Welding Procedure Specification is a vital document in WPS welding operations that outlines the specific welding procedures to be followed for a particular welding job. The WPS serves as a guide for welders, supervisors, inspectors, and quality control personnel in ensuring that welding is performed consistently and to the required standard.
WPS welding procedures involve many variables such as welding position, base metal thickness, filler metal, welding parameters, preheating, and post-weld heat treatment, among others. The WPS documents all these variables to ensure that WPS welding is carried out in a standardized manner. It also specifies the acceptance criteria for the welds, which is usually determined by applicable codes and standards.
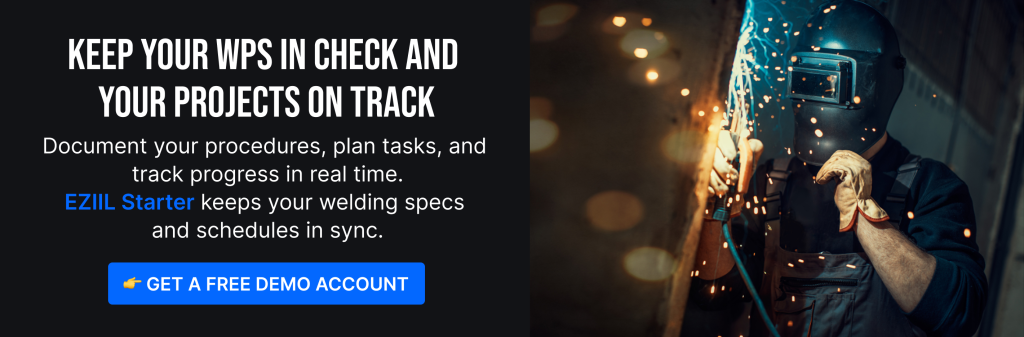
A WPS is typically developed by a welding engineer or qualified welding personnel, who evaluates the welding requirements for WPS welding and prepares a comprehensive document that provides a clear and concise procedure to follow. The WPS includes information on the type of welding process, such as Shielded Metal Arc Welding (SMAW), Gas Tungsten Arc Welding (GTAW), Gas Metal Arc Welding (GMAW), or Flux-Cored Arc Welding (FCAW), and the specific parameters that must be followed for each process.
What is a Prequalified Welding Procedure Specification?
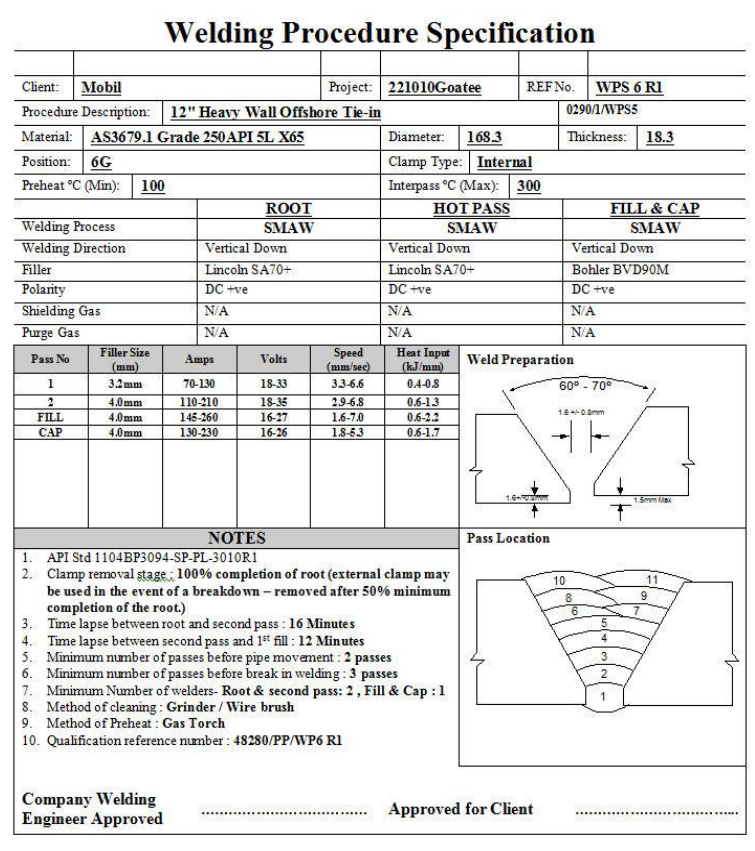
Image credit: https://www.ohiogasassoc.org/
A prequalified Welding Procedure Specification (WPS) is a standardized document that provides guidelines for performing a specific WPS welding task. A prequalified WPS means that it has been previously approved by a welding authority, such as the American Welding Society (AWS), without the need for additional testing.
Prequalified WPSs are typically used for relatively simple WPS welding tasks that have been proven to be reliable and effective over time. This can include processes like shielded metal arc welding (SMAW), gas tungsten arc welding (GTAW), and gas metal arc welding (GMAW).
The benefit of using a prequalified WPS in WPS welding is that it can save time and resources in the welding process. Central to the WPS is the welding inspection, a key process ensuring procedure compliance and utmost quality in WPS welding. Welders can refer to prequalified WPSs to ensure that they are following the correct procedures and using the appropriate materials and equipment. This can help to ensure that the final welded product is of high quality and meets the necessary standards for safety and performance.
Some Other Welding Procedures
The WPS also specifies the required Welding Procedure Qualification Record (WPQR) and Weld Procedure Qualification Record (PQR) tests to be performed to ensure that the welding process produces quality welds.
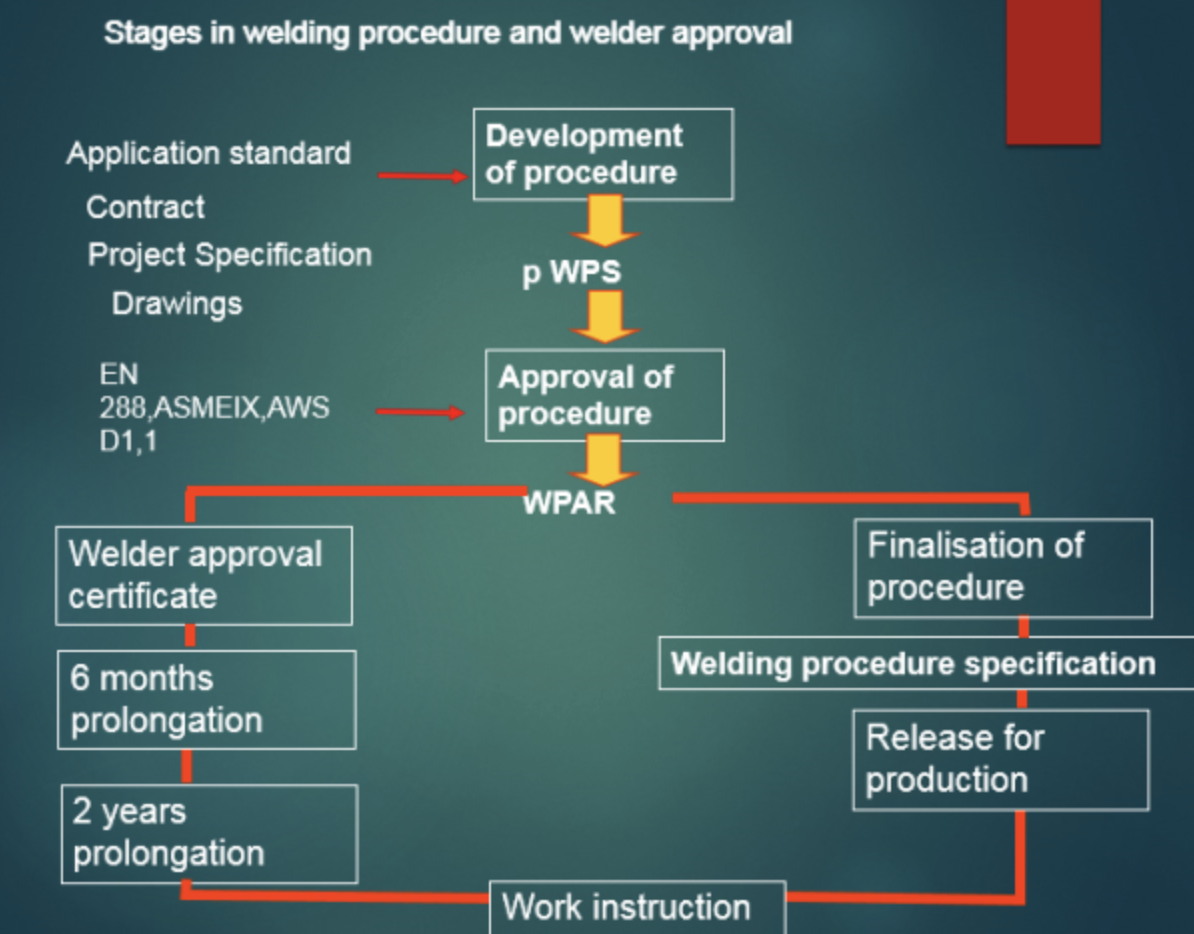
Welding Procedure Qualification Record (WPQR)
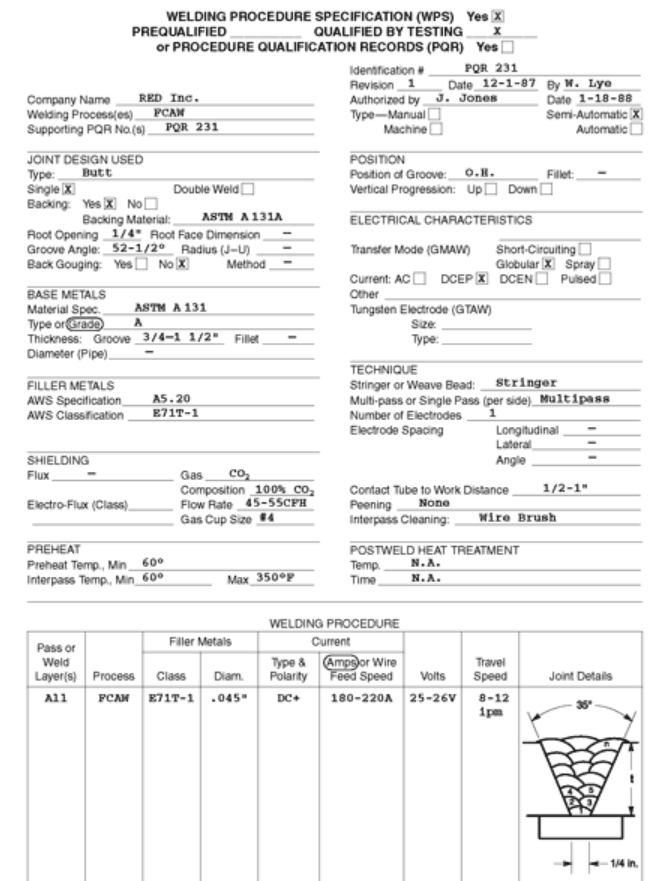
Image credit: https://www.metallurgyfordummies.com
WPQR stands for Welding Procedure Qualification Record. It is a document that certifies that a particular welding procedure has been tested and has met the required codes and standards. A WPQR is a necessary requirement for developing a Welding Procedure Specification (WPS).
The WPQR test involves welding a test coupon using the welding procedure specified in the WPS. The test coupon is then subjected to various tests to evaluate the quality and soundness of the weld. These tests may include visual inspection, radiography, ultrasonic testing, or mechanical testing. The results of the tests are recorded in the WPQR document.
The WPQR document typically includes the following information:
- Identification of the welding procedure specification (WPS) used for the test.
- Welding process used.
- Base metals specification.
- Filler metal specification.
- Welding parameters, including amperage, voltage, travel speed, and preheat temperature.
- Results of the tests performed on the test coupon, including visual inspection, radiography, ultrasonic testing, or mechanical testing.
- Any limitations or restrictions associated with the welding procedure
The WPQR is closely related to the WPS, as it is used to verify that the welding procedure specified in the WPS produces quality welds that meet the required codes and standards. The WPQR provides evidence that the welding procedure has been tested and has passed the required tests. The WPS, on the other hand, is a document that outlines the welding procedures to be followed for a particular welding job based on the information in the WPQR.
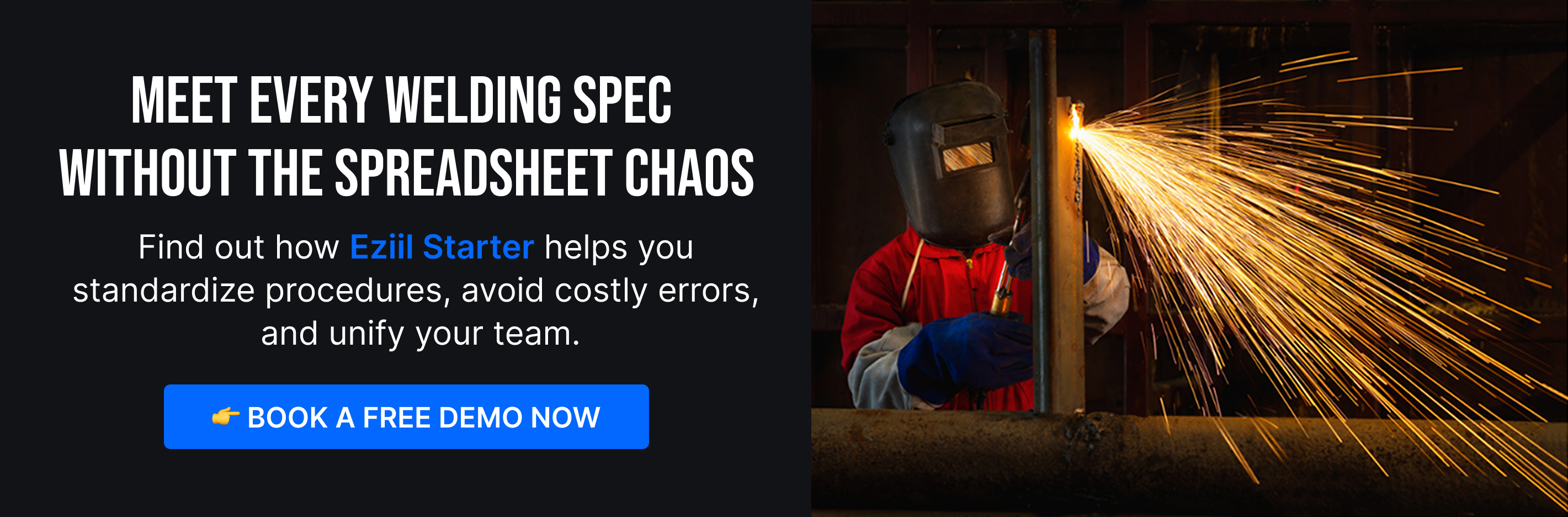
Procedure Qualification Record (PQR)
PQR stands for Procedure Qualification Record. It is a document that certifies that a particular welding procedure has been qualified to meet the required codes and standards. The PQR is an essential element in developing a Welding Procedure Specification (WPS).
The PQR involves welding a test coupon using the proposed welding procedure. The test coupon is then subjected to various tests to evaluate the quality and soundness of the weld. These tests may include visual inspection, radiography, ultrasonic testing, or mechanical testing. The results of the tests are recorded in the PQR document.
The PQR is closely related to the WPS, as it is used to develop the welding procedure specified in the WPS. The PQR provides evidence that the welding procedure has been qualified to meet the required codes and standards. The WPS, on the other hand, is a document that outlines the welding procedures to be followed for a particular welding job based on the information in the PQR.
See the PQR form sample below:
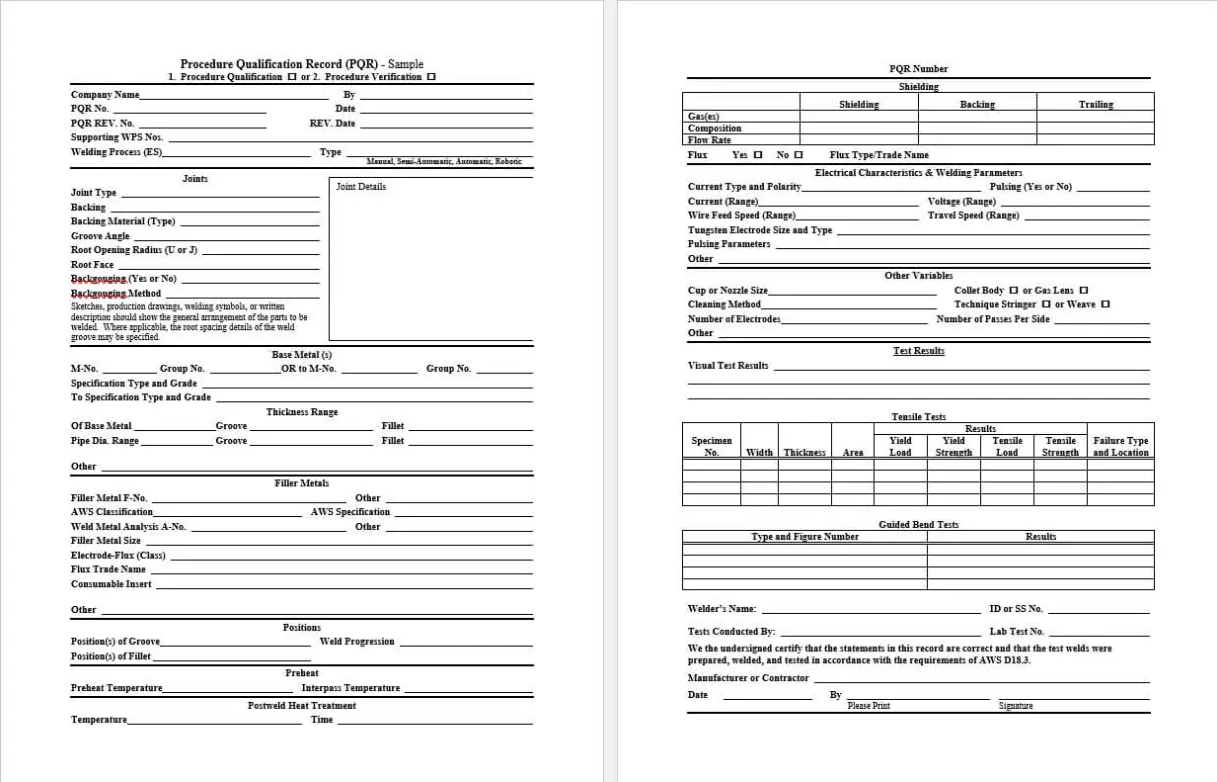
What is the Relation Between all these Welding Procedures?
WPS, WPQR, and PQR are all related to each other in the context of welding.
They are all important documents that are used to ensure that welding procedures are developed and followed correctly to produce high-quality welded joints.
The Welding Procedure Specification (WPS) is a document that outlines the specific welding procedures that are to be used for a particular welding job. The Procedure Qualification Record (PQR) is a document that certifies that a particular welding procedure has been qualified to meet the required codes and standards.
The Welding Procedure Qualification Record (WPQR) is similar to the PQR in that it involves welding a test coupon using the proposed welding procedure and subjecting it to various tests.
However, the WPQR includes additional information, such as the identity of the welder, the welding equipment used, and any other relevant details that are specific to the welding procedure.
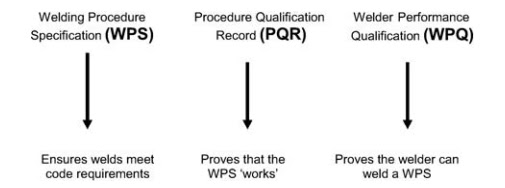
Conclusion
To summarize, WPS (Welding Procedure Specification), WPQR (Welding Procedure Qualification Record), and PQR (Procedure Qualification Record) are interconnected documents that play a critical role in ensuring the proper development and implementation of welding procedures, resulting in high-quality welded joints.
The PQR is utilized to validate a welding procedure, which is then recorded in the WPS. On the other hand, the WPQR is used to confirm that a welding procedure has been qualified and is prepared for deployment in real-world welding assignments.
These meticulously crafted documents serve as roadmaps, detailing the unique characteristics of different metal types and the precise flow rates required.
With WPS, we bring standardization to the welding world, paving the way for precision and excellence.