Spot welding is a process that is extensively used in manufacturing industries. It uses heat and pressure on metal surfaces via electrodes and is pivotal in crafting high-strength joints with speed and consistency.
As a foundation for producing automobiles, electronics, and a vast array of metal products, spot welding’s role in modern fabrication warrants a closer examination of its techniques, benefits, and equipment.
What is Spot Welding?
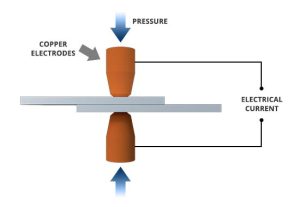
Spot welding is one of the most popular types of resistance welding techniques used to join two or more metal sheets together with pressure and an electric current through the metal. The process involves electrodes, typically made of copper, that deliver the electrical current to the joined metals, creating heat with the resistance to electricity in the metals.
This heat and the pressure the electrodes apply causes the metal to form a weld at the contact spot. The simplicity and speed of the process make the spot welding process a common choice for manufacturing industries, especially in applications where high-speed welding is advantageous and other welding techniques might be too cumbersome.
Specifically, automotive manufacturers favor spot welding sheet metal to form the car’s frame and other components. The method is efficient and cost-effective, requiring minimal preparation for automated mass production.
What are the Various Types of Spot Welding?
Spot welds are common in manufacturing industries, primarily to join metal sheets where other methods might be less effective.
There are several types of spot welding, each suited for different applications:
- Resistance Spot Welding (RSW) is the most common form of spot welding. In this method, electrodes apply pressure and heat to melt the metal at the spot. It’s mainly used in the automotive industry to weld sheet metal.
- Capacitor Discharge Spot Welding (CDSW) is a method where a stored electrical charge in capacitors is released to create a weld. This technique is ideal for materials with high electrical or thermal conductivity that require precise energy control to avoid warping.
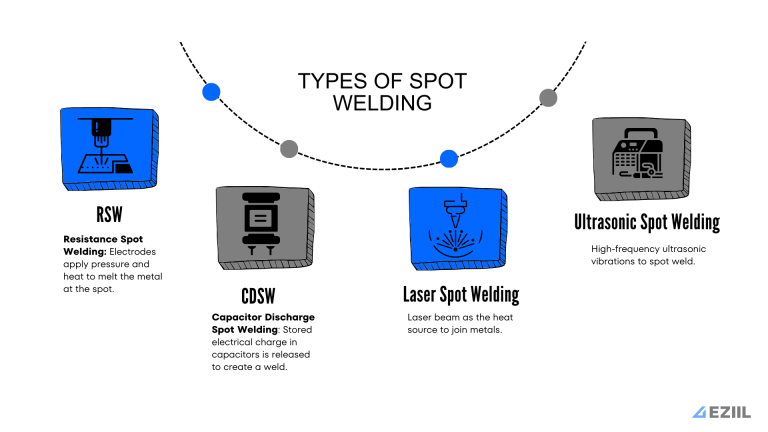
- Laser Spot Welding uses a laser beam as the heat source to join metals. It offers high accuracy and control, making it suitable for small, delicate components in the electronics and medical device industries.
- Ultrasonic Spot Welding uses high-frequency ultrasonic vibrations to spot weld plastics and lighter metals without introducing thermal distortion or degradation.
Manufacturers can choose the most appropriate method for their materials and product requirements, ensuring strong, consistent welds for various projects.
What are the Four Primary Types of Spot Welding Equipment?
Spot welding technology is diverse, presenting designs and setups tailored to meet varying operational demands and workplace scenarios.
Here, we identify the four main classes of spot welding equipment.
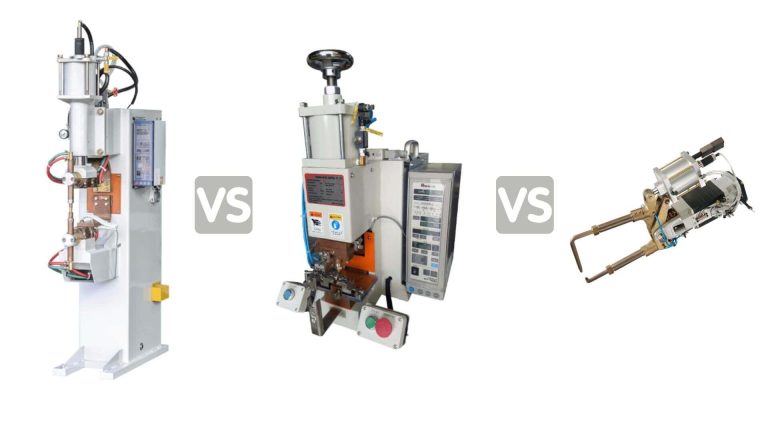
- Portable spot welders are compact and easy to move, making them the go-to solution for working in various locations. These machines are ideal for smaller projects or on-site repairs where mobility is crucial.
- Bench spot welders, on the other hand, are designed for stationary use on workbenches. They are more suitable for workshops and offer greater precision for small to medium-sized workpieces.
- Pedestal spot welders have a stand-alone design featuring a pedestal base that supports the welding apparatus. They are well-suited for larger production work and provide a stable, ergonomically optimized welding position.
- Robotic spot welders represent the peak of automation and efficiency in welding technology. These highly sophisticated machines are employed in industrial settings, delivering superior quality, consistency, and speed, particularly in mass production environments where they can operate around the clock with minimal supervision.
Book a 60-minute demo to see
how eziil mrp solution works for you
What are the Advantages of Spot Welding?
- Precision: Spot welding allows for the relatively precise application of welds to specific points on the workpiece.
- Efficiency: A fast welding process does not require filler materials.
- Economy: Spot welding is cost-effective due to minimal energy usage and the small amount of consumables it requires.
- Automation: The process can be easily automated, allowing for consistent and repetitive welds, which increases productivity.
- Versatility: Spot welding can join a variety of conductive metals.
- Minimal Distortion: The localized heat from spot welding reduces overall metal distortion, maintaining the integrity of the workpiece.
- Durability: Spot welding produces solid and durable welds.
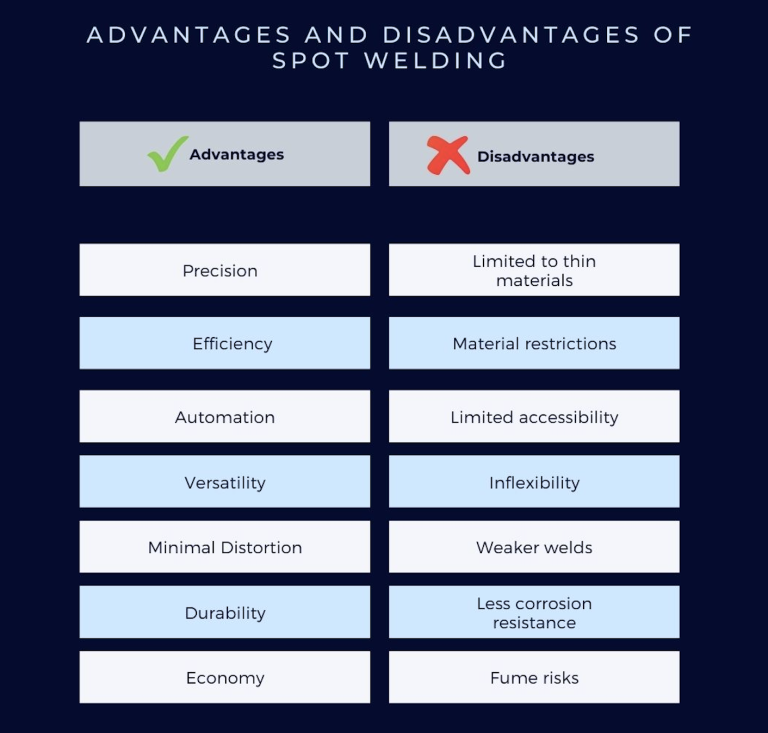
What are the Disadvantages of Spot Welding?
- Limited to thin materials: Spot welding is generally unsuitable for thicker materials, which can significantly limit specific manufacturing processes.
- Material restrictions: Only certain techniques, such as steel spot welding, conduct electricity well and are suitable for spot welding, limiting its application range. Spot welding aluminum is not recommended.
- Limited accessibility: The electrodes used in spot welding must be able to access the points to be welded, which can limit the technique’s use in complex structures.
- Inflexibility: Spot welding is less versatile than other welding techniques, which can perform a variety of welds; it is constrained to lap joints only.
- Weaker welds: The joint strength is often weaker than those created by other welding processes, potentially leading to durability issues in some applications.
- Less corrosion resistance: Spot welding can affect the chemical and physical properties of the metals, meaning reduced corrosion resistance.
- Fume risks: The fumes from spot welding can be harmful.
How Does Spot Welding Compare to Other Resistance Welding Techniques?
Spot welding stands out among resistance welding techniques due to its speed and efficiency in joining overlapping metal sheets.
Unlike other methods, such as seam or projection welding, spot welding applies concentrated heat and pressure to small points, resulting in discrete welds that are highly controllable.
This localized approach minimizes warping and allows for welding complex or delicate assemblies that might be susceptible to damage from more extensive heat.
Future Trends
The market for spot welding robots, a critical component in industrial manufacturing processes, attained a value of $6.8 billion in 2021 and is anticipated to surge to $15.7 billion by 2030, ascending at an annual growth rate of 9.5% between 2022 and 2030.
These advanced robotic systems are instrumental in product assembly lines, where precision and efficiency are paramount. Governed by programmable logic controllers (PLCs), spot welding robots accurately execute complex movements driven by pre-programmed routines. Robots excel by trimming cycle times during mass production phases, significantly boosting productivity for large-scale manufacturing.
The manufacturing sector’s drive toward automation and the scalability of operations is a substantial factor propelling the expansion of the spot welding robot market. Additionally, the shift towards these robotic solutions comes from their capacity to minimize errors inherent in spot welding tasks and the broader trend of integrating smart technologies in line with the principles of Industry 4.0.
Manufacturing professionals recognize that adopting these sophisticated robotic systems is an excellent solution to meet the rising demand for quality, speed, and adaptability in production environments!