Adopting a robust shop floor management framework—rooted in lean thinking and reinforced by modern digital tools—is important in 2025 to keep a competitive edge and optimize performance and thus your revenue. If you’re a small metal fabricator, you may already feel the strain.
“Thriving in today’s business environment requires companies to continuously strive for operational excellence at all levels of the organization. Simply working to maintain existing operations is not an adequate or sustainable business strategy, especially when competing in a global market.” — Fundamentals of Daily Shop Floor Management: A Guide for Manufacturing Optimization and Excellence (Philip J. Gisi)
This statement rings especially true today for small metal fabrication shops. The shop floor has evolved into a central hub of activity where multiple complexities intersect: tighter customer deadlines, increased customization demands, and ever-rising cost pressures. Customers expect on-time deliveries at competitive prices without compromising on quality, forcing fabricators to juggle schedules, capacity, and labor constraints more carefully than ever before.
The good news is you don’t have to leap into a full-blown, complex ERP to modernize. In this article we’ll dive into specific lean shop floor management strategies tailored for small metal shops.
We’ll also show how tools like EZIIL Starter empower you to implement these lean tactics with minimal disruption and a clear ROI.
lean shop floor management: 5 proven techniques
Before diving into the five lean shop floor management techniques, it’s worth noting that “lean” isn’t just about cutting costs or speeding up production; it’s about creating a shop floor environment that naturally promotes continuous improvement, open communication, and real-time problem-solving.
1. Visual task and workflow management
First and foremost, let’s talk about process visibility. Effective visual controls let employees see problems immediately and focus on them quickly without waiting for management’s approval. When your team can glance at a board—or open a real-time digital dashboard—and instantly understand what needs doing, when, and by whom, confusion and idle time will drop dramatically. For small metal fabricators often juggling multiple orders and customized jobs, clear visual cues can prevent tasks from getting overlooked, especially under tight timelines.
2025 best practices:
- Cloud-based dashboards: Replace static spreadsheets or whiteboards with digital tools that update in real time, ensuring everyone is looking at the same information.
- Mobile-friendly access: With employees often moving between machines, stations, and offices, having a visual workflow that’s accessible via smartphones or tablets fosters quick issue resolution on the shop floor.
How EZIIL Starter helps:
- Centralized platform: Eliminates the chaos of multiple Excel files and scattered project documents; all data is available in one easy-to-use interface.
- Drag-and-drop scheduling: Quick changes can be made to reflect design updates or rush orders without derailing the rest of production.
- Color-coded progress bars: Clearly displays job status (on time, at risk, behind schedule), allowing teams to solve bottlenecks before they become critical delays.
2. Standardized work processes and templates
Standardizing work—whether it’s how you cut raw material or how you log finishing times—creates predictability and consistency. This predictability in turn reduces rework, helps maintain quality, and preserves valuable labor hours for higher-level problem-solving rather than last-minute fixes.
Key lean shop floor management techniques
- Standard Operating Procedures (SOPs): Clearly document the steps for each task, from part loading to machine calibration.
- Repeatable routing and templates: Particularly crucial if you run the same or similar projects repeatedly. Defining a standard route ensures no detail gets missed when pressure mounts.
How EZIIL Starter helps:
- Auto-planning for repeat projects: Quickly set up new jobs based on saved templates, ensuring consistent sequencing of tasks.
- Standardized input fields: Eliminates guesswork by enforcing mandatory data entries—like material specs or machine assignment—so critical details never fall through the cracks.
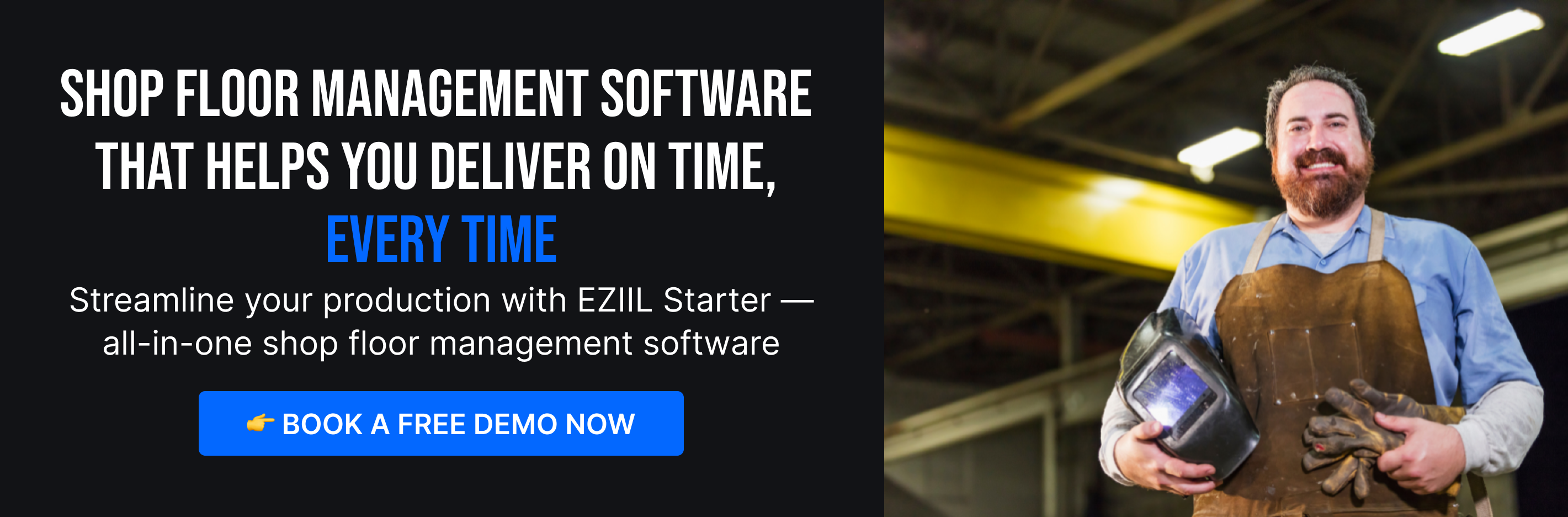
3. Real-time production monitoring and bottleneck prevention
Unplanned downtime or slowdowns can sabotage the most carefully scheduled plan. These setbacks quickly cascade into missed deadlines and frustrated customers. A single delayed welding machine, for instance, can disrupt multiple downstream tasks.
Lean shop floor management principle: “Go and see” (Gemba)
Lean practitioners advocate digitally or, if needed, physically checking on the shop floor and investigating processes firsthand. Suzaki emphasizes that continuous improvement starts with “direct engagement at the point of action” so managers and operators don’t miss subtle early warnings. Early identification of a potential backlog or equipment glitch helps you resolve it before it becomes a crisis.
How EZIIL Starter helps:
- Live capacity overview: Immediately shows team leads where potential overload is brewing, letting them redistribute tasks accordingly.
- Real-time status tracking: No more toggling between five different spreadsheets—everything from machine uptime to job progress is consolidated on a single dashboard.
4. Quick changeover and efficient scheduling (SMED principles)
For metal fabrication shops handling diverse, low-volume orders with frequent changeovers, Single-Minute Exchange of Dies (SMED) can be a lifesaver. By focusing on rapid changeover steps that you can perform while machines still run (external setup) and streamlining tasks that must happen when machines are idle (internal setup), fabricators cut downtime drastically. This method is particularly relevant when your backlog mixes urgent one-off projects with regular production runs.
Lean shop floor management tactic: SMED for high-mix, low-volume
- Identify: Break down every changeover action into discrete steps.
- Separate: Distinguish external tasks (can be done in advance) from internal ones (must be done during machine downtime).
- Optimize: Eliminate or reduce any redundant steps, and ensure vital tools or materials are on standby before the swap begins.
How EZIIL Starter helps:
- EZIIL’s drag-and-drop scheduler: Shift tasks and reorder priorities in seconds, responding seamlessly to design changes or new orders.
- Adaptive task templates: Quickly apply consistent best practices for setup across similar jobs, reinforcing SMED principles.
5. Data-driven continuous improvement
Peter Drucker famously said, “What gets measured, gets managed.” In any kind of manufacturing business, daily shop floor management thrives on factual information and measurement data. In a metal fabrication context, data highlights which processes consume the most time, produce the most scrap, or cause the highest rework. Armed with numbers, you can tackle root causes instead of putting on band-aids.
Practical steps:
- Define KPIs: On-time delivery rate, idle machine hours, and scrap/rework rates are common.
- Set up regular Kaizen huddles: Daily or weekly short meetings with team members for continuous improvement, each driven by real metrics.
- Close the loop: Implement changes and track whether they deliver measurable improvements in future cycles.
How EZIIL Starter helps:
- Planned vs. reality reporting: Quickly compare estimated times and costs against actuals to see where profits slip.
- Productivity tracking: Spot which machines or tasks repeatedly cause delays, ensuring you prioritize the right fixes.
- Visual analytics: Color-coded charts or progress bars highlight inefficiencies, so your team can respond proactively rather than reactively.
Shop floor management software for small custom metal fabricators
While historically, “lean shop floor management” might have seemed synonymous with massive ERP deployments, the reality in 2025 is different. You can adopt scalable digital shop floor management software that grow with your business—ensuring you gain all the benefits of lean shop floor management without drowning in unnecessary complexity or ballooning costs.
Additionally, for many small metal fabricators, the fear of “going digital” is often rooted in past nightmares with complex systems and endless training sessions. EZIIL Starter flips that narrative by giving metal shops a simple, user-friendly platform that replaces pen-and-paper chaos and eliminates the need to juggle multiple spreadsheets. It offers a centralized hub for task scheduling, job status updates, and real-time production overviews—all without forcing you into expensive features you won’t use.
Crucially, you only pay for what you truly need on a monthly basis (no upfront costs, cancel an time). This means if your team is primarily focused on streamlining scheduling and monitoring tasks on the shop floor, you won’t be saddled with modules for purchasing, inventory management, or BOMs until you’re ready. It’s designed to be a lightweight, cost-effective tool that any metal fabricator can adopt quickly, reaping immediate ROI by cutting down on miscommunication and rework.
As your business grows—whether through new projects, expansions into multi-stage operations, or advanced customer requirements—you can add on more powerful modules, such as:
- Bill of Materials (BOM) management
- Purchasing and inventory: Manage warehouse stock, track material movements, and handle pricing inquiries efficiently.
- EN 1090-2 compliance: Keep detailed records to meet industry standards without letting paperwork slow you down.
- Subcontractor and shipment management: Oversee outsourced tasks seamlessly and track deliveries in one place.
Unlike typical ERPs that impose a “take-it-or-leave-it” approach, EZIIL Enterprise is modular. You can “pick and mix” features—whether it’s just BOM management or full production oversight—so you don’t get buried under functionality your shop doesn’t need.
What is shop floor management?
The term “shop floor management” (SFM) encompasses the day-to-day processes, methods, and leadership approaches that keep production flowing smoothly. It involves real-time monitoring of tasks and resources, proactive problem-solving, and close collaboration between teams on the ground and management.
Now, what makes shop floor management lean is the shift away from localized command techniques toward a learning environment, enabling everyone on the shop floor to quickly spot and resolve issues. This approach perfectly encapsulates the lean ethos: empower teams, reduce waste, and cultivate a culture of continuous improvement.
For custom metal fabricators, lean shop floor management typically translates into:
- Waste reduction in material handling, setup times, and rework.
- Streamlined workflows that sequence tasks logically to prevent bottlenecks.
- Ongoing improvement cycles where every step is measured, evaluated, and refined for better results.
Whether your core challenge is meeting increasingly tighter deadlines or controlling production costs, lean shop floor management ensures you stay ahead of competitors, protect your reputation, and run a profitable shop in the process.
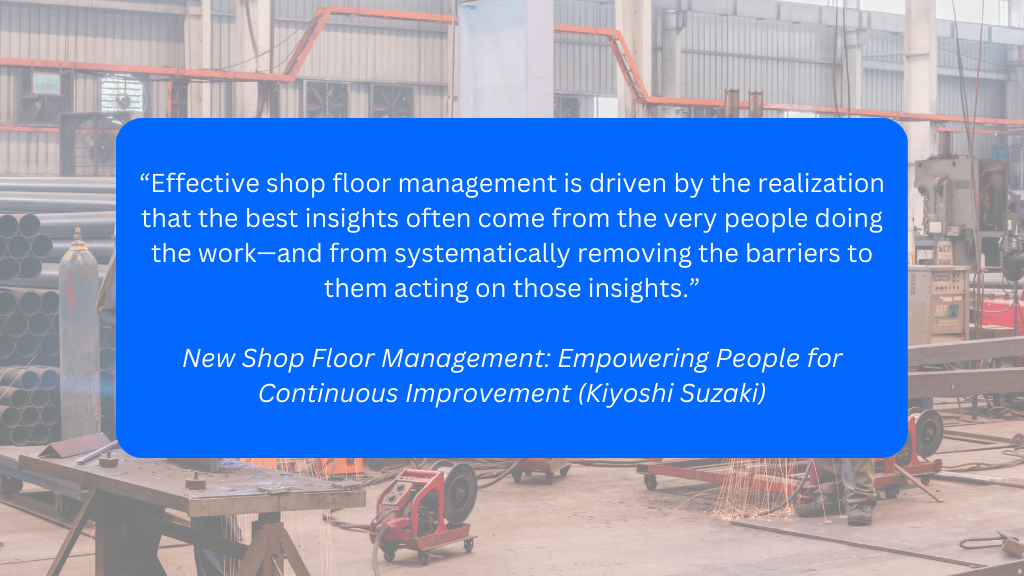
The importance of lean shop floor management
“Processes must be stable, capable, and controlled as a prerequisite for sustainable improvement.” — Fundamentals of Daily Shop Floor Management: A Guide for Manufacturing Optimization and Excellence (Philip J. Gisi)
This observation captures the precarious situation many small metal fabrication shops find themselves in today. Market competition intensifies with each passing quarter, while customers push for faster turnaround times, higher customization, and uncompromising quality.
According to the 2025 Global Metal Fabrication Market Report, the industry is poised to grow from USD 24.86 billion in 2025 to USD 37.29 billion by 2033.
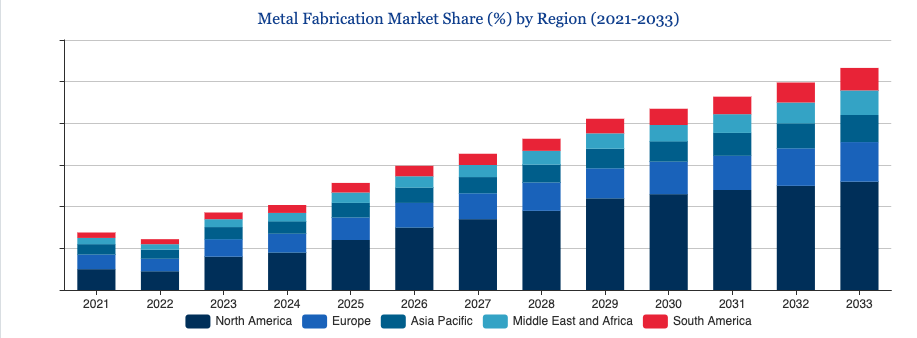
This means increasing competition and heightened customer demands, especially for custom or precision-engineered metal parts. Under these pressures, any instability in shop floor processes—be it a bottleneck at a critical machine or a sudden rush order—can quickly snowball into rework, late deliveries, and customer dissatisfaction.
Often it’s the daily hurdles that become the invisible drain on profit and team morale:
- Production delays and scheduling chaos Rushed orders, last-minute design changes, or poorly synced workflows can cause entire production lines to stall.
- Machine downtime and resource bottlenecks When critical equipment fails or support teams aren’t aligned, hours of lost production time result in delayed deliveries.
- Missing design updates and confusion In a pen-and-paper or spreadsheet-based environment, any updated blueprint or spec can get overlooked if it isn’t shared with everyone on time.
- Team miscommunication and task overlaps Without a single source of truth, multiple people might be assigned the same task (or no one takes ownership at all), leading to wasted effort and rework.
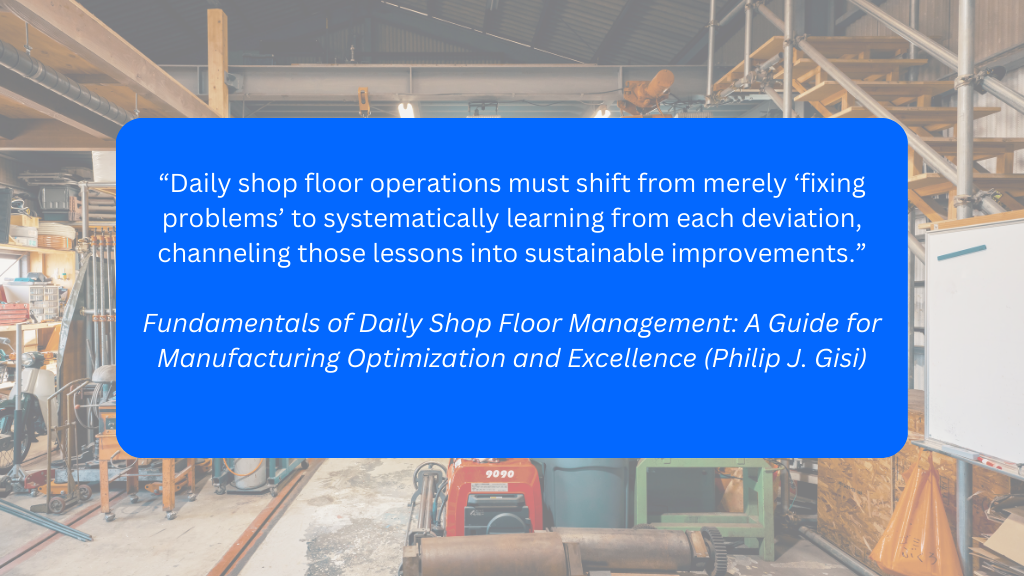
Added to this is the fear of losing a competitive edge. As machine downtime, excess scrap, or poor coordination eat away at profit margins, small shops risk falling behind larger competitors that have already embraced systematic, data-driven workflows. Even worse, reputations built over decades can be jeopardized by just a few botched deliveries or visible production delays.
The reality is, you either modernize and adapt to the accelerating pace, or risk your clients and profits slip away to more efficient rivals.
Benefits of adapting lean shop floor management techniques
So why do metal fabricators embark on this journey toward more disciplined, data-driven management? Because the rewards are both tangible and transformative:
- Increased profitability and ROI Eliminating excess rework and reducing machine downtime put dollars back into your business, helping you stay competitive without cutting corners.
- Enhanced transparency and control Real-time insights into job statuses and resource allocation let you spot issues early, reducing last-minute chaos and boosting on-time deliveries.
- Stable operations and peace of mind With streamlined, predictable workflows, team members can spend more time on continuous improvement rather than crisis management.
- Improved customer satisfaction Faster turnarounds, accurate quotes, and fewer mistakes build trust, resulting in more repeat projects and referrals.
In concrete terms, many shops report up to a 20% increase in on-time deliveries and a significant reduction in rework after standardizing procedures and investing in digital planning tools.
To sum it up…
In essence, the lean shop floor management techniques outlined in this article can dramatically cut through the noise and inefficiencies that plague small metal fabrication shops. Whether you implement two, or more of these approaches, the end goal remains the same: boosting profitability, streamlining work, and sustaining a culture of continuous improvement that keeps you one step ahead of the competition.
Above all, remember to address real pain points, keep your team motivated with clear ROI metrics, and leverage tools like EZIIL to turn your shop floor into a high-performing, future-ready operation.
What is shop floor management in lean manufacturing?
It’s the day-to-day system that keeps workers, machines and materials flowing at the pace of customer demand. Think of it as the operating rhythm—stand-ups, visual boards and KPIs—that supports continuous improvement on the shop floor.
Which lean techniques improve shop-floor efficiency fastest?
Start with 5S for workplace order, add visual management boards so everyone sees the plan, then introduce Kanban cards to trigger material flow. Those three steps typically cut search-time and WIP by 20–30%.
How does a Gemba walk differ from a Kaizen event?
A Gemba walk is a short, daily visit by leaders to observe work and ask questions; a Kaizen event is a dedicated multi-day workshop focused on eliminating a specific waste. Both reinforce continuous improvement but at different cadences.
Can software support lean shop floor management?
Yes. Tools like Eziil visualise the schedule, flag bottlenecks in real time and collect data automatically, so teams spend less time updating spreadsheets and more time improving the flow.
What KPIs should I track on the shop floor?
Start with OEE, first-pass yield, on-time-delivery and inventory turns. Together they reveal how well people, machines and materials are utilised and how reliably orders ship.
How to manage a shop floor effectively?
Start with a clear, visual production schedule that everyone sees at a glance. Pair it with standard work instructions, daily Gemba walks to remove bottlenecks, and real-time KPI tracking (OEE, on-time delivery). Software like EZIIL centralises some of those pieces so updates flow automatically.