Welding plays a pivotal role in various industries such as automotive manufacturing, construction, and product design. With a multitude of welding processes at their disposal, including MIG welding, stick welding, and arc welding, professionals must understand the differences between each technique to achieve optimal results. In this article, we will delve into different types of gas welding, their applications, and their advantages for those working with carbon steel and other welding materials.
Oxyfuel welding, is the process of melting the edges of two pieces of metal using a gas flame, causing the molten metals to diffuse into each other, forming a solid joint after it cools. Since the development of arc welding, oxyfuel welding isn’t as standard as it once was, but smaller weld shops and home workshops still rely on it.
When metals are joined with this method, oxygen and fuel gases are combined to create a high-temperature flame of about 3,200°C. The gases used with oxygen are typically acetylene, hydrogen, propylene, butane, and others. The choice of fuel gas often depends on the project type and the flame control desired (more on that later).
Gas Welding Types:
Gas welding is a versatile category encompassing several techniques. Some of the most popular gas welding methods include oxyacetylene welding, MIG (Gas Metal Arc) welding, and TIG (Gas Tungsten Arc) welding. Each type has distinct characteristics and advantages, making them suitable for various applications in product design and mechanical engineering.
Because acetylene is the most frequently used fuel gas, many welders refer to the process as oxyacetylene welding. However, there are five types of oxyfuel welding, and here are the details on each of them:
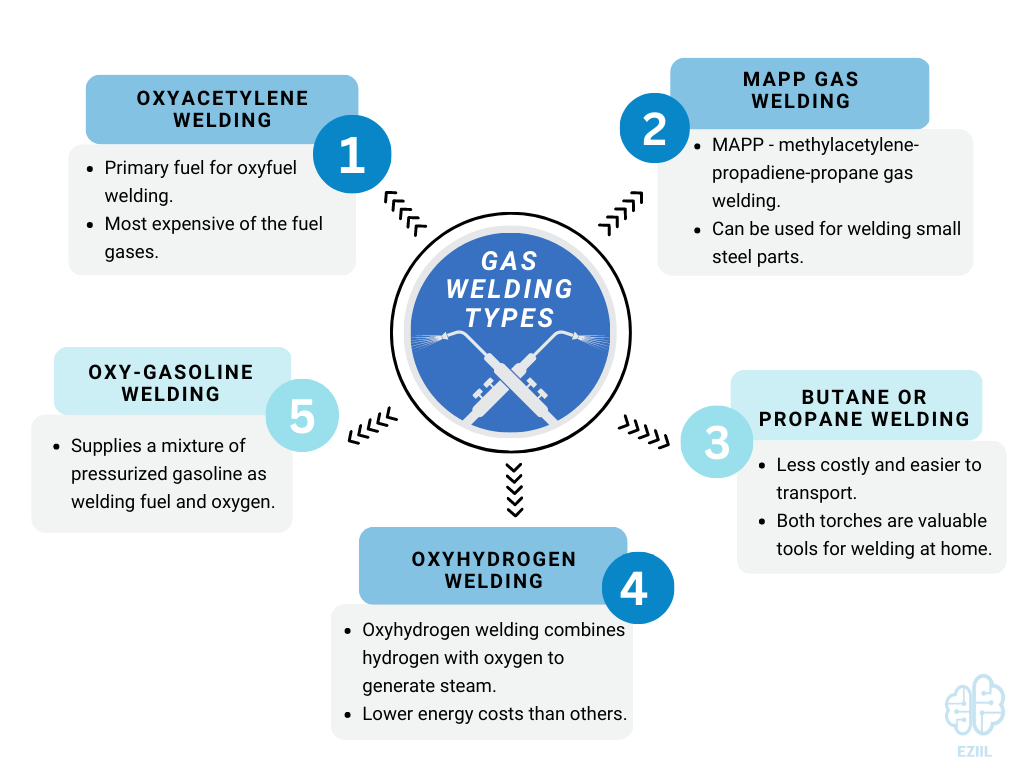
1. Oxyacetylene welding
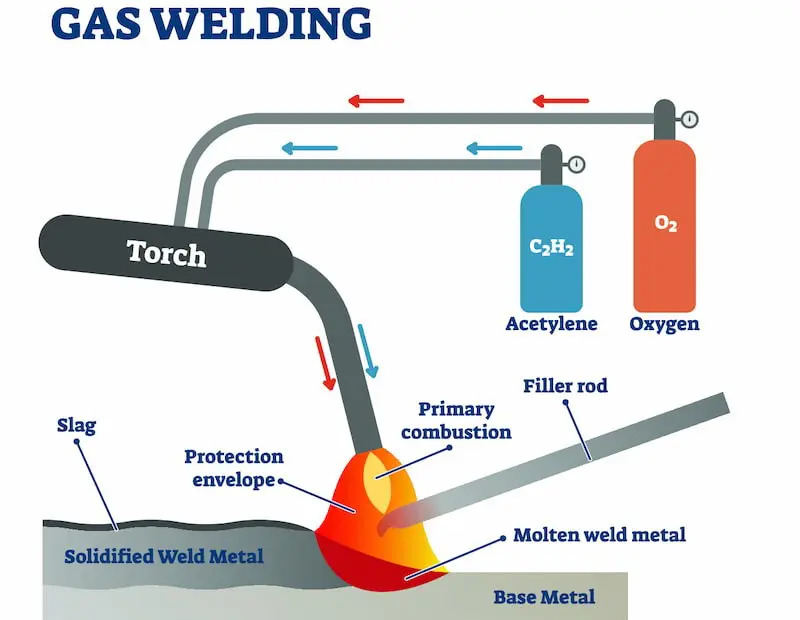
Source: https://fractory.com
Acetylene is the primary fuel for oxyfuel welding. Oxyacetylene provides the highest flame temperature of the fuel gases, making it ideal for welding high-strength steels. The equipment is portable and relatively easy to use. It comprises individual steel cylinders of oxygen and acetylene gases under pressure, each fitted with regulators and hoses that lead to the mixing chamber.
Welders can adjust the flame by changing the ratio of oxygen to acetylene, creating three flame settings: neutral, oxidizing, and carburizing. Most welding occurs with the neutral flame setting, meaning there are equal quantities of oxygen and acetylene. Increasing the oxygen flow rate produces an oxidizing flame while carburizing is obtained with a higher acetylene rate.
Specially designed safety valves between the hoses and the cylinder regulators keep the gas flowing in one direction, reducing the possibility of a hazardous flashback. And because acetylene is a volatile gas, it requires careful handling and specific storage procedures.
Even though acetylene is typically the most expensive of the fuel gases, oxyacetylene welding is the top choice of many beginners and part-time welders since it is a flexible and forgiving process.
2. MAPP gas welding
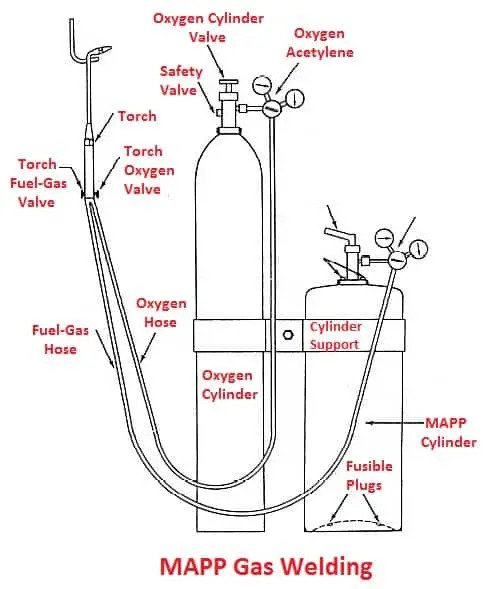
Source: https://www.theengineerspost.com
MAPP stands for methylacetylene-propadiene-propane oxyfuel welding. It is a gas mixture that is more inert than others, making it safer and easier to use than acetylene and a favorite of beginner and recreational welders. Unlike acetylene, MAPP gas is less likely to explode if the cylinder is hit or bumped. It also withstands higher pressures, making it ideal for underwater work, such as ship repairs.
MAPP gas production ended in North America in 2008. Still, MAPP substitutes containing mostly propylene, some propane, and occasionally dimethyl ether are available. Although MAPP gas flames do not burn as hot as acetylene, some welders insist it meets or exceeds the performance of acetylene in welding.
However, the hydrogen concentration in the flame infuses into the molten steel, making the welds brittle. But for small-scale welding projects, the hydrogen escapes, and MAPP can be used for welding small steel parts.
3. Butane or propane welding

Source: https://homebounties.com
Butane and propane are similar gases that can be used individually as fuel or combined. They have lower flame temperatures than acetylene and are less costly and easier to transport.
Propane torches are often used for soldering, bending, and heating, and because propane is a heavy gas, they require a different torch tip than the injector tip. Both torches are valuable tools for welding at home, but each torch produces different temperatures: Butane reaches around 2,400 degrees Fahrenheit, while propane torches can heat to 3,600 degrees Fahrenheit.
Propane torches have a small torch head that curves inward, allowing a more concentrated flame. The closer the flame is to the workpiece, the more precise and hot it is, and vice-versa. Butane torches have straight open ends, emitting a full flame. However, butane torch triggers can emit low or high amounts of butane, enabling the welder to control the flame temperature.
Although butane torches have a weaker flame, they are more compact and portable, making them better suited for soldering metals, drying wet materials, and heat-shrinking tubing and wiring. Propane torches are primarily used for welding.
Book a 60-minute demo to see
how eziil mrp solution works for you
4. Oxyhydrogen welding
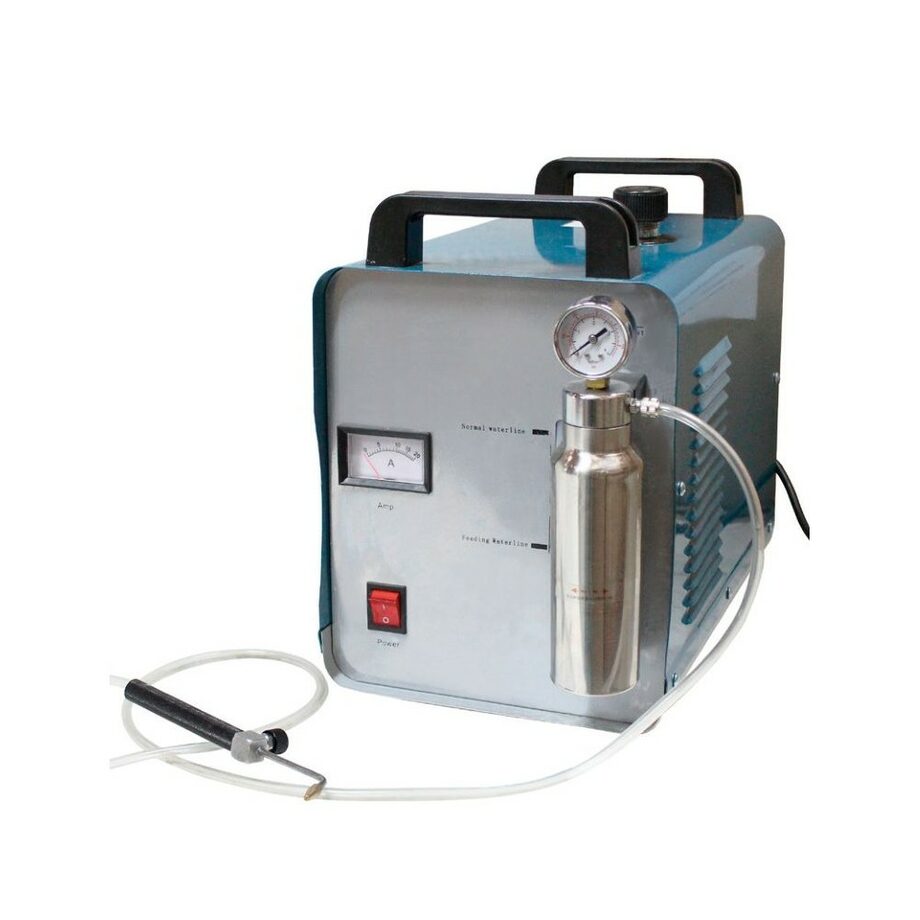
Source: https://forniturasdelarosa.com
Oxyhydrogen welding combines hydrogen with oxygen to generate steam, producing a flame temperature of around 2800 degrees C. However, the weld pool has no protection from the atmosphere when the torch completely provides the combustion oxygen. So, the torch delivers a smaller amount of oxygen, and atmospheric oxygen burns the remaining hydrogen, providing a protective preheating flame to surround the main flame.
Because this protection reduces the flame temperature, oxyhydrogen welding is typically slower. Still, it is a safe and convenient process used mainly to weld thin sheets of steel and alloys with low melting temperatures. No gas cylinder is required, and there is no risk of explosion.
Oxyhydrogen welding entails fuel from water and water vapor left behind, ensuring an environmentally friendly process. Moreover, the welding work is fast, precise, and smooth, with lower energy costs than other welding processes.
5. Oxy-gasoline welding
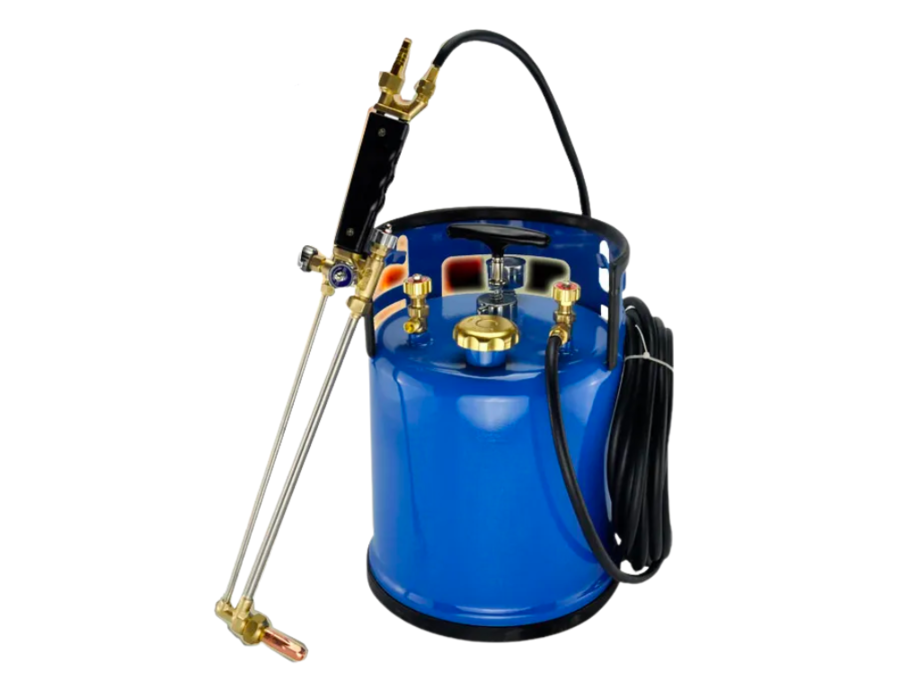
Source: https://www.aliexpress.com
Oxy-gasoline welding supplies a mixture of pressurized gasoline as welding fuel and oxygen to the welding torch.
This mixture works well as a cost-saving method to cut thick steel plates. This gasoline can be pressurized by a hand pump on the cylinder, giving more advantages to this type of welding used in more remote areas or wherever construction costs are an issue.
Advantages and Disadvantages of
Oxyfuel Welding
Even though oxyfuel gas welding is no longer a preferred method of welding, it has many applications in fabricating shops, automobile repairs, and various cutting and joining operations. Following are some of the pros and cons of this well-established way of welding:
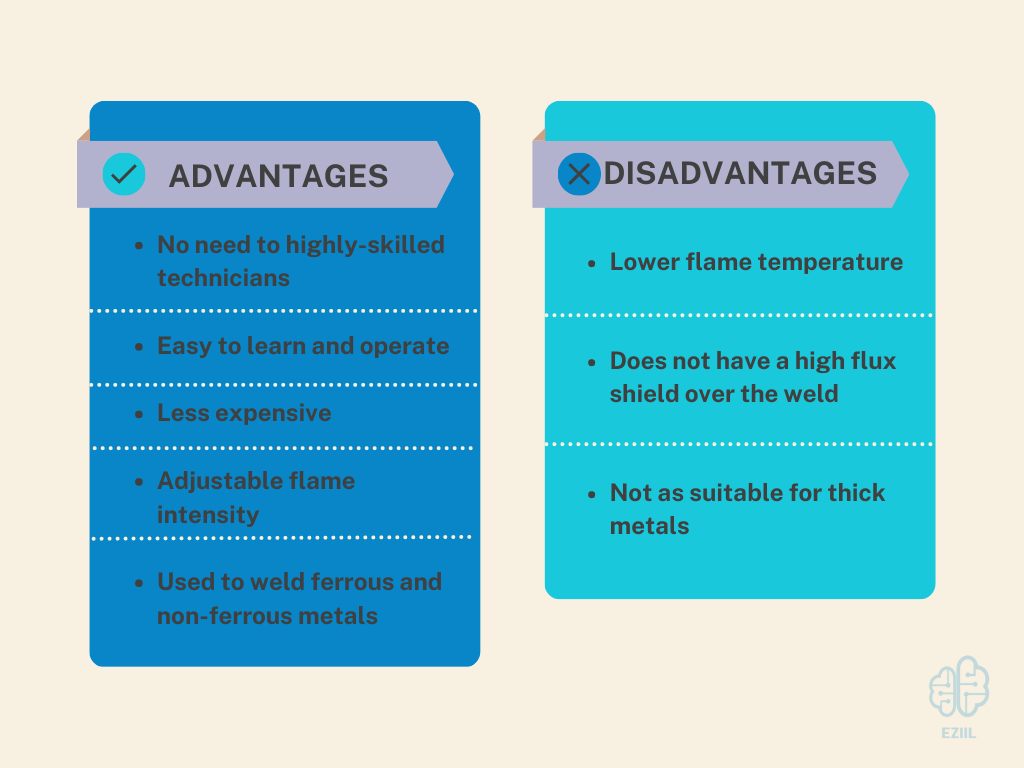
The advantages of oxyfuel welding:
- Relatively easy to learn and operate and
- No need to hire highly-skilled technicians
- Excellent for construction (no bulky, complicated equipment)
- Good for welding and cutting material
- Less expensive
- Used to weld ferrous and non-ferrous metals
- Adjustable flame intensity
The disadvantages of oxyfuel welding:
- Lower flame temperature than arc welding
- Does not have a high flux shield over the weld
- Not as suitable for thick metals
MIG (Gas Metal Arc) Welding:
MIG welding, or Gas Metal Arc welding, is a versatile and widely-used welding technique. It utilizes a consumable wire electrode and a shielding gas, typically argon or a mixture of argon and carbon dioxide, to protect the weld pool from contamination. MIG welding is suitable for various welding materials, including carbon steel, stainless steel, and aluminum. It is often employed in conjunction with other welding techniques such as shielded metal arc welding, flux cored arc welding, and gas tungsten arc welding.
Stick (Shielded Metal Arc) Welding:
Stick welding, also known as shielded metal arc welding, is an electric arc welding process that uses a consumable, flux-coated electrode. This flux coating produces a shielding gas and slag when burned, protecting the weld from atmospheric contamination. Stick welding is widely used for different types of welding projects, including carbon steel and other base metals.
TIG (Gas Tungsten Arc) Welding:
TIG welding, or Gas Tungsten Arc welding, is a precision welding technique that uses a non-consumable tungsten electrode and a shielding gas, often argon, to protect the weld area from contamination. TIG welding is popular for various applications, including welding stainless steel, aluminum, and other alloys. It offers excellent control over the welding process and produces high-quality, clean welds.
Emerging Welding Technologies:
Laser welding, electron beam welding, and plasma arc welding are emerging technologies that offer unique advantages over traditional welding processes. Laser beam welding and electron beam welding use highly concentrated energy sources to create strong, precise welds without the need for filler materials or shielding gas. Plasma arc welding employs a constricted arc to generate a high-velocity jet of ionized gas, enabling deep penetration and high-quality welds.
Which is the Most Commonly Used
GAS welding type?
Gas welding, particularly oxyacetylene welding, is a key technique in the welding industry. Without a doubt, acetylene is the most popular fuel gas used in gas welding. When mixed with oxygen, acetylene generates a flame that can reach temperatures up to 3,200 degrees Celsius, making it ideal for a variety of metal joining tasks. The flame’s temperature in gas welding is adjustable by changing the ratio of oxygen to acetylene, giving the operator precise control over the welding process.
In gas welding, the fumes generated are typically from the base metal, filler metal, and any fluxes used. Fortunately, the levels of these fumes are minimal compared to other welding methods. Moreover, the temperatures achieved during gas welding are generally lower than those in arc welding, making gas welding a preferred method for projects requiring finer temperature adjustments.
Gas welding is not only effective but also versatile. It allows for welding a wide range of materials, from delicate alloys to robust steels, ensuring strong, durable joints. Whether for industrial fabrication or artistic metalwork, mastering gas welding is essential for any skilled welder.
Explore more about Different Types of Welding and Their Uses!