Thousands of years ago, humans discovered that metals were some of the most robust and long-lasting materials. They started using metal to create weapons and fabricate practical items like utensils, furniture, jewelry, and transportation. Eventually, ancient welders learned to fuse metals such as bronze, gold, and iron, and the first metal fabricators came into being.
Modern, sophisticated welding techniques and welding types have grown from these rudimentary methods into several types of welding. Although each of these welding styles is somewhat unique, they all have a similar goal: to connect two or more pieces of metal with the strongest bond possible in the shortest time.
Here are seven of the most popular types of welding and their typical applications. As you will see, some methods are more challenging to learn than others, and some are more hazardous. However, anyone learning to weld should realize there is some degree of danger associated with all welding, and wearing personal protective equipment (PPE) is the best way to remain safe.
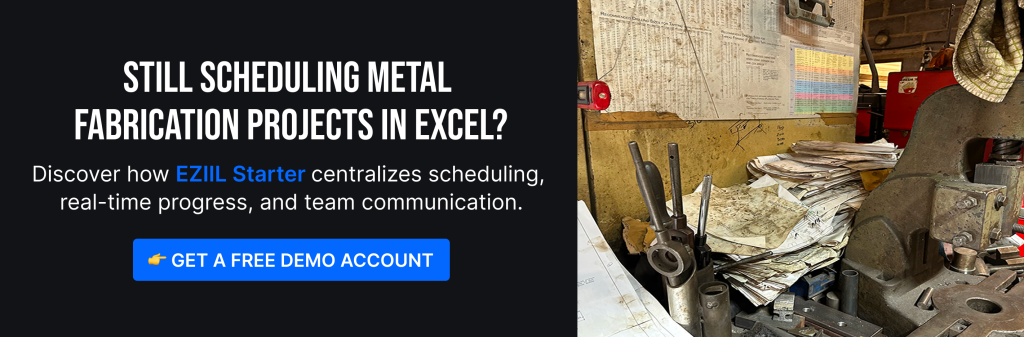
1. Stick, or Shielded-Metal Arc Welding (SMAW)
Stick welding has been around for one hundred years and remains popular while being updated and improved. Stick is easy to learn and a relatively inexpensive way to weld, although it spatters easily, requires cleanup, and doesn’t produce the prettiest welds.
A consumable electrode (stick) serves as the filler metal. The heat from an arc between the end of the electrode and the base metal melts the stick into filler metal and creates the weld. The stick is coated in flux, creating a gas cloud protecting the metal from oxidation. When it cools, the gas stays on the metal and becomes slag.
Because it doesn’t require a shielding gas, stick welding works outdoors, even in inclement and windy weather and on dirty, painted, and rusty surfaces. Stick welding is ideal for repairing farm equipment and for numerous applications in the construction industry. Welders can use several types of electrodes that are easy to switch out for different metals.
2. MIG, or Gas Metal Arc Welding (GMAW)
MIG welding is one of the simple forms of welding and is typically the method of choice for new welders, hobbyists, DIY enthusiasts, and others who don’t want to spend too much money on expensive equipment.
With MIG, the filler metal is a consumable wire fed from a spool through the wand, acting as the electrode. As the arc is created from the wire to the base metal, the wire melts, becoming filler metal and forming a weld that is usually visually appealing.
At the automobile plants where workers assemble auto parts into finished vehicles, MIG welding is used for heavier metals and equipment. MIG is also popular at auto repair shops and has a long history in the transportation industry. It has also played a role in preparing and assembling the country’s railroad tracks.
3. TIG, or Gas Tungsten Arc Welding (GTAW)
As opposed to MIG welding, TIG is a complicated welding method reserved for experienced and skilled welders. With TIG welding, the electrode is made of tungsten and is non-consumable. It is unique in that it can be done without filler metal, using only the two metals being welded together. You can add a filler metal if you feed it by hand.
You’ll need a shielding gas tank to protect the weld, meaning TIG is typically preferable for indoor welding. Because there is no weld spatter with TIG, no cleanup is necessary, and the welds tend to be attractive. And although the welding method is versatile and precise, it is one of the most challenging techniques to learn.
TIG requires two hands when using a filler: One holds the TIG torch, and the other feeds the filler rod. This torch creates heat and arc to weld metals, such as steel, nickel alloys, stainless steel, aluminum, titanium, and others.
TIG is commonly used when welding small, thin items that require a stylish appearance. It’s also preferred for DIY projects like repairing lawnmowers, making furniture, fixing bike frames, and building metal shelving.
4. Plasma Arc Welding
Plasma arc welding is another technique similar to TIG but uses a smaller arc for even greater precision. It also has a different torch that can reach higher temperatures, and the gas is pressurized inside the wand to create plasma. The plasma is then ionized to make it electrically conductive, enabling the creation of the arc that produces the extremely high temperatures that melt the base metals.
Like TIG welding, the plasma arc can occur without filler metal. This welding method provides deep and narrow weld penetration producing solid welds that are aesthetically pleasing with high welding speeds.
Plasma arc welding is used in aerospace applications where the metal can be as thin as 0.015″. It’s also excellent in the automotive industry for steel tubes in the exhaust systems and welding thin electronic chips and other small metal components.
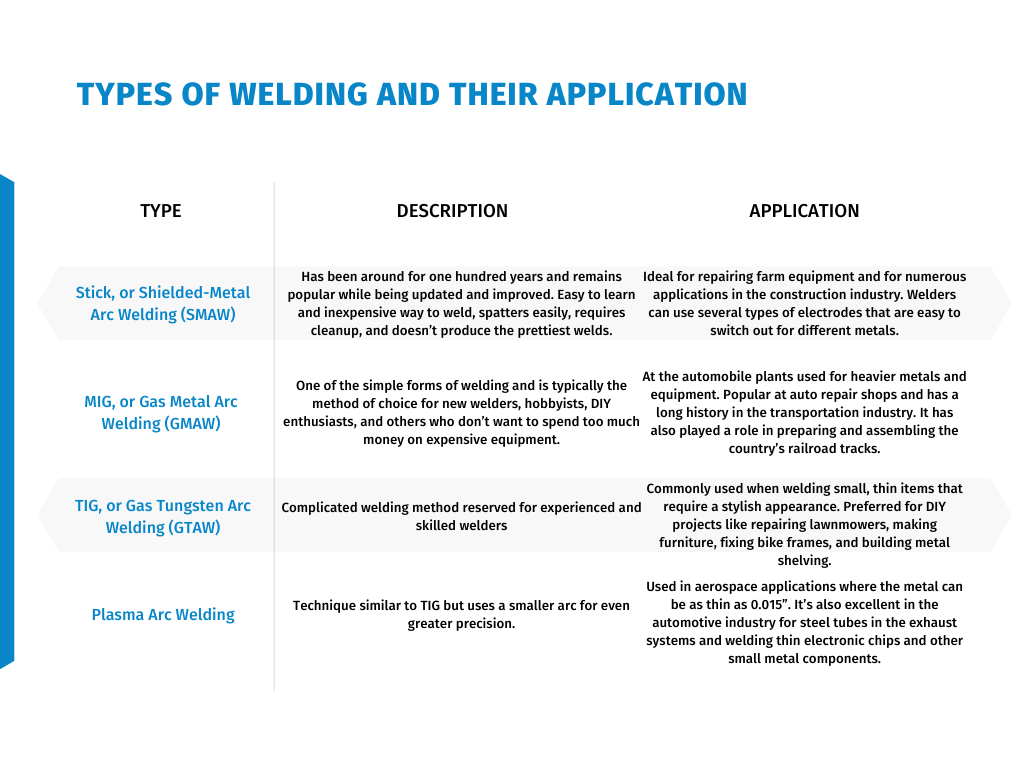
5. Flux-Cored Arc Welding (FCAW)
Flux-cored arc welding is much like MIG welding; welding professionals often use MIG welders to perform FCAW. As in MIG welding, a wire electrode and filler metal are fed through the wand. However, the wire has a core of flux that creates a gas shield around the weld in FCAW, which eliminates the need for external shielding gas.
FCAW works well with thicker, heavier metals because it is a high-heat welding process, so it’s generally preferred for repairing heavy equipment. Although the weld may require some cleanup, it is an efficient, low-cost method that produces little waste.
Flux welding is portable and versatile, making it useful in the construction and shipbuilding industries. It is widely used in mechanical industries and is the go-to technique for surfacing and hard facing. Various repair shops like it because it works on rusted or contaminated metals.
Book a 60-minute demo to see
how eziil mrp solution works for you
6. Electron Beam Welding
Electron beam welding is a high-energy welding method where a high-velocity beam of electrons creates heat through kinetic energy, welding two materials together. EBW is a complex type of welding usually performed in a vacuum by a machine. When the ray hits the metal, it melts just enough to fuse the adjoining piece into place.
EBW welding plays a role in several industries. For example, the beams are so accurate they can weld the tiniest implantable medical devices and so versatile they can weld large spacecraft parts. Manufacturers also employ EBW welding to fuse many metal parts used in cars, trucks, and planes. And because EBW is vacuum-based, the technique is safe for emergency work in evacuated buildings.
7. Laser Welding
Laser welding uses a laser beam to concentrate heat and fuse multiple pieces. Laser welding can produce a strong seam at high speed by delivering a focused heat source. This welding technique can be used on metals or thermoplastics, including steel, stainless steel, titanium, and aluminum. Since it’s easily automated with robotics, laser welding is prevalent in manufacturing, especially in the automotive industry.
Laser welding is also used in the medical industry and for making jewelry. As long as the material has a high heat conductivity, it is a candidate for laser welding.
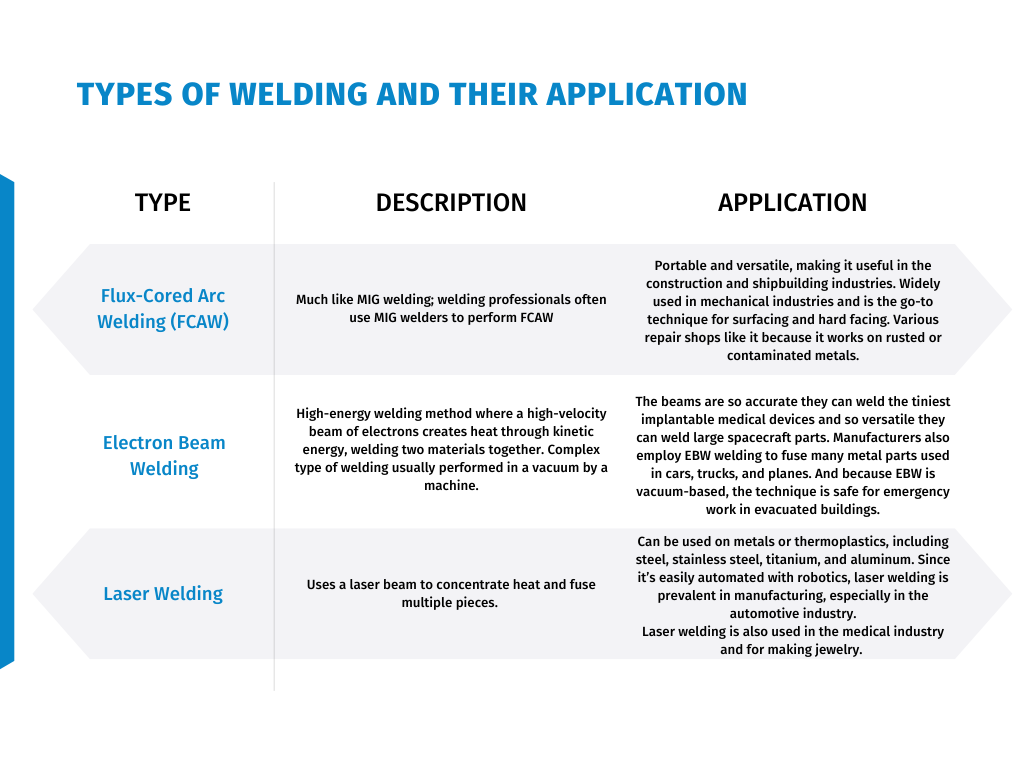
Some less common types of welding
Although MIG, TIG, and stick welding are far and away the top welding techniques, a few others are worth mentioning:
· Atomic hydrogen welding is still used in tungsten welding, where a fast welding process is needed, such as in stainless steel.
· Oxy-fuel welding employs liquid fuel and oxygen to weld metal, usually in an indoor environment.
· Submerged arc welding requires flux to shield the metal when the welding occurs. Hence the name “submerged.”
· Carbon arc welding is a technique that fuses metals by applying temperatures exceeding 300 degrees Celsius.
· Electroslag is a vertical process of bonding heavy metal pieces for use in machines and industrial equipment.
· Resistance spot welding is an arc welding method during which electrical currents generate heat to bond metal surfaces.
Conclusion
You should now have a basic understanding of the different welding methods. Although some of these require expensive equipment, others can be used by a home hobbyist for a relatively small initial investment.
Remember that the type of welding that works best for you depends on the project you take on, the materials you use, and your experience. MIG welding is usually the method of choice for beginners, while TIG is versatile and precise but takes time and patience to learn.