Welding is a fundamental process in the metal industry that involves joining two or more pieces of metal together by applying heat, pressure, or both. It is a critical process that has found applications in various industries, including construction, automotive, aerospace, and shipbuilding, among others. The welding process ensures the integrity and durability of metal structures, making it an indispensable part of modern manufacturing processes.
As important as welding is, it also carries inherent risks that require close attention to quality and safety. The role of the welding supervisor or manager, therefore, is crucial in ensuring that the welding process is executed safely and efficiently. These professionals are responsible for overseeing welding projects, including the planning, execution, and monitoring of welding operations. They must ensure that the welding process meets quality standards and adheres to industry regulations. In this article, we will delve into the world of welding qualifications and certifications. We will explore the different types of welding qualifications available, their importance, and how they impact the welding process.
We will also discuss the benefits of investing in welding certification and the impact it can have on your business’s bottom line.
Let’s get started.
Welding Qualification and Safety
Welding qualification play a crucial role in ensuring the quality and safety of welding projects. These qualifications help to ensure that the welding process meets industry standards and regulations and that it is executed safely and efficiently.
Types of qualifications:
There are various types of welding qualification of which the most renowned are:
● Certified Welding Inspector (CWI): is a certification provided by the American Welding Society (AWS). The CWI certification is recognized by many industries and organizations, including the American Society of Mechanical Engineers (ASME), the U.S. Department of Defense (DoD), and the Federal Aviation Administration (FAA).
● Certified Welding Supervisor (CWS): is another certification provided by the AWS. The certification is tied to the AWS D1.1 Structural Welding Code and is recognized by many industries and organizations.
● Welder Performance Qualification (WPQ): this certification ensures that welders have the necessary skills and knowledge to perform welding operations in compliance with codes, standards, and regulations. The WPQ is tied to various codes and standards, including the AWS D1.1 Structural Welding Code, the ASME Boiler and Pressure Vessel Code, and the American Petroleum Institute (API) 1104 Welding Standard.
Obtaining welding qualification typically involves undergoing rigorous testing, which may include welding tests, written exams, and documentation of work experience.
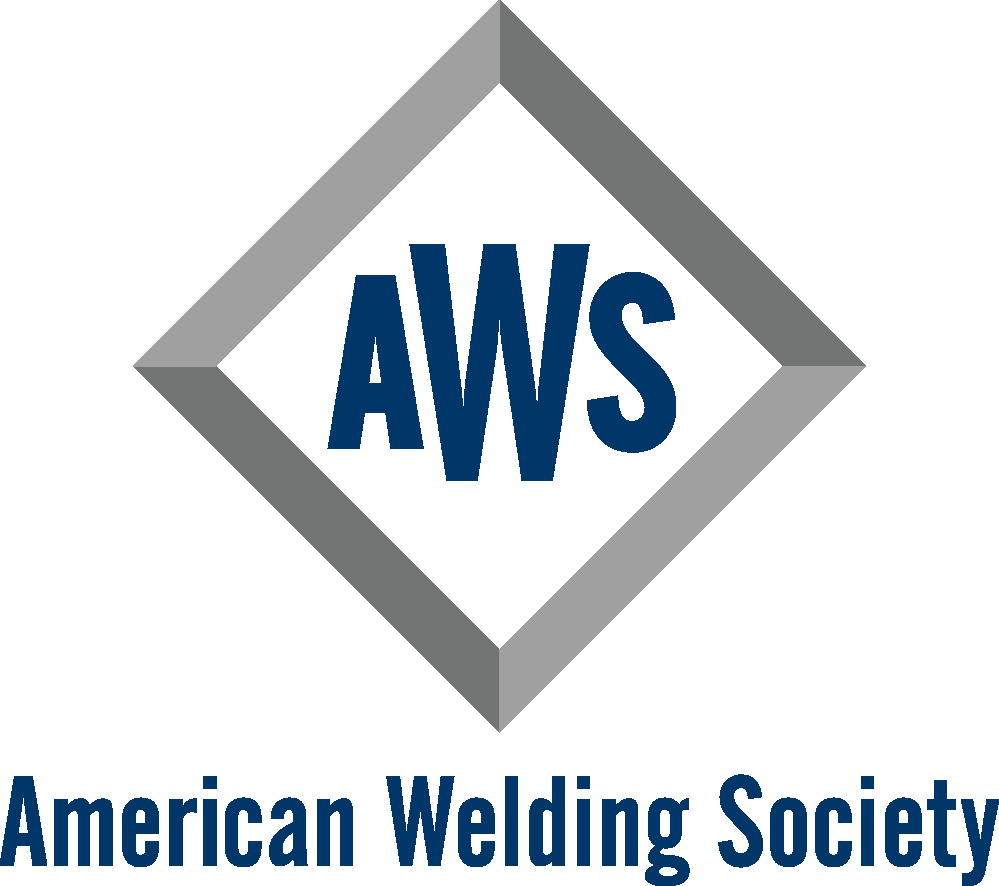
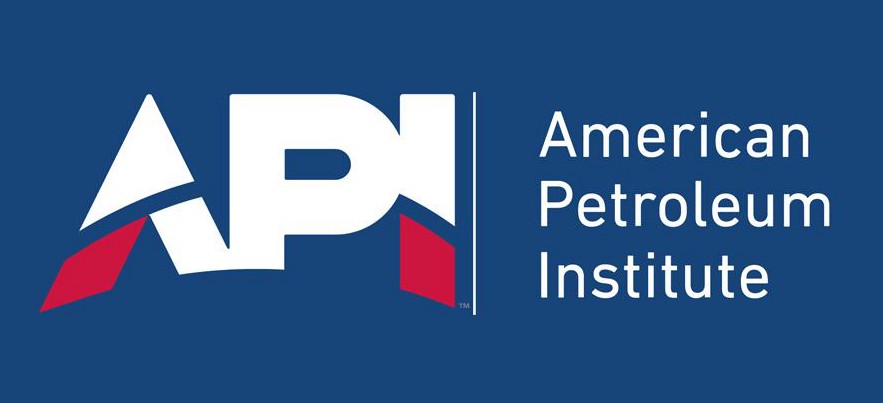
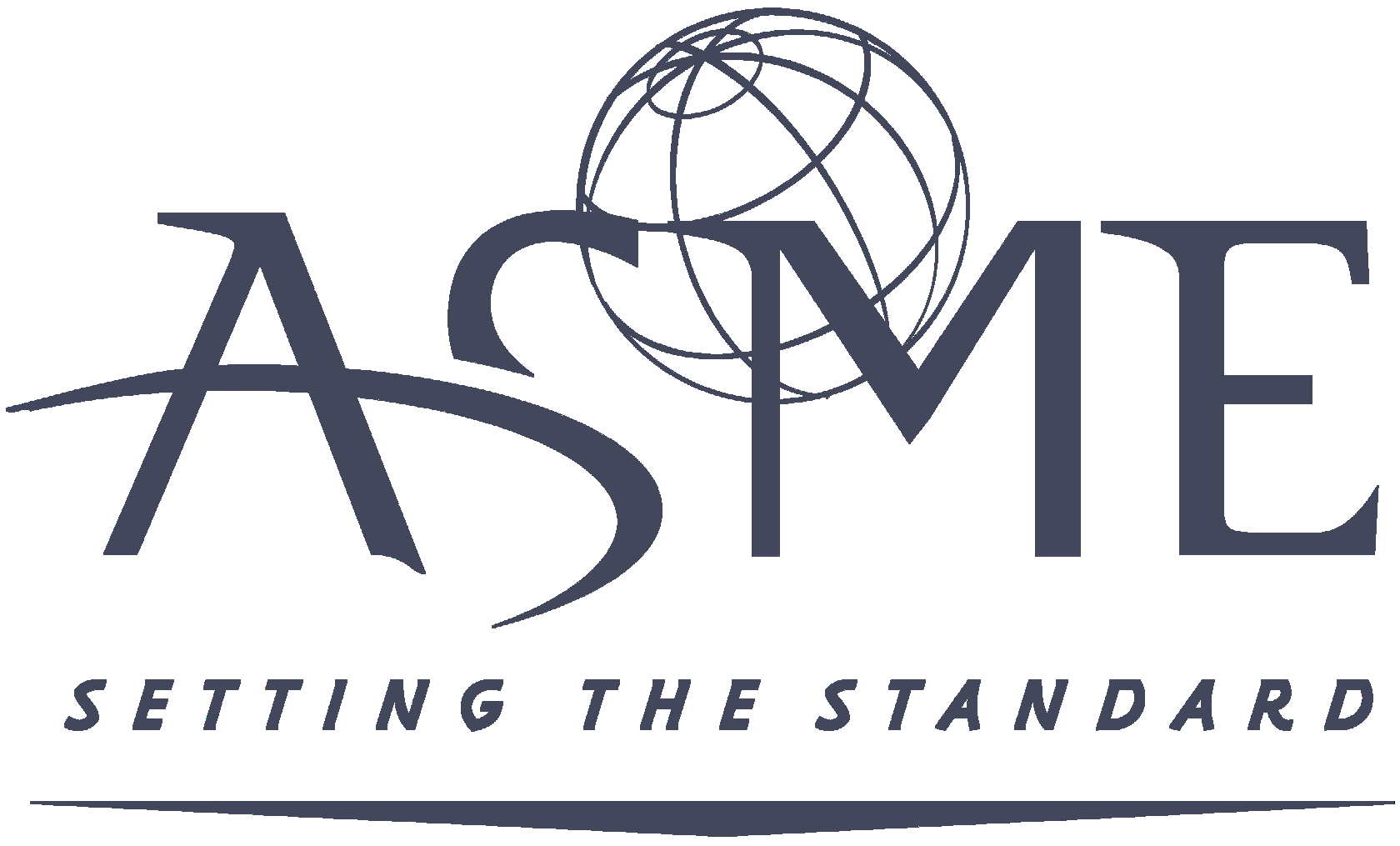
The importance of welding qualifications:
Companies have a responsibility to ensure that their welders and welding procedures comply with industry standards and regulations. Failure to do so can result in costly rework, safety hazards, and even legal repercussions.
Investing in welding qualifications can help companies maintain high-quality welding projects and reduce the risk of accidents and errors. By prioritizing compliance with welding qualifications and requirements, companies can ensure that their welding projects meet industry standards and regulations, which can lead to improved customer satisfaction and a better reputation in the industry.
The importance of welding qualifications cannot be overstated. Companies bear the responsibility of ensuring that their welders and welding procedures adhere to industry standards and regulations. Failure to comply can lead to costly rework, safety hazards, and potential legal repercussions. By investing in welding certification, companies can uphold the highest standards of quality in their welding projects while minimizing the risk of accidents and errors. Prioritizing compliance with welding certification requirements demonstrates a commitment to excellence and safety, which can enhance customer satisfaction and bolster the company’s reputation in the industry
Training and Development for Welders
As responsible for welding, you understand the importance of training and development for welders. Proper training and development are crucial to ensuring that your welders have the necessary skills and knowledge to complete welding projects successfully.
There are several types of training, including vocational schools, apprenticeships, and on-the-job training.
Vocational schools provide formal training in welding techniques and safety practices, while apprenticeships provide hands-on experience under the guidance of experienced welders. On-the-job training allows welders to learn while working on actual welding projects.
By providing your welders with access to these training programs, you can ensure that they have the necessary skills and knowledge to complete welding projects to your high standards. Investing in employee training and development can also benefit your company by increasing employee satisfaction and retention. It is also intimately linked to the safety of your employees, and should be a priority for you in the company.
Hiring and Qualifying Welders
Welding requires a high level of skill and knowledge, and hiring the wrong person can lead to quality issues, safety risks, and potentially costly mistakes. That’s why it’s essential to have a thorough process in place for evaluating and hiring welders.
The qualifications required for welding jobs may vary depending on the project, but there are some basic requirements that should be considered. Education is an important factor, as welders may need to have completed vocational or technical training programs to gain the necessary skills and knowledge. Certifications, such as those offered by the American Welding Society (AWS), are also commonly required to demonstrate proficiency in specific welding techniques. Experience is another key factor, as welders with a proven track record of success on similar projects are often preferred.

What to evaluate when hiring?
When evaluating a welder’s qualifications, it’s important to look at their education, certifications, and experience in detail. This may involve reviewing resumes and portfolios, conducting interviews and weld tests, and contacting references to verify past performance.
It’s also essential to assess whether the welder has the physical ability to perform the job safely and effectively, including factors such as visual acuity, manual dexterity, and hand-eye coordination. As the responsible party in your company, it’s your responsibility to ensure that only qualified welders are hired and assigned to projects. Failure to do so can result in quality issues, safety risks, and even legal liability in the event of accidents or injuries.
Continuous training
In addition to ensuring that welders are qualified for the job, it’s also important to provide ongoing training and development to help them improve their skills and stay up-to-date with new techniques and technologies. This can help your company remain competitive in the marketplace and attract and retain top talent. By investing in the development of your welders, you can help ensure that your company is well-positioned for success both now and in the future.
Explore more about “Women in Welding: Is It a Good Career Choice?”
Book a 60-minute demo to see
how eziil mrp solution works for you
Quality and Safety
The risks involved if quality and safety are not properly managed can be disastrous, leading to accidents, delays, and even legal issues.
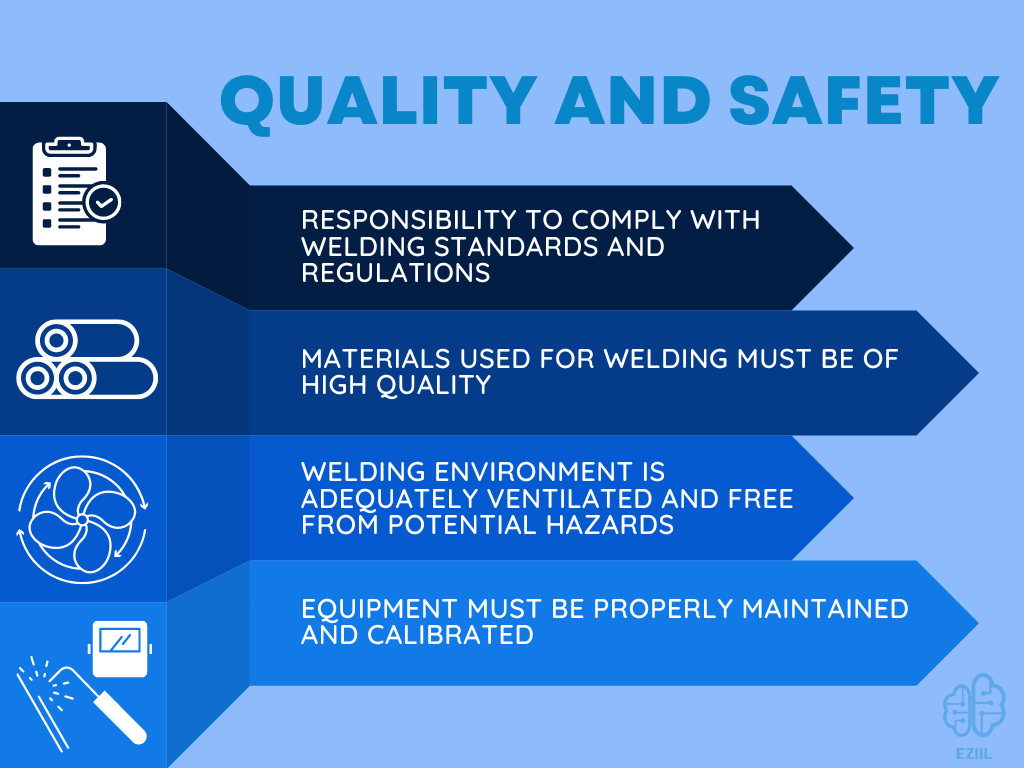
As mentioned above, the company has a responsibility to comply with welding standards and regulations set by organizations such as ASME and AWS.
It is important to ensure that all welding projects comply with these standards to maintain the company’s reputation and avoid potential legal issues.
Several factors can affect quality and safety in welding projects, such as the welding environment, materials used, and the equipment used for welding. Managing these factors effectively is essential for successful project outcomes. For example, maintaining proper ventilation in the welding environment and keeping it free from flammable materials are key measures to ensure safety. Additionally, using high-quality materials appropriate for the project and ensuring that equipment is well-maintained and calibrated can significantly enhance performance.
Becoming a welder requires dedication, training, and ongoing education. This role is pivotal in product design and mechanical engineering, with a strong demand for skilled welders across various industries. Attending a welding school is an excellent strategy to acquire the necessary knowledge and hands-on experience. Most welding schools require a high school diploma or equivalent and offer courses in techniques such as MIG welding, arc welding, gas metal arc welding, and shielded metal arc welding. A solid foundation in math and science is beneficial for mastering these techniques and understanding the equipment involved.
Obtaining a welding certification is a critical step in becoming a professional welder. This certification usually involves passing both a written test and a practical welding test to demonstrate proficiency in various welding techniques and positions. A welder with a welding certification from a recognized organization, such as the American Welding Society (AWS), has proven skills in various techniques and is qualified to work in diverse industries. Advanced professional certifications, like Certified Welding Inspector (CWI) and Certified Welding Engineer (CWE), are vital for career advancement and showcasing expertise in different welding methods and equipment.
Conclusion
In conclusion, the success of welding projects is heavily reliant on the qualifications, training, and safety measures put in place by the company. As a responsible person overseeing welding projects, it is crucial to prioritize these factors to ensure the successful completion of projects and the safety of all involved.
We discussed the importance of proper training and development for welders, including the different types of training available and the responsibility of the company to facilitate and support ongoing training.
Additionally, we highlighted the significance of hiring qualified welders with appropriate qualifications and experience for specific projects, as well as the company’s responsibility to evaluate and ensure compliance with welding standards and regulations.
Ensuring quality and safety in welding projects requires managing different factors such as the welding environment, materials, and equipment, and the implications of not doing so can be significant. By prioritizing welding qualifications, training, and safety in company operations, we can create a culture of safety and success for all welding projects.
We urge companies to prioritize welding qualification, training, and safety in their operations to ensure successful and safe welding projects. By doing so, companies can create a work environment that promotes safety, success, and profitability for all involved.