Bead blasting and sandblasting are two popular surface finishing techniques used in various industries, including automotive, aerospace, and manufacturing. These methods are often employed to improve the appearance, durability, and functionality of metal parts.
The main focuses of this comprehensive guide are the bead blasting process, examining bead blasted aluminium and bead blast finishes, and comparing bead blasting vs sandblasting, which can be helpful in choosing the right technique for a project.
What is Bead Blasting?
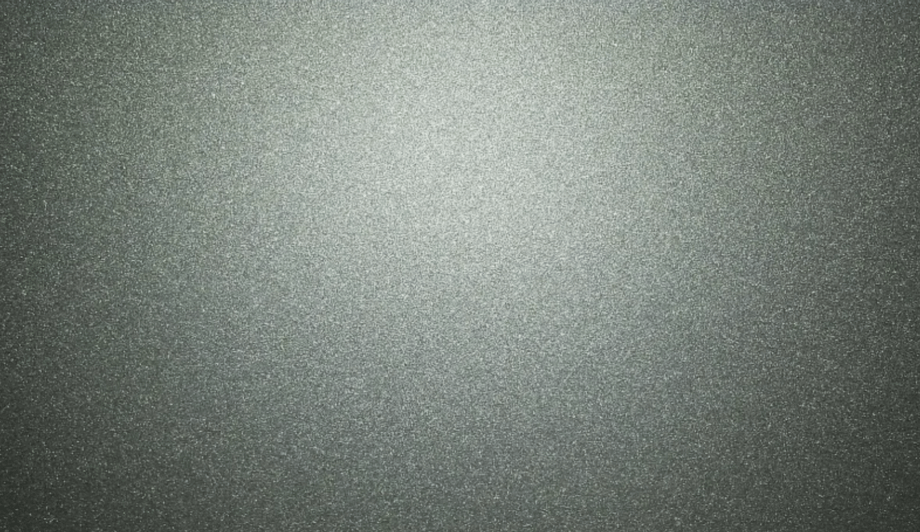
Bead blasting is a surface finishing technique that involves the use of small, spherical media (typically glass beads) to clean, deburr, and finish a workpiece.
The bead blasting media is propelled at high velocity against the surface of the material, removing contaminants, smoothing rough edges, and creating a uniform matte finish.
Bead Blasting Media
The choice of bead blasting media plays a crucial role in determining the final finish of the workpiece. Common bead-blasting media include:
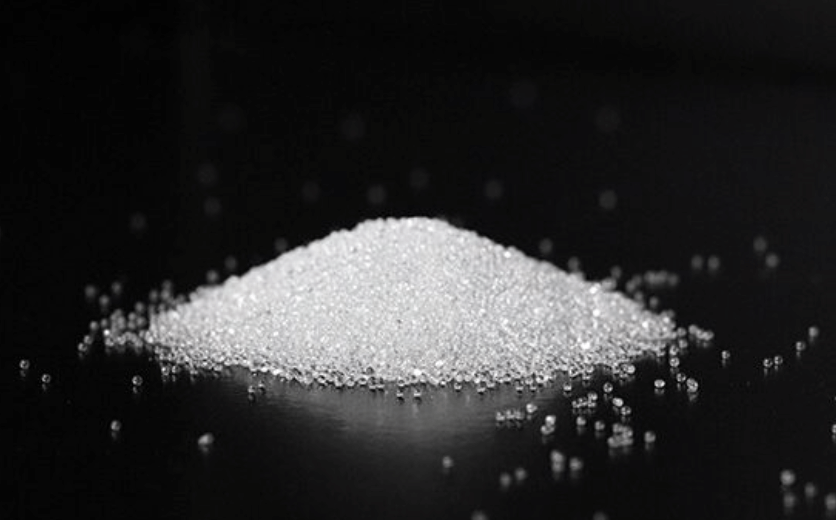
- Glass bead blasting media: Made from lead-free, soda-lime glass, these beads are the most popular choice for bead blasting. Glass bead blasting produces a smooth, satin-like finish while preserving the underlying surface details of the workpiece.
Utilizing glass beads, bead blasting creates an appealing, satin-like texture, unlike sandblasting’s rougher finish. When combined with powder coating, this process enhances both the aesthetics and durability of the end product.
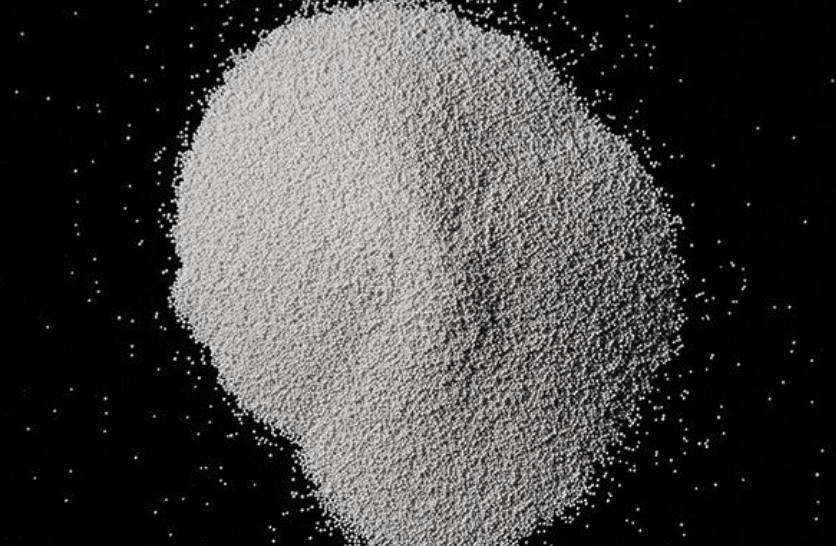
- Ceramic beads: These beads are more aggressive than glass beads, providing a faster cutting rate and longer service life. Ceramic bead blasting is suitable for applications requiring a more aggressive surface finish or the removal of more substantial contaminants.
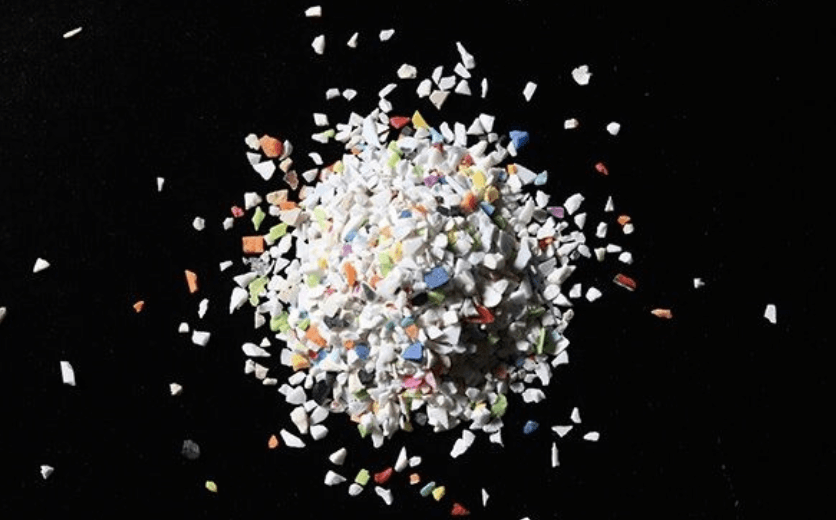
- Plastic beads: Ideal for delicate or sensitive surfaces, plastic bead blasting media offers a gentle cleaning action that removes contaminants without damaging the workpiece.
Process
Here are some key steps involved in the bead blasting process:
- Preparation: The material to be bead blasted is cleaned and prepared by removing any grease, oil, or other contaminants that could affect the blasting process.
- Abrasive Selection: Different materials require different types and sizes of abrasive beads, such as glass beads, aluminium oxide, steel shot, or silicon carbide. The selection depends on the desired finish and the material being blasted.
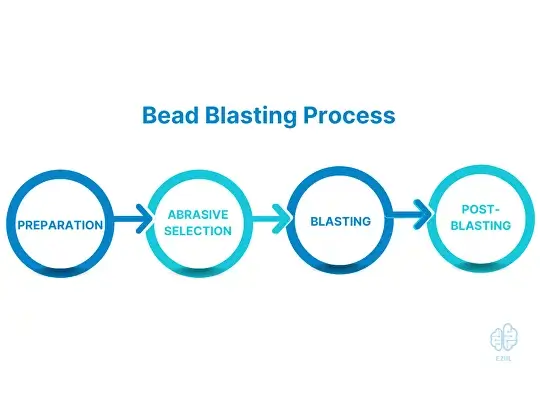
- Blasting: The abrasive particles are propelled through a specialised blasting gun or nozzle using compressed air or other propellant. The high-velocity impact of the particles on the material’s surface removes surface contaminants and creates the desired finish or texture.
- Post-Blasting: After the bead blasting process, the surface is typically cleaned to remove any remaining abrasive particles and debris. Coatings or finishes may be applied to protect the newly treated surface.
Benefits or Pros of Bead Blasting
- Surface Cleaning: Bead Blasting effectively removes rust, scale, old paint, dirt, and other contaminants from the surface of the material, restoring it to its original condition.
- Surface Preparation: It creates a clean and roughened surface, enhancing the adhesion of coatings, paints, or other finishes applied afterward.
- Deburring and Descaling: Bead blasting can remove burrs, sharp edges, and scale from metal components, improving their safety and functionality.
- Surface Finishing: By adjusting the type and size of abrasive beads, bead blasting can produce various surface finishes, from a smooth matte look to a textured or matte appearance.
- Non-Destructive: Bead blasting is a non-destructive method, as it removes only surface contaminants and does not damage the material itself.
- Versatility: It can be applied to various materials, including iron, steel, aluminium, brass, and even non-metallic materials like glass or plastics.
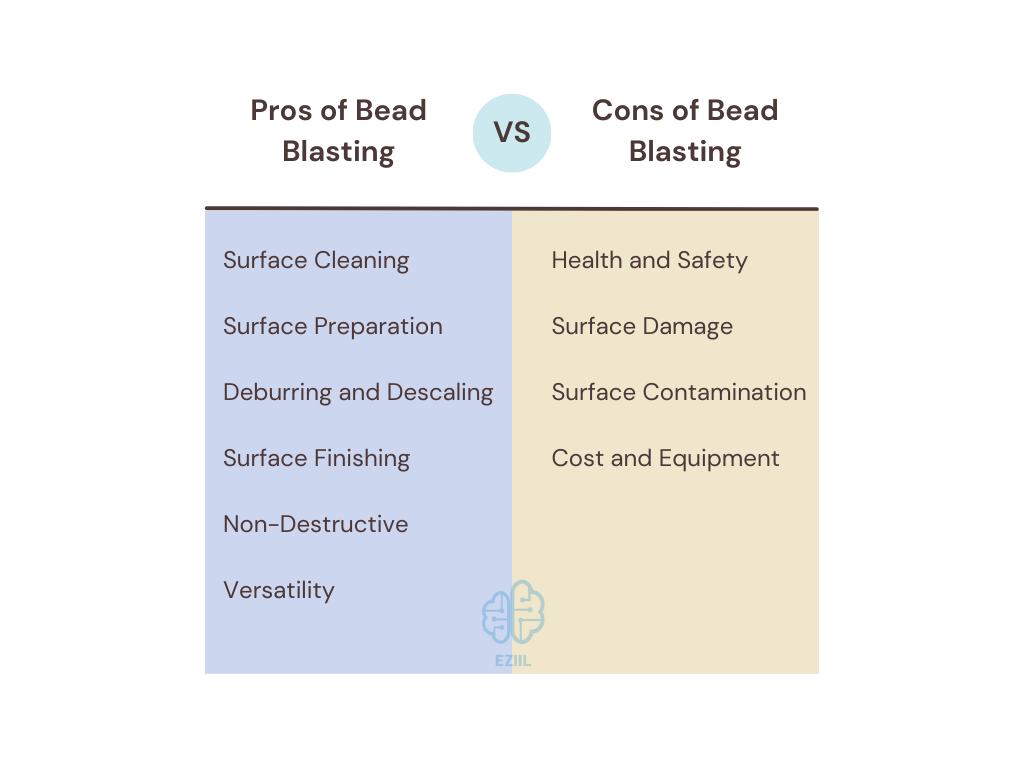
Cons and Considerations of Bead Blasting
- Health and Safety: Bead blasting generates dust and airborne particles that can be hazardous if inhaled. Proper safety measures, such as wearing protective clothing, and masks, and ensuring adequate ventilation, must be followed.
- Surface Damage: If not performed carefully or with improper equipment, bead blasting can cause damage to delicate or thin materials. It’s important to choose the appropriate pressure, abrasive type, and technique for each specific application.
- Surface Contamination: If the blasting process is not properly controlled or cleaned afterward, residual abrasive particles can remain on the surface, leading to potential contamination issues.
- Cost and Equipment: Bead blasting equipment can be expensive, especially for large-scale applications. Additionally, the cost of abrasive materials and the maintenance of the equipment should be considered.
Overall, bead blasting is a versatile and effective method for surface preparation and finishing. It offers numerous benefits but requires proper equipment, safety measures, and expertise to achieve the desired results while minimising potential drawbacks.
Sand Blasting
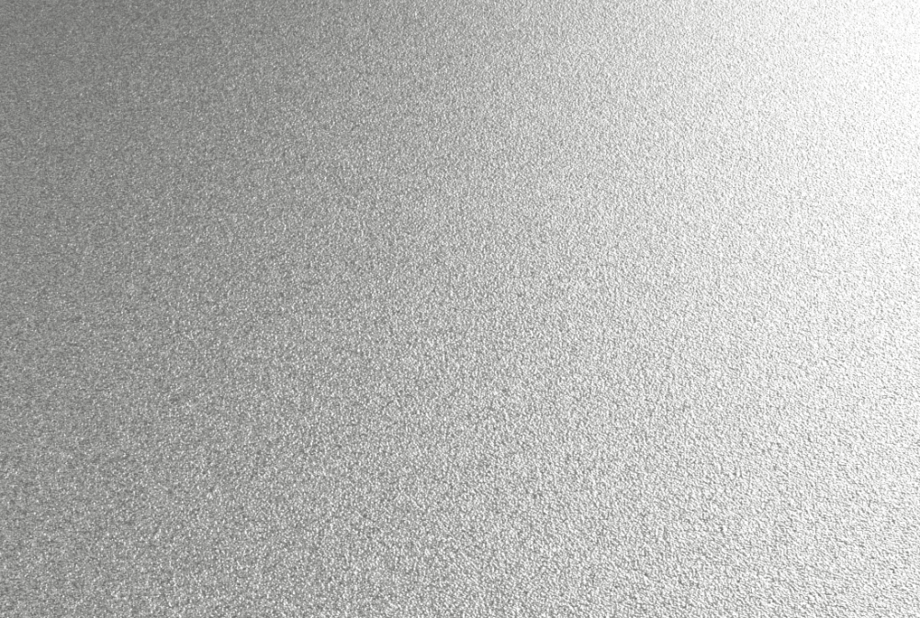
Sandblasting is a surface preparation technique that involves propelling fine grains of sand at high velocity to impact the surface being treated.
Here is a brief overview of the sandblasting process and its pros and cons.
Process
- Surface Preparation: The surface to be treated is cleaned and prepared by removing any grease, oil, or other contaminants that could affect the blasting process.
- Abrasive Selection: Sand of varying grit sizes is commonly used as the abrasive material in sandblasting. The size and type of sand particles are chosen based on the desired finish and the material being blasted.
- Blasting: The sand is propelled through a specialised blasting gun or nozzle using compressed air or other propellant. The high-velocity impact of the sand particles on the surface removes coatings, rust, scale, or other contaminants, preparing the surface for further treatment or finishing.
- Post-Blasting: After the sandblasting process, the surface is typically cleaned to remove any residual abrasive particles and debris. Coatings, paints, or other finishes may be applied to protect the treated surface.
Pros or Benefits of Sand Blasting
- Versatile Surface Preparation: Sandblasting suits various materials, including metals, concrete, brick, stone, and wood. It effectively removes coatings, rust, scale, and other contaminants from surfaces.
- Roughened Surface: Sand blasting creates a roughened surface, enhancing the adhesion of coatings, paints, or other finishes applied afterward.
- Wide Range of Abrasive Grit Sizes: Sand is available in various grit sizes, allowing for flexibility in achieving different surface textures or profiles.
- Powerful Cleaning Action: Sandblasting can remove thick coatings, heavy rust, scale, or other stubborn contaminants that may be difficult to remove using other methods.
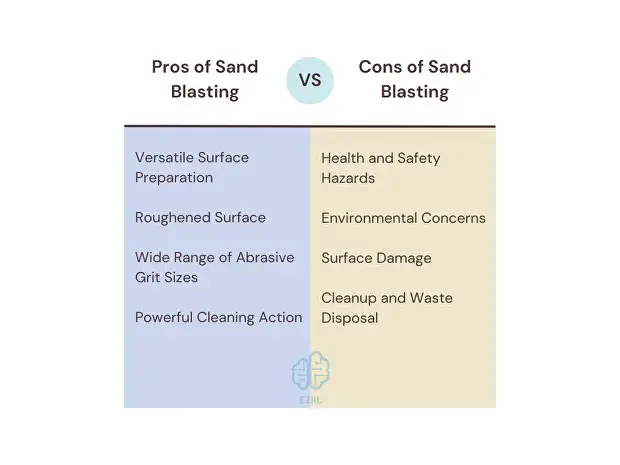
Cons and Considerations of Sandblasting
- Health and Safety Hazards: Sandblasting generates a significant amount of fine dust particles, which can pose health risks if inhaled. Proper safety measures, such as wearing protective clothing, and masks, and ensuring adequate ventilation, must be followed to minimise exposure to dust.
- Environmental Concerns: The dust generated during sandblasting can also contribute to environmental pollution if not properly contained or captured.
- Surface Damage: If not performed carefully or with improper equipment, sandblasting can cause damage to delicate or thin materials. The high-velocity impact of sand particles can lead to surface abrasion or material deformation.
- Cleanup and Waste Disposal: Sandblasting generates a considerable amount of waste, including used sand and debris. Proper disposal methods must be followed to prevent environmental contamination.
It’s important to note that due to environmental and health concerns related to the dust generated during sandblasting, alternative abrasive materials and blasting methods, such as bead blasting or other forms of abrasive blasting, are gaining popularity in certain industries.
Glass Beads Sandblasting: An Alternative Media
While sand is the traditional media used in sandblasting, glass beads can also be employed in the sandblasting process. Glass beads sandblasting provides a gentler, more controlled surface treatment that is ideal for delicate or intricate workpieces. The advantages of glass bead sandblasting include:
- A smoother finish: Glass beads produce a more refined, satin-like finish compared to sand.
- Reduced surface damage: Glass beads are less aggressive than sand, making them ideal for delicate or sensitive surfaces that require gentler treatment.
- Enhanced surface properties: Glass bead blasting can help improve the surface properties of the workpiece, such as increasing wear resistance and reducing friction.
Bead Blasting vs Sandblasting: Key Differences
When deciding between bead blasting and sandblasting for the project, it’s essential to understand the key differences between these two surface finishing techniques.
Here are some factors to consider when choosing between bead blasting and sandblasting:
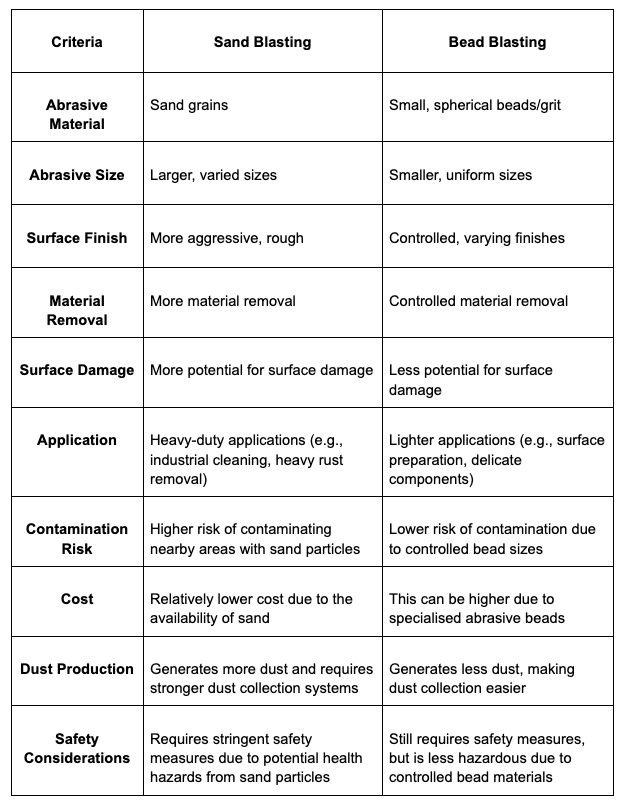
Bead blasting, a process that manipulates the surface of a workpiece with small glass beads, crafts a unique satin-like finish. It stands distinct from sandblasting, which employs gritty materials like aluminum oxide for a coarser result (sandblasting employs the abrasive qualities of silica sand to create a more rugged, textured surface).
The aluminum oxide in sandblasting, while aggressive and effective in creating a textured surface, does not offer the subtle sheen that bead blasting does.
Despite their differences, both methods can benefit from aluminum oxide when it comes to preparation for further treatments, as its usage can facilitate a clean and ready-to-use surface.
In comparison, when it’s about the final finish, bead blasting achieves a refined look that aluminum oxide’s rugged texture can’t match.
Book a 60-minute demo to see
how eziil mrp solution works for you
How to Choose the Right Surface Finishing Technique
When deciding between bead blasting and sandblasting for the project, consider the following factors:
- Desired surface finish: It is usually suggested to choose sandblasting for a smooth, satin-like finish, and bead blasting for a rougher, more textured surface.
- Material sensitivity: Examine the workpiece whether it is made of a delicate or sensitive material that requires a gentler treatment or not. If it is made out of a delicate material, then opt for bead blasting with a less aggressive media, such as glass or plastic beads.
- Material removal or profiling needs: If the project requires aggressive material removal or surface profiling, sandblasting may be the better choice.
- Environmental impact: Consider the environmental implications of the chosen surface finishing technique, including dust generation and waste disposal.
Conclusion
Bead blasting and sandblasting are popular surfaces finishing techniques used to clean, deburr, and finish workpieces in various industries. Both methods offer unique advantages and produce different surface finishes. Bead blasting is ideal for creating a smooth, uniform, satin-like finish while sandblasting is better suited for rougher surfaces or aggressive material removal.
By understanding the differences between bead blasting and sandblasting, including the types of media used, the resulting surface finishes, and the applications best suited for each technique, more informed decisions can be made about the best surface finishing method for a specific project.
Whether the work is to be done with bead-blasted aluminium, glass beads sandblasting, or traditional sandblasting, selecting the right technique can help achieve the desired results and enhance the functionality, appearance, and durability of the workpiece.