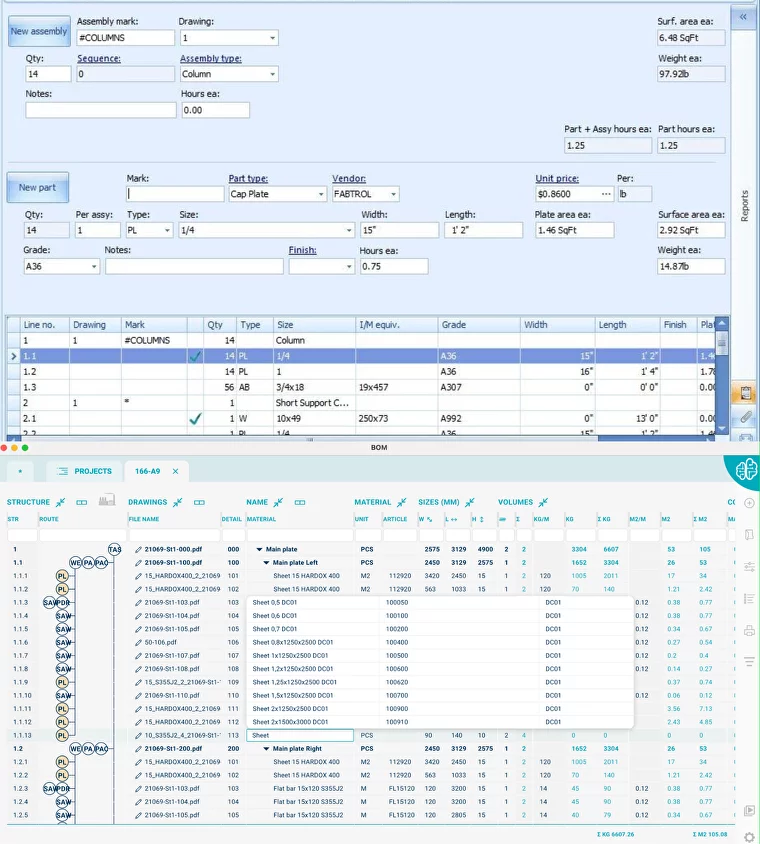
The following are several advantages of Eziil:
Plan and optimize your resources in real-time
Know exactly how much production capacity you have and prevent bottlenecks, so you commit to your customer deadlines with confidence.
Get total warehouse control and visibility
With Eziil, you know exactly what materials you already have and what you need to purchase across all projects: no more guesswork or hours spent pouring over inventory spreadsheets.
Stay on top of your production schedule
Get a live project progress overview form the shopfloor. Assign digitized work orders to shop employees and get real-time progress feedback.
Close the gap between estimations and real results
Compare project price estimates against actual performance and find out where your profit is made. Understand how they impact the higher-level P&L.
Eziil is a low-risk solution available with a SaaS cost model that allows you to pay on a monthly subscription basis. This reduces the risk of tying up large amounts of capital into a new investment. Furthermore, Eziil provides ongoing support to migrate your data and implement the new MRP system. We support you every step of the way.
Is FabTrol MRP still supported?
No. AVEVA stopped all new sales and mainstream support in June 2022; only self-hosted licences continue to run without updates or security patches.
Why was FabTrol discontinued?
The code base lagged behind cloud and model-integration demands. AVEVA redirected R&D to Tekla-branded products after the Trimble/AVEVA asset swap.
What are the best FabTrol alternatives?
EZIIL Starter for small-to-mid job shops, EZIIL Enterprise for large multi-site fabricators, StruMIS or SigmaNest where deep nesting is critical.
Can I migrate FabTrol data to Eziil?
Yes—you can import CSV or SQL exports of FabTrol BOMs, drawings and inventory; expect 2–4 weeks for data mapping.
How much does a FabTrol replacement cost?
Cloud-based software starts at €90/month (EZIIL Starter). On-prem suites like Tekla EPM begin around €20k + maintenance.
What features should I look for in 2025?
Visual scheduling, API connectivity and cloud backups—none of which FabTrol now updates. |