Intumescent paint is not very well known to many, yet it performs a vital role in the safety of our modern infrastructure. Intumescent paint is used in fire management and safety strategies for commercial buildings across the world in passive applications.
Using this type of paint is an excellent solution for fire damage mitigation, and it is likely that you have seen it in the rafters of your local commercial buildings.
Intumescent paint is a paint that is quite literally made with a substance that has intumescent properties, or properties that swell as a result of heat exposure.
This swelling leads to an increase in volume and a decrease in density, which prevents the coated material from receiving as much direct heat as it otherwise would have in a non-intumescent coated situation.
Intumescent paint is commonly required in fire protection and fire management applications, primarily as a passive fire protection method.
A passive fire protection method refers to an approach to fire safety that does not have an active release of energy or require an input to work at the right time.
In other words, intumescent paint is passive protection in the sense that it is always ready, with no further monitoring needed beyond the initial application of the paint and insurance that it has properly adhered to the desired surface.
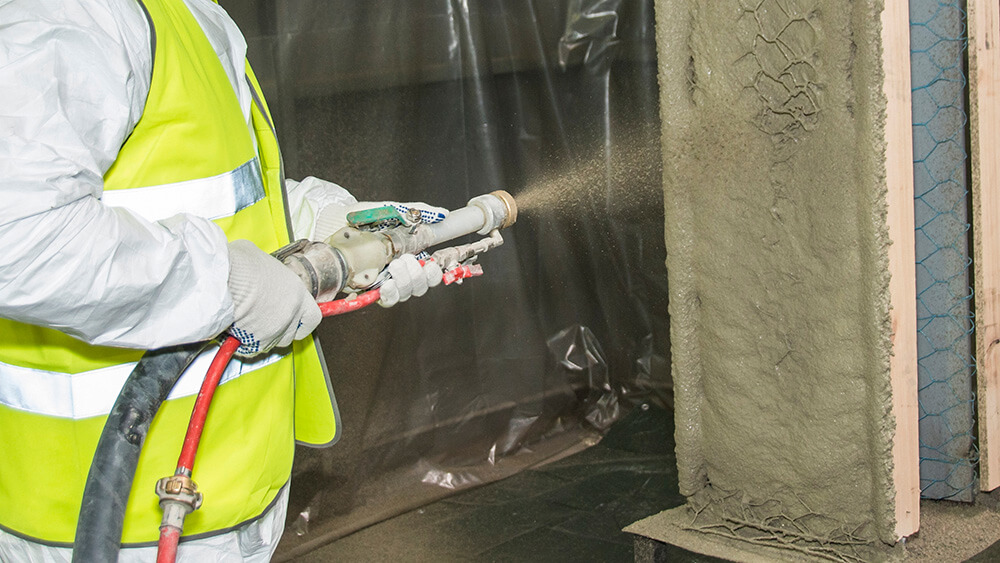
Grades of Intumescence
Intumescent paint finds itself in many different applications, and depending on the application the level of intumescence can vary. When thinking of intumescence, imagine a roasted marshmallow that chars and expands as it is heated – this is known as a soft char and is apparent in other materials used in coatings as well.
There are two primary types, or grades, of intumescent materials: Soft Char and Hard Char.
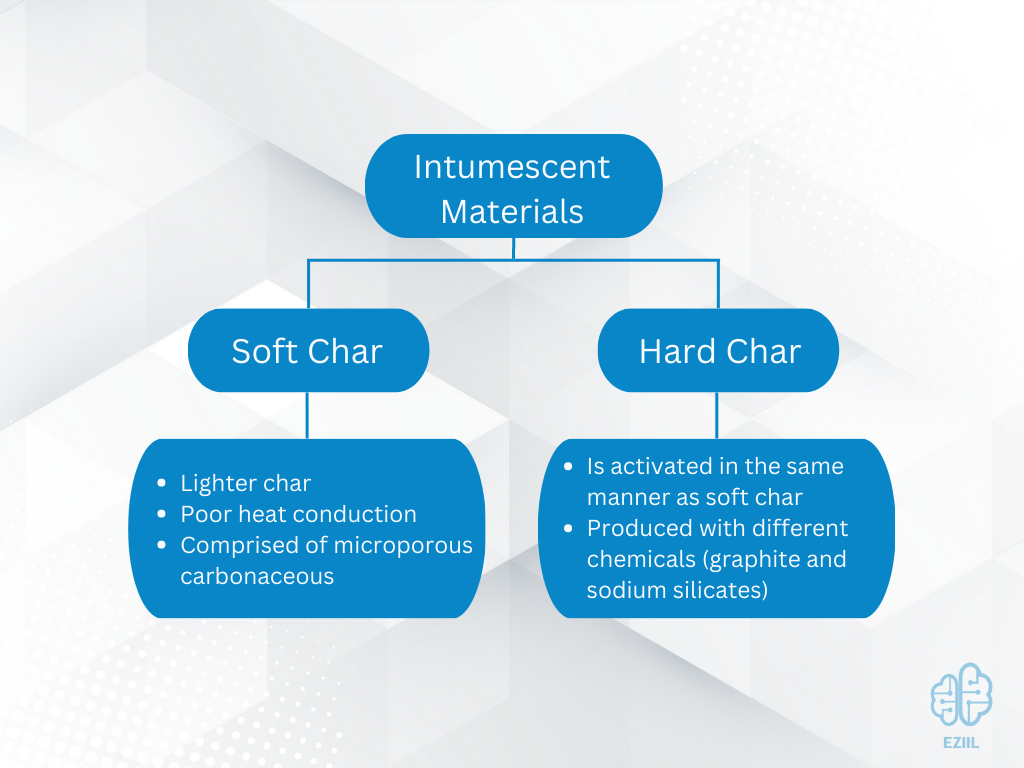
Soft Char
Soft Char intumescent materials produce a lighter char than Hard Char materials, referred to as light char. The light char produced during the heating process has poor heat conduction, which acts as a retardant in the transfer of heat from the heat source (fire) to the material that is coated.
Light char is typically comprised of microporous carbonaceous foam that is a result of the chemical reaction between three main components: melamine, ammonium polyphosphate, and pentaerythritol tetranitrate.
The chemical reaction takes place in a matrix that is formed by a molten binder which is typically based on styrene acrylates or vinyl acetate copolymers.
Soft char is typically used in thin coatings for the fireproofing of structural steel as well as being present in firestop pillows, which are essentially large pillows used to block holes in which fire is actively trying to pass through.
Hard Char
Hard Char is activated in the same manner as soft char but is produced with different chemicals. The primary chemicals used to produce hard char are graphite and sodium silicates.
The matrix used to house these chemicals is like that of Soft Char, but depending on manufacturer the compositions can change per the desired level of charring.
How is Intumescent Paint Made?
The manufacturing process of intumescent paint involves a large amount of chemical processing, similar to any modern paints.
Intumescent paints are comprised of a primary binder that suspends a series of chemicals within itself. This binder is in a liquid form as well as the associated chemicals, and when the product is applied to a surface, it hardens and waits to react to heat.
As the intumescent paint heats up, it begins to soften and revert towards a more ‘molten’ state, which allows the chemicals to interact and cause the charring process.
Intumescent paint is typically offered in black, dark gray, ‘white’ gray, and white color options with the most common color seen in application being white.
There are two primary reasons why white is the most commonly used color for intumescent paints: the cost to manufacture is cheaper with respect to pigments, and more importantly white paint will show evidence of charring or cracks in the coat more prominently.
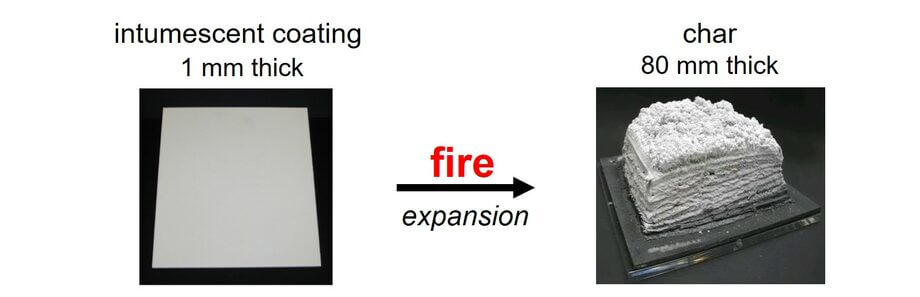
Image credit: https://knowledge.ulprospector.com
Book a 60-minute demo to see
how eziil mrp solution works for you
When to Apply Intumescent Paint?
Intumescent paint can be applied during any stage of the construction process and is typically done at the beginning or end stages of building.
For modular, bolt together structures that require little welding and consist primarily of lifting into position and fastening, it is common to see intumescent paint applied before material is delivered to the job site.
If the structural components are expected to be handled significantly, some builders and fireproofing agencies recommend waiting until the build is completed to apply the coating.
One of the risks with either timing scenario is improper surface preparation and layer adhesion, which is present with any painting applications.
If handled too much or applied in too high or low of humidity, intumescent paint may begin to crack and form laminations on the surface in which proper adhesion never occurred.
The safest bet when applying intumescent paint is to apply it to individual structural members before construction begins, with a plan to finish off the structure with a final topcoat at the end stages of the build.
The photo below shows intumescent paint in its traditional white colour applied to an I-Beam before construction:
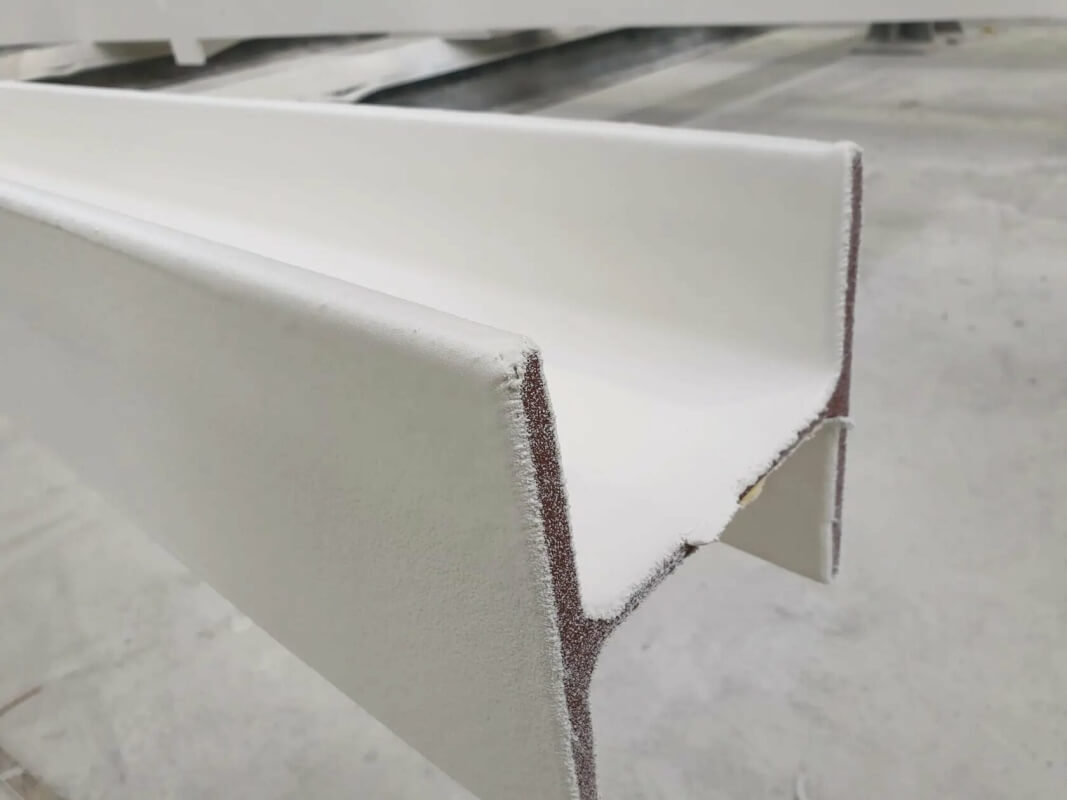
Intumescent Paint Supplier Qualifications
While intumescent paint is a practical solution for many situations, there are specific ways to determine if the supplier you are considering provides a product that is up to specification.
Check for Code Adherence
The easiest way to identify if the supplier has an adequate product is to check if they are meeting fireproofing compliance requirements.
In the United States, ASTM E119 (UL 263) and ASTM E84 (UL 723) are the most referenced standards for intumescent coatings and fireproof building materials. When in doubt, ensure that the product you are choosing meets one, or both, of these specifications.
Check for Industry Membership
The next qualification to consider is supplier memberships to known fireproofing organizations, such as the NFCA (National Fireproofing Contractors Association).
If the supplier is a member of this organization, they are required to invest in continued education within the industry and are vetted by the organization before being allowed to become a member.
As an example, the NFCA requires that all its active members have at least two years and 20 jobs within the passive fireproofing industry.
Gauge Supplier Expertise
When sending requests for quotations, be mindful of the responsiveness and knowledge base of the supplier. Have they been in the industry a long time? Are they able to answer all of your questions effectively and in a timely manner? Do they have any in-house specialists that can answer more technical application questions?
These are all good questions to ask to gauge the supplier’s knowledge within the passive fireproofing business.
Alternatives to Intumescent Paint
While intumescent paint is a practical solution for many passive fireproofing applications, there are a few other alternatives that can be used.
These two coatings are known as lightweight cementitious coatings and a dense concrete coating.
Both coatings do not show the same expansion or char characteristics as intumescent paint, but they can withstand extremely high temperatures without flaking off or allowing direct flame contact to the materials underneath them.
Conclusion
In conclusion, intumescent paint serves as a critical solution in ensuring fire safety in a wide range of applications within product design and mechanical engineering. By providing reliable fire protection for various building materials, including structural steel, these specialized coatings play an essential role in enhancing fire resistance and preventing structural failure during fires. The availability of both environmentally friendly water-based and durable solvent-based intumescent paints enables professionals to select the most suitable fire protection solution for their specific needs while adhering to building codes and fireproofing standards.
Compliance with these building codes and fireproofing standards is of utmost importance in guaranteeing the effectiveness of intumescent paint products in offering fire protection and maintaining fire safety. These codes establish minimum fire rating requirements for materials like structural steel, which, when met, contribute to creating safer structures and a more secure environment for occupants and users. Adherence to fireproofing standards, such as ASTM E119, BS 476, and ISO 834, ensures that intumescent paint products meet the required fire resistance criteria, ultimately enhancing the overall fire safety in buildings and structures.
Therefore, intumescent paint is an indispensable tool in the realm of fire safety, offering vital fire protection for structural steel and other construction materials, and contributing to a safer and more secure built environment. By selecting the most appropriate type of intumescent paint and adhering to building codes and fireproofing standards, professionals in product design and mechanical engineering can effectively enhance fire resistance, protect lives and property, and create a better, safer world.