It is no secret that structural steel fabrication requires many steps to create the finished product. However, many fabricators may not know all the steps involved or the proper order to complete them.
So, let’s get started!
This blog post will outline the main stages of a structural steel fabrication process and explain their importance. We will also discuss some key points to consider during the fabrication process.
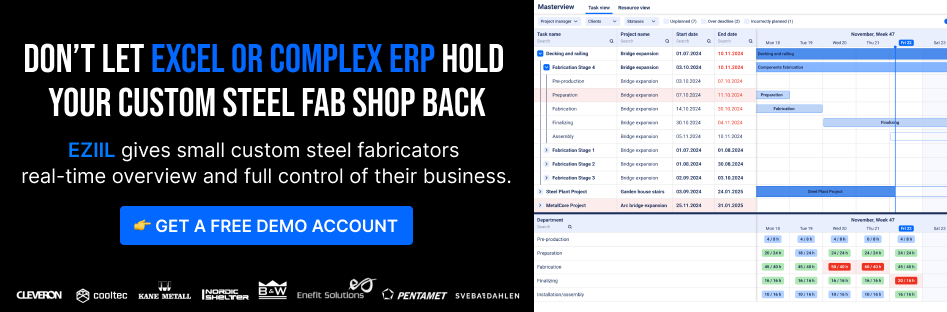
What is Structural Steel Fabrication?
Structural steel fabrication is the process of constructing or reconstructing metal structures with steel. This fabrication process basically consists of cutting, bending, and assembling the fabricated steel. This can be done for various purposes, including building bridges, housing, factories, and other large structures.
There are many reasons why structural steel is the material of choice for industrial construction. Steel is incredibly strong, highly resistant to heat, easy to fabricate, and extremely durable, making it an ideal choice for factories and warehouses.
Main Steps of Structural Steel Fabrication Process
Now that we have a basic understanding of structural steel fabrication let’s look at the main steps involved in the process.
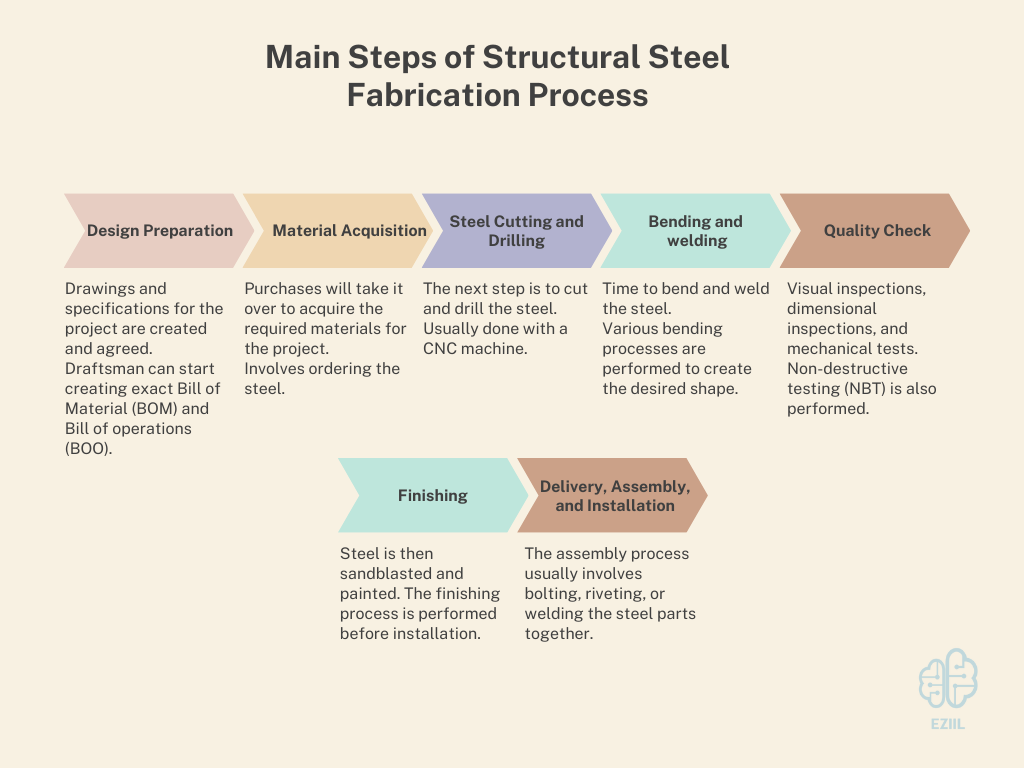
1. Design Preparation:
The first step in any structural steel fabrication process is design preparation. This is where the drawings and specifications for the project are created and agreed. Once the design is complete, the draftsman can start creating the exact Bill of Material (BOM) and Bill of Operations (BOO) to prepare the information needed for purchase and production.
2. Material Acquisition:
When the draftman finishes the detailed BOM then purchases will take it over to acquire the required materials for the project. This usually involves ordering the steel from a supplier. Steel can be in standard length or already cut into length based on the order. The steel will then be delivered to the fabrication site.
3. Steel Cutting and Drilling:
The next step is to cut and drill the steel. This is usually done with a CNC machine. The steel is first cut to the correct length and then drilled to create the holes needed for the project. Steel cutting can be performed by circular saw machines, laser cutting machines, waterjet machines, or plasma cutting machines.
4. Bending and welding:
Once the steel is cut and drilled, it is time to bend and weld it. Various bending processes such as section bending, roll bending, plate bending, and tube bending are performed to create the desired shape. The steel is then welded together using either MMA welding or MAG welding. The welding can be performed by hand or with a machine. Welding must be performed under strict quality management conditions as per BS EN ISO 3834, under the supervision of a welding coordinator.
5. Quality Check:
The quality check ensures that the steel meets all the required specifications. It includes visual inspections, dimensional inspections, and mechanical tests. Non-destructive testing (NBT) is also performed to ensure that the welded parts are free from hidden defects and cracks.
6. Finishing:
After the quality check is complete, the steel is then sandblasted and painted. This is done to protect the steel from corrosion. The finishing process is performed before installation to reduce the installation time and cost.
7. Delivery, Assembly, and Installation:
In the final step, the steel is delivered to the site and assembled as per the required design. The assembly process usually involves bolting, riveting, or welding the steel parts together. The fabricated steel parts must be handled carefully to avoid any damage. Installation can be performed by using heavy-duty cranes. BCSA (The British Constructional Steelwork Association) has published several guides on structural steelwork installation and safety measures.
The steel structural fabrication process can be completed by following all these steps.
Key Points to Consider during the Structural Steel Fabrication Process
Structural steel fabrication requires a high degree of skill and precision, as even a tiny error can jeopardize the structure’s safety. As our world becomes increasingly industrialized, the demand for fabricated steel structures will continue to grow. Here are some key points to consider during the structure steel fabrication process:
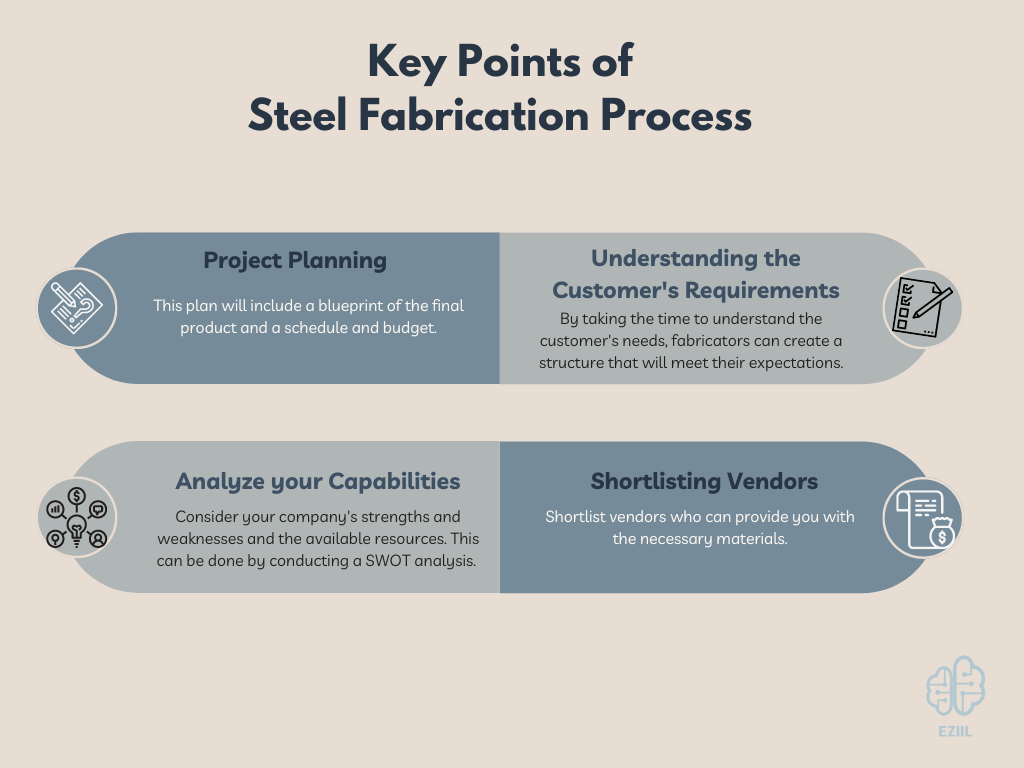
Project Planning
The first thing to consider in any fabrication project is to create a detailed plan. This plan will include a blueprint of the final product and a schedule and budget. Completing a project on time and within budget would be impossible without a well-designed plan. In addition, the plan helps to ensure that all aspects of the fabrication process are considered. For example, the plans for a bridge will take into consideration the weight and type of traffic that will be using the structure.
Understanding the Customer’s Requirements
In order to meet the customer’s expectations, it is essential to understand their requirements. This includes understanding the purpose of the structure, as well as the load-bearing capacity and environmental conditions. By taking the time to understand the customer’s needs, fabricators can create a structure that will meet their expectations. Efficient communication and a professional team are essential to ensure customer needs are met.
To avoid any inconvenience, it’s better to share your developed design with the customer for approval. Also, get their feedback during each stage of the manufacturing process to ensure your customer satisfaction.
Analyze your Capabilities
One of the most important key points to consider during your steel structure manufacturing project is to analyze your company’s capabilities. You should consider your company’s strengths and weaknesses and the available resources. This can be done by conducting a SWOT analysis. Here are some of the critical factors that you should consider while analyzing your company’s capabilities:
- Does your company have the necessary resources to complete the project?
- Do you have the required expertise and experience to fabricate the structure?
- What are your company’s core competencies?
- Do you have a good understanding of the market and the competition?
- What are your company’s financial resources?
After analyzing your company’s capabilities, you should make a list of the resources that are required to complete the project. This will help you understand the project’s cost and whether or not your company can achieve it.
Shortlisting Vendors
Once you are done analyzing your company’s capabilities, you should have a good idea of the resources required to complete the project. The next step is to shortlist vendors who can provide you with the necessary materials.
The vendor must hold relevant certifications from authorities such as the American Institute of Steel Construction (AISC), American Welding Society (AWS), International Organization for Standardization (ISO), and the National Institute of Certification in Engineering Technologies (NICET). They should also be able to provide you with the necessary resources promptly.
Analyzing Project Progress
It is essential to monitor the project’s progress at every step closely. This includes understanding each task’s status and the resources being used. You can identify potential problems by analyzing the project’s progress and taking corrective action. This can be done by proper reporting from shop floors. The reporting process is divided into three steps:
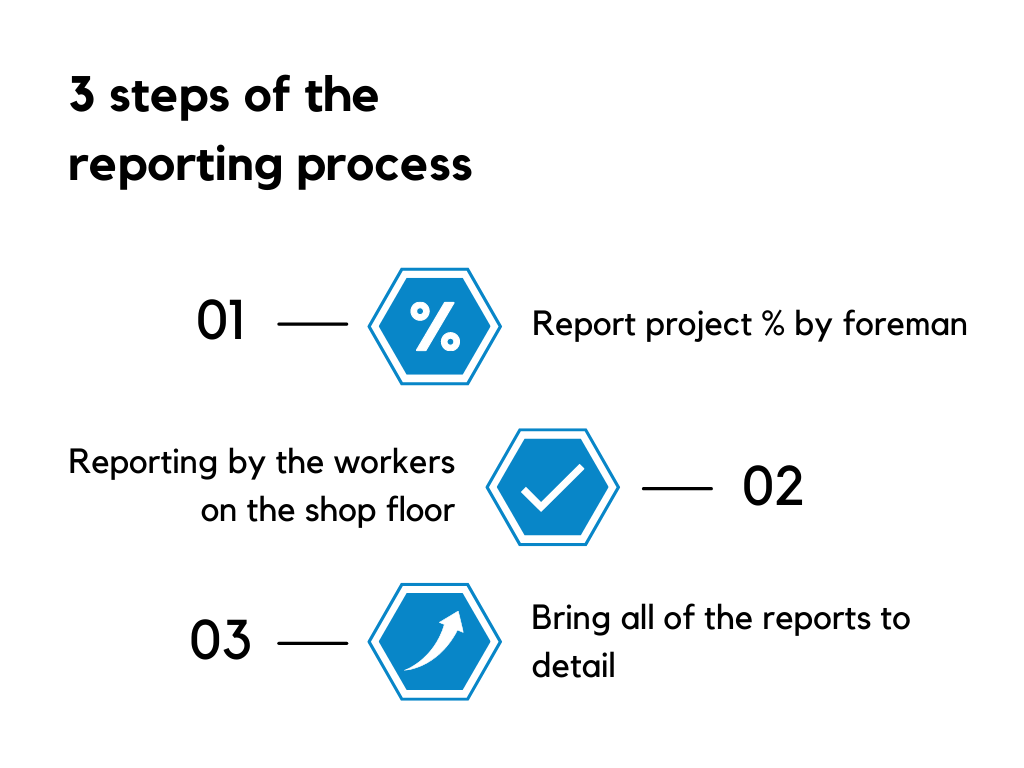
- Report project % by foreman:
The project manager or foreman should fill out this report. It includes a list of all the tasks that have been completed, as well as the percentage of work that has been completed. It helps identify which tasks are behind schedule and on track. This report also helps to understand the project’s overall progress.
- Reporting by the workers on the shop floor:
In a typical structural steel fabrication company, the shop floor is where the bulk of the work takes place. It’s a busy, sometimes chaotic environment, and it’s important for workers to be able to report on what’s going on efficiently and effectively.
There are several ways to do this, but one of the most popular is known as “the production board.” The production board is essentially a physical chart that lists all of the different elements that need to be fabricated for a particular project. Workers use it to track their progress and report any issues that arise. It’s essential for keeping things moving forward on the shop floor and ensuring that everything is on track.
- Bring all of the reports to detail:
After the reports are completed, they should be brought to a meeting to discuss the project’s progress. During this meeting, any issues that have been identified should be addressed, and solutions should be proposed.
This is an essential step in the process because it allows everyone to be on the same page and ensures everyone is aware of the project’s status. It also allows for any necessary changes to keep the project on track.
Ensuring Quality and Safety
Quality and safety are of the utmost importance in steelwork fabrication. There are several ways to ensure the quality of your work. This includes having a quality control plan in place and conducting regular inspections. The quality control plan should be focused on:
Incoming materials: All materials that are used in the fabrication process should be inspected before they are used. This includes checking for damage and ensuring that they meet the required specifications.
Work in progress: Inspections should be conducted regularly to ensure that the work is being done according to the plans and specifications. This includes checking for errors, as well as ensuring that the work is being done safely.
Finished products: The finished products should be inspected to ensure they meet the required standards. This includes checking for defects, as well as ensuring that they are safe to use.
The safety of the workers is also a crucial aspect to consider during the fabrication process. Several safety hazards are associated with steel work fabrication. You can avoid it by following some simple safety guidelines.
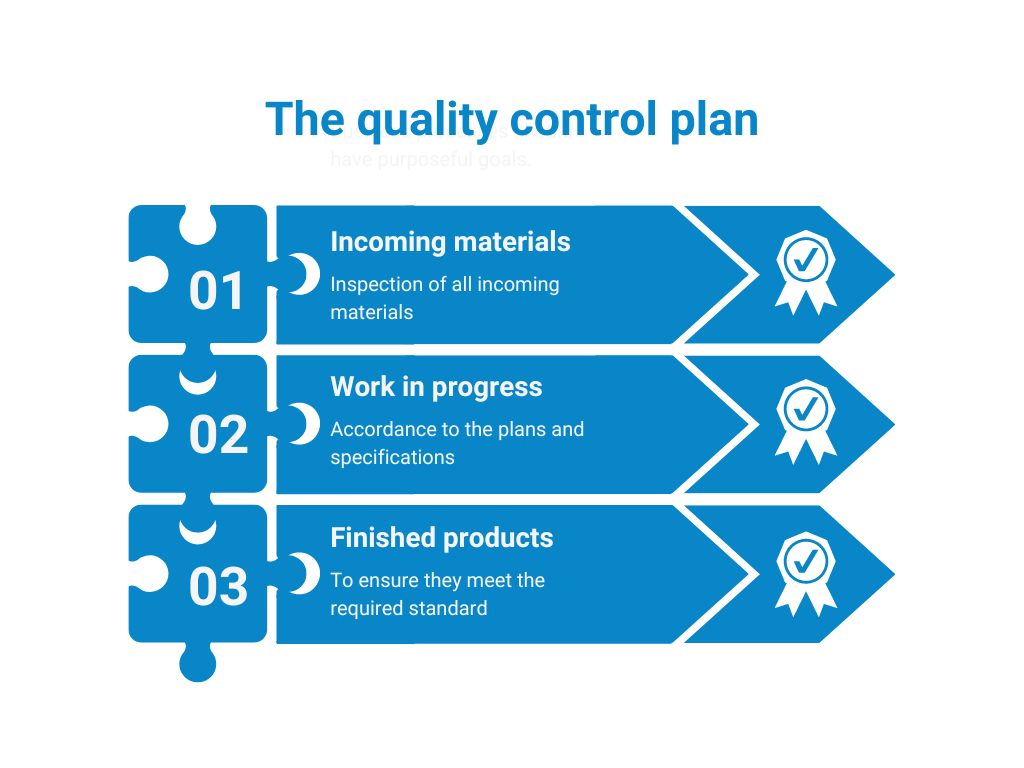
Conclusion
In closing, the structural steel fabrication process is an intricate and rigorous undertaking that forms the backbone of numerous industries, most notably the construction and energy sectors. It is a journey that begins with the precision of detailed shop drawings and ends with the final assembly of robust structures on a construction site. Every step of the process, from the initial designs to the final quality control checks, is instrumental in ensuring the integrity and longevity of the built structures.
A key component of this process is the use of advanced industrial equipment, which ensures the accurate shaping and assembly of the steel components. Laser cutters, for instance, play a pivotal role in this process. Their precision and efficiency in trimming steel beams to exact dimensions are critical to the overall structural integrity of the finished product. These beams, once cut, are then expertly shaped and assembled by skilled steel fabricators, transforming them from simple pieces of metal into integral parts of vast structures.
Furthermore, structural steel fabricators apply various treatments to the fabricated structural steel to enhance its durability and resistance to environmental factors. One such treatment is powder coating. This method not only gives the steel a clean and professional finish, but it also fortifies it against corrosive elements, thereby extending its lifespan and ensuring the safety and stability of the structure it supports.
Once the fabrication process is complete, the structural steel components are transported to the construction site. Here, the meticulous assembly of these parts takes place, following the blueprints outlined in the shop drawings. Whether these structures are being erected in the bustling heart of a city or at an isolated energy industry site, the importance of accuracy in this phase is paramount.
Moreover, the role of structural steel in the construction industry and energy industries is invaluable. Structural steel fabricators provide these sectors with sturdy, reliable, and durable components that are capable of withstanding tremendous pressure and harsh conditions. This functionality and versatility make structural steel a go-to resource in these industries.
In essence, the entire process of structural steel fabrication is a testament to the ingenuity and technological prowess of modern manufacturing. It is a synergy of human skill and advanced machinery, all working together to create structures that form the backbone of our built environment. From the precision of laser cutters to the durability provided by powder coating, each step of the process plays a critical role in producing high-quality steel components.
The process is a testament to the expertise and dedication of steel fabricators, the precision of industrial equipment, and the resilience of steel as a material. In the construction industry and energy industries alike, the demand for fabricated structural steel continues to grow, underlining the importance and relevance of this intricate process in our modern world. As we move forward, the role of structural steel fabrication will continue to be central to our progress, enabling us to build safer, more durable, and more efficient structures.