If you are considering working with a manufacturing process, you owe it to yourself to understand its fundamentals. Of course, you can’t expect to become an expert by learning the basics, but it provides an excellent starting point.
Sheet metal fabrication refers to several processes working collectively to produce a product or part.
The manufacturing steps are often technical and must include the correct procedures to achieve the final product. Let’s begin by looking at what sheet metal fabrication entails before moving on to the individual steps that result in metal parts and products.
What is Sheet Metal Fabrication?
Sheet metal fabrication refers to transforming flat metal sheets into shapes and structures. Rather than looking at it as a single process, the sheet metal processing methods involve using a collection of forming techniques, working in tandem, and producing the required part. Metal fabrication is used extensively in the automotive, aerospace, and construction industries.
Sheet metal manufacturing works with a range of metals.
Some of these include:
- Stainless steel: Used for its strength and resistance to corrosion
- Cold-rolled and hot-rolled steel: Both of these are easily formed, but cold-rolled has a smoother finish and tighter size tolerances
- Aluminum: A lightweight metal with exceptional strength-to-weight ratio
- Copper and brass: These metals are easy to work with and look good in a fabrication
Your choice of metal will be determined by the end product and what you expect from it.
What are the Steps in the Sheet Metal Fabrication Process?
After the engineering department has created drawings for turning flat sheets of metal into functional, three-dimensional products, the workers in the fabrication shop can take the first steps toward completing the project.
Here is how it typically transpires:
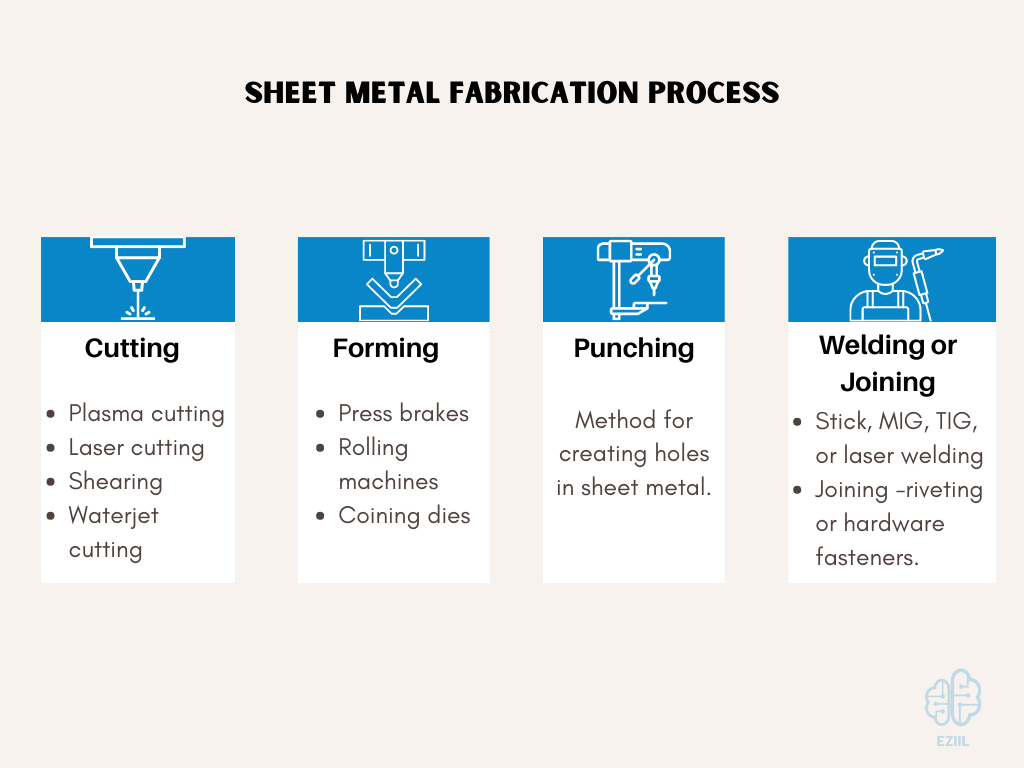
1. Cutting
The cutting process can be challenging, depending on the material and the cutting method. For instance, stainless steel is difficult to cut with a saw blade but cuts easily with laser or waterjet cutting. The main cutting processes include:
- Plasma cutting
- Laser cutting
- Shearing
- Waterjet cutting
2. Forming
Forming, or bending, is a critical step in sheet metal fabrication and is completed with the help of machines like press brakes, rolling machines, coining dies, and other equipment. Hot and cold rolling create curved or cylindrical shapes from sheet metal.
The most challenging aspect of forming is knowing how to bend the material to achieve the desired angle or shape. Since sheet metal tends to spring back to its original shape, trained operators must know how to “overbend” the metal to allow it to spring back to the correct angle.
Spinning is an obscure sheet metal forming process that employs a lathe to rotate sheet metal as it is pressed against a tool. The deformation process, as it is officially called, looks similar to manual lathe turning, and it is used for creating rounded sheet metal parts such as cones and cylinders.
Stamping combines cutting and forming, using complex dies to produce intricate-shaped parts with fewer operations.
3. Punching
Punching is a method for creating holes in sheet metal. The technique relies on a hardened steel punch and dies that force the holes into the metal and collect the scrap metal from the hole.
4. Welding or Joining
Welding and joining bring all the metal components together to assemble them into the finished product. The welding could be any type, including stick, MIG, TIG, or laser. Non-welding joining is typically accomplished by either riveting or hardware fasteners.
Sheet metal fabrication is a versatile manufacturing process that can be used to create a wide range of products, from simple brackets to complex machinery. CNC machining, laser cutting, plasma cutting, waterjet cutting, and sheet metal bending are just a few of the techniques that can be used in sheet metal fabrication.
One common material used in sheet metal fabrication is mild steel, which has a relatively low melting point and can be easily formed and welded. Other materials, such as cold-rolled steel and sheet metals of various thicknesses, can also be used depending on the specific application.
Engineering drawings are a critical component of sheet metal fabrication, as they provide a detailed blueprint for the manufacturing process. This includes specifying the dimensions, tolerances, and materials required for each component of the final product.
Plasma cutting and laser cutting are two commonly used techniques in sheet metal fabrication. Plasma cutting uses a plasma cutter to cut through metal, while laser cutting uses a high-powered laser to cut through sheet metal. Both methods produce precise cuts that can be used to create complex shapes and designs.
Sheet metal bending is another important process in sheet metal fabrication, which allows flat pieces of sheet metal to be formed into three-dimensional shapes. Roll forming is another method that can be used to create complex shapes by continuously bending and forming sheet metal.
Injection molding is another manufacturing process that can be used in sheet metal fabrication to create plastic parts that can be integrated with sheet metal components. This process involves melting plastic pellets and injecting them into a mold, which is then cooled and removed from the mold to create the final part.
Book a 60-minute demo to see
how eziil mrp solution works for you
Suitable Materials for Sheet Metal Fabrication
In order to achieve the best results, it is important to use suitable material for your sheet metal fabrication project. This section will discuss some of the most suitable materials for sheet metal fabrication. Remember that there are many different types of sheet metal, so be sure to consult with a professional before making any final decisions. Some of the most recommended materials are as below.
Aluminum
Aluminum is one of the most popular materials used in sheet metal fabrication. It is lightweight, strong, and corrosion-resistant. It is also easy to work with and can be used to create a wide range of products.
Stainless Steel
Stainless steel is another popular choice for sheet metal fabrication. It is also strong and durable, making it ideal for various applications. Stainless steel is also resistant to corrosion and is easy to work with.
Carbon Steel
Carbon steel is a type of steel that contains carbon. It is one of the most common materials used by sheet metal fabricators. Its physical and structural properties, such as strength, flexibility, and hardness, make it ideal for several heavy-duty projects.
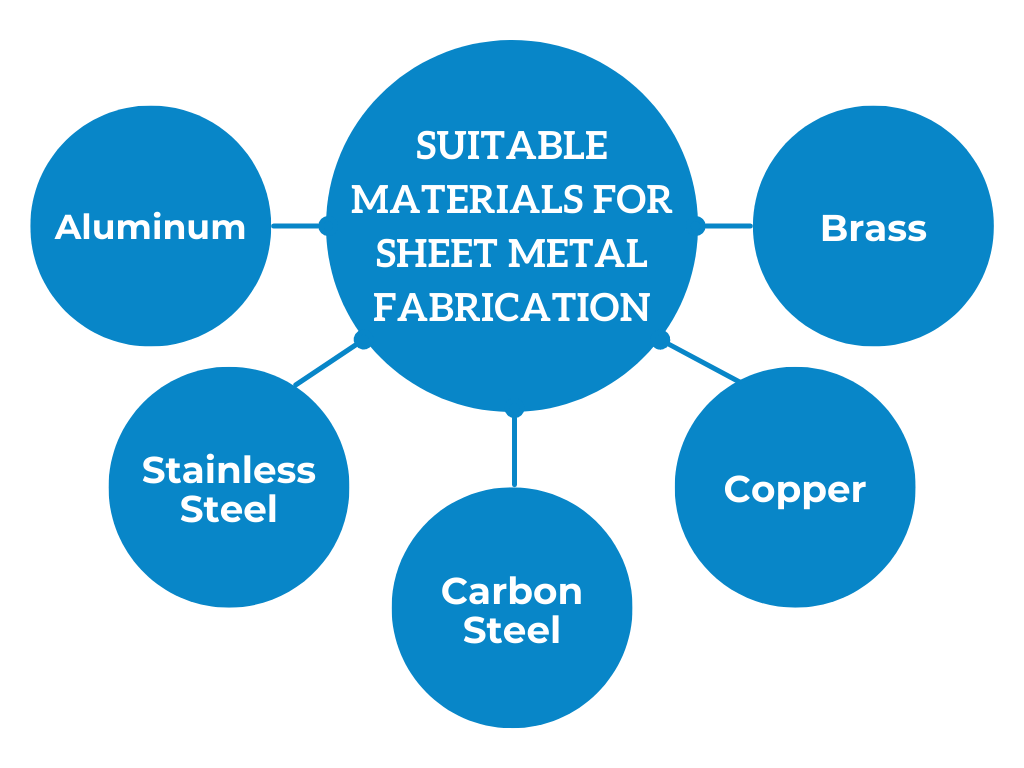
Copper
Copper is a soft metal that is easy to work with. It has excellent resistance to corrosion and heat. Its fabricated parts are often used in electrical applications due to their conductivity.
Brass
Brass is an alloy of copper and zinc. Its strength, flexibility, and durability make it a perfect choice for metal fabrication projects. It is widely used to develop fabricated parts for a variety of industries.
Consult with a professional to ensure that you use suitable materials and methods for your specific application.
Sheet Metal Fabrication Surface Finishes
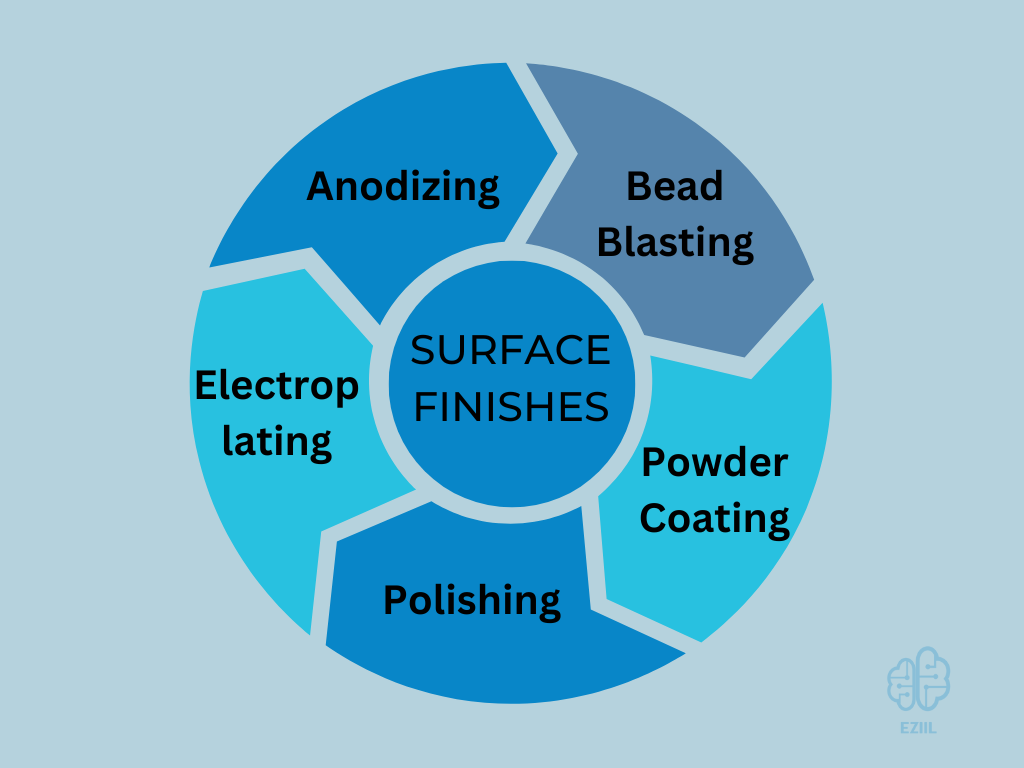
- Anodizing thickens the natural oxide layer on the metal, helping to give the component excellent corrosion and wear resistance properties. It improves the hardness and durability of the surface with a smooth, matte finish.
- Bead Blasting (a.k.a. sandblasting) involves shooting a high-speed jet of sand or other abrasives against the sheet metal, giving it a matte texture and preparing it for coating.
- Powder Coating involves directly spraying powdered paint onto the metal part, followed by curing the part in an oven or with ultraviolet light to form a wear-resistant layer of gloss or semi-gloss texture.
- Polishing is when a cloth wheel “buffs” or rubs the metal surface, giving it a shiny look.
- Electroplating is often used for decorative purposes but also corrosion resistance. Chrome-plating is one of its popular forms, used extensively in the automobile industry.
Design Considerations for Sheet Metal Fabrication
Without getting overly technical or offering too many details, here are a few general considerations when designing sheet metal parts:
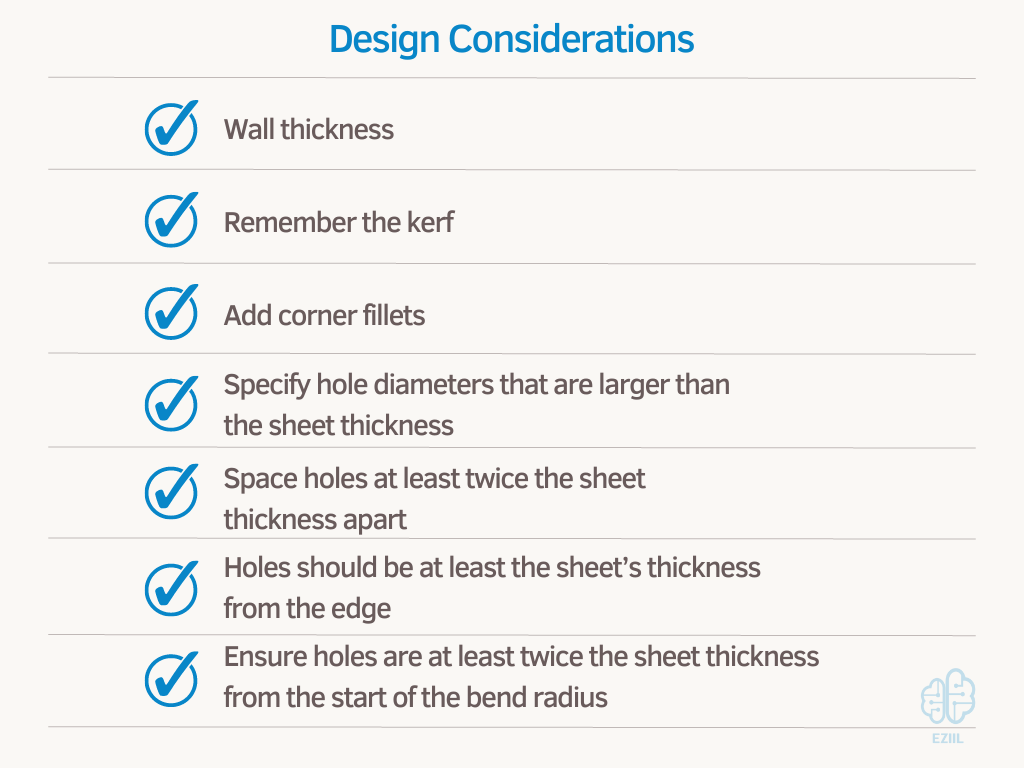
- Wall thickness: Since sheet metal parts are made from one sheet of metal, it’s essential to maintain a uniform wall thickness throughout the part.
- Remember the kerf: Laser, plasma, and waterjet cutting remove a small amount of material cutting process. This material loss is called a cutting kerf, and designers need to plan for this, especially if parts must fit into one another at assembly.
- Add corner fillets: The outside corners of sheet metal parts are sharp, so adding corner fillets helps to avoid cuts from handling the part.
- Specify hole diameters that are larger than the sheet thickness: Holes with a smaller diameter than the part’s thickness can result in deformation or be inaccurate because of distortion caused by a laser beam. Stick to a hole diameter the same or greater than the sheet thickness.
- Space holes at least twice the sheet thickness apart: Holes that are too close to each other might lead to deformation or a broken part during forming or bending.
- Holes should be at least the sheet’s thickness from the edge: If holes are placed too close to the edge, the hole is more likely to deform, especially if the part later undergoes forming.
- Ensure holes are at least twice the sheet thickness from the start of the bend radius: If the hole is placed too close to the bend, it can become distorted or might act as an unintended relief cut.
The above list is not exhaustive since there are many factors to consider in any sheet metal fabrication. Creating a design using best practices, choosing the appropriate material, ensuring the steps in the fabrication process are completed correctly, and picking the best surface finish, if necessary, require lots of planning.
Conclusion
High-quality sheet metal fabrication does not happen in a vacuum. It results from much collaboration, cooperation, skills, and experience in a well-run manufacturing environment.
Sheet metal fabrication is a dynamic and multifaceted process that has broad applications in various industries.
From selecting the right type of metal to choosing an appropriate fabrication method and finish, each step is crucial for achieving a quality end product. Understanding the basics laid out in this article can be the cornerstone for anyone delving into the world of metal fabrication, whether you’re a seasoned professional or just getting started.
Keep in mind that design considerations are pivotal, as they play a significant role in the functionality, durability, and aesthetics of your finished piece.
Armed with this foundational knowledge, you are better equipped to navigate the complexities and realize the full potential of what sheet metal fabrication has to offer.