Digitization plays a significant role in the manufacturing sector. With the help of digitization, various tasks in the manufacturing process can be automated, which leads to higher efficiency and accuracy. MES vs ERP, these are two of the most critical enterprise software systems a manufacturer can deploy. But with so much terminology flying around, it can be challenging to know which system is right for your company.
This guide will help you to differentiate between MES and ERP, and help you decide which system is best for your operations. We will also discuss their integration methods and benefits.
So whether you’re still trying to understand the basics or ready to start comparing specific features, read on to know more about ERP vs MES.
What is Manufacturing Execution System (MES)?
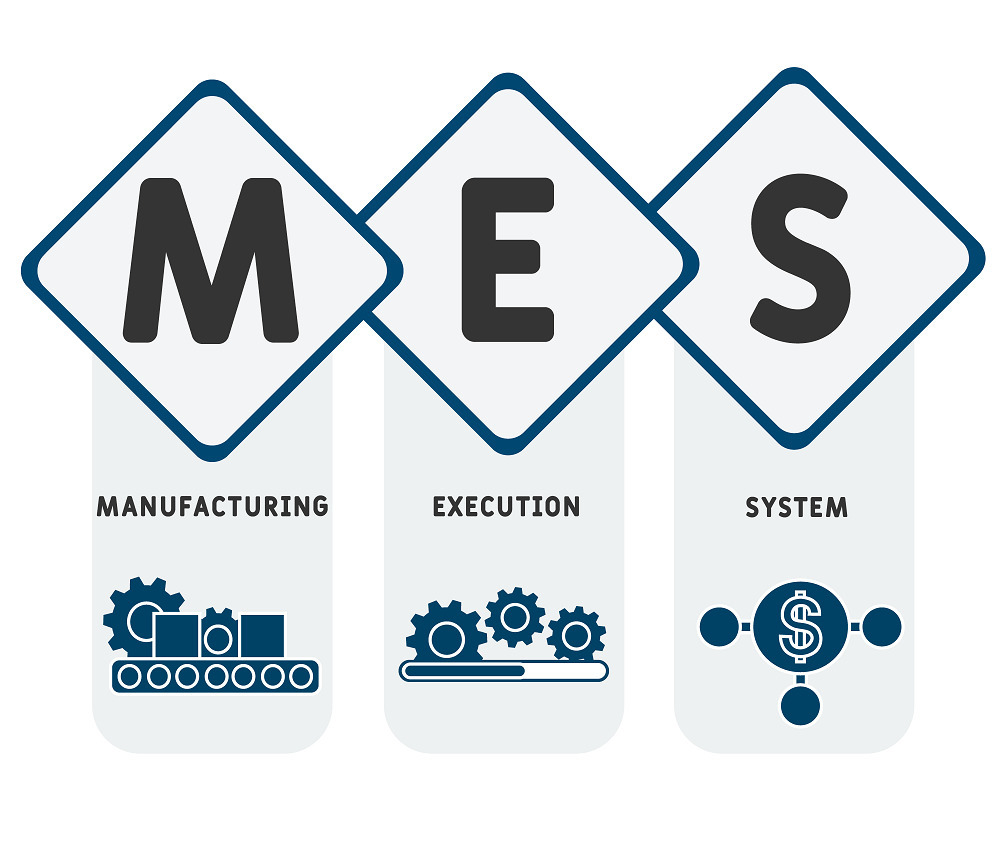
MES or manufacturing execution system, is a software application that helps businesses better manage their on-floor production processes. By giving real-time visibility into all factors of the manufacturing process, MES systems can help companies optimize their operations and improve overall efficiency.
Some of the significant manufacturing execution system functions are as follows:
- Provide Real-time Data: MES software can help optimize production processes by providing real-time data on equipment utilization and material levels.
- Product Tracking: MES software can also track and trace products throughout the manufacturing process, meaning that any issues can be quickly recitified.
- Valuable Insight: Manufacturing execution software can provide valuable insights into the manufacturing process, which can be used to improve efficiency and reduce costs.
How Does Manufacturing Execution System Work?
The manufacturing execution system works by gathering data from various sources within the manufacturing process. This data is then processed and analyzed to provide insights into the production process. Based on these insights, the MES system can provide recommendations on improving the production process.
What is Enterprise Resource Planning (ERP)?
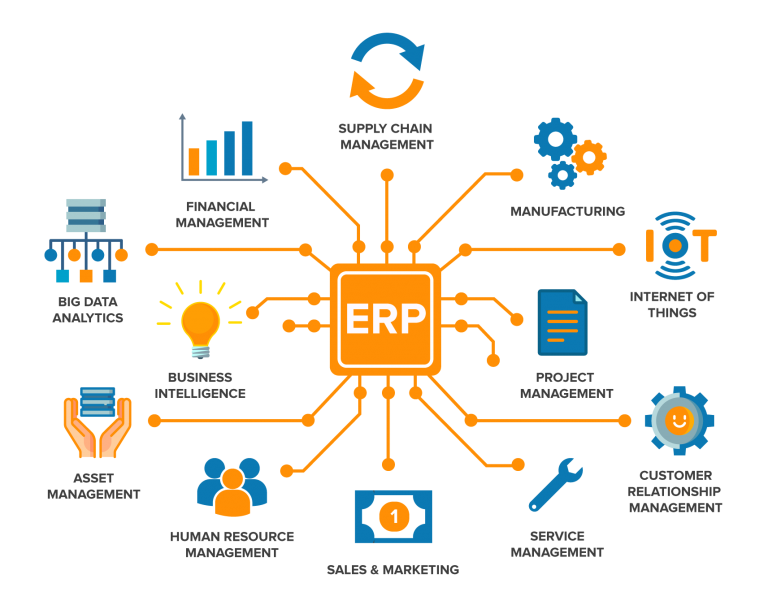
Enterprise resource planning (ERP) is also a business process management software that allows businesses to manage and automate many back-office functions, such as accounting, human resources, procurement, and supply chain management. ERP systems typically integrate with other software solutions, such as CRM, to provide a complete business view.
What does Enterprise Resource Planning System Do?
ERP systems are designed to help businesses manage their resources more efficiently and effectively. Here are three key ways that an ERP system can help your business:
- Improved visibility: An ERP system gives you a centralized view of all your company’s resources, including inventory levels, production schedules, and financial data.
- Increased efficiency: An ERP system can automate many of the tasks associated with resource management, such as ordering supplies and tracking production progress.
- Enhanced decision-making: An ERP system can help you make informed decisions about where to invest your resources for the best return by providing accurate and up-to-date information.
How does the Enterprise resource planning software work?
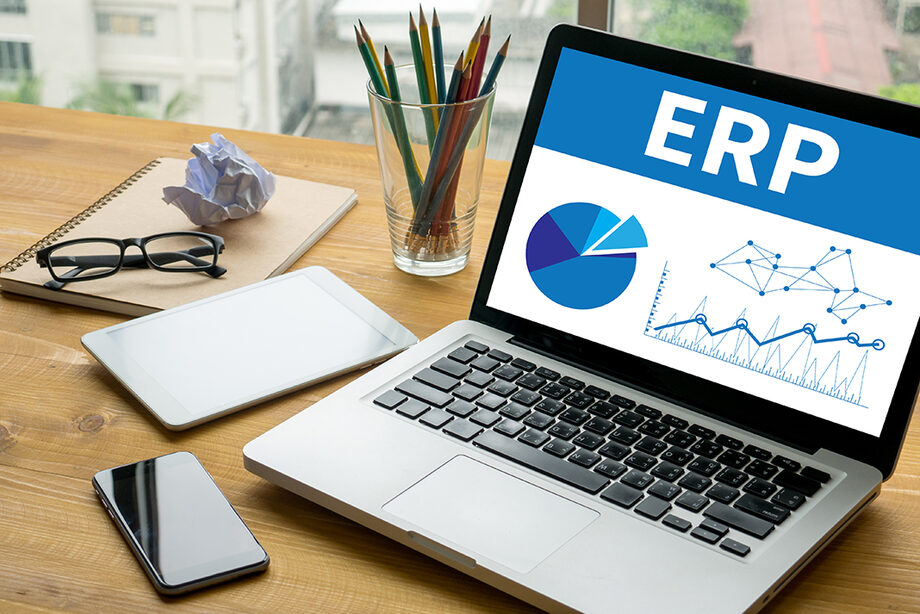
An ERP system gives you a centralized view of all your company’s resources.
Source: industrytoday.com
The ERP system integrates all the different departments within an organization, such as accounting, finance, human resources, inventory, and manufacturing, to provide a unified view of all the organization’s data. Furthermore, it can generate reports and track or manage customer orders, shipping, and invoicing. By automating these processes, you can significantly improve the efficiency of your manufacturing facility.
What are the main differences between MES vs ERP?
MES vs ERP are two different types of software used to manage various aspects of the manufacturing process.
- Operations: MES software focuses on managing and monitoring the production process on the factory floor, while ERP software provides a broader view of the business, including accounting, human resources, and supply chain management. While they are essential to the manufacturing process, MES and ERP serve different purposes.
- Data Visualization: MES system provides real-time reports, meaning that users can see up-to-date information on production progress and performance. On the other hand, ERP provides periodic reports, typically daily, weekly, or monthly. This means that users must wait for the report to be generated before viewing the data. While MES is beneficial for tracking short-term trends, ERP is better suited for long-term planning and decision-making. As a result, many businesses use both systems to get the most comprehensive view of their data.
- Complexity: ERP software is typically more complex than MES software because it must integrate with other business systems. On the other hand, MES software is more focused on managing the production process and typically does not require integration with other business systems.
- Integration: The most apparent difference between MES and ERP systems is how they are integrated. MES software is integrated directly with machines on the factory floor, while ERP software is combined with other business systems, such as CRM, accounting, and supply chain management.
- Cost: MES systems are typically less expensive than ERP systems, as they are designed to manage a specific aspect of the manufacturing process. On the other hand, ERP systems are more comprehensive and can be more expensive to implement.
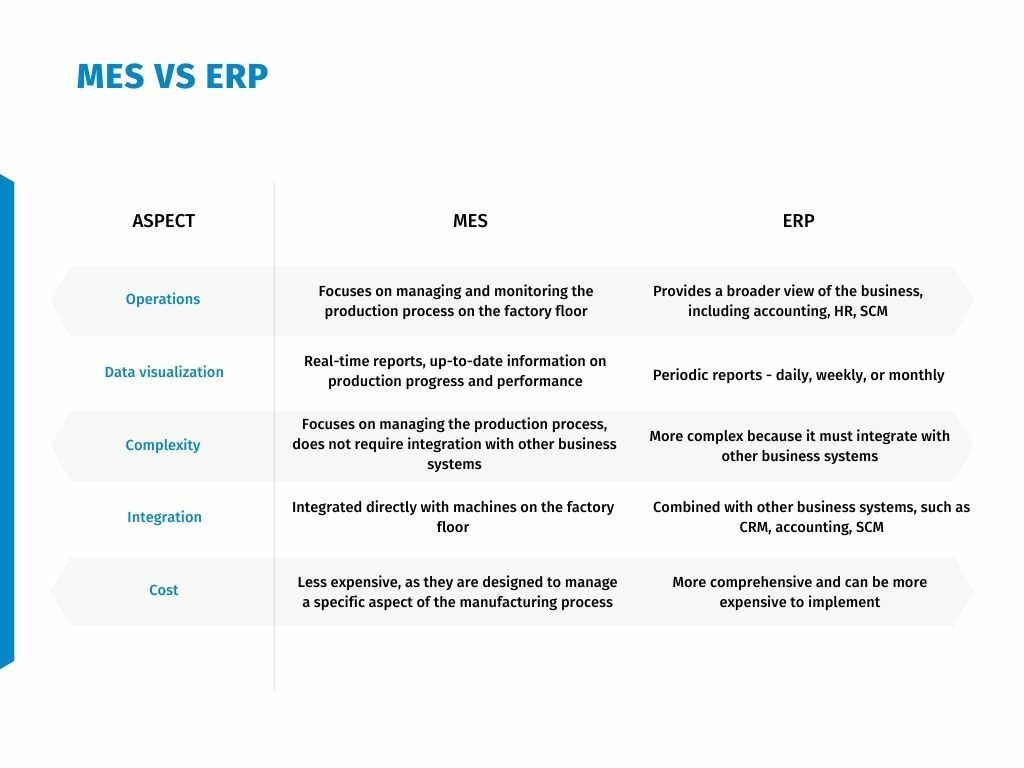
Did you know that more and more manufacturing companies are integrating Manufacturing Execution Systems (MES) with their Enterprise Resource Planning (ERP) software? While the two systems have traditionally been kept separate, there are many benefits to integrating them. So, let’s discuss how they can be combined!
Both systems have their strengths and weaknesses, but they can be integrated to provide a more comprehensive solution. MES deals with executing production orders, while ERP focuses on overall planning and resource management. By integrating these two systems, manufacturers can benefit from the best of both worlds.
MES ERP integration typically involves two different approaches: direct integration and data synchronization. Direct integration is the most comprehensive approach, as it allows the two systems to share data in real-time. It means that changes made in one system are immediately reflected in the other. On the other hand, data synchronization involves exporting data from one system and importing it into the other. This approach is less comprehensive, but it can be easier to implement.
As a result, MES integration with ERP can help manufacturers improve their bottom line.
Integrating MES and ERP can help streamline operations, improve quality and traceability, and improve data visibility across the enterprise. When done correctly, combining these two systems can result in several benefits for manufacturers.
- Improved quality and traceability: One of the key benefits of integrating MES and ERP is improved quality and traceability. By integrating data from both systems, manufacturers can get a complete view of the manufacturing process and identify potential issues early on. This can help reduce scrap and rework and improve overall quality.
- Improved resource utilization: Another benefit of MES ERP integration is improved resource utilization. By integrating data from both systems, the user can view the manufacturing process and identify areas where resources are being wasted. This information can then be used to alter the approach to optimize resources and improve efficiency.
- Improved data visibility: One of the main benefits of integrating MES and ERP is improved data visibility. By integrating the two systems, manufacturers can see all their data in one place. This makes it easier to identify trends and make decisions.
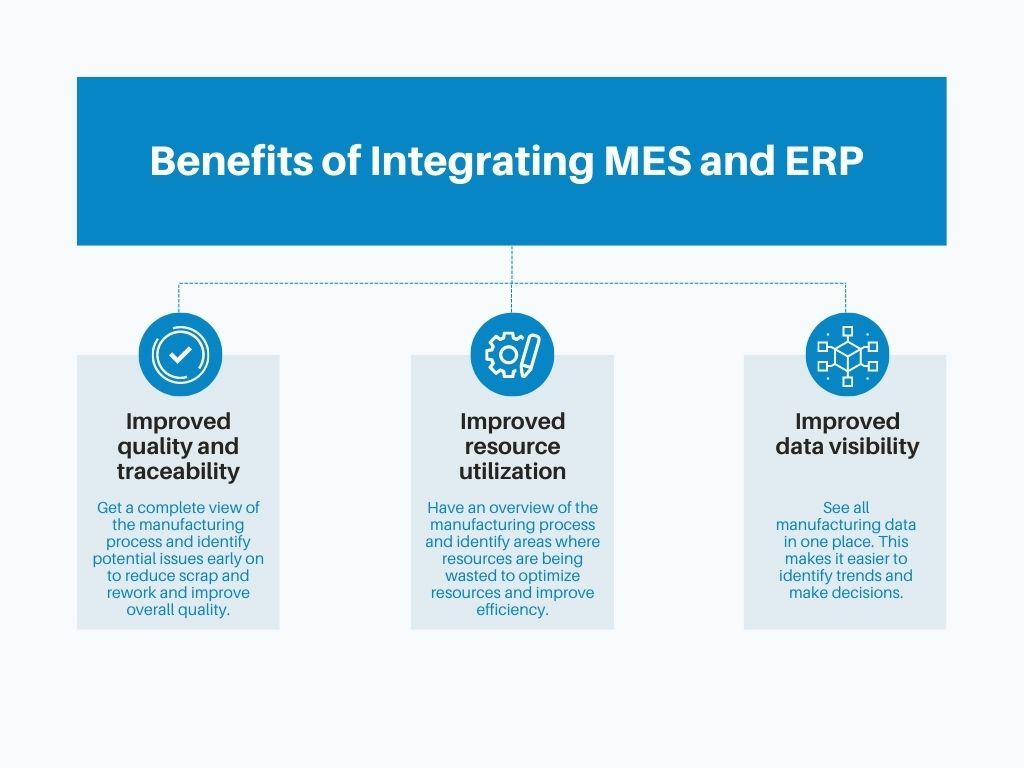
Conclusion
In conclusion, MES and ERP are two different types of software that can be integrated to provide a more comprehensive solution. Both systems have advantages, so choosing the right one for your needs is essential. If you have any queries related to MES and ERP, feel free to ask us, we will be more than happy to assist you.
You can find more information from our blogpost about the differences between MRP and ERP, and the benefits of MRP ERP systems software for manufacturers.