In the realm of steel manufacturing, the process of galvanization has long been employed to enhance the durability and corrosion resistance of steel products. Two commonly used variations of galvanized steel are galvanized steel and galvannealed steel.
While both types offer protection against rust and offer a range of industrial applications, they possess distinct characteristics that set them apart.
Understanding the differences between galvanized steel and galvannealed steel is essential for making informed decisions in various construction, automotive, and manufacturing industries.
In this article, the properties, manufacturing processes, and applications of galvanized steel and galvannealed steel, shedding light on their unique attributes have been discussed.
Overview
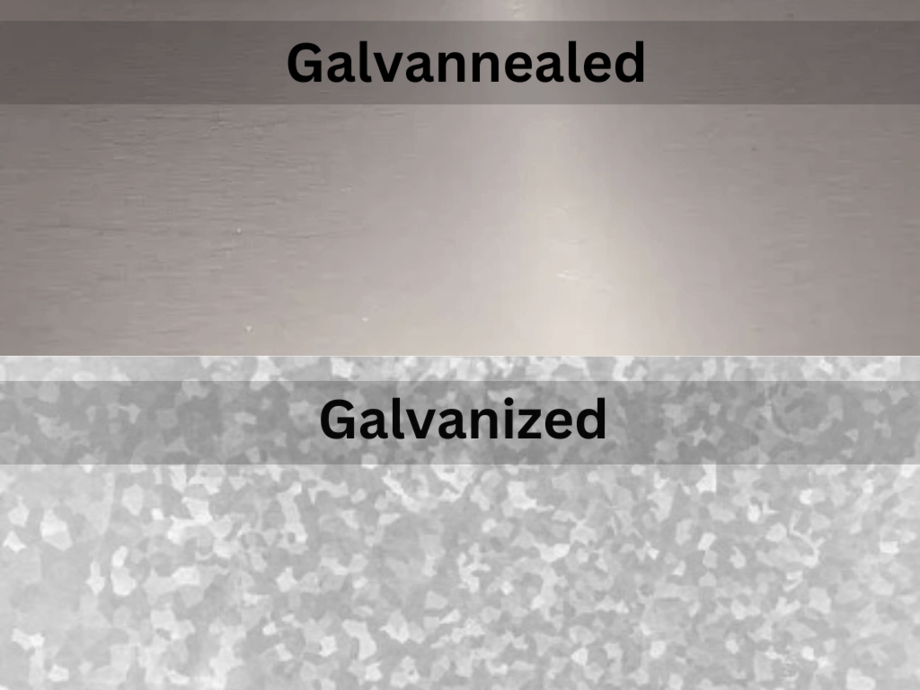
Galvanized Steel: It refers to steel that has been coated with a layer of zinc to protect it from corrosion. This process involves immersing the steel in a bath of molten zinc, forming a protective barrier on its surface. Galvanized steel offers excellent corrosion resistance and is commonly used in outdoor applications, construction, and automotive industries.
Galvannealed Steel: It undergoes an additional manufacturing step. After the steel is galvanized, it is further heated to allow the zinc coating to alloy with the steel, creating a unique zinc-iron alloy layer. This process results in a matte finish with improved paint adhesion and enhanced weldability. Galvannealed steel is often utilized in applications that require superior paint adhesion, such as automotive body panels, appliances, and HVAC systems.
The Evolution of Galvanized and Galvannealed Steel
The evolution of galvanized and galvannealed steel has led to improved corrosion resistance, paint adhesion, and weldability. Galvannealed steel combines the benefits of galvanized steel with a zinc-iron alloy coating, making it ideal for applications requiring enhanced properties.
Both types of steel continue to evolve to meet industry demands for durability and cost-effectiveness.
Properties of Galvanized Steel
Galvanized steel possesses several properties that make it a popular choice in various industries.
The detailed properties of galvanized steel are as follows:
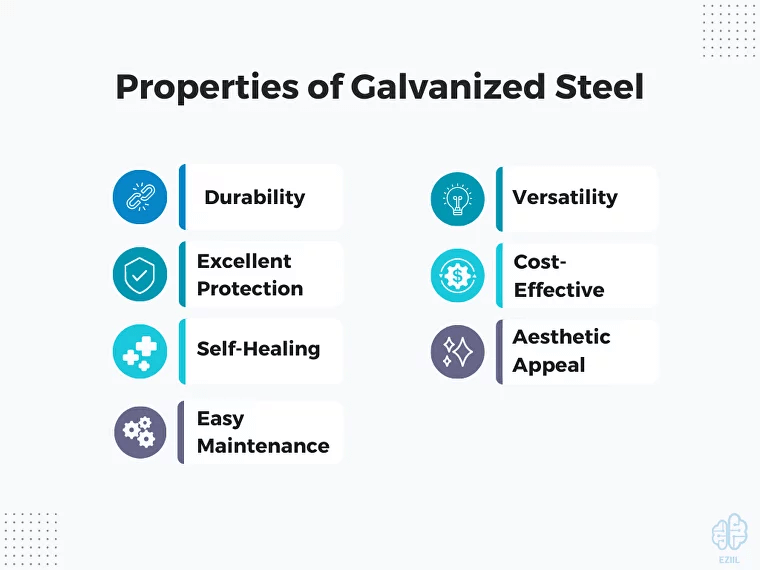
- Durability: Galvanised steel is known for its exceptional durability. The zinc coating provides a robust barrier against moisture, chemicals, and atmospheric elements, making galvanized steel resistant to damage and wear. It can withstand exposure to harsh conditions, including outdoor environments, without significantly degrading.
- Excellent Protection: The zinc coating on galvanized steel provides an excellent protective barrier. It shields the underlying steel from rust, oxidation, and other forms of corrosion. Galvanized steel is particularly suitable for applications where long-term protection against corrosion is critical, such as construction, infrastructure, and outdoor equipment.
- Self-Healing: Galvanized steel possesses a unique self-healing property. If the zinc coating is scratched or damaged, it forms a protective layer of zinc oxide and zinc carbonate over the exposed area, effectively sealing it from further corrosion. This self-healing mechanism helps maintain the integrity of the steel and prolongs its lifespan. Owing to this zinc-oxide magic, Galvanized steel presents itself as a reliable, long-lasting solution in various applications demanding superior corrosion resistance.
- Easy Maintenance: Galvanized steel requires minimal maintenance throughout its service life. It does not need frequent repainting or recoating to maintain its corrosion resistance. The zinc coating provides long-lasting protection, reducing the need for regular maintenance, touch-ups, or replacement.
- Versatility: Galvanized steel is highly versatile and can be fabricated, formed, or welded to meet specific requirements. This versatility makes galvanized steel suitable for a wide range of applications, including construction, automotive, agricultural, and manufacturing industries.
- Cost-Effective: Galvanized steel offers cost-effectiveness in terms of both initial investment and long-term maintenance. The extended lifespan and corrosion resistance of galvanized steel reduces the need for frequent repairs, replacements, and associated costs. It provides a reliable and economical solution for various applications.
- Aesthetic Appeal: Galvanized steel can have an attractive, shiny appearance, particularly when it is newly galvanized. Over time, the zinc coating develops a characteristic dull grey patina, which is often desired in architectural and industrial applications for its distinct aesthetic appeal.
Galvanized steel’s combination of corrosion resistance, durability, easy maintenance, and versatility makes it a preferred choice in numerous industries, including construction, infrastructure, automotive, and manufacturing sectors.
Properties of Galvannealed Steel
Galvannealed steel possesses several distinct properties that differentiate it from other steel coatings.
The detailed properties of galvannealed steel are as follows:
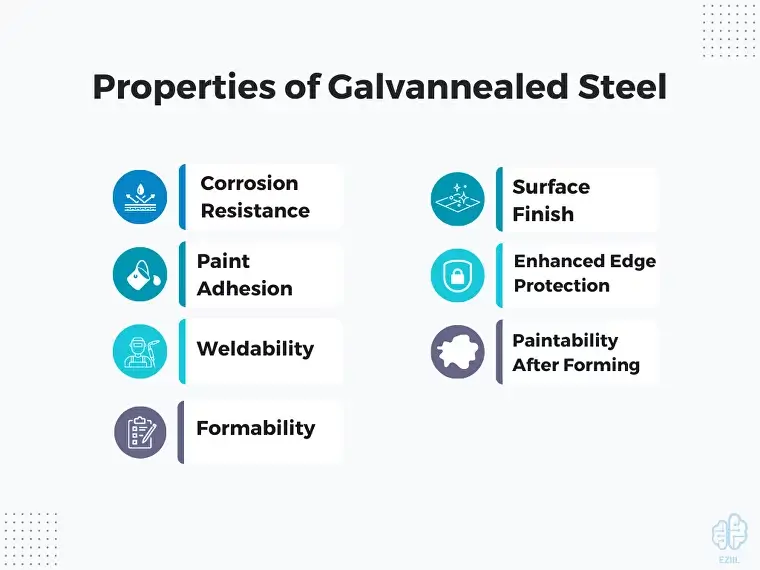
- Corrosion Resistance: Galvannealed steel exhibits excellent corrosion resistance due to the zinc-iron alloy layer formed during the galvannealing process. The zinc-iron alloy provides a robust protective barrier against rust and corrosion, making galvannealed steel highly durable, even in harsh environments.
- Paint Adhesion: One of the notable properties of galvannealed steel is its exceptional paint adhesion. The matte and rough surface resulting from the galvannealing process provides an ideal texture for the paint to adhere effectively. This property is crucial in applications where the steel needs to be painted or coated for additional protection or aesthetic purposes, such as automotive body panels and appliances.
- Weldability: Galvannealed steel offers excellent weldability, making it easier to join and fabricate. The zinc-iron alloy layer formed during galvannealing has beneficial properties for welding, as it helps prevent weld spatter and provides a conducive surface for strong weld joints. This property is advantageous in industries that require extensive welding operations, such as automotive manufacturing and construction.
- Formability: Galvannealed steel maintains good formability, allowing it to be easily shaped, bent, or stamped without cracking or damaging the coating. This property is important in industries that require complex or intricate shapes, such as the production of appliances, HVAC systems, and various fabricated metal components.
- Surface Finish: Galvannealed steel has a distinctive matte grey finish. This surface appearance is aesthetically appealing in certain applications, and it can also help reduce glare or reflection in outdoor or high-visibility settings.
- Enhanced Edge Protection: The zinc-iron alloy layer in galvannealed steel provides enhanced edge protection compared to other steel coatings. This property is especially beneficial in applications where exposed edges are prone to corrosion, such as cut edges or bends.
- Paintability After Forming: Galvannealed steel retains its excellent paint adhesion even after forming processes, such as bending or deep drawing. This allows for post-forming painting or coating, ensuring consistent protection and aesthetics throughout the product.
It is important to note that while galvannealed steel offers unique properties, it may have lower corrosion resistance compared to traditional galvanized steel in certain applications where the zinc-iron alloy layer may be compromised or damaged.
Thus, the choice between galvannealed steel and other steel coatings depends on the specific requirements and environmental conditions of the intended application.
Galvanneal vs Galvanised: The Distinctions
Now that we understand the basics of these two materials, let’s dive into the difference between galvanized and galvannealed steel.
Property | Galvanized Steel | Galvannealed Steel |
---|---|---|
Coating Composition | Pure Zinc Coating | Zinc-Iron Alloy Coating |
Appearance | Shiny, Metallic | Matte, Gray |
Paint Adhesion | Good | Excellent |
Weldability | Good | Excellent |
Corrosion Resistance | Excellent | Excellent |
Formability | Good | Good |
Surface Finish | Smooth | Matte, Rough |
Edge Protection | Standard | Enhanced |
Self-Healing | Yes | No |
Aesthetic Options | Various colour options are available | Suitable for post-forming painting or coating |
Recommended Applications | Outdoor applications, general purpose | Automotive body panels, appliances, HVAC systems |
Paintability After Forming | Yes | Yes |
Heat Resistance | Moderate | Moderate |
Coating Thickness | Typically thicker coating | Typically thinner coating |
Cost-effectiveness | Cost-effective | Cost-effective |
Maintenance | Minimal maintenance required | Minimal maintenance required |
Weld Spatter | Potential for weld spatter | Reduced weld spatter |
Comparison with other Metals
Here is a short comparison of Galvanized steel with other metals, based on different properties.
- Zinc Coated vs Galvanised: The terms “zinc coated” and “galvanized” are often used interchangeably. However, the process of zinc coating can involve either galvanizing or zinc plating. Zinc plating, also known as zinc plated vs galvanized, involves applying a thin coating of zinc to a metal substrate to prevent rust.
While both zinc-coated and galvanized materials offer rust resistance, the thickness of the zinc layer can vary significantly. Galvanized steel typically has a thicker zinc coating, making it more durable and longer-lasting.
- Galvanised Steel Melting Point and Rust Resistance: An intriguing aspect of galvanized steel is its melting point. The galvanized steel melting point is around 1,200 degrees Celsius. This high melting point, along with the protective zinc coating, makes it an ideal material for high-temperature and high-pressure applications.
A common question is, does galvanized steel rust? The answer is, eventually, it does. However, the protective zinc layer significantly slows down the rusting process, thus extending the material’s lifespan.
- Galvanised vs Stainless Steel: The difference between galvanized and stainless steel is another important topic in the realm of the metal industry. Stainless steel is an alloy comprising iron and a minimum of 10.5% chromium, which provides excellent corrosion resistance and is highly suited to areas where sanitation is critical or harsh chemicals are present.
In contrast, galvanized steel has a steel base with a protective zinc layer. While it also resists corrosion, it does not offer the same level of resistance as stainless steel, particularly in environments with high salinity or acidity.
- Carbon Steel vs Galvanised Steel: Carbon steel, as the name implies, is primarily composed of iron and carbon. Unlike galvanized steel, it does not have a protective zinc coating, making it less resistant to corrosion. However, it is stronger and more durable than galvanized steel, making it a preferred material for applications requiring high strength.
For example, given its notable strength and durability, carbon steel often proves to be the material of choice for handrails, offering reliable support and longevity despite its absence of a protective zinc layer like galvanized steel.
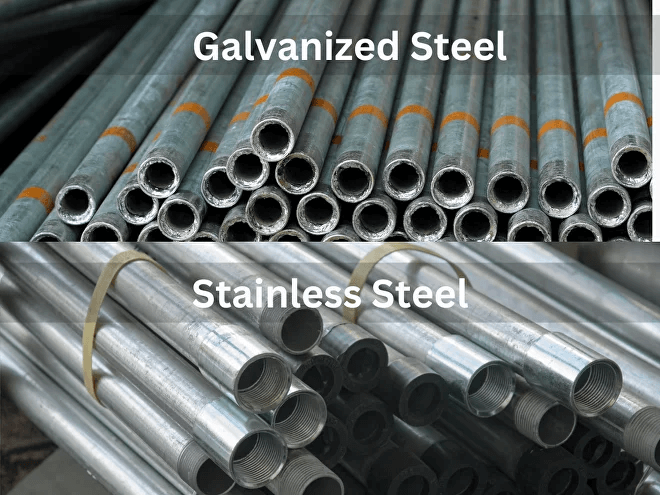
How to Galvanize Steel?
The process of making galvanized steel involves several steps that ensure the steel is coated with a layer of zinc, providing it with enhanced corrosion resistance. The detailed process description of making galvanized steel is as follows:
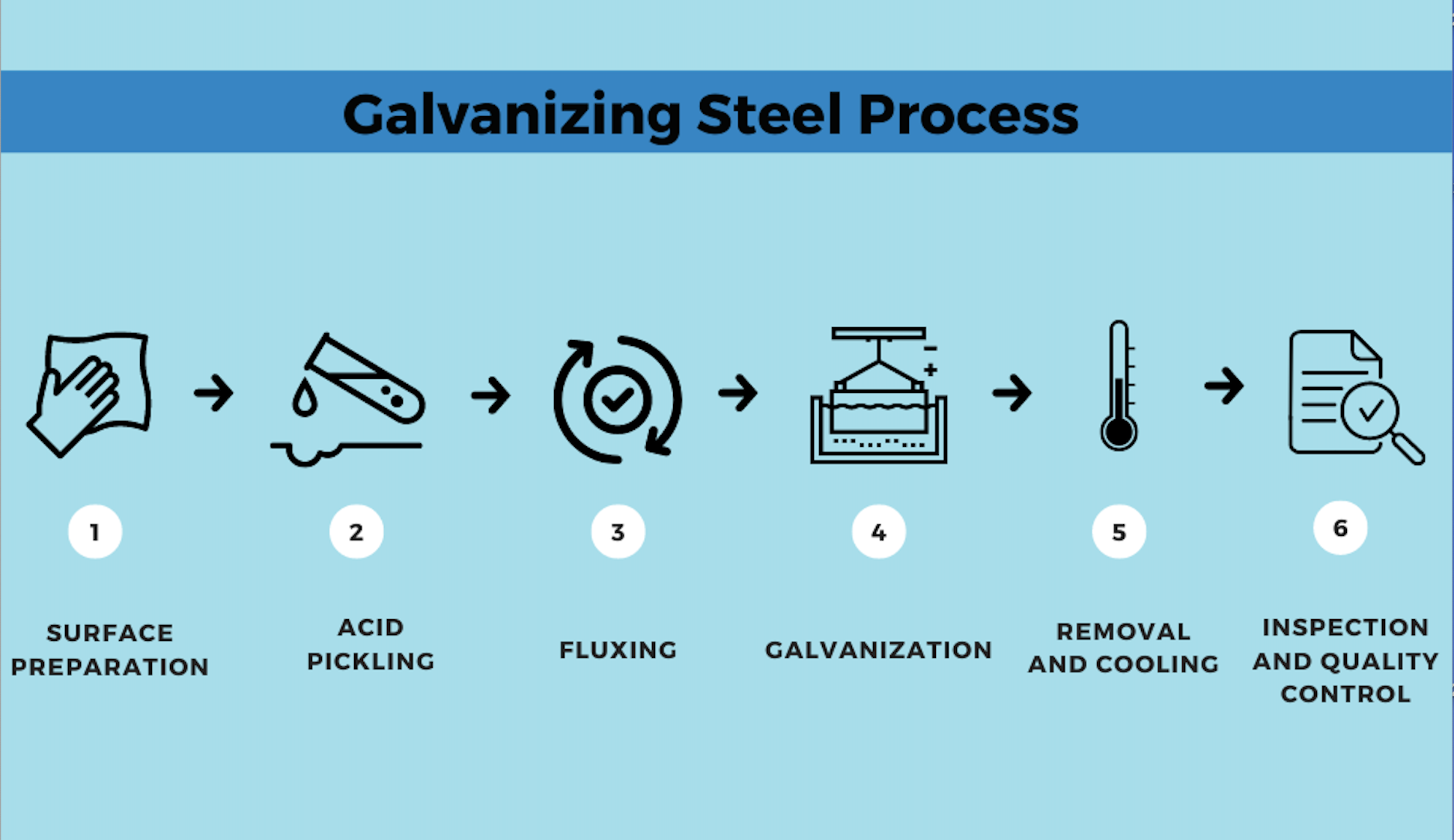
- Surface Preparation: The steel to be galvanized is first thoroughly cleaned to remove any dirt, rust, or contaminants. This is typically done by immersing the steel in a degreasing bath or using chemical cleaning agents. The goal is to ensure a clean and smooth surface for proper adhesion of the zinc coating.
- Acid Pickling: After the initial cleaning, the steel is immersed in an acid solution, usually a diluted mixture of hydrochloric acid and sulfuric acid. This step, known as acid pickling, removes any remaining mill scale, rust, or oxides from the steel’s surface. It also helps to etch the surface, creating a rough texture that improves the bond between the steel and the zinc coating.
- Fluxing: Once the steel has been pickled, it undergoes fluxing. Flux is a chemical compound, often a mixture of zinc ammonium chloride and other additives, which is applied to the steel’s surface. Fluxing helps to remove any remaining oxides, promotes the flow of the zinc coating, and prepares the surface for galvanization.
- Galvanisation: The steel is now ready for galvanization. It is immersed in a bath of molten zinc, typically heated to a temperature between 815°C and 850°C (1500°F and 1560°F). The zinc bath may contain additional alloying elements, such as aluminum, to enhance the coating’s properties. As the steel is immersed in the bath, the molten zinc reacts with the iron in the steel, forming a metallurgical bond. The zinc coating covers the entire surface of the steel, providing a protective layer.
- Removal and Cooling: After the steel has been thoroughly coated with zinc, it is slowly withdrawn from the zinc bath to allow excess zinc to drain off. The steel is then cooled, either by air or by quenching in water. This solidifies the zinc coating and ensures it adheres firmly to the steel surface.
- Inspection and Quality Control: Once the galvanization process is complete, the galvanized steel is inspected for any imperfections, such as bare spots or rough areas. Various quality control tests, including coating thickness measurement, visual inspection, and adherence to relevant standards, are conducted to ensure the final product meets the required specifications.
The resulting galvanized steel exhibits excellent corrosion resistance due to the protective zinc coating. It can be further processed, fabricated, or used as is in a wide range of applications, including construction, infrastructure, automotive, and manufacturing industries.
The Process to make Galvannealed Steel
The process of making galvannealed steel involves additional steps beyond the galvanization process, which result in the formation of a zinc-iron alloy layer on the steel surface.
The detailed process description of making galvannealed steel is as follows:

- Surface Preparation: Similar to galvanized steel, the surface preparation of the steel is crucial. It involves thorough cleaning to remove dirt, rust, and contaminants. The steel may undergo a degreasing process or chemical cleaning to ensure a clean surface for proper coating adhesion.
- Acid Pickling: After the initial cleaning, the steel is subjected to acid pickling. This step involves immersing the steel in an acid solution, typically a mixture of hydrochloric acid and sulfuric acid. Acid pickling removes any remaining mill scale, rust, or oxides from the steel surface, leaving it clean and prepared for the subsequent processes.
- Fluxing: Once the steel has been pickled, it goes through fluxing, similar to the galvanization process. Flux, a chemical compound containing zinc ammonium chloride and other additives, is applied to the steel’s surface. Fluxing removes any remaining oxides, promotes the flow of the zinc coating, and prepares the surface for galvanization.
- Galvanization: The galvanization step is similar to the process used for galvanized steel. The steel is immersed in a bath of molten zinc, heated to a temperature between 815°C and 850°C (1500°F and 1560°F). As the steel is submerged, the molten zinc reacts with the iron in the steel, forming a zinc coating.
- Heat Treatment (Annealing): After galvanization, the steel is further processed through a heat treatment known as annealing. The galvanized steel is heated to a specific temperature, typically around 550°C to 600°C (1020°F to 1110°F), and held at that temperature for a predetermined time. This heat treatment allows the zinc coating to alloy with the steel, creating a zinc-iron alloy layer.
- Cooling: After the annealing process, the galvannealed steel is slowly cooled. The controlled cooling process helps in solidifying the zinc-iron alloy layer, ensuring its adhesion to the steel surface.
- Inspection and Quality Control: Once the galvannealing process is complete, the galvannealed steel undergoes a rigorous inspection and quality control. The steel is examined for any imperfections, such as uneven alloying, surface defects, or insufficient coating thickness. Various tests, including visual inspection, coating thickness measurement, and adherence to applicable standards, are performed to ensure the final product meets the required specifications.
The resulting galvannealed steel possesses a unique zinc-iron alloy layer on its surface. This layer provides not only corrosion resistance but also improved paint adhesion and weldability. Galvannealed steel finds applications in industries that require excellent paintability, such as automotive manufacturing, appliances, HVAC systems, and other applications where a painted or coated finish is desired.
Unravelling the Mystery of Zinc Coating:
Zinc Coating vs Galvanising
To understand the difference between zinc coating vs galvanized, we need to take a closer look at the zinc coating process. Zinc coating, also known as zinc plating, involves applying a thin layer of zinc to a metal surface to provide a barrier against corrosion. This is done either by hot-dip galvanizing, where the metal is dipped into a bath of molten zinc, or by electroplating, where a layer of zinc is deposited onto the metal using an electric current.
While both methods provide corrosion resistance, the thickness and durability of the zinc layer can vary significantly. For galvanizing It is immersed in a bath of molten zinc, typically heated to a temperature between 815°C and 850°C (1500°F and 1560°F). The zinc bath may contain additional alloying elements, such as aluminum, to enhance the coating’s properties. As the steel is immersed in the bath, the molten zinc reacts with the iron in the steel, forming a metallurgical bond. Hot-dip galvanizing typically results in a thicker and more durable coating, making it a preferred method for heavy-duty applications.
Choosing the Right Material
In the end, the choice between galvanized and galvannealed steel will depend on specific needs.
- If material is required with superior corrosion resistance and durability, galvanized steel might be the best bet. It’s protective zinc coating and high melting point make it a suitable choice for outdoor structures and heavy-duty applications.
- On the other hand, if the project requires a material that offers excellent paintability and weldability, galvannealed steel would be a more suitable choice. With its uniform, matte finish and enhanced fabricability, it’s an ideal choice for automotive parts, electric enclosures, and other applications that require a high-quality finish.
In reflecting on the multitude of advantages that galvanized steel and galvannealed steel bring to the table, it’s clear that each holds its own in the vast world of metal manufacturing. Galvanized steel, robust and resilient, shines when subjected to the elements, standing as a testament to durability.
Whether it’s used in outdoor fixtures or industrial installations, galvanized steel repeatedly proves its worth. Furthermore, the self-healing properties of galvanized steel—its ability to form a protective zinc-oxide layer when scratched or damaged—only add to its sterling reputation. In essence, the myriad uses and benefits of galvanized steel are clear, making it a material of choice for countless applications.
So, whether you opt for galvanized steel or its galvannealed counterpart, remember the unique strengths of galvanized steel, and consider how they can serve your specific needs.
Undeniably, galvanized steel, utilized correctly, can be an effective tool in your material selection arsenal.
Conclusion
In conclusion, both galvanised and galvannealed steel has their unique properties and applications. Galvanised steel, with its robust zinc coating and high melting point, is ideal for outdoor structures exposed to harsh elements. On the other hand, galvannealed steel, with its superior weldability and paint adhesion, is a better choice for applications that require aesthetic appeal and detailed fabrication.
Choosing between these two materials will depend on your specific needs and the environment in which the material will be used. As it has seen, there is no one-size-fits-all answer in the galvanneal vs galvanised debate.
It’s about picking the right material for the job, and with this knowledge, you are now equipped to make that choice wisely.