In steel fabrication, production routing is the master-ordered list of operations that a part or assembly must follow, start to finish, before it can ship. It’s the system that tells every work-centre what, in what order, for how long, and with which resources the job should run.
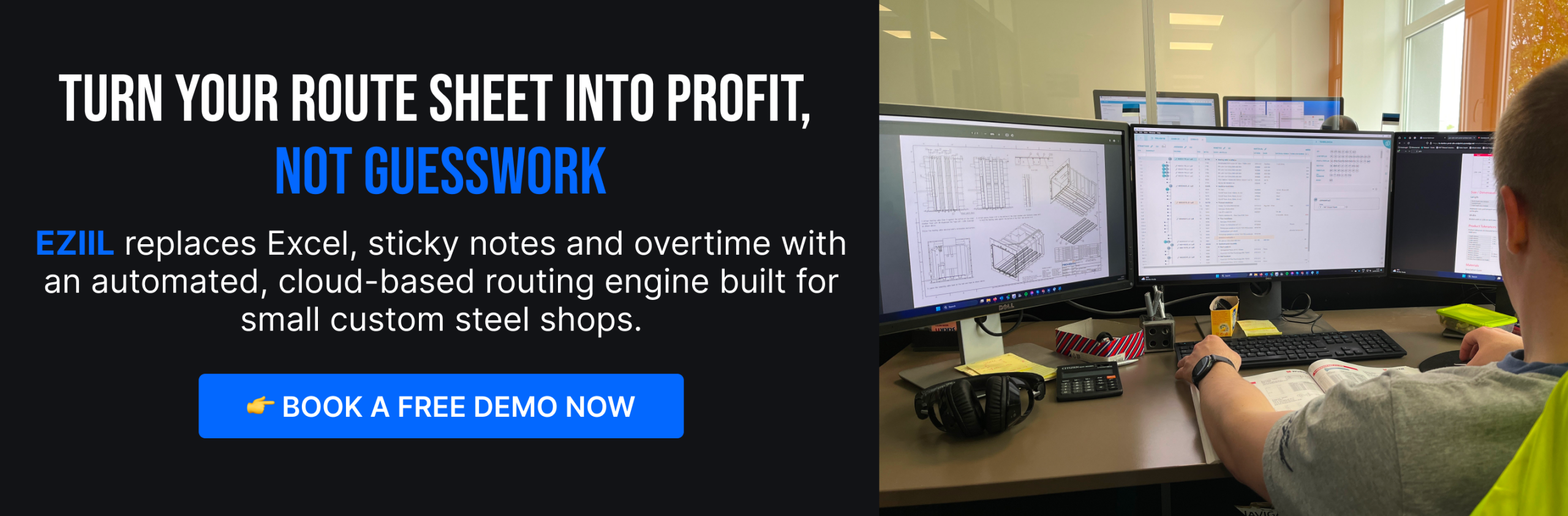
Why production Routing is an Important Activity in Small Custom Steel Fabrication Shops
Unlike high-volume plants that push thousands of identical parts through a fixed line, the typical custom steel shop swaps programs and fixtures constantly. Those frequent changeovers and “one-off” parts make scheduling complex and margins fragile.
In a <50-person job shop, every lost hour is visible on the bottom line. For a small custom steel fabrication shop that lives on thin margins, a single routing mistake can snow-ball into overtime, missed ship dates, and unhappy buyers. That’s exactly why production routing isn’t just a “nice to have” but rather the backbone.
Job routing gives you a playbook everyone, from the production planner to the welder and the accountant, can follow.
For example, when a staircase, steel bridge, mezzanine, or boiler frame moves from blueprint to shipping crate, it passes through dozens of value-adding stops: laser tables, brakes, fit-up benches, weld bays, blast rooms and paint booths. Routing is the formal roadmap that locks those stops into the right order, with the right resources and times, long before production begins.
A production routing sheet documents:
- Work-centers (saw bay, CNC drill, press brake, paint booth, etc.)
- Sequence of operations in the order that makes the most sense for quality and flow
- Setup and cycle times enabling production planners can quote accurately and spot bottlenecks
- Inspection points to catch weld or dimensional issues before they travel downstream
Below is a fabrication process routing example for a single-stringer steel staircase order:
- Plasma-cut stringer and tread blanks
- Mill and drill bolt-holes and notch ends
- Brake-form connection plates
- TIG-weld treads and hand-rail posts to the stringer
- Grind and metal-finish the assembly
- Hot-dip galvanise
- Powder-coat
- Final QA, pack, and ship
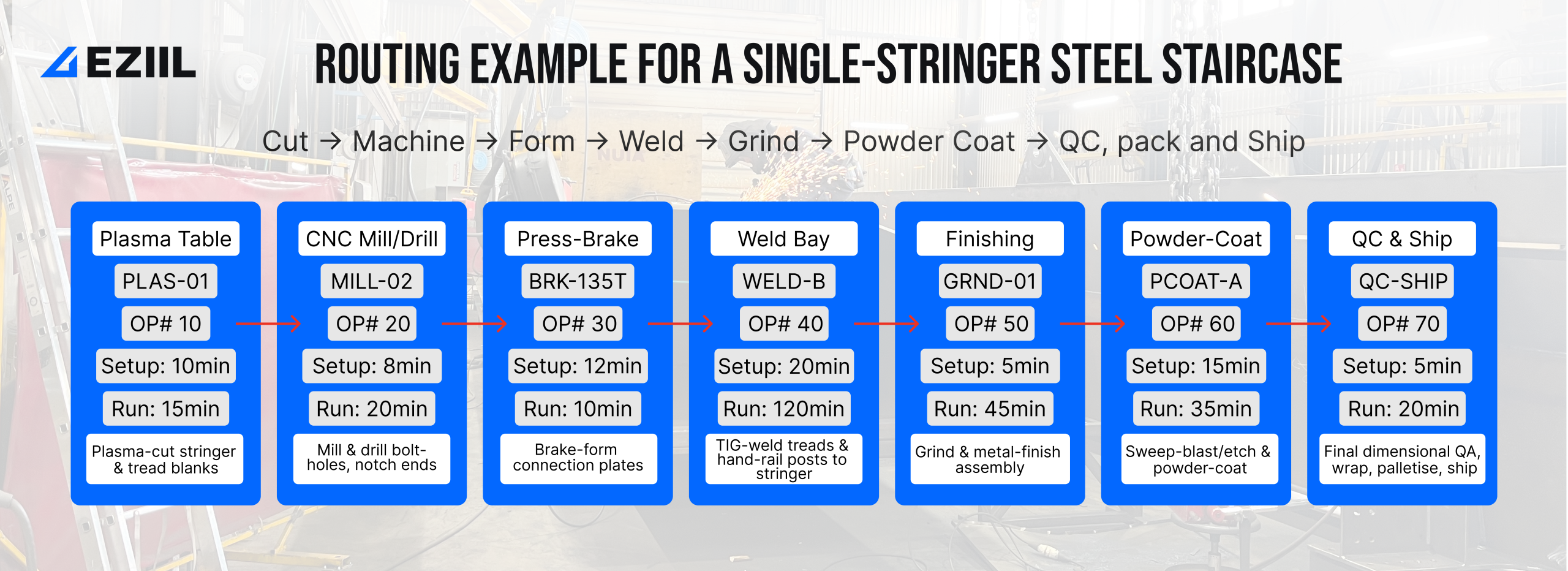
Production Routing vs Production Scheduling
You can look at routing and scheduling as two halves of the same system. Simply put, production routing is the process plan, while production scheduling decides when that plan is executed. A solid routing is a crucial foundation for successful scheduling and capacity planning. So, in practice, you build the routing first, because without knowing the correct path, assigning times is guesswork.
The routing sheet ensures every beam, bracket, and gusset follows the smartest path and the schedule calendar makes sure they hit each workstation exactly when capacity is free. Get both right and you’ll ship faster, quote tighter, and squeeze more revenue out of every hour on the floor.
Production Routing | Production Scheduling | |
---|---|---|
Core question | “Where and how will each step happen?” | “When will each step happen, and with which resources?” |
Focus | Path, sequence, machines, tools, inspections | Timing, start/finish dates, labor and machine assignments |
Time-horizon | Relatively static (changes only when process changes) | Dynamic, short-term (shifts daily as orders and capacity change) |
Outputs | Route sheet or digital routing: operation list, setup and cycle times, QC points | Gantt chart or finite schedule: detailed timetable with due dates and priorities |
Primary owner | Process/manufacturing engineering | Production planning or scheduling team |
Key question answered for a job-shop welder | “Which workstation do I take this beam to next?” | “Is that workstation free at 10am or do I need to slot it in later?” |
How do Production Routing and Production Scheduling Help in Optimizing Production?
As mentioned earlier, routing and scheduling share a common backbone and create a dynamic feedback loop that connect every key metric and activity on the shop floor. Together, routing and scheduling can significantly improve your shop floor performance and effectiveness of a production by allowing for:
- Superior bottleneck detection: Routing tags every op with a machine group and scheduling layers real-time demand on top of that path. This highlights double-booked assets (for example, the single CNC drill everyone fights over) days in advance, letting you split lots or resequence work in time to avoid chaos. Not only can this translate to up to 30% reduction in overtime because conflicts are solved in the plan, not on the floor, but also equals happier and more aligned workforce as each station knows what to do and what’s coming up.
- Accurate capacity and cost calculations: Cycle and setup times captured in the routing feed straight into the scheduler’s finite-capacity engine. This loop gives you realistic promise dates and prevents the over-commit/under-deliver cycle that erodes margin. With clear capacity data, you can confidently accept premium jobs knowing exactly if and when it makes financial sense.
- Fewer changeovers, more green-light hours: The scheduler can cluster jobs that share a routing step, cutting setup time. For example, grouping all parts needing the press brake with the same tooling.
- Synchronized inventory and cash-flow: When routing links parts to operations and scheduling ties those ops to dates, material releases are timed to the minute. That slashes WIP and raw-stock inventory, freeing cash while still keeping the line fed.
- Faster response to disruption: A broken plasma table? Update the routing with an alternate work-center, let the production scheduling software re-optimize timings automatically, and keep the customer date intact. Because the two systems talk, changes propagate instantly instead of living in tribal knowledge.
- Continuous improvement data-loop: The scheduler records actual start/finish times. Comparing these to routed standards shows where cycle times are optimistic or outdated. That feedback keeps both the recipe and the timing realistic, which is an essential Plan-Do-Check-Act (PDCA) loop for lean steel fabrication shops.
How does Routing Fit Together with BOM and Capacity Plan
In a custom steel fabrication shop’s digital backbone, the bill of materials (BOM), the fabrication process routing, and the capacity plan function like ingredients, recipe, and seating chart at dinner service.
The BOM itemises every length of tube, plate, bolt, and consumable required for a job, while the routing sets out the exact sequence of operations, machines, and standard times needed to transform those materials into a finished assembly. Each element answers a different question: what you need versus how you’ll make it. Yet neither can drive the business alone.
The capacity plan (your overview of machine and labour load) draws directly from those two datasets. Cycle and setup times stored in the routing translate into hours against each workstation group and the quantities in the BOM tell the production planner how many cycles to expect. Because routing is the source for capacity planning, the system can now forecast when a drill line will hit 120% load next month and warn you to add a shift or subcontract.
For a small custom steel shop, this eliminates guesswork: materials are ordered only when the BOM says they will be consumed, machines are booked exactly for the hours the routing demands, and the capacity plan exposes bottlenecks before they hijack your promise dates. Routing, BOM, and capacity plan are therefore not separate documents but interlocking gears that keep the entire production system turning in unison.
Routing Best-Practices for Small Fabrication Shops
For a high-mix, low-volume steel shop, the routing sheet is the production playbook: if it’s clean, everyone from the saw bay to accounting works from the same script, if it’s cluttered or out-of-date, lead times and margins unravel. The following best practises will help you keeping that playbook top notch:
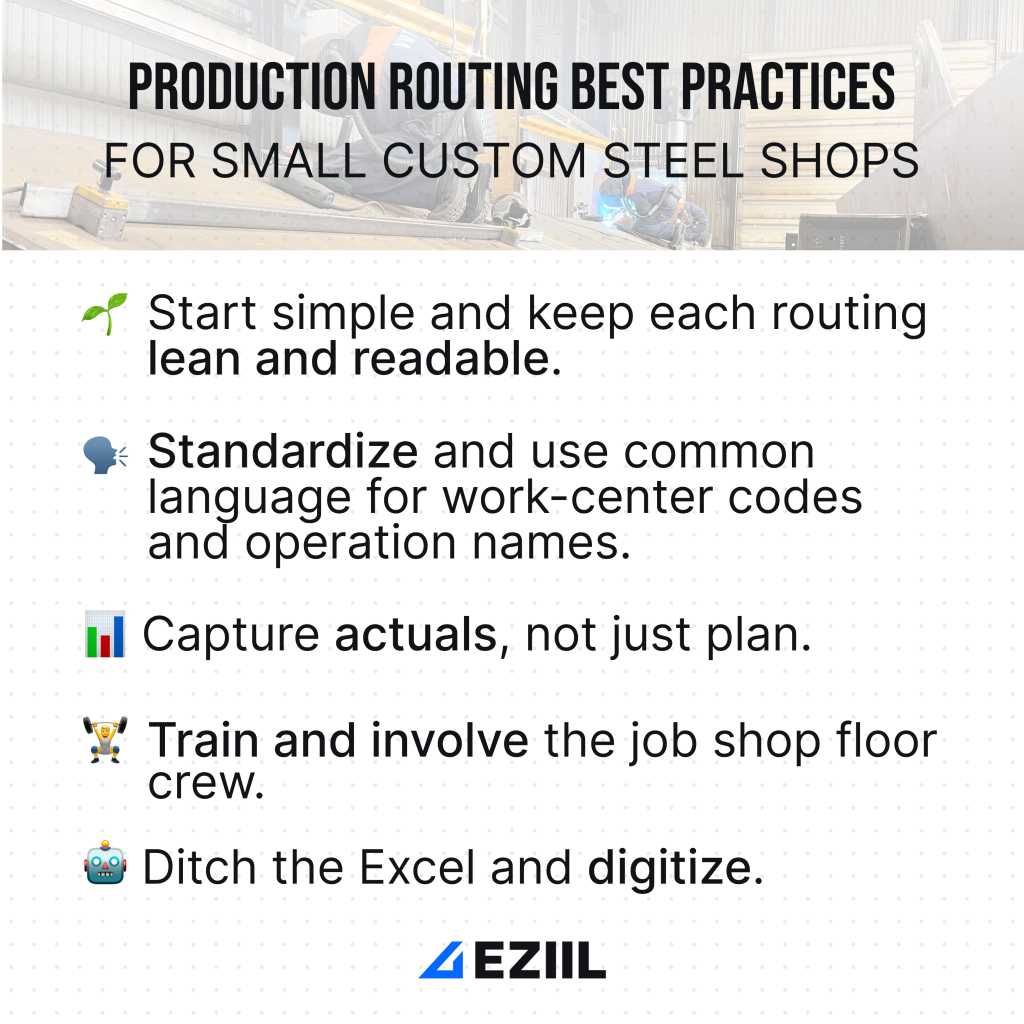
- Start simple and keep each routing lean and readable. A good route sheet spells out only what the operator truly needs: operation name, work-centre, setup time, cycle time, and critical inspections. Overloading the document slows everybody down, whereas concise language and the occasional flow-chart make it instantly digestible for new hires and veterans alike. ☝️ Start by documenting the top 10 repeat operations. You’ll capture 80% of shop time with minimal admin overhead.
- Standardize and use common language for work-center codes and operation names. Group similar machines under consistent labels (for example, “BRK-02” for press-breaks). This lets production planners copy operations between jobs, compare loads across shifts, and surface bottlenecks at a glance. Using common language means codes are understood the same across different departments.
- Capture actuals, not just plan. When real-world set-up and cycle times feed back into the routing, future quoting and scheduling becomes more accurate and you can easily spot tasks that routinely over-run your planned time.
- Train and involve the job shop floor crew. Operators who understand why routing exists are quicker to flag mistakes and suggest better sequences, turning continuous improvement from a buzzword into daily practice.
- Ditch the Excel and digitize. If you’re still using Excel or other disconnected tools for routing, it might be a good time to consider moving to a cloud-based steel fabrication production management tool. Housing your routings digitally links each operation to material availability, capacity calendars and dispatch lists. Cloud tools push live tasks to tablets, so the floor always sees the latest revision and production planners see progress in real time.
How does EZIIL automate routing for custom steel shops
Many small custom-metal shops still rely on paper or Excel for routing. The result is tribal knowledge, late jobs, and heavy impact on margins whenever the schedule changes. EZIIL replaces that patchwork with a cloud-native routing engine: you start from pre-built fabrication templates, drag operations into the right order, and lock in setup and cycle times that automatically feed BOM cost and capacity calendars.
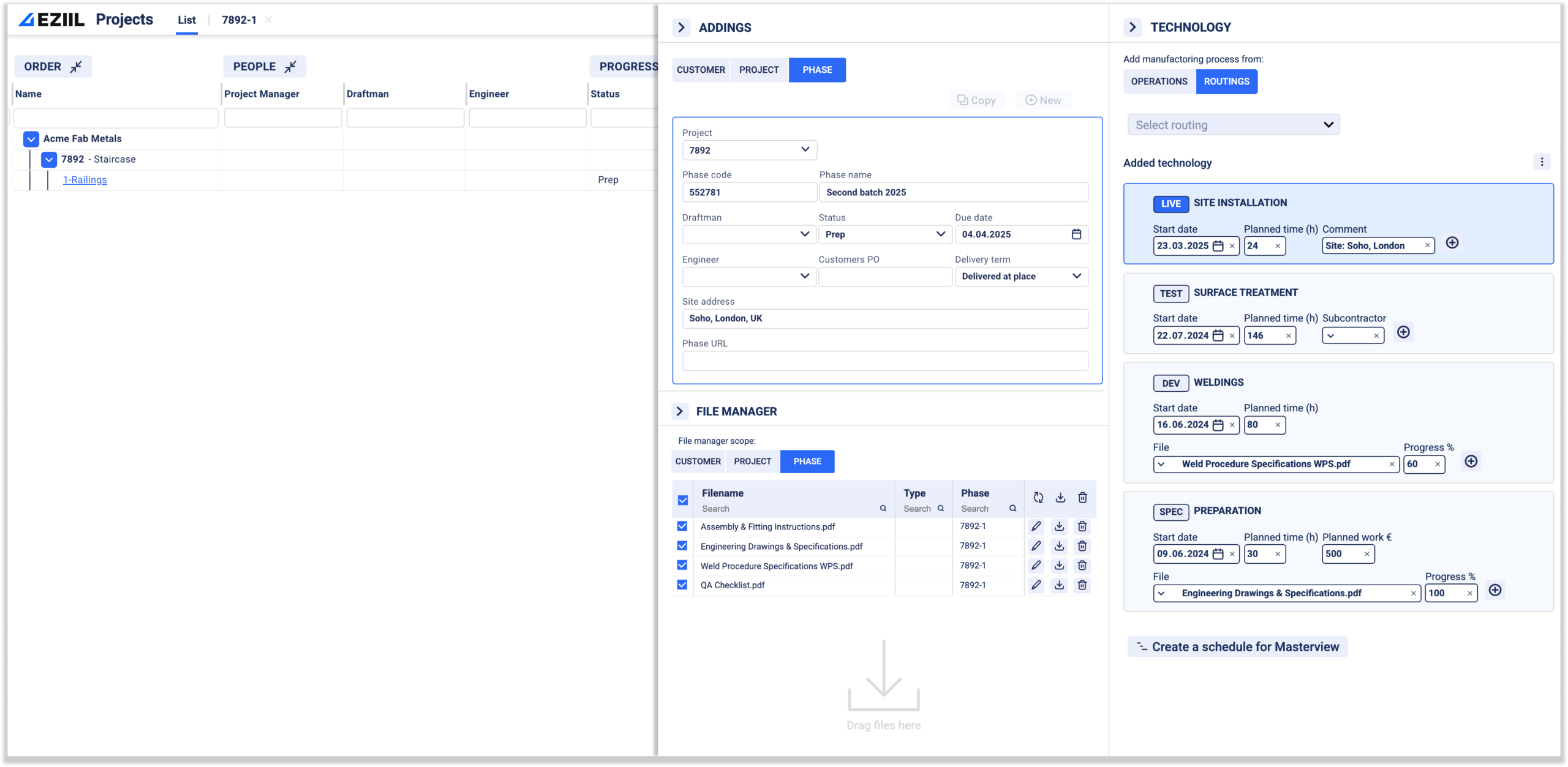
Because those routings live in the same database as the production scheduling and planning, every step instantly becomes a digital work order on the shop-floor app. Operators see drawings, QC images and live task queues on their phones, while production planners watch project progress, capacity heat-maps and bottleneck alerts update in real time.
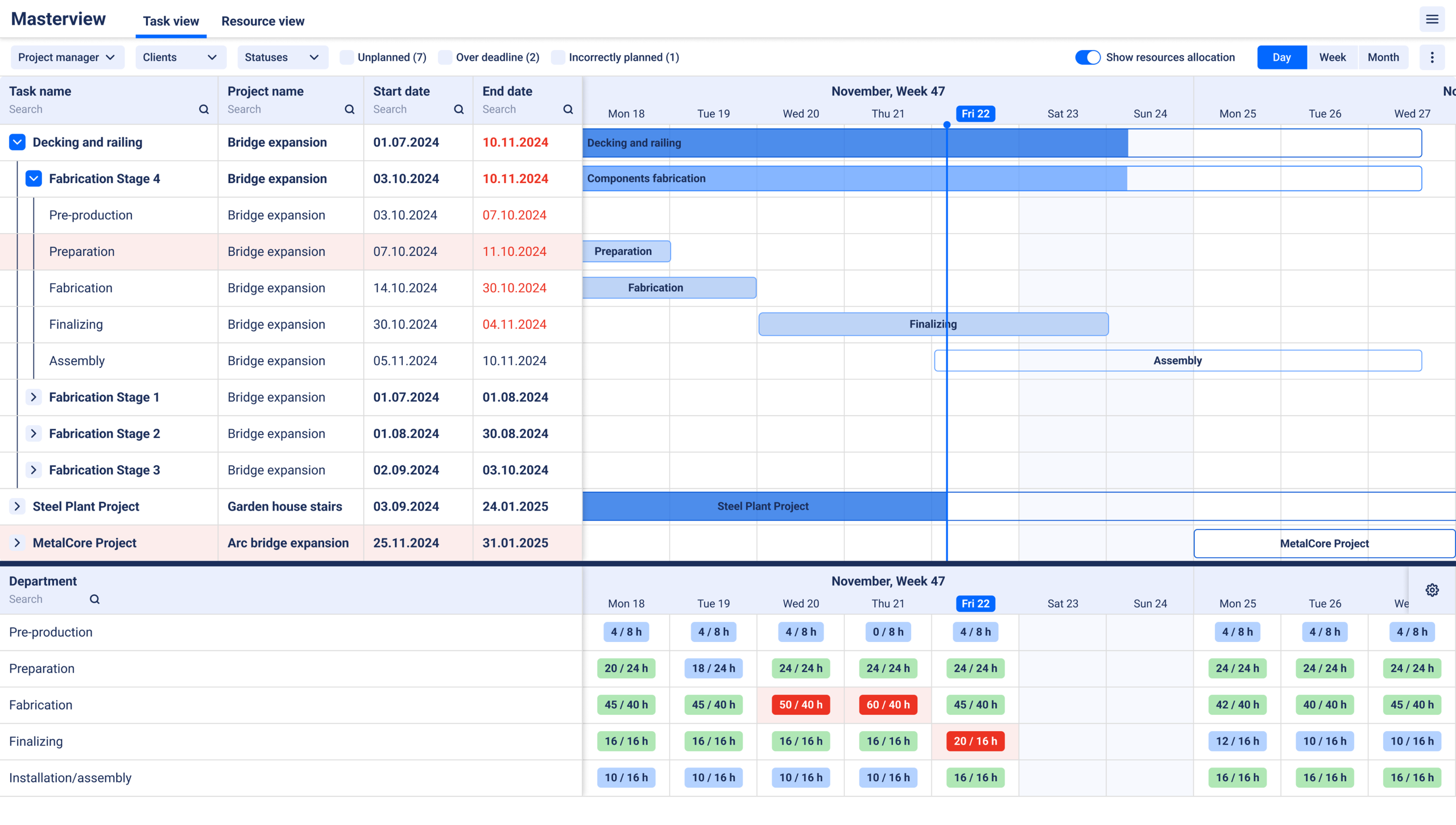
The impact is measurable: on average, swapping paper travelers for digital work orders trims make-to-order lead times by about 20% and eliminates hours spent hunting for parts or status updates.
EZIIL’s routing feature also encourages smarter resource use, resulting in lower waste, faster throughput, and tighter quality control, and rolls actual labour and material consumption straight into margin dashboards, so finance can see where each project makes or loses money.
All of this lands without the overhead of a full-blown ERP system: EZIIL is subscription-based, deploys in weeks, and was built for small custom steel fabrication shops migrating off disconnected spreadsheets, giving small fabricators an affordable path to the same digital solution the big players enjoy.
A well-built routing is a system that keeps cutting, welding, and painting firing in tune. Shops that move from tribal knowledge to EZIIL routinely see significant improvements in:
- on-time delivery
- reduction in WIP queues
- gross-margin (you can calculate your EZIIL ROI here)
- team alignment
Real-World Example of Why Routing Matters to Custom Steel Shops
We recently had a new customer, who back then used Excel as their metal project planning, scheduling and management, tell us a horror story about a staircase project they had been working on. Materials were on the floor, welders scheduled, paint booth free. Yet the truck didn’t leave on time and the shop lost a significant amount of money in weekend overtime, rush freight, and a bruised on-time-delivery score.
What went wrong?
There was no proper fabrication process routing.
- Cutting nested plates finished on time, but the parts sat in a cart because nobody had reserved the press-brake cell.
- The welding team picked up the job a day late, only to discover that the landing stringers needed extra bevel prep the router never flagged.
- By the time pieces reached the paint line, the booth had already switched colours.
In other words, the job lacked the DNA sequence that tells every work-centre “what’s next”. Without a routing sheet that links each operation to its sequence code, standard hours, and the right Bill of Materials (BOM) revision, the shop relied on memory and sticky notes. The cost?
Hidden cost | $ | How routing would have prevented it |
---|---|---|
Press-brake idle (6h) | 1,080 | Reserved capacity and start date calculated from the routing. |
Emergency weld prep (2h) | 360 | Operation step would have included bevel spec and fixture. |
Paint booth colour change (4h) | 720 | Routing would group like-colour jobs and freeze sequence. |
Premium freight | 1,350 | On-time release to shipping via finished-goods step. |
Total avoidable loss | $3,510 |
Multiply that by even one staircase a month and you’re leaking $42,000 a year.
How EZIIL fixed the problem
Problem | How EZIIL solved it | Outcome |
---|---|---|
No standard routing in production, ops depended on tribal knowledge | EZIIL pulls the BOM, auto-fills the routing sequence: laser → press-brake → MIG weld → paint | Every job leaves engineering with a living, digital route sheet |
Idle machines/overtime firefighting | EZIIL’s MasterView semi-automatic scheduler drops each op on the right work-centre calendar, respecting resource limits and other jobs | Smooth project flow and zero surprise queues or idle presses |
No work-in-progress visibility | EZIIL Mobile Reporting on phones and tablets allows welders to log Start/Finish and progress rolls automatically back into MasterView | Real-time WIP status for production and PM teams |
Hidden cost overruns | EZIIL’s Planned vs Reality reports compare routed hours to actual, flagging overruns early | Users can tweak standard times and tighten future quotes more accurately |
FAQ
What is production routing in steel fabrication?
Production routing is the ordered list of operations: cutting, forming, welding, finishing, etc. that a steel part or assembly must follow before it ships. It specifies the work-centre, sequence code, setup time and run time for every step so planners, operators and schedulers all work from the same playbook.
What’s the difference between production routing and production scheduling?
Routing defines what happens and in what order; scheduling decides when each routed operation will run and which resources will perform it, based on current capacity. In short, routing is the recipe, scheduling is the calendar.
Why is production routing important for small custom steel shops?
With limited machines and people, a single routing error can snowball into idle presses, last-minute colour changes, missed ship dates and overtime. A clean routing sheet keeps every cut–weld–paint step in sync, protects margin and improves on-time delivery.
What does a routing sheet include?
A routing sheet lists operation descriptions, sequence codes, work-centre codes, setup time, run time, required tooling or fixtures and any in-process quality checkpoints.
How do setup time and run time differ in a routing sheet?
Setup time is the one-off preparation (for example clamping a stair stringer in a jig). Run time is the repeatable cycle time needed to process each unit once setup is complete. Separating the two prevents under-quoting small batches.
How does production routing connect to the Bill of Materials (BOM)?
Each line in the BOM spawns its first routing operation (laser-cut, saw, plasma, etc.). When the BOM changes, an integrated system propagates the update into the routing so capacity plans and purchase orders stay accurate.
Can production routing be automated?
Yes. Tools like EZIIL import the BOM, auto-generate the full routing sequence, complete with standard times and QA gates, and push live work orders to tablets on the shop floor.
What benefits can a shop expect after automating its routing?
Typical gains include double-digit improvements in on-time delivery, 15-30% lower WIP queues, and a 3-5% lift in gross margin thanks to fewer surprises and more accurate quoting.
How to Create a Production Routing for a Custom Steel Fabrication Job
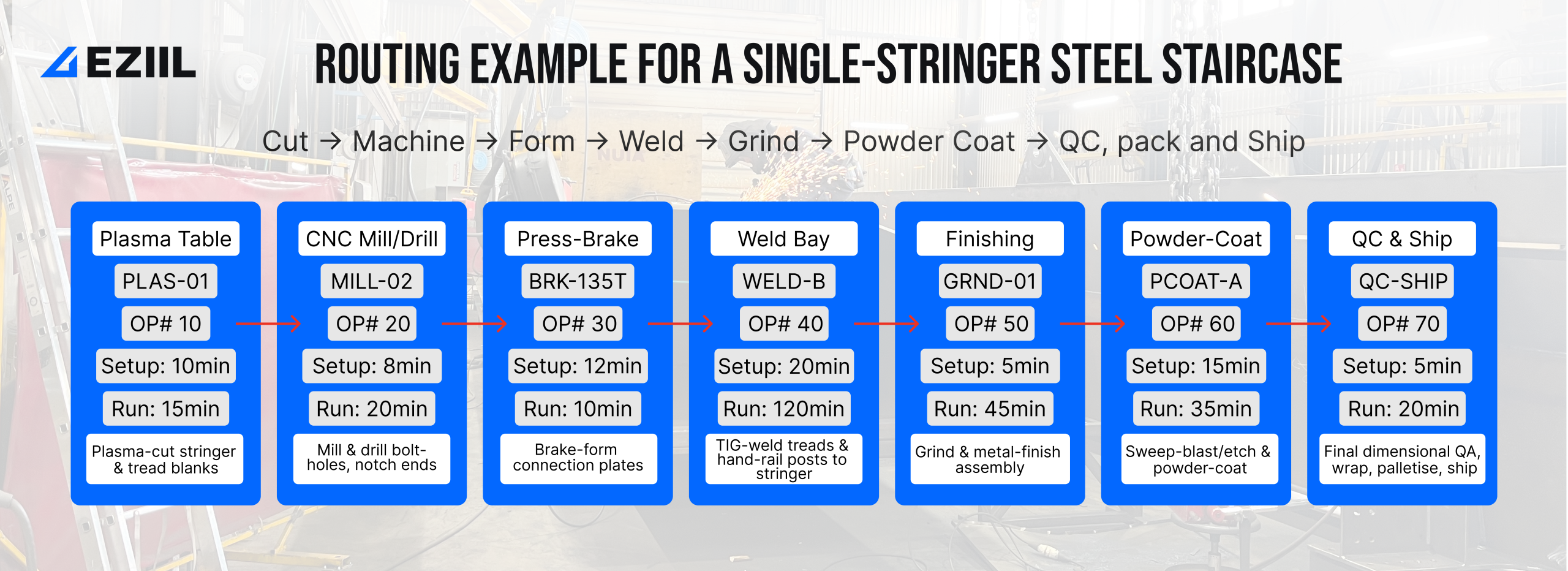
Step-by-step process for building a production routing sheet that keeps cutting, welding and painting in sync in a small custom steel shop.
Total Time: 2 hours
Start from an accurate BOM
Import or create the Bill of Materials so every part has a revision-controlled record.
List each manufacturing operation
Write down every value-adding step—laser cut, drill, press-brake form, TIG weld, grind, galvanize, powder-coat, final QA.
Assign sequence codes
Give each operation a numeric or alphanumeric sequence (10, 20, 30…) to lock the order and leave space for late inserts.
Link operations to work-centres
Specify the machine or cell code for every step—for example LAS-01, BRK-135T, WELD-B.
Enter setup and run times
Add engineered setup minutes and per-part run minutes; if you lack data, start with time studies or historical tickets.
Embed QA checkpoints
Insert in-process inspections such as bend-angle verification or blast profile checks to prevent rework downstream.
Feed routing into the capacity plan
Push the times into your scheduler to detect overloads; adjust sequence or resource allocation as needed.
Publish & capture shop-floor feedback
Release the routing as a digital work order, collect actual times from operators and refine the standards for the next job.
Tools:
- Bill of Materials (BOM)
- Routing template or MES software (e.g., EZIIL)
- Work-centre list with capacities