Metal fabrication is an essential part of many different sectors such as construction, manufacturing, and transportation. It’s an industry that has, in the past, been notorious for the impact it has had on the environment, and current statistics for 2023 show that for every ton of steel produced in the world, 1.83 tons of CO2 is emitted, which means over the course of a year, the metal industry in part, contributes 3.3 million tons to global emissions.
Over 240 kilos of steel is created for every single person in the world every year, and we can’t really function without it as it is a part of so many items in our daily life and in the industrial world.
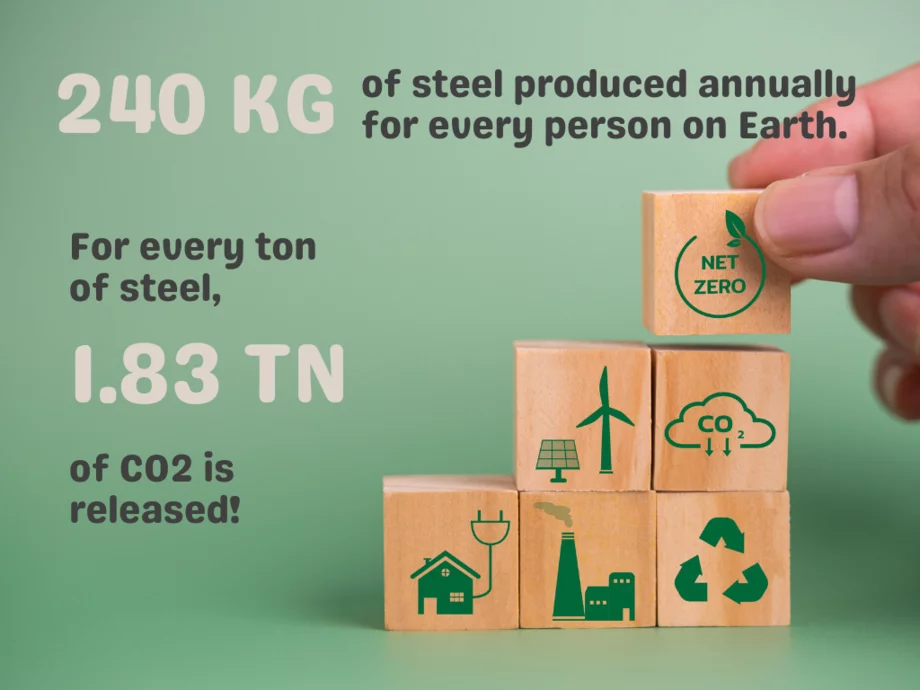
Companies involved in metal fabrication are becoming more aware of their carbon footprint, and their use of other natural resources such as water. They are now seeking ways to help minimize their impact on the wider world and human life, and also to think about making their practices more sustainable.
It’s important to understand how metal fabrication can play an integral role in reducing its environmental impact. There are considerations as to how the workers operating within the industry carry out their work safely and carefully whilst still maintaining sustainable protocols (usually in the form of proper certification and qualifications). Also, there are environmental concerns about the by-products metal fabrication works create.
Here we’ll consider all of these and discuss how the metal fabrication industry is bringing sustainability to the fore.
The Key Health and Environmental Concerns Arising From the Metal Fabrication Industry
There are risks posed by the chemical and industrial processes that the metal fabrication industry uses. These are outlined as follows:
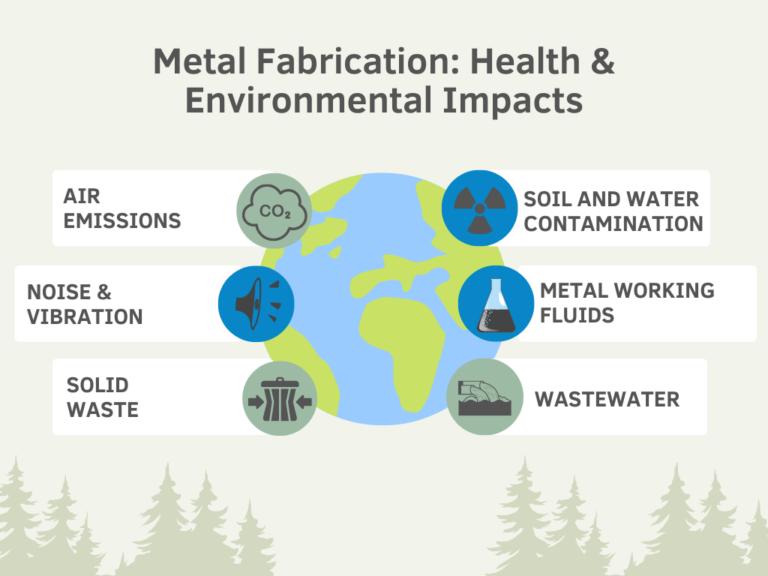
Air emissions: Air emissions in the metal fabrication industry mainly come from VOCs that are released during degreasing and cleaning operations. These can also occur through the volatilization of solvents when they’re placed in storage.
There can be issues from dust and particulates that are emitted during grinding operations. Welding also generates gases like carbon monoxide, and toxic metal fumes, too.
Noise & Vibration: On-site equipment and the processes they are designed to help with can produce levels of noise that can be harmful to people and the environment.
Actions such as grinding, hammering steel, guillotining, cutting metal, pressing, and disposal of scrap metal can produce harmful levels of noise.
In addition to this, there are risks to humans from the vibrations caused by these processes, such as hand and arm vibration syndrome.
Metal Working Fluids: Metalworking fluids can become spoiled or contaminated with extended use and reuse, no matter how careful operatives are in any given situation. These used fluids contain high levels of metals and they can sometimes also contain contaminants from other processes, e.g. acids, alkalis, waste oils, and solvents.
Soil and Water Contamination: Contamination is often caused by the discharge of untreated wastewater to sewers and the incorrect disposal of metal sludge on working sites. This is something that could have occurred in the past and could also still be happening in the present.
Contamination can occur if there are accidental spillages and leaks of solvents and oils.
Solid Waste: Solid waste is usually related to metal offcuts and chips that have been contaminated with cutting fluids or cleaning agents.
These wastes are hazardous and a danger to human life and as a result must only be disposed of by registered handlers.
Wastewater: Wastewater that contains acidic or alkaline wastes, waste oils, and solid wastes, such as metals and solvents, are often created by the metal fabrication industry and must be treated safely and handled professionally prior to their discharge.
The Environmental Processes that Offer More Sustainability to the Metal Fabrication Industry
Environmentally friendly materials are becoming more important in metal fabrication. These types of materials need to be as strong as virgin materials but must have a lower environmental impact.
Here are just a few examples of environmentally friendly materials that are currently being used and/or trialed in metal fabrication:
Recycled Aluminum: Aluminum is a metal that can be recycled forever. Recycled aluminum used in metal fabrication will help reduce the amount of energy that’s required to produce brand-new aluminum and it’ll also minimize the environmental impact of mining bauxite, which is the primary raw material used in the production of aluminum.
This is because the aluminium recycling process requires only 5 percent of the energy needed to produce the primary metal, resulting in greenhouse gas emissions of 0.5 tonne CO2 eq/tonne recycled aluminium (gate to gate).
It does not include the inherent carbon footprint of the aluminium scrap, because of this it’s believed that aluminum will achieve full circularity by the year 2030, which would be a superb achievement.
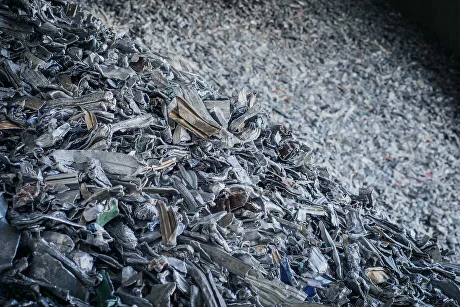
Recycled Aluminium
Recycled Copper: Copper isn’t permanently recyclable but it can be reused multiple times.
Using recycled copper within the metal industry will help reduce the amount of energy that’s required to produce new copper.
It’ll also help minimize any environmental impact caused by mining and refining copper ore.
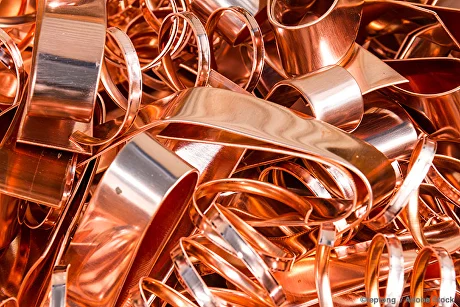
Recycled Copper
Recycled Steel: Steel can be recycled indefinitely. Using recycled steel will help to conserve natural resources. The IEA currently states that direct CO2 emissions due to crude steel production stood at approximately 1.4 tons CO2 per ton of steel that is produced (at the time of writing).
However, it’s believed that the numbers could be slightly higher at roughly 1.85 metric tons of CO2 per ton of steel. This figure is backed up by the World Steel Association.
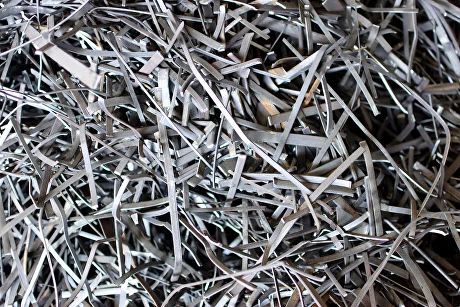
Recycled Steel
There are likely to be issues surrounding amounts of CO2 levels and how the steel has been produced in the first place. These numbers are a weighted average taken from a couple of different production methods. The primary route of steel production is the Blast Furnace-Basic Oxygen Furnace (BF-BOF) method, most commonly undertaken across the world.This uses 13.8% scrap, with emissions of 1.987 tonnes of CO2/tonne of steel.
This is what gives us the average amount of 1.85 metric tonnes of CO2 emissions per metric tonne of steel.
There are also materials that aren’t directly made from metal but are required in the metal fabrication process. These are things like bio-based plastics which are made from plant-based materials like corn, sugar cane, or potatoes rather than coming from petroleum-based sources. They can be in metal fabrication to replace traditional plastics, which are often non-renewable and can have a severe impact on the environment.
Some companies are now investing in renewable energy sources to help provide energy for their operations.
Materials like bamboo are useful too. This is a renewable resource that can be used as an alternative to wood when working in the metal fabrication industry. It’s very light yet strong and it’s possible to make products like handrails, ladders, and scaffolding from it.
Finally, there are composites, which are materials made from two or more different things, such as carbon fiber or fiberglass. Like bamboo, they’re durable yet light and can be used most successfully in the automotive industry. Composite use can help to reduce the weight of products and this in turn will minimize fuel consumption and emissions.
Having looked at the changes that can be made in terms of material usage, the metal fabrication industry is also looking at ways in which they can save energy and reduce waste. Some companies are now investing in renewable energy sources to help provide energy for their operations. Others are actively seeking out recycling programs that help reduce waste and protect precious resources. Companies are also looking to try and work in more sustainable ways with materials like aluminum, which can have a lower environmental impact than other metals:
- Implementing Energy-Saving Practices: The industry requires a lot of energy use, but companies are actively reducing their energy consumption by installing energy-efficient lighting and equipment or adopting renewable energy sources like solar or wind power.
- Reducing Waste and Emissions: There is a lot of waste generated by the industry. Companies are working to minimize these environmental impacts by implementing recycling programs for scrap metal and other waste materials. They are also adopting water-saving technologies in production processes, and choosing equipment that reduces emissions.
Book a 60-minute demo to see
how eziil mrp solution works for you
Certification, Initiatives, and Technologies to make the Metal Fabrication Industry Greener
The watchword for so many industries is ‘sustainability’ and the metal industry is keen to do what it can to come up with initiatives and practices that help reduce its impact locally and globally.
Changes need to come from within the industry itself, but that doesn’t mean that help and advice from other sectors aren’t needed.
For the metal fabrication world, finding and utilizing new ways to be greener and cleaner, is both profitable and convenient.
One small part of this is for businesses operating within the industry to achieve their ISO 14001 qualification certificate.
This is an important certification to have, especially in a sector where there are concerns about sustainability and environmental damage.
The ISO 14001 Certification will improve company cost control, and the other main advantage is that it shows you are a socially responsible business and compliant with any legal requirements.
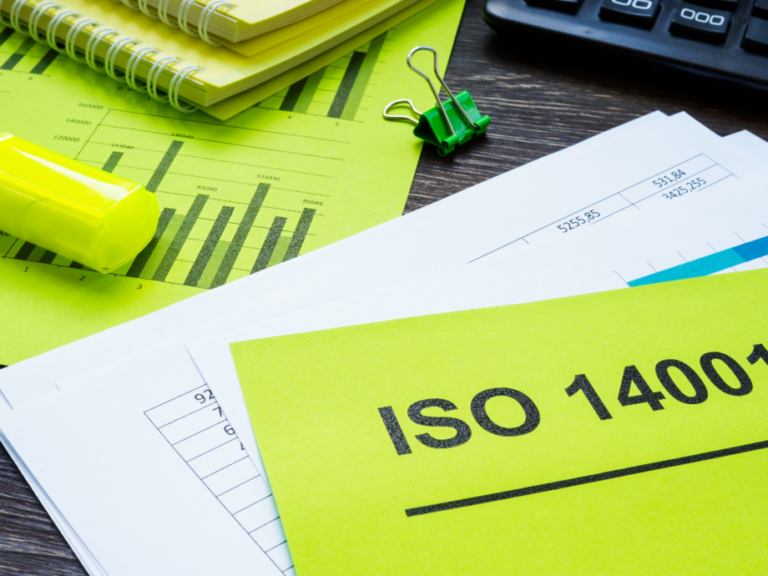
Governments all over the world want more manufacturers from all industries to adopt sustainable production methods that will help make us all more environmentally friendly and eco-aware. The Bureau of Labor Statistics calls it the ‘output approach’. This “identifies establishments that produce green goods and services, and counts associated jobs“. In addition to this, a key sustainability toolkit produced by the OECD provides what they term ‘seven steps to environmental excellence’ which can be applied in the metal fabrication industry to help streamline processes.
A group called the Green Suppliers Network has been established by the USA’s Environmental Protection Agency and Department of Commerce and its main aim is to help small or medium-sized businesses within the manufacturing industry stay competitive but also reduce how much impact they have on the environment.
Reducing the amount of industrial energy generated is an important consideration too and programs such as the Save Energy Now scheme are said to be helping reduce industrial energy intensity by 25% over 10 years. There is also the Better Plants Initiative and Superior Performance Certification. These departments cover all bases in terms of sustainability innovations.
Green Job Creation and Lean Manufacturing
A sustained approach to the greening of the metal fabrication industry will bring about economic growth but it will also be more likely to attract younger people to commit themselves to entering the industry to train and work full time.
The creation of ‘green jobs’ is something that welders and other workers in the industry are keen on.
There are lots of different ways to do this, such as by finding ways of creating products that have a much lower environmental impact or trying out manufacturing practices with lower environmental effects.
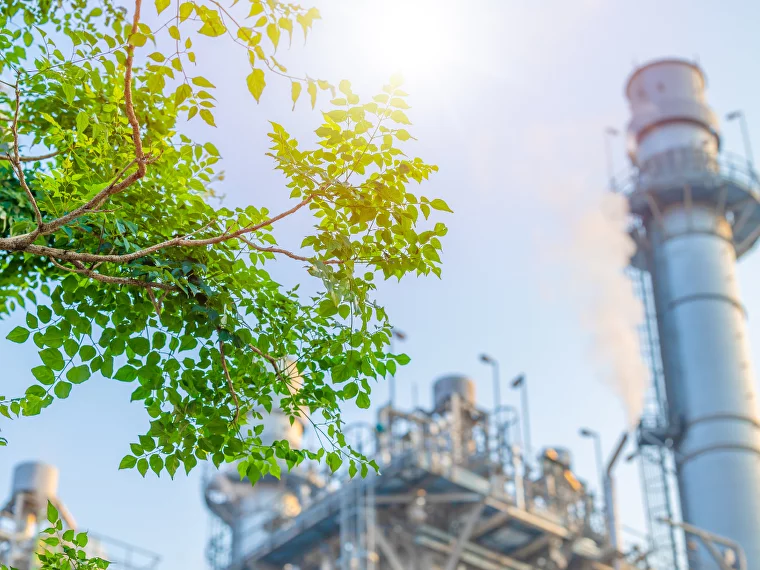
The single most popular approach to creating green jobs in the industry is by reducing the amount of pollution produced during manufacturing, and metal fabricators have been experimenting with this by trying the procedures we’ve mentioned above.
They can dramatically reduce a company’s carbon footprint, which then allows it to pursue high-value markets for sustainable goods.
How would this work? Well, let’s look at one option of how a welding business could adopt the idea of using environmentally-friendly techniques. They could include vacuum soldering or diffusive welds in their processes.
These innovative technologies may become more commonplace over the next few years, as environmental regulations become tighter and the need to reduce hazardous wastes increases.
Lean Manufacturing and Encouraging Younger People into the Industry
Lean manufacturing is a way forward for metal fabrication workers. This is a production method that puts emphasis on minimizing waste and maximizing efficiency. By using these principles, the industry can actively reduce the amount of energy and materials they use and at the same time improve the quality of their products. If this can be achieved then costs can be reduced, productivity will rise and the impact on the environment should be cut.
The change to more sustainable practices can also help attract younger people to the industry, too, which is essential if it is to carry on in an environmentally friendly way. Younger workers are key to ensuring that a centuries-old industry can survive and thrive in a world that truly needs to be more considerate to its people, its climate, and its surroundings.
There’s still a lot to do to make this industry a more environmentally competitive force to be reckoned with, but small changes really can help, and putting these protocols in place means that they’re on the right footing to forge forward with bigger and better changes in the years to come. Whether it’s by creating products that have a low environmental impact or utilizing manufacturing practices that have lower impacts and emissions – the industry is doing what it can to reduce the amount of pollution produced during manufacturing processes.