Paint has been the conventional approach to metal finishing, with only some exceptions until the 1960s. That’s when powder coating was introduced in North America and became a more advanced method of achieving a durable finish on various surfaces. Today, metal powder coaters represent over 15% of the total industrial finishing market, according to the Powder Coating Institute.
As a result, more companies specify the powder coating process for their parts and products since protective and decorative finishes are available in numerous textures and colors.
So, what is powder coating, and how does it maximize production, improve efficiencies, and simplify environmental compliance?
Here’s what manufacturers should know:
What is Powder Coating?
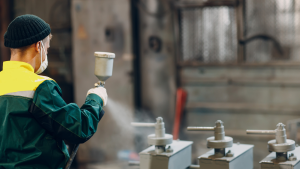
Powder coating is a dry powder applied to a charged surface, creating a thicker coating in one application than a single coat of paint. An electrostatic charge holds the coating onto the surface after curing.
The time-consuming process required to prepare and powder coat metal surfaces makes it a practical solution for large-volume orders.
Powder coatings contain several ingredients: a polymer resin for the finish’s core, curatives, color pigments, leveling agents, flow modifiers, and other additives. These ingredients are melted, mixed, cooled, and ground into a uniform powder. These parts work together to create a colored, protective surface that performs well in many environments after curing.
How Does Powder Coating Work?
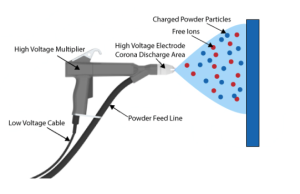
Using a spray gun, an electrostatic spray deposition (ESD) is typically used to apply the powder coating to a grounded metal substrate. Although the powder is inert, an electrode fitting in the gun provides an electrostatic charge as the particles pass through it. When heat is applied, the particles stick onto the grounded surface and become solidified into a dense coating during curing.
Another application method is a fluidized bed, where heated parts are dipped in a hopper of fluidizing powder, and the coating melts and flows onto the piece. Post-cure might be needed depending on the part’s mass and temperature and the type of powder used.
Regardless of the application process, powder coatings are environmentally friendly, cost-effective, and durable.
Check out this easy-to-follow video explaining powder coating, its process, and how it works:
Surface Preparation is Essential
Before applying any powder coating material, the substrate’s surface must be cleaned and treated to ensure the part is free of dust, dirt, and debris. If a surface is not sufficiently prepared, these residues could affect the powder’s adhesion and the final finish’s quality. The complete preparation depends on the material, but the treatments typically include cleaning, rinsing, etching, blasting, and drying. Wash stations, blast rooms, and dry-off ovens are the most common material preparation equipment.
Oil, grease, solvent, and other residue are removed from a part’s surface using weak alkali and neutral detergents in dip tanks or wash stations. Wash stations can spray parts with hot water, steam, detergent, and other pretreatment solutions to prepare the surface for coating.
If specific sections remain uncoated, masking products are applied to the substrate before the application stage. These products come in various standard and custom shapes and forms but are usually made of a paper or plastic film coated with a pressure-sensitive adhesive. They stick to the substrate’s surface, protecting the covered area from powder during coating operations.
How Long Does Powder Coating Last?
The longevity of powder-coated steel depends on several factors, including the type of powder coat used, the quality of preparation, and the environment in which the product is exposed. Powder coating finishes typically last up to 20 years, but they could break down sooner because of constant use, UV light exposure, and a harsh outdoor environment.
Different coatings also have various lifespans. For instance, coatings containing fluoropolymers and urethanes can last longer since they are designed to withstand extreme conditions and are better suited for outdoor products. On the other hand, epoxy coatings lasting very long indoors, tend to break down faster when exposed to the outdoors.
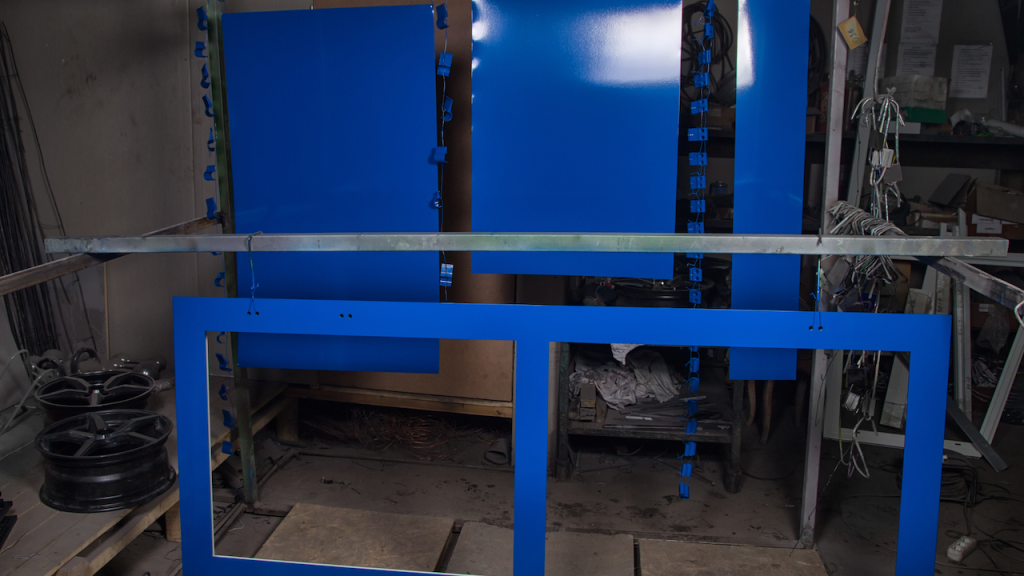
Is Powder Coating Durable?
Regarding powder coating, durability is the word that consistently crops up to describe it. It’s a high-quality finish on thousands of products in homes and businesses. With powder coating, manufacturing found a process that protects the most complex working machinery and components from impact, moisture, chemicals, ultraviolet light, and other extreme weather conditions.
This reduces the risk of scratches, chipping, abrasions, corrosion, fading, and other wear issues.
The same holds for all the household items consumers depend on, giving these items more durability than liquid paint finishes.
Book a 60-minute demo to see
how eziil mrp solution works for you
Why Choose Powder-Coating Paints Over Traditional Liquid Paints?
Powder coatings have several advantages, making them the preferred choice for metal fabrication. Aside from their durability, powder-coated parts and products have benefits that can’t be ignored:
- Environmentally friendly: Because it’s reusable and recyclable, powder coating is eco-friendly. Unlike paint, notorious for overspray, the powder is used precisely with minimal waste. Another advantage is that solvents containing volatile organic compounds are not released to harm the environment. Also, the powder is safer and does not pose the same health threat as other finishes.
- Cost-effective: Powder coating is much less expensive over time than paint or other finishes, particularly after workers become familiar with the process.
- Polished, clean look: It’s easy to get a polished look when powder coating metal. It repels chemicals, moisture, and other elements, making cleaning easy.
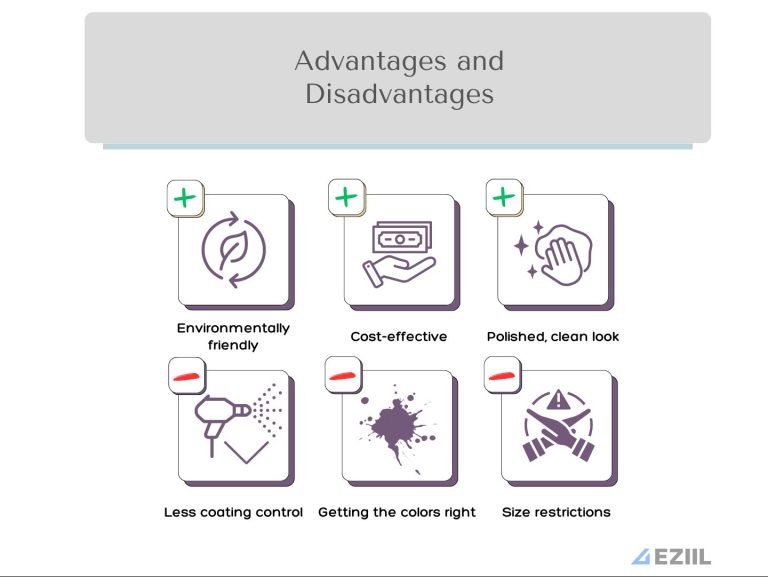
Are there any Disadvantages?
Although powder coating has several advantages, the disadvantages must be addressed.
- Less coating control: It’s sometimes challenging to get the correct thickness level; uneven thickness levels can affect the overall texture. If the powder coating runs, the coating process must be redone.
- Getting the colors right: Even though recycling and reusing powder coatings is advantageous, it could also lead to cross-contamination, meaning that the colors might not come out as intended. You can avoid this by packaging all powders when they are not being used.
- Size restrictions: Because powder coating requires heating the part in the oven, it’s all but impossible to coat large fabrications or non-standard items, such as construction components.
In summary
Powder coating offers some of the best finishes in metal fabrication. They are tough, look great, and last a long time.
In addition to being durable, powder coating is an attractive choice with environmentally-friendly advantages.