Regarding manufacturing, SKU logic is a key part of the process. But what is SKU logic, and how can you build it into your business? In this post, we’ll explain everything you need to know about SKU logic and show you some of the best SKU generators to create your SKUs. Read on to learn more!
What is SKU, and what it’s used for?
An SKU (stock keeping unit) is a unique identifier for a product or service. It helps businesses keep track of inventory, including raw material, work-in-progress (WIP) and finished goods inventory. SKUs can be assigned to products manually or generated automatically using an SKU generator. SKUs are alphanumeric codes, meaning they typically contain both letters and numbers.
Excel is a popular and straightforward tool for SKU creation, as it offers a variety of SKU templates that can be customized to fit the needs of any business.
Uses
SKUs work as a product identifier, but they can help any business to manage their inventory and ensure efficient operations. Some of the most common uses of an SKU are listed below:
- To keep track of inventory levels
- To generate sales reports
- To create purchase orders
- To track customer order
- To monitor inventory movements
Now that we’ve answered the question “what is SKU?” it’s time to dive into how you can create your own SKUs for your products.
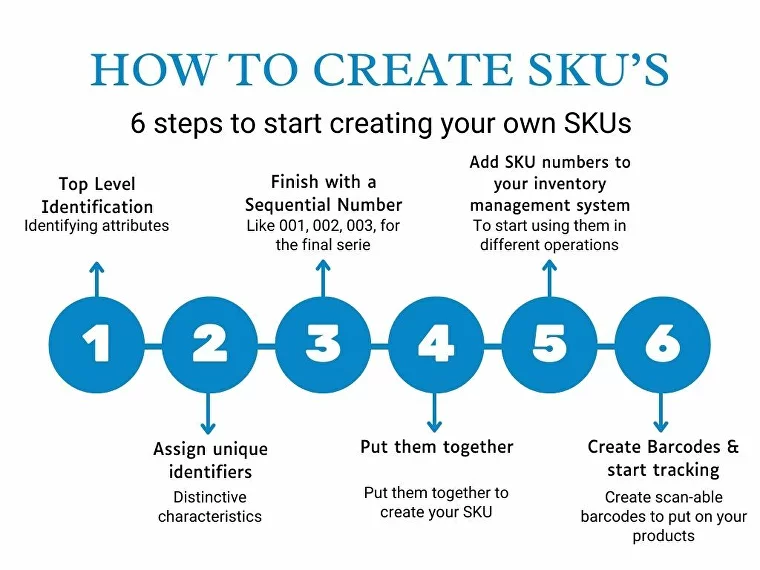
How do you create SKU’s and what are the different methods of creating them?
It is important to create simple, but efficient SKU code system that aligns with your business operations. Follow these steps to start creating your own SKUs.
Step 1: Top Level Identification
The first step is identifying which attributes will be used to create the SKU. For example, if you are a material supplier, you might use material type, grade, and size as your attributes. The first 2 or 3 alphabets/digits of an SKU could be used to identify the category, department, supplier, or even manufacturer.
Step 2: Assign unique identifiers
Use the middle section of your SKU numbers to give your products distinctive characteristics, such as item type, or subcategory—whatever makes sense for how you’ve arranged the material you offer. For instance, you might assign “A” for grade-1, “B” for grade-2, “C” for grade-3, etc.
Step 3: Finish with a Sequential Number
Setting up an SKU number is simple when you use sequential numbering, like 001, 002, or 003, for the final series. This method also makes it easier to distinguish between older and newer products in a product line. In rare circumstances, it can also be beneficial to link the final series of an SKU number to a supplier product number. Use whatever makes sense logically for the products you sell once more.
Step 4: Put them together
Once you have assigned codes to all of your attributes, you can put them together to create your SKU. So, if you are dealing in aluminum grade 2040, the SKU might be “AG2”. If you have aluminum grade 6061, the SKU would be “AG6”.
Step 5: Add SKU numbers to your inventory management system
It is possible to manually establish SKUs and maintain inventory using notebooks or spreadsheets, you must enter the new SKUs into your inventory management system in order to generate sales reports, purchase orders, and other documents. You can also trace product data as like:
- Product name
- Category
- Price
- Description
- Type
- SKU number
- Any other distinguishable aspect
Step 6: Create Barcodes & start tracking
The final step is to create scan-able barcodes to put on your products. Scannable barcodes can make warehouse operations faster and more efficient. You can create barcodes using various online tools or purchase them from a third-party provider.
Once you have your barcodes, you can attach them to your products and start tracking inventory levels.
Methods of creating an SKU
One of the key elements in inventory management is to create and track SKUs. But you must be thinking, what are the methods of creating an SKU? When you first use the ERP system, the ERP automatically creates SKU codes in accordance with the entered rules. There are several methods of creating an SKU, but some of the most common are discussed below. Let’s take a closer look at all of them.
Excel
One popular method is to use an Excel spreadsheet. This method is fairly straightforward – create a column for each piece of information that you want to include in your SKU (product name, color, size, etc.), and then use a formula to generate a unique code for each row. The key benefits of using excel as SKU generator include:
- Simple stock management and product SKU tracking
- Choose the goods with the highest profit margins.
- By employing the same brand references, keep your staff on the same page.
Book a 60-minute demo to see
how eziil mrp solution works for you
Dedicated SKU generators
Another popular method is to use a dedicated SKU generator tool. These tools usually have a more user-friendly interface than Excel, and they often come with additional features such as the ability to check for duplicate codes or export your codes in bulk.
Free SKU generators
There are also some online SKU generators that can be used for free. These generators usually have more limited features than paid tools, but they can still be effective for simple projects.
5 best free SKU generators on the market
When managing inventory, every detail matters. That’s why having a system for generating SKUs is essential for any business that wants to keep track of its products. And luckily, there are plenty of options on the market. To help you find the right solution for your business, we’ve compiled a list of the five best free SKU generators.
1. SkuGen
SkuGen is a versatile SKU creator that offers a wide range of features and customization options. With SkuGen, you can create SKUs for any product, including physical goods, digital products, and services. And if you need to make changes to your SKUs, you can do so with just a few clicks.
Salient features:
- SKUs are created for the products in a collection and set of products selected on the admin products page
- To create SKUs, you can combine components like the prefix, the product title abbreviation (PTA), the product options abbreviation (POA), the product type abbreviation (PTA), and the product vendor abbreviation (PVA)
- Product selections, product groups, and product vendor abbreviations can all be enabled using code types.
- SKUs are created for products directly in your store, all at once and saved across the QR field.
Benefits
- The tool can produce SKUs seamlessly, easily, and quickly when you construct a new product or edit an existing one.
- You may trust that the SKUs will be generated in accordance with established guidelines because the app is quite consistent.
- The tool generates special SKUs and customized codes and even allows you to print product labels.
2. MageCloud SKU Auto Generator
MageCloud SKU Auto Generator is a powerful tool that can help you automatically generate SKUs for your products. With this tool, you can create SKUs for both physical and digital products.
Salient features:
- The app offers 3 types of auto-generation: by product attributes, by categories, and by-product types
- You can create SKUs for both physical and digital products
- The app can generate SKUs for multiple products at once
- Establish specific SKU guidelines for various Product Types and Categories
- Automated SKU enable/disable
- Allows you to specify the SKU string’s minimum length.
Benefits:
- Effortlessly and easily integrates with Magento
- Use codes to generate SKU tags for your items.
- You have control over the system and can specify a wide range of different rules.
3. Gorgias SKU number generator
It is a simple but effective tool that can help you automatically generate SKU codes for your products. The website’s design is uncomplicated and user-friendly for everyone. Your email is required to set you up, and after that, you are ready to go.
Salient features:
- Trim any code fragments with inappropriate details.
- You can create SKUs for multiple products at once
- Allows you to specify the SKU string’s minimum length
- Allows for the creation of unique codes instead of instantiating
- Minimize the use of gaps and special characters
Benefits:
- Assist with replacements and vendor details as appropriate
- It includes a storage area for large catalogs.
- Set algorithms that make SKUs easy to comprehend
4. Logiwa
Logiwa is a cloud fulfillment platform that offers an internal SKU generation tool, as well as a manual SKU generation template.
Salient features:
- Users can opt to have the software create product SKUs automatically
- User-friendly interface
- Simple system for creating SKUs
- Provides guidelines for beginners
Benefits:
- The platform offers superior scalability and will support and back your expanding range of items and new versions.
- Simple and entirely rule-based naming helps avoid any specified process mix-ups.
- Regular output
- It keeps a pattern going across all SKUs
- Simple to use
5. WooCommerce SKU creator
WooCommerce SKU creator is a Word Press plugin that allows you to generate SKUs for your online products. The plugin is free to download and install. Once you have installed the plugin, you can start creating SKUs for your products.
Salient features:
- Create SKUs for various product versions automatically whenever a product is upgraded or activated through publishing
- Utilize the variation ID or attribute slugs to create variant SKUs
- Utilize bulk product updates to force the development of SKUs for several products with ease
- Available to bulk-generate SKUs for products created before this specific plugin was installed
Benefits
- Checks if all versions of items have automatically created SKUs
- Identifies if all items, or just simple products, require automatic SKU assignment
- Creates SKUs for all product classes and varieties
Frequently Asked Questions – FAQ Guide
Why not just use the barcode (GTINs)?
There are a few reasons why using SKUs can be preferable:
- Your barcodes could be too general for managing inventory; for instance, a barcode might apply to numerous product colors, which will make it harder for your team to ensure the proper item to the customer.
- If you redistribute other people’s goods, the barcodes may often change, which could toss off the order of your lists.
- Supports the encoding of only numeric data.
What product details should be included in the SKU?
The SKU should be made up of information that will help you quickly and easily identify the product. This can include product name or code, color, size, style, material, manufacturer or brand, country of origin, and model number. Usually, an SKU number includes 3-5 features of the product.
Does the SKU have to be unique?
Yes, each SKU should be unique to a single product. This will help to avoid confusion and mix-ups when ordering and stocking inventory.
What is the minimum length for a SKU?
There is no minimum length for a SKU, but it is generally recommended to keep them as short as possible while still including all the necessary information.
Summary
In wrapping up, the indispensable role of effective inventory management in the field of product design and mechanical engineering, particularly in the laser and plasma cutting industries, cannot be overstated. Key to this process is the use of an SKU generator, a tool that creates unique identifiers, or SKUs, for each product in your inventory.
An SKU generator is a significant boon to inventory management. It provides each item with a unique identifier, comprised of letters, numbers, and special characters, which serves as a linchpin for efficient inventory tracking. A SKU, different from the Universal Product Code (UPC) that is standardized across multiple stores, is unique to a specific business and encapsulates valuable information about the product. In this context, an SKU generator comes into play sevenfold or even more, given the complexity and diversity of products in the laser and plasma cutting industries.
The use of an SKU generator enhances inventory management by allowing for precise tracking and identification of products, from raw materials to finished goods. It simplifies the process of inventory management, ensuring that every item, regardless of its unique properties or characteristics, has a unique identifier that can be easily tracked.
In addition, the SKU generator’s seamless integration with other inventory management systems amplifies its benefits. With the unique identifiers it generates, inventory tracking software can accurately monitor stock levels, track product movement, and even project future demand. Such integrated functionality significantly boosts operational efficiency and minimizes the risks associated with overstocking or understocking.
Moreover, the SKU generator goes beyond providing a mere tracking number. It creates SKUs that encapsulate detailed product information, offering a depth of insight that is invaluable in managing inventory. This can include specifics related to the product’s features or the cutting process used, providing a level of granularity that is particularly beneficial in the laser and plasma cutting industries.
In conclusion, the SKU generator stands as an integral tool in the realm of inventory management, particularly in precision-dependent industries like laser and plasma cutting. It fosters efficiency, precision, and integration, making it an essential asset for businesses seeking to optimize their inventory tracking and management processes. The unique identifiers it generates serve not only as tracking mechanisms but as encapsulations of product information, bridging the gap between inventory control and product knowledge. As such, the SKU generator represents a major stride forward in inventory management, setting the stage for more streamlined, efficient, and effective operations.
We hope that this article has helped you understand SKU’s a little better, given you some tips on how to create them, and shown you some of the best free SKU generators on the market. Eziil is a modern MRP system designed for the metal industry. It also assists as an SKU generator to control and manage the inventory level in your industry. You can also book a 60 minutes free demo to check how Eziil MRP system works. If you have any questions or would like more information, please feel free to reach out to us. Thanks for reading!